3D Printed Surfboards from Paradoxal Surfboards To Be Made From Green Algae
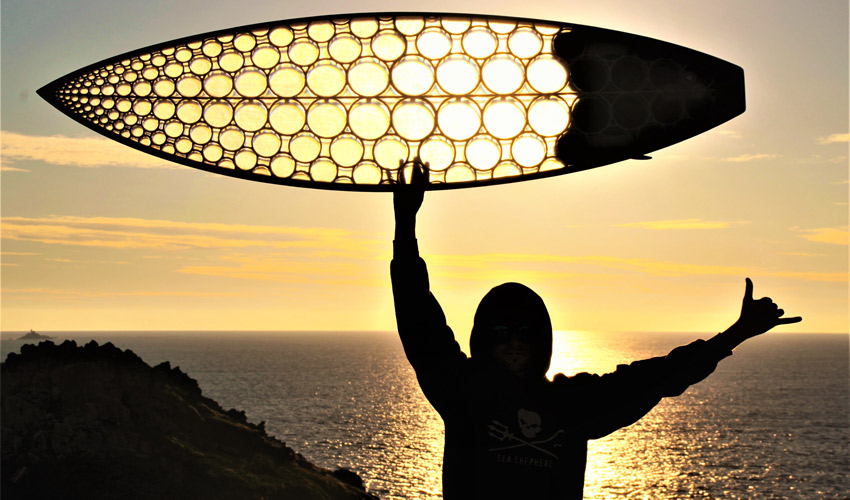
Paradoxal Surfboards is a project led by a young Frenchman who wants to make surfing more respectful of our environment. Jérémy Lucas has imagined 3D printed surfboards designed with greener materials, not those that come the oil industry. Namely, from the green algae that washes up on the Breton coast, he has developed a material compatible with 3D printing. He can thus recycle a waste product from the sea and create value. We met with Jérémy to learn more about this project and his future plans.
3DN: Can you introduce yourself? How did you discover 3D printing?
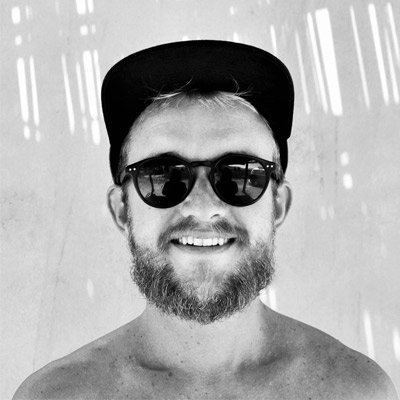
Jérémy Lucas
Hello, my name is Jérémy Lucas and I am a 32-year-old entrepreneur and surfer from France. I am the founder and owner of the Paradoxal Surfboards project. Basically, I discovered the joys of surfing about ten years ago during a road trip in Australia. I heard for the first time about 3D printing several years ago in specialized press articles that were focused on new technologies. At the time, it seemed so futuristic and inaccessible that I didn’t get more interested in it.
Then in 2019, I decided to co-create, with my partner at the time, a Mechanical Design office in Douarnenez. Under the name FL3D, we were mainly doing two things: industrial design, CAD, for professionals such as boilermakers, metalworkers, sheet metal workers, etc.; also, we were answering very specific requests for individuals thanks to our Ultimaker 3D printer installed in our small 9m² office. We had difficulty making this second activity profitable.
As this is a relatively time-consuming technology, our vision was clear: either we launch into mass production, with a substantial machine park, to meet industrial demands, or we put forth a predefined product with high added value.
3DN: How did you get the idea to create Paradoxal Surfboards?
It was in December 2019, I went surfing with some colleagues on the beach of Ris in Douarnenez in the middle of a storm. That day, there was swell, back-wash, the spot was full of green algae (unfortunately a recurrent phenomenon in this city) and I went under several times during the session. I came out of the water in a not so great state: headaches, vomiting, plus I was bedridden for two days. I had an environmental trigger and told myself that it was time to act, at our scale and by our means, to mitigate this phenomenon of green algae.
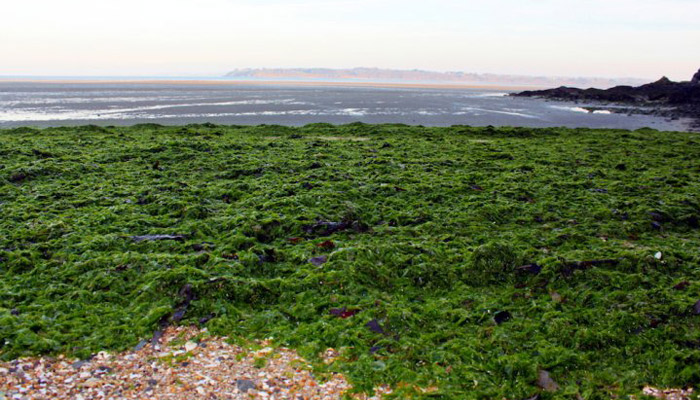
Green algae are more and more numerous on the Breton coasts (photo credits: Reporterre)
A week later, when we hand-delivered a 3D printing order to our office, a customer asked us about the origin of the materials we use for our 3D prints. We tell her that it is mainly a vegetable plastic, without oil, PLA. Then the customer, obviously well informed, explains to us that the PLA we use is made from corn sugar, which is very greedy for water, and which, in fact, devastates areas of dedicated biodiversity (and is also incidentally a GMO).
