PBF vs. DED: Which Metal 3D Printing Process Should You Choose?
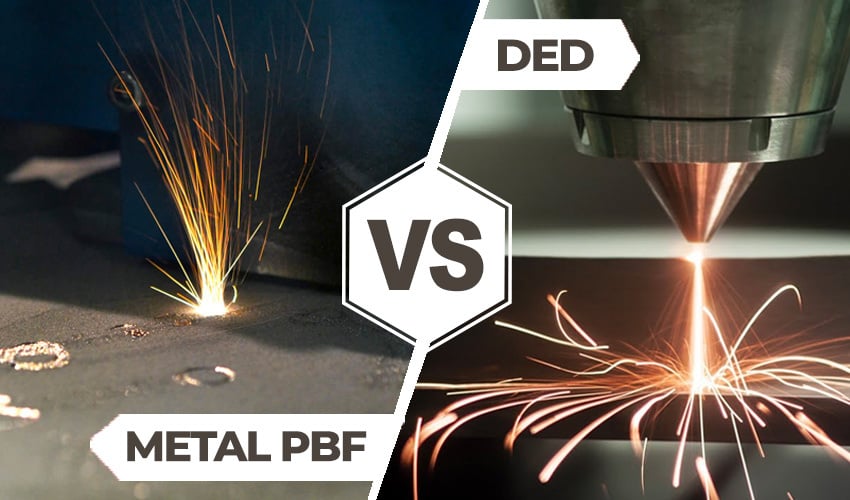
Metal is one of the most widely used materials, along with plastic, in additive manufacturing. The properties of this material make it suitable for the most demanding markets including for high-performance applications. In this article, we are comparing two of the main metal printing processes: Laser-Powder Bed Fusion (L-PBF) and Directed Energy Deposition (DED). We will be examining the characteristics, most common applications and leading manufacturers of each technology, highlighting their similarities and differences.
To begin with a brief introduction, PBF encompasses several additive manufacturing processes that involve the use of a powder bed, be it plastic, ceramic or metal. As you may have guessed, today we will be focusing on metals. This process can use a laser or an electron beam as an energy source, for example electron beam melting (EBM), introduced by the manufacturer Arcam in 2002. However, in order to compare more directly, we will only be focusing on the process that uses a laser as a heat source. The process is also known by other names, depending on the designations of the various manufacturers, such as DMLS, a term patented in 1994 by EOS, a leader in metal 3D printing. The acronym comes from the German “Direkt Metall Laser Schmelzen” which translates into English as Direct Metal Laser Melting. It can also be called SLM for Selective Laser Melting, a term introduced by the Fraunhofer Institute in 1995.
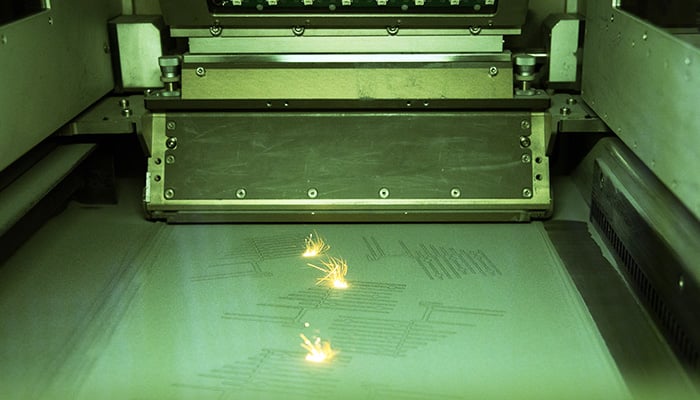
The PBF process
In contrast, DED is a more recent method than other metal powder bed technologies. It has been known for longer, but has only become truly effective in the last decade. The process uses a material, in powder or wire form, that is melted by a direct energy source while being deposited directly onto the part. The process is best known for its ability to repair and/or coat large metal objects. DED technology can use different energy sources such as laser, plasma or electron beam. For example, WAAM (Wire Arc Additive Manufacturing) technology falls into this category. It is therefore not easy to compare PBF and DED processes, as they are two very different technologies. We will therefore try to understand how they work, how they differ and how they can be complementary.
