ORNL Targets Faster, Safer Inspection for 3D Printing in Nuclear Applications
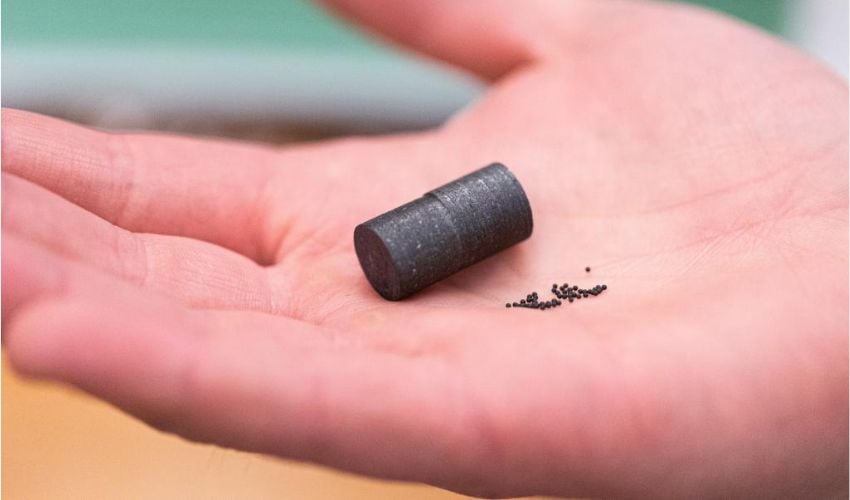
For years, the United States’ Oak Ridge National Laboratory (ORNL) has been one of the most active players in additive manufacturing for nuclear energy. In 2020, the lab made headlines for designing the first prototype of a 3D-printed nuclear reactor. Since then, they have printed nuclear reactor components, and in 2022, their researchers created a deep-learning framework that allows them to inspect these additively manufactured parts with greater speed and accuracy. In partnership with Idaho National Laboratory (INL), the two labs accelerated the inspection of 3D-printed nuclear components, and now, they are expanding to inspect nuclear fuels.
Critical to this research is this deep-learning framework created by ORNL. The software algorithm, called Simurgh, checks for flaws in AM parts, which helps them identify metals for 3D printing the next generation of nuclear reactors. It can take decades to verify new materials and manufacturing methods for nuclear reactor components, so the collaboration will accelerate the process.
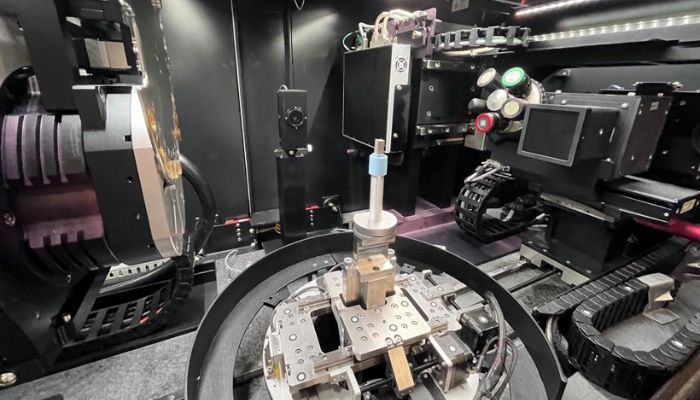
A 3D-printed part is scanned and analyzed using the ORNL software. (Photo credits: ORNL)
Simurgh uses X-ray computed tomography, which is a type of CT scan, to check the interior quality of 3D printed objects without damaging them. By compiling a series of X-ray images, the internal structure of a 3D-printed part is revealed, identifying weaknesses or printing errors. Typically, scanning the same part from many angles is time-consuming and expensive.
Simurgh, however, ameliorates this process by taking realistic training data to teach a neural network and using physics-based simulations with computer-aided design to reconstruct more accurate images with fewer CT scans. By requiring fewer CT scans than the conventional method, scanning for dense materials can be completed twelve times faster with a fourfold greater ability to detect defects.
Developing the Algorithm
The technology was initially developed for the Department of Energy’s (DOE) Advanced Materials & Manufacturing Technologies Office (AMMTO) for use with 3D-printed metal parts. But now, it is expanding under the Advanced Materials and Manufacturing Technologies program, or AMMT, in DOE’s Office of Nuclear Energy. By using the material in multiple offices, both labs are benefiting from Simurgh, creating opportunities for new applications.