So we decided to think about making a new thermoformable material for 3D printing. From this we though why not from green algae? But what could we print from the material? The connection was quite quick when remembering the surf session of the previous week: “We’re going to 3D print surfboards from beached green algae!”.
We decided to name this project “Paradoxal Surfboards” for several reasons: as explained by the colleagues of YUYO, we come to answer, through this initiative, the “paradox of the surfer”. This person who, by his sport practice in the open air, agrees to a vision of sport that is more respectful of the environment but who also has no other choice than to use petro-composite materials (neoprene wetsuits, polystyrene or polyurethane boards, gloves, leash, etc.)
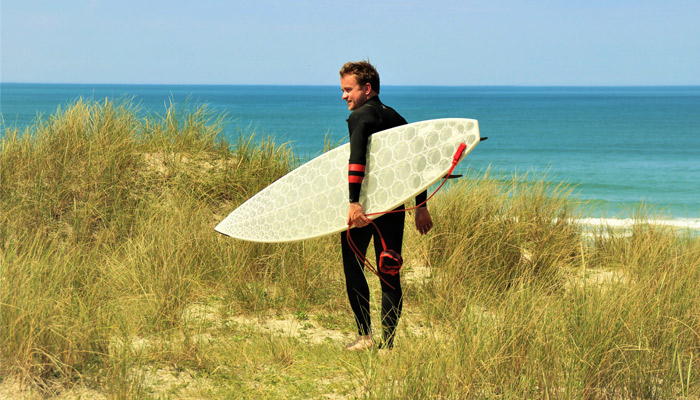
The objective is to not use materials from the oil industry to manufacture the boards
“Paradoxical” also, because we come through this project, to revalorize, not to say “upcycling”, the beached green algae which is considered as waste and which is present on all the Breton coast. In a “cradle to cradle” logic, we will use this waste found in the ocean to manufacture sports equipment, which will replace the oil commonly used in the manufacture of a surfboard (PU or EPS) and which will return in time to the ocean.
This undesirable material that has a negative commercial value, people didn’t know what to do with it, except to mix it (once collected, treated and stabilized) with other green waste as fertilizer in the fields in order to replenish a production system that already seems to be suffocating.
Without going into details about the quantities of algae collected each year near us and the quantity of seaweed necessary to manufacture a single surfboard, Paradoxal Surfboards acts neither on the preventive, nor on the curative part, but on a proposal of a new valorization of this “waste” that we find in abundance here in Brittany and which seems to be an excellent alternative to petro-composed products (toxic, not recyclable, and which come from far) that constitute a surfboard in nearly all cases.
The day when there will be no more green algae, we will be interested in making boards with beached plastic (the numbers are even more mind-boggling unfortunately). We are currently studying the possibility of 3D printing our surfboards from recycled fishing nets (from beachings).
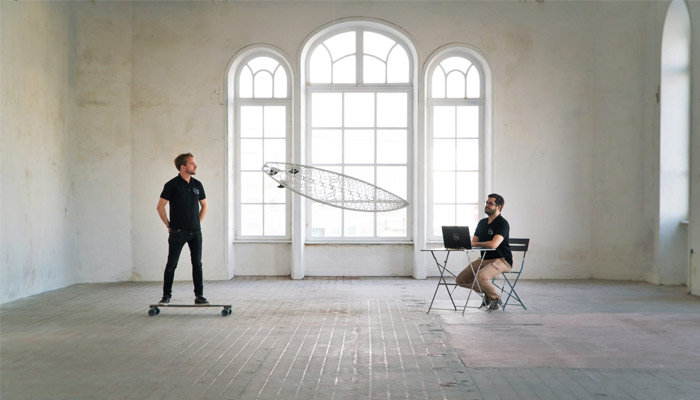
Photo Credits: Paradoxal Surfboards
3DN: How are the 3D printed surfboards made?
The blueprint is both simple, once established, and relatively complex to implement since it requires a certain amount of multi-skilling – three things were essential to the completion of this project:
Designing the board – Industrial Design – CAD:
Starting from a blank page and designing 3D printed surfboards is not an easy task. We had to find a balance between a relatively innovative design, which uses the right amount of printable material for a certain production cost, within a certain production time, while taking into account the performance of the board, its final weight, a balanced load distribution with little post-production. The business model depends on it.
3D printing and creating a new material:
Once designed, the board must be printed with the appropriate material (in large volume 3D printer). On our first prototype, the core of the board (which replaces the traditionally used foam blocks) is printed in two parts that will be thermo-clipped afterwards. The printing parameters are complex to set up and require some iteration before obtaining a final product at the top of its performance.
On this first prototype, we used PLA. The specifications of a new thermoformable material based on green algea powder from beachings combined with recycled Dyneema, from offshore racing boats, are currently being developed for future models.
