Optimizing projects with both FDM and SLA 3D printing
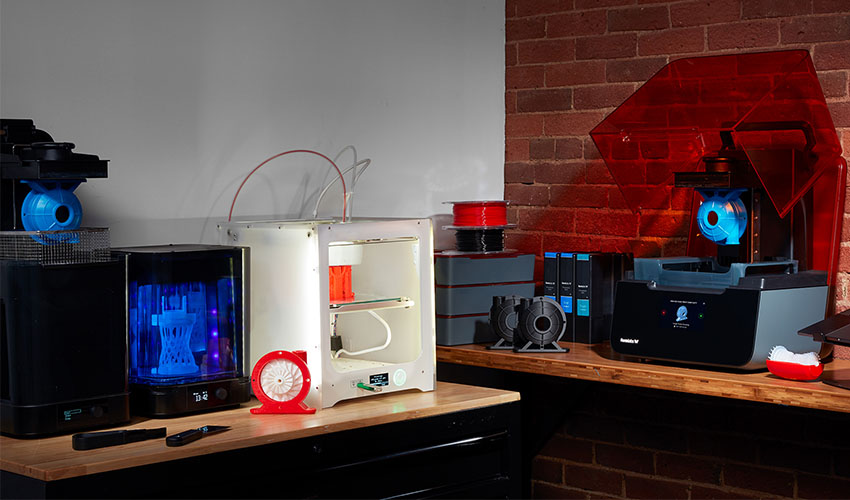
Not everyone is aware that FDM and SLA are complementary technologies that when used together can be highly beneficial for your AM projects. In product development, SLA 3D printing is ideal for detailed concept models or functional prototypes. In manufacturing, both technologies can be used to create jigs, fixtures and other tooling. FDM is usually preferred for large, simple parts, while SLA is better suited for complex jigs, highly accurate tooling and molds. For businesses, it is crucial to understand the fundamental differences in print quality, materials, applications, workflow, speed and cost in order to optimize projects.
Comparing FDM and SLA 3D Printing
At the consumer level, FDM 3D printing remains the most widely used technology. FDM 3D printers work by extruding thermoplastics layer by layer on the build plate, until the part is produced. On the other hand, SLA is more widely used in professional sectors. It uses a laser to cure resin into hardened plastic, a process called photopolymerization. While FDM produces a mechanical bond between layers, SLA creates chemical bonds by cross-linking photopolymers across each layer. The result is a fully dense part that is water and airtight and also ideal for many engineering and manufacturing applications where material properties matter. SLA parts also provide high degrees of lateral strength, resulting in isotropic parts. In terms of precision and accuracy, FDM technology still struggles with very fine detail, especially for complex parts.
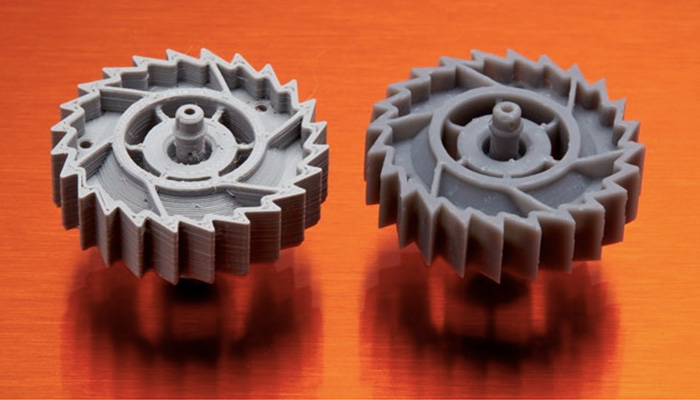
FDM 3D printed part (left) and SLA 3D printed part (right). In terms of geometric complexity, SLA technology is more precise and accurate | Credits: Formlabs
As you may know, once the part has been 3D printed, the final step in the 3D printing workflow is post-processing. During this step, SLA parts always need to be rinsed in isopropyl alcohol (IPA) or alternative solvents to remove any uncured resin from their surface. Some also require post-curing, which provides the part with higher strength and stability. The FDM process does not require cleaning. Additionally, both FDM and SLA parts can be machined, primed, painted and assembled for specific applications or finishes.
