Osaka University Researchers Discover Ultrasonic Quality Control Method
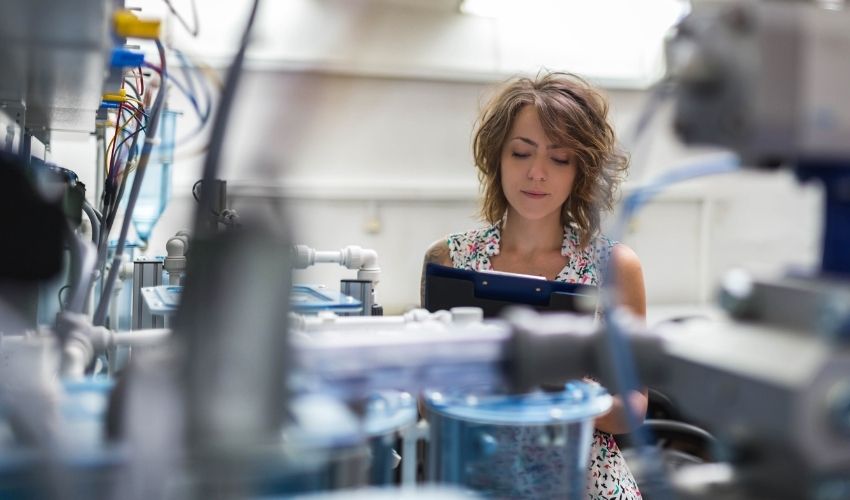
As additive manufacturing companies embrace the design freedom of 3D printing products and parts, they also have to overcome the obstacle of maintaining quality control. Researchers from Osaka University in Japan have uncovered a solution that will help companies achieve highly complex 3D-printed products while conserving high-caliber consistency in the print process. In an academic study published in Ultrasonics, researchers from Osaka University used laser ultrasonics to detect what they called fine-scale defects below the surface of 3D-printed metal assemblies. This study lead to the discovery of a unique quality control technology that can be applied throughout the 3D printing industry.
In traditional manufacturing or subtractive manufacturing, quality control can be conducted at each step of the process. However, quality control checks become challenging when rapidly building a prototype or a complex product. “It is often challenging to use laser-generated ultrasonic echoes for identifying subsurface defects in 3D-printed devices,” explains the lead author of the study Takahiro Hayashi. “We generated ultrasonic waves in the megahertz range to uncover small defects that are frequently difficult to image.”
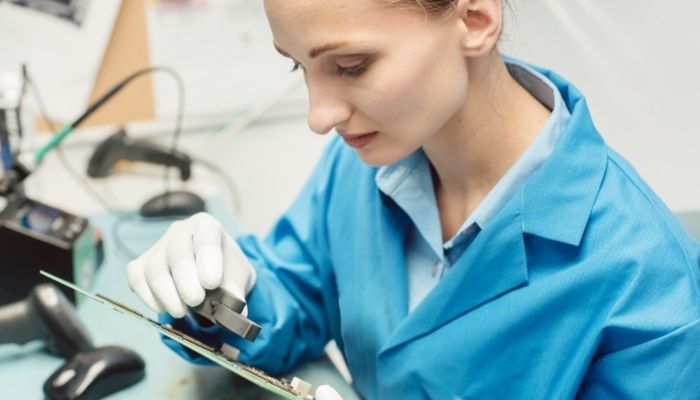
The study revealed the potential to implement a real-time defect detection system.
Quality Control for 3D Printing
Within 3D printing and the layer-by-layer assembly comes the obstacle of having to detect internal defects, without damaging the product—this is precisely what the researchers at Osaka University examined in their study. The researcher created artificial defects in a 3D-printed part to conduct their analysis. First, they fabricated an aluminum plate that had a millimeter-scale hole drilled into it. Next, they placed a thin, defect-free aluminum plate on top. The unit was then scanned with a laser across the surface which resulted in ultrasonic vibrations from the aluminum.
Mathematical processing of these vibrations produced a graphical readout that illustrated where the defect (the hole) was located as well as the size of the internal defect. The results of this study revealed the potential to implement a large-scale defect detection system that would allow for real-time repair of parts as they are being 3D-printed. This would be particularly helpful for 3D printing complex parts on a commercial scale. You can learn more about this study HERE.
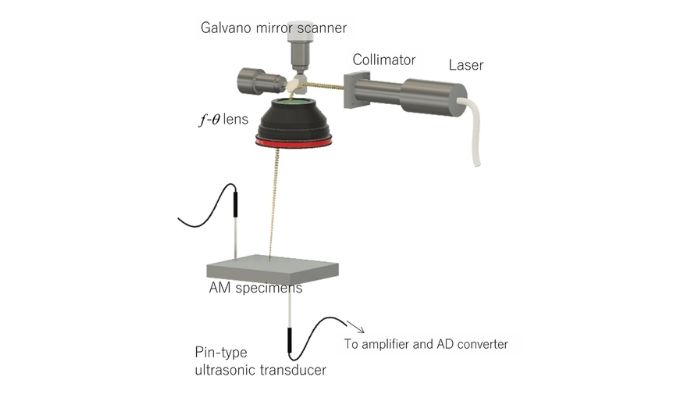
Photo Credit: Osaka University
What do you think of Osaka University’s quality control discovery? Let us know in a comment below or on our Linkedin, Facebook, and Twitter pages! Don’t forget to sign up for our free weekly Newsletter here, the latest 3D printing news straight to your inbox! You can also find all our videos on our YouTube channel.