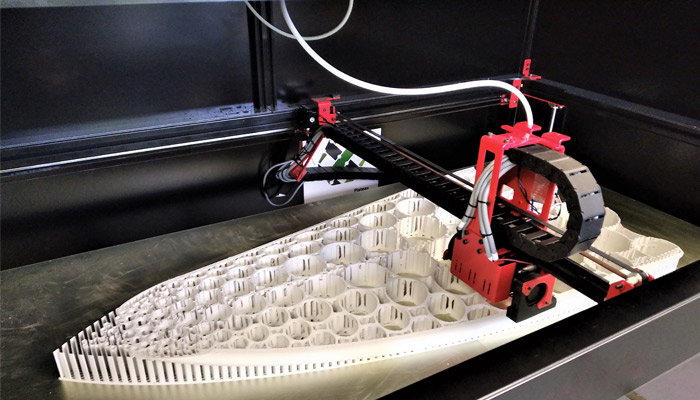
Printing the board prototype on a large format 3D printer (photo credits: Paradoxal Surfboards)
Layering:
Once the internal structure is printed, the board must be sealed by covering it with a fiber and then imbibing it with a resin. This is the lamination step. For this first model, and with rather large structural cells, the range of the fiber was a problem. We therefore, initially, relied on a process of reverse lamination by machining molds (negative form of the board) with the CNC, to be able to integrate the structure and then laminate it. This relatively complex step is the result of a great collaboration with several engineers and technicians specialized in composite materials in Brittany.
3DN: Why 3D printing?
Although currently time-consuming, 3D printing remains a low-energy technology and allows the realization of structures with very complex designs that are almost impossible to achieve by a craftsman in a conventional way. Moreover, 3D printing allows the use of a wide variety of materials with different properties. We were inspired by the living world, by biomimicry, by the structure of a green algae to be more precise. Since the vocation of our project is to 3D print surfboards from beached green algae, we found the idea of being inspired by living things to design the internal structure of our boards rather cool. We are currently developing new designs, still inspired by this same idea of biomimicry!
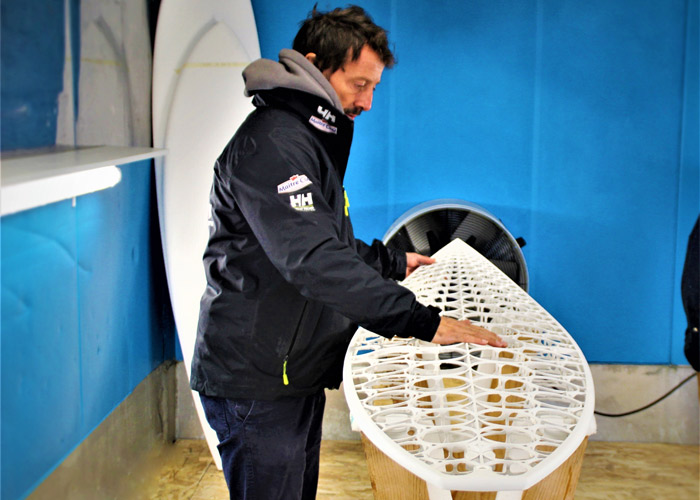
Photo Credits: Paradoxal Surfboards
3D printing also allows us to print the equipment associated with the board. For example, we 3D printed the core of the daggerboards from corn starch and then laminated them with recycled carbon from ocean racing boats, like the Vendée Globe.
3DN: What are the challenges you are still facing today with your 3D printed surfboards?
Paradoxal Surfboards was, until last March, an intrapreneurial project carried by a young start-up Douarneniste that I co-directed and which, today alas, does not exist anymore. The project is suddenly slowing down and my biggest challenge is probably to allow it to “continue” as a simple project leader and not as a company.
Another challenge is to succeed in formulating this new thermoformable material in green seaweed from beachings. Complex specifications, financing, tests… There is a lot of work to do. But there is already a whole network that centers on the creation of this first board and for the moment I continue to develop the project by advancing a little blindly.
3DN: Any last words for our readers?
Thanks for reading the article and/or sharing it! I also wanted, by the same occasion, to salute our colleagues at Wyve Surfboards who do a remarkable job. They inspired me in the development of this beautiful project and have been a great source of motivation to carry out this great challenge which consists in making surfing more respectful of our environment in its conception and manufacturing.
What do you think of Paradoxial Surboards and its 3D printed surfboards? Let us know in a comment below or on our Facebook and Twitter pages. Don’t forget to sign up for our free weekly newsletter, with all the latest news in 3D printing delivered straight to your inbox!
*Thumbnail Photo Credits: Paradoxal Surfboards
This is a good effort for sure, but makes little progress on the work started about five years ago? We already had a high invasive-species algal-based thermoplastic when we printed the first board. https://magicseaweed.com/news/the-worlds-first-3d-printed-recyclable-surfboard/10324/
Hi what its the cost of a board ?b
Building electric cars started about a hundred years ago. In an age where instant gratification is the norm, patience is forced on us.. Captain Tiny