How Do Metal PBF and DED work?
One of the biggest similarities between the two centers on some of the set steps that must occur within 3D printing. Notably, 3D printing process always begins with the creation of a 3D model of the object to be printed, using CAD software. A slicer then digitally cuts the part, layer by layer.
Now let’s start with PBF: the chamber is heated with an inert gas to reach the ideal temperature (for the EBM process, this must take place in a vacuum). A thin layer of powder is then applied to the plate, which is also heated to a temperature of about 300/400°C. The laser then selectively melts the metal particles and solidifies them. Once the layer is complete, the tray moves down, allowing another layer of powder to be added. The process is repeated until the finished part is obtained.
Once ready, it must be allowed to cool. The surrounding loose metal powder is then removed, along with the printing supports, which are almost always required for PBF. They are highly recommended, especially for the first layer, to fix the part on the printing plate without compromising the final geometry and properties of the part. Finally, metal parts undergo various post-processing processes, which we will detail in the dedicated section.
As far as DED is concerned, it could be considered to be a bit of a mix between extrusion and PBF. Indeed, this technology manufactures parts with a focused energy source to melt the material. The print head is fed with powder or metal wire and a nozzle deposits the metal used layer by layer. The metal is melted as it exits the nozzle onto a base or component to be repaired. The process is repeated, until the 3D model that was previously designed via CAD software is reached.
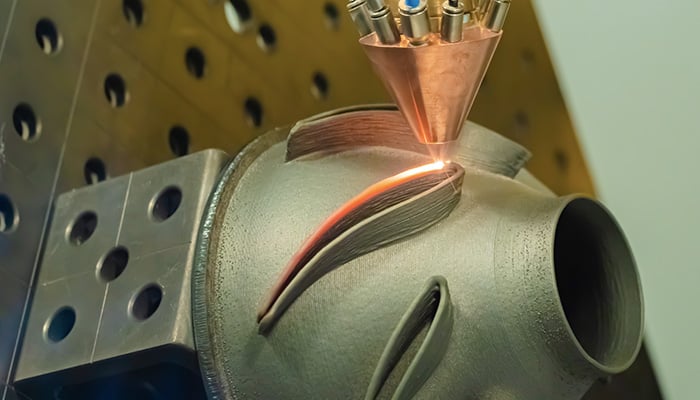
The DED process with a laser
DED 3D printers are industrial machines that can be used with three possible energy sources: laser, electron beam and plasma. Depending on the type of energy chosen, the 3D printer will have a different environment. Note that most DED machines are large industrial machines that require a closed and controlled structure to operate. For laser systems, a completely inert chamber is required for reactive metals. This requires a significant amount of gas and time to reach the desired oxygen levels. For the electron beam, the process must be performed in a vacuum to avoid electrons interacting with or being deflected by air molecules. Finally, when using plasma as the energy source, the material is precisely melted in an inert argon gas environment. The process is monitored over 600 times per second for quality assurance.
Advantages and Limitations of PBF and DED
Metal powder bed fusion is one of the most widely used technologies for producing final parts that can be used directly, as opposed to DED, which is used more for repairing, coating or adding custom parts. Looking at the two techniques, both have advantages and limitations. The main advantage of metal laser fusion is that it can create parts with high geometric complexity. In addition, when combined with topological optimization, the technology can create lighter metal parts with less material, which is critical in industries such as automotive and aerospace.
DED technology, on the other hand, is ideal for machining large metal parts with high mechanical properties. DED 3D printers consist of a nozzle placed on a multi-axis robotic arm (there can be four or five), allowing for both a high degree of freedom in printing as well as a large printing volume. In terms of production time, the material deposition process, which can print up to 5 kg/h, is one of the fastest. According to Optomec, a U.S. 3D printer manufacturer, DED is 10 times faster than PBF. This is an advantage, but also a disadvantage in terms of part accuracy, because a higher printing speed requires a greater layer thickness (between 5 and 10 mm), and therefore a less accurate rendering of parts. PBF, on the other hand, has very thin layers (down to 0.02 mm), and the laser works on the part point by point, which lengthens the production time but increases the level of detail.