From an investment perspective, it is undeniable that FDM 3D printers are more affordable than SLA 3D printers, the former is available for only a few hundred dollars. This is very attractive for makers, hobbyists or small companies that can try the technology at an affordable price. Of course, professional FDM printers exist, and prices are significantly higher, between 2,000 EUR and 8,000 EUR. For this price range however, these machines compete directly with SLA 3D printers which start around 3,000 EUR. For example, Formlabs offers the Form 3L, the only accessible large scale SLA 3D printer, just below 10,000 EUR. Some affordable SLA 3D printers have emerged, however they are limited by their small build volume, which used to be an important limitation in general with SLA 3D printing. Today, it is possible to create large parts on an SLA 3D printer, as demonstrated by the Form 3L from Formlabs, which boasts a build volume of 300 x 335 x 200 mm.
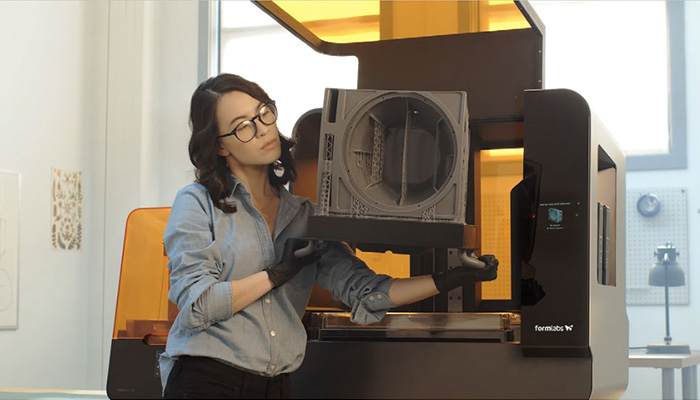
The Form 3L from Formlabs delivers large parts, it uses Low Force Stereolithography (LFS) to scale up to a larger print area built | Credits: Formlabs
How can you benefit from both technologies?
FDM and SLA 3D printers both have similar, often complementary features. Many companies actually invest in both technologies, which demonstrates that contrary to some beliefs, these technologies are not always competing. The rationale behind investing in both technologies is that you can benefit from the best of both worlds: low-cost rapid prototyping, coupled with high quality, functional parts for a wide range of applications.
A concrete example is the Third Thumb project, created by Dani Clode in collaboration with The Plasticity Lab in the Institute of Cognitive Neuroscience at University College London (UCL). The project is a prosthetic thumb controlled by the user’s foot, ultimately trying to improve the usability and control of prosthetic devices. The thumb is composed of both SLA and FDM components.
Dani Clode explains: “The thumb itself is FDM printed flexible thermoplastic polyurethane, with a low print fill. FDM flex is hard to work with, but it is the best option for the thumb at the moment. It also makes it light and strong. The fingertips are Formlabs elastic, and that’s because I need a high-resolution flexible material that can be printed thin, hold its shape and grip nicely. I also love that it can be secured easily to my other materials, unlike silicone. SLA is the only printing method that can handle my intricate internal piping to control the thumb.”
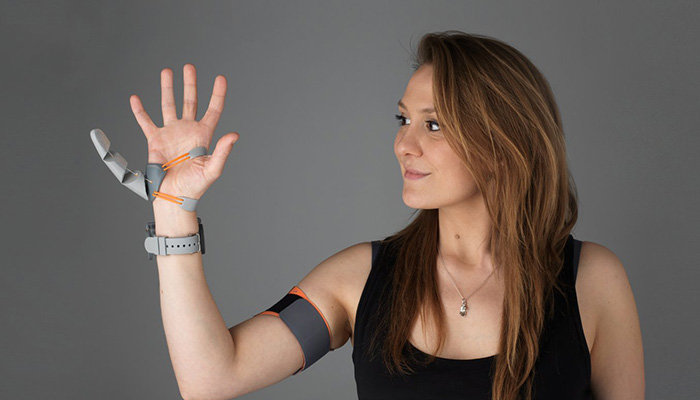
Dani Clode wearing the third thumb
As you will have been able to see, you can expand what’s possible with 3D printing by combining multiple technologies, playing to the strengths of FDM and SLA. If you are an FDM user you can grow your capabilities with an exclusive discount on Formlabs SLA technology! Learn more HERE.
Let us know what you thought in a comment below or on our Facebook and Twitter pages! Sign up for our free weekly Newsletter, all the latest news in 3D printing straight to your inbox!