Ryan Dehoff, director of DOE’s Manufacturing Demonstration Facility (MDF) at ORNL explained, “Nuclear is a high-cost environment with extremely high standards for precision, materials and safety. The fact we’re using this tool suite in the nuclear sphere speaks to the quality and reliability of the technology.”
INL decided to implement Simurgh when facing a logistical challenge. The lab was trying to link defects to specific printing parameters, but to do so, they needed to scan more than 30 samples to recognize patterns. The issue? Each scan took 30 hours. So, Bill Chuirazzi, an instrument scientist and leader of INL’s Diffraction and Imaging group, consulted ORNL before going forward with the effort. This led him to license ORNL’s algorithm so that he could collect data more efficiently. “Including prep, it now takes about 15% of the time it did to scan something with our setup,” Chuirazzi said. “We can do three scans in the amount of time it took us to complete one.”
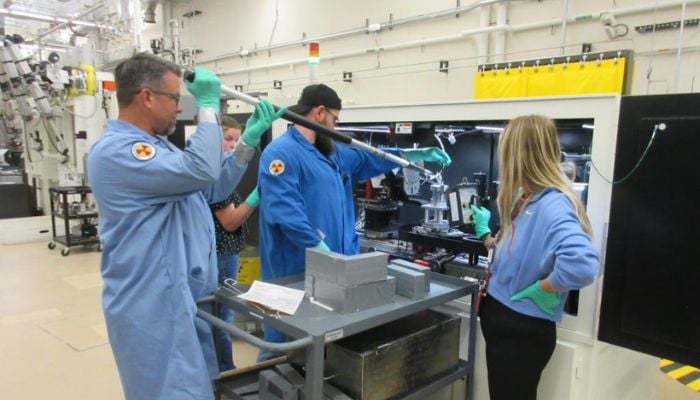
INL technicians (Photo Credits: Bill Chuirazzi/INL, U.S. Dept. of Energy)
And the technology’s use case did not end there. Chuirazzi foresaw that the technology could be used for another federal program focused on nuclear fuels: INL’s Irradiated Materials Characterization Lab. This lab specializes in scanning radioactive nuclear fuels and materials. Every time these highly radioactive materials move through the lab, they require high precaution and shielding. This causes researchers to delay examining materials removed from a nuclear reactor to let radioactivity dissipate enough for the safety of lab technicians. Additionally, radiation accrued during repeated scans wears on the detector, limiting its operating life and image accuracy. Simurgh, which permits shorter scans, means less radiation exposure per scan and less waiting, all while allowing for higher-quality data and faster feedback.
Nuclear Reactor Development Made Faster and Safer
According to the press release from ORNL, the Simurgh technology has the potential to help develop and characterize structural materials and fuels for advanced or high-temperature gas reactors, molten salt reactors and small modular reactors. One of the most promising fuels for new reactor designs is Tri-structural ISOtropic particle fuel, TRISO. These particles are made of a tiny fuel kernel encapsulated within a carbon- and ceramic-based material.
The INT team is now training the algorithm to inspect the ceramic casings of irradiated nuclear fuel like TRISO. By running the Simurgh program, they can check for irradiation-induced swelling, cracks and separation of outer layers. Going forward, this could be used to test irradiated metal components like 3D-printed fuel brackets created by the MDF.
The partnership between INL and ORNL is sure to accelerate the development of new fuel designs and material qualification for 3D-printed nuclear components. “If we use this algorithm to reduce the scan time for radioactive fuels by 90%, it will increase worker safety and the rate we can evaluate new materials,” Chuirazzi said. “Down the road, it enables us to expedite the life cycle of new nuclear ideas from conception to implementation in the power grid.” To learn more about the partnership, read ORNL’s press release HERE.
What do you think of ORNL and INL’s partnership to accelerate nuclear energy development? Let us know in a comment below or on our LinkedIn, Facebook, and Twitter pages! Don’t forget to sign up for our free weekly Newsletter here, the latest 3D printing news straight to your inbox! You can also find all our videos on our YouTube channel.
*Cover Photo: TRISO nuclear fuel resembles the tiny grains seen here. Photo Credit: Mark Richardson/INL, U.S. Dept. of Energy