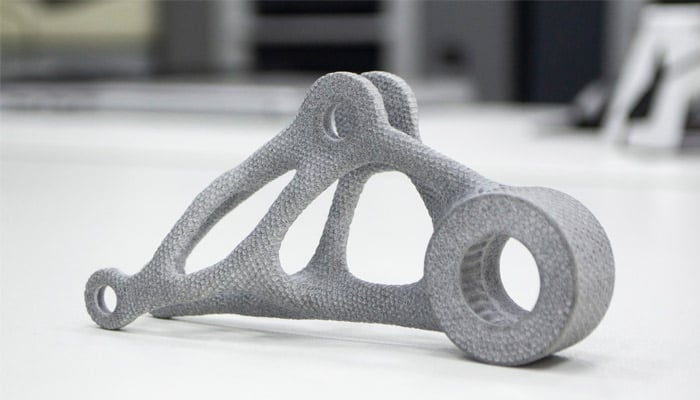
Topology optimization can make 3D printed metal parts lighter
In terms of part dimensions, DED favors the production of large-scale products, where powder bed fusion is limited by the size of the plate. It should be noted that the largest part that can be manufactured with PBF is no larger than one meter, whereas DED offers the possibility of working on large surfaces of several meters. However, both technologies offer environmental advantages. For the fusion, in some cases and with some metals, unprocessed powder can be reused as new powder can be mixed with old. DED, on the other hand, uses less material in its manufacturing process, although the process does require machining techniques to remove material from the part. Still, both technologies promote waste reduction compared to traditional construction methods.
From a more “practical” point of view, PBF technology is not suitable for mass production because it would be too costly compared to CNC machining. It is therefore more suitable and used for small series requiring specific or customized geometries, such as dental prostheses. Finally, the amount of material used in PBF printing also has a greater impact on production costs compared to DED. As for the limitations of the material deposition technology, it does not allow the production of parts with complex geometries. DED will be used for parts with simple shapes. However, the large dimensions of the components also have an impact on the price. The costs of the machines themselves are very high, even if the process remains less expensive than PBF. Finally, both technologies are also subject to numerous post-processing steps that increase costs. We will discuss this in more detail later in the article.
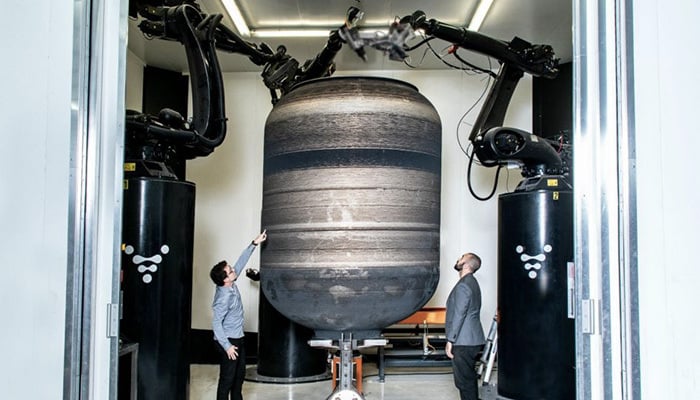
A 3D printed tank with Relativity Space’s DED technology (photo credits: Relativity Space)
Metal as a Primary Material
The choice of material has a significant impact on both technologies, as it represents the major cost for each process. For PBF, the chamber will need to be filled with metal powder to print the parts, and for DED, the larger the part, the more material will be needed.
In general, laser fusion offers a wide choice of compatible metals, but some continue to remain incompatible today, such as high carbon steels, which are ideal for welding, or high silicon aluminum. This can be a limiting factor when specific materials are required. However, the process can employ metals and alloys such as stainless steel, cobalt chrome, aluminum (used primarily in the aerospace and automotive industries), titanium (particularly suitable for the medical sector), Inconel and copper. Precious metals such as gold, platinum and silver can also be used. For DED technology, there is a choice between metals and ceramics; here we will focus mainly on the former. Indeed, ceramics are rarely used because they are complex to implement and are only compatible with a laser energy source.
