PARI Researchers Use 3D Printed Dark Ceramics to Advance Hypersonic Manufacturing
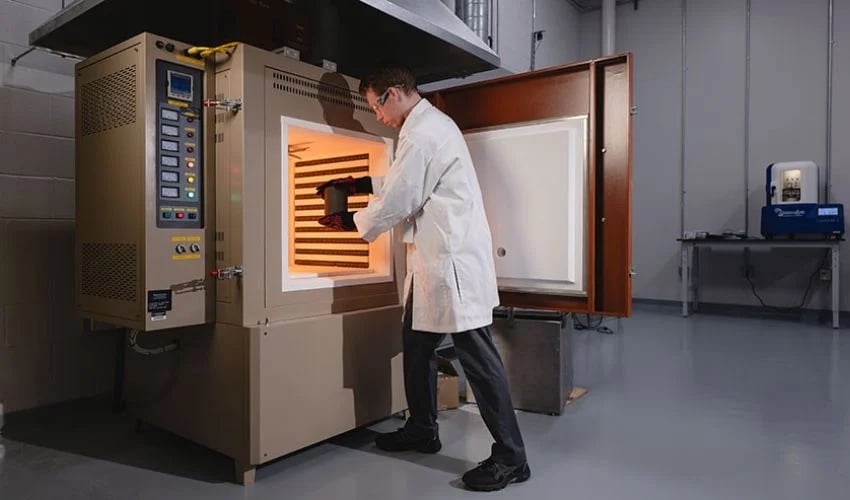
Hypersonic manufacturing is one of the most challenging areas of research in modern aerospace applications. Vehicles traveling at more than five times the speed of sound have to withstand extreme conditions, including temperatures of more than 2000°C and enormous mechanical loads. Conventional materials quickly reach their limits here. That is why researchers at the Purdue Applied Research Institute (PARI) are now developing additive manufacturing processes to produce dark ceramics in complex shapes for the components of hypersonic vehicles using 3D printing.
Dark ceramics were chosen because they can withstand the extreme conditions of hypersonic flight and are less susceptible to cracking or wear. Rodney Trice, professor in the College of Engineering’s School of Materials Engineering and the thrust lead in ceramic processing at PARI’s Hypersonics Advanced Manufacturing Technology Center (HAMTC), is leading the research. The goal? To 3D print components on a large scale to increase the efficiency and performance of hypersonic vehicles.
The team used 3D printers at HAMTC that use digital light processing (DLP) technology and work with a UV light projector. This irradiates a thin layer of ceramic powder and resin, which hardens the material and fixes the powder. Trice emphasizes that this process allows complex designs and geometries to be produced with smooth surfaces and micrometer precision. The team has succeeded in producing different shapes, including cones and hemispheres, which are suitable for the construction of hypersonic vehicles.
Nevertheless, the research presented challenges, particularly in relation to the interaction of the color with the UV light of the 3D printer. Light-colored ceramics such as aluminum oxide reflect and scatter the light, allowing the entire layer to cure evenly. Dark ceramics, on the other hand, tend to absorb light, which hinders the curing process.
“Because dark powders absorb the UV light that would be necessary to cure the material, we cannot form as thick of a layer. Therefore, we get cure depths that are too thin, which then negatively impacts the time it takes to build each part,” explains Trice.
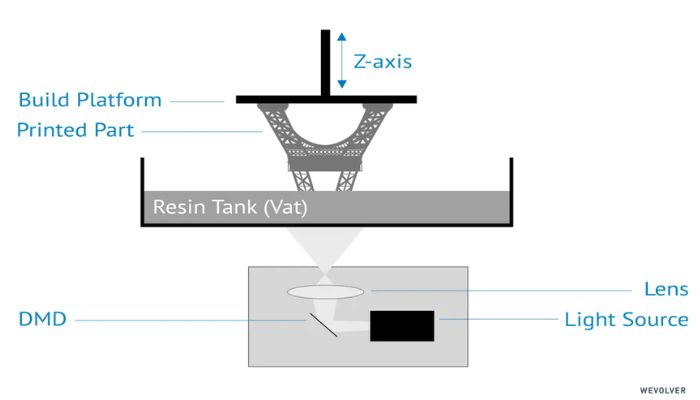
An illustration of the classic DLP process, which was originally commercialized by EnvisionTEC (photo credits: Wevolver)
For this reason, he worked with Matthew Thompson, a PhD student in materials engineering, and Dylan Crump, a ceramics research engineer at HAMTC, to research resin systems, surface treatments and other approaches to increase cure depths. “We’ve been operating essentially as a research and development test bed for these materials. We’ve been tuning properties and performing surface modifications to improve their performance and enhance the printing process,” Thompson emphasizes.
The team is also working to avoid problems in the post-processing phase, which can be particularly difficult with larger components. For example, delamination, i.e. the part peeling or separating between layer, or cracking, which can become a risk. “What we’re trying to do is find solutions for how we can either set up a pipeline to make these parts or find strategies that actual stakeholders can use. So, it gives people a starting point to save time on the research and development for any new system,” he continues.
This project is one of five that is being funded by the Office of the Secretary of Defense Manufacturing Science and Technology Program, in partnership with Naval Surface Warfare Center, Crane Division, and the National Security Technology Accelerator’s Strategic and Spectrum Missions Advanced Resilient Trusted Systems. Find out more HERE.
What do you think of the research at PARI into 3D printed dark ceramics for hypersonic applications? Let us know in a comment below or on our LinkedIn, Facebook, and Twitter pages! Don’t forget to sign up for our free weekly Newsletter here, the latest 3D printing news straight to your inbox! You can also find all our videos on our YouTube channel.
*Cover Photo Credits: Purdue University/Charles Jischke