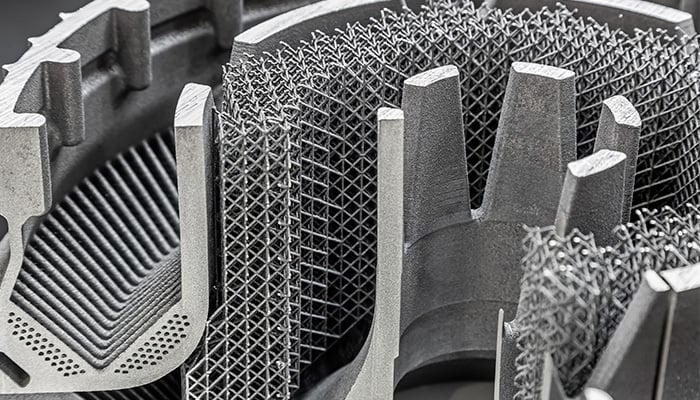
The metals currently compatible with the processes are vast
Many metals, in powder or filament form, can also be used for DED technology. Unlike PBF technology, direct energy deposition generally allows the use of all weldable materials, such as titanium and titanium alloys, Inconel, tantalum, tungsten, niobium, stainless steel and aluminum. In this case, it is important that the melting temperature is higher than the chamber temperature, so the process requires different and controlled degrees for each material.
Applications for PBF and DED
Both technologies can be used in a wide range of applications and sectors. The major differences between the two processes are the way the powder is deposited and treated by the laser, as well as the purpose for which the processes are used. They are used in demanding sectors such as aerospace, automotive, medicine or even jewelry, in the case of PBF technology.
For example, for DED technology, the main applications include the repair of large parts. If we take the aerospace sector, typical examples of use are the repair of turbine propellers, valves or tools of all kinds. It is also possible to use different powders or to join materials such as, for example, steel and cast aluminum to weld batteries for electric motors. However, PBF technology does not allow for the joining of powders, as they would mix and be unusable. However, aerospace industry can still benefit from its advantages, especially for the production of complex, custom-made parts or end pieces.
The precision and quality of PBF parts also make them particularly suitable for end use in the automotive industry, with 3D printed parts integrated into cars such as oil separators, chassis or engine components. As mentioned above, it can also be used with precious metals to create jewelry or accessories. For the medical sector, this technology offers the possibility of detailed implants, such as metal cranial implants or dental crowns, customized for each patient.
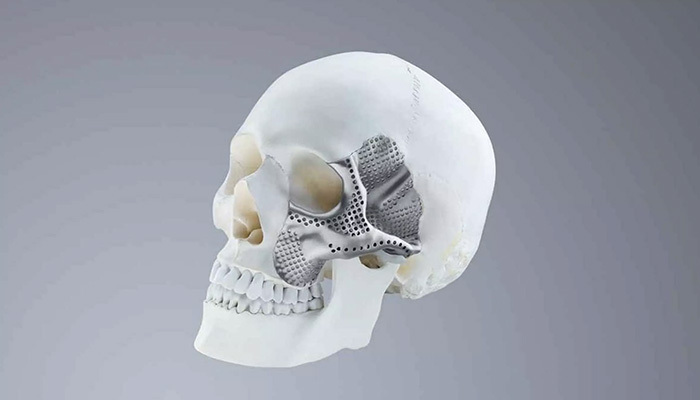
PBF technology enables the production of customized medical implants (photo credits: Trumpf)
Like PBF, the DED process is also used in the medical sector to produce orthopedic implants, surgical devices and prostheses. Some metals, such as titanium or stainless steel, are even biocompatible. This means that they can be inserted into the body without the risk of allergic reactions from the immune system. Finally, material deposition is also used for the protective metal coating of various types of components. This makes the parts harder, more resistant to corrosion, rust, chemicals or weathering.
Other sectors benefit from these technologies, such as the oil and gas industry with applications like pressure vessels, which can be produced with DED, as well as the maritime and defense industry, for example for the production of components. Moreover, in the case of complex parts, it is possible to use both technologies in a complementary way in order to obtain the most detailed hybrid part possible and in the shortest time. For example, as Didier Boisselier, Application and Development Manager for Additive Manufacturing at Irepa Laser, explains, Irepa Laser produced a hybrid metal part for the defense sector. The part had a high degree of internal geometric complexity, which required the use of PBF for the inner part, while DED technology was used for the outer part to speed up the process.
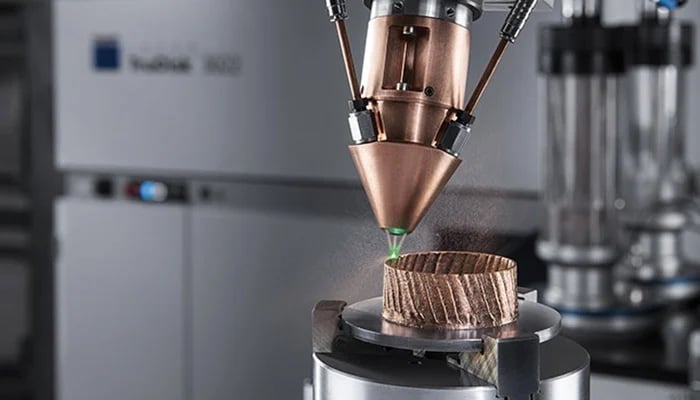
DED is used for parts with a simple geometry (photo credits: Trumpf)
The Different Stages of Post-Processing
While parts made with these two technologies provide high performance parts, products with super alloys that can pass the most severe tests, it is also true that to achieve such a result, both processes require more post-processing steps, which increases costs. For example, surface finish is important, although to different degrees. Indeed, in the case of PBF, it will be necessary to treat the surface to make it smoother, because the parts appear grainy. With DED, you will get parts with an imperfect surface, because the material is melted directly during extrusion. Therefore, the CNC machining step is always necessary to get a more defined and smooth surface.
In addition, the rapid heating and cooling of the metal during both processes results in the accumulation of internal stresses. Heat treatments can relieve these stresses and improve mechanical properties such as hardness, elongation, fatigue strength, etc. For metal laser fusion, it is necessary to remove excess powder and substrates. This can be done manually, mechanically or by wire EDM. Next comes surface finishing, where a polishing or CNC process can be added to improve the aesthetics of the part.
For DED, milling (CNC) the part is an essential step in finishing it. This is time consuming and requires a significant investment due to the large size of the parts. In general, the most commonly used techniques for post-processing metal parts are hot isostatic pressing (HIP), which removes any residual internal microporosity and completely solidifies the part, and annealing, a heat treatment option used to improve the mechanical properties of the part by heating it to a high temperature and then cooling it rapidly. Surface finishing methods for metals include dry electropolishing, sandblasting, etc.
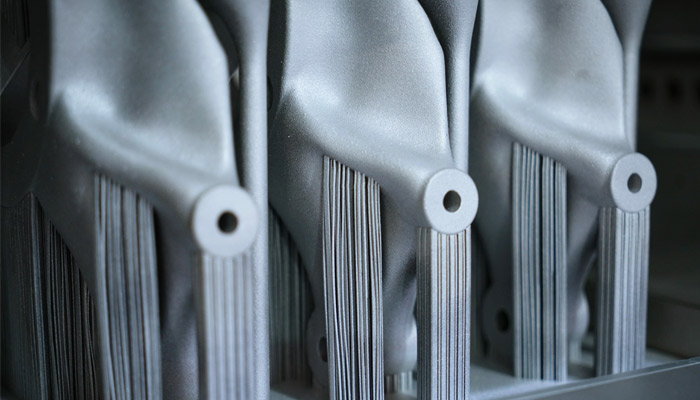
3D printing supports have to be removed
It should be kept in mind that, for both DED and PBF, it is not possible to define a single post-processing process, which will depend on the size of the part, the metal used (e.g., materials such as titanium require specific, even more expensive, treatments), the type of part produced and the specifications required by each specific industry.
Major Manufacturers
Today, many manufacturers offer laser melting machines on powder bed. Among the main ones, we can mention EOS, a major player in metal 3D printing, which remains today one of the main manufacturers of DMLS 3D printers. Let’s not forget 3D Systems, which acquired the French brand Phenix Systems in 2013 to expand into the metal additive manufacturing segment. Its process has been dubbed DMP for Direct Metal Printing. Other companies offering metal laser fusion printers include the British company Renishaw or the German manufacturer SLM Solutions – though even this list is not exhaustive.
Manufacturers specializing in laser DED machines include AddUp, which in 2018 acquired BeAM, one of the leading DED machine manufacturers in the market. The company also offers two L-PBF solutions. American Optomec is also one of the leading players with its patented LENS process that was brought to market in 1998. Today, the company has no less than seven solutions. The manufacturers FormAlloy, DMG Mori, InssTek, Relativity and Meltio are also worth mentioning. The latter claims to offer the cheapest DED machines on the market. Finally, other companies offer both solutions such as the German company Trumpf or the Italian company Prima Additive, with the latter offering a double laser or green laser option for copper and reflective metals. Although there are many more.
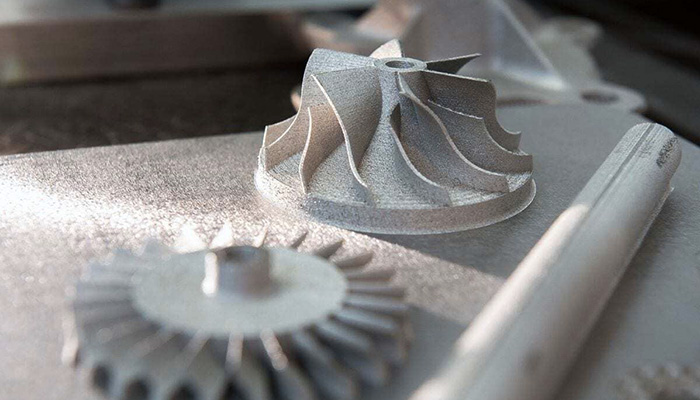
Photo Credits: AMFG
Price
As mentioned earlier, the prices between DED and PBF 3D printers are high, but not the same. In fact, directed energy deposition process could be considered to be about 5 times cheaper than powder bed fusion. Though it is difficult to give exact figures. Manufacturers do not disclose the price of their products online, and costs can vary depending on how the user will operate the 3D printer. It also depends on whether the buyer also wants to benefit from post-processing solutions, or specific materials. In any case, it will be difficult to find a metal machine in this category for less than $80,000. Some 3D printers may even go up to almost $1,000,000. When it comes to powder bed laser fusion solutions, prices can start at $200,000. Consider 3D Systems’ DMP Flex 350, estimated at about $575,000, or the DMP Factory 350, which can go up to $763,000. For DED systems, prices can increase dramatically when considering more complex solutions, such as DMG MORI’s LASERTEC 6600 DED hybrid machine, which combines DED technology and subtractive machining into one solution. Its estimated cost is one of the highest, between $1.5 and 3 million.
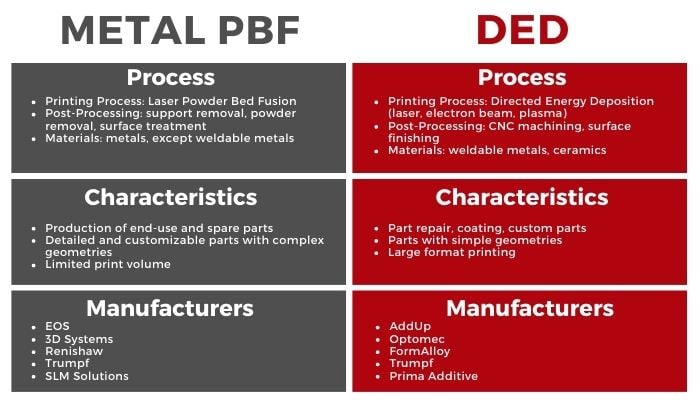
Photo Credits: 3Dnatives
Which technology would you use between laser powder bed fusion and directed energy deposition? Let us know in a comment below or on our LinkedIn, Facebook, and Twitter pages! Don’t forget to sign up for our free weekly Newsletter here, the latest 3D printing news straight to your inbox! You can also find all our videos on our YouTube channel.