OMNI3D on its Solutions and the Applications of Industrial 3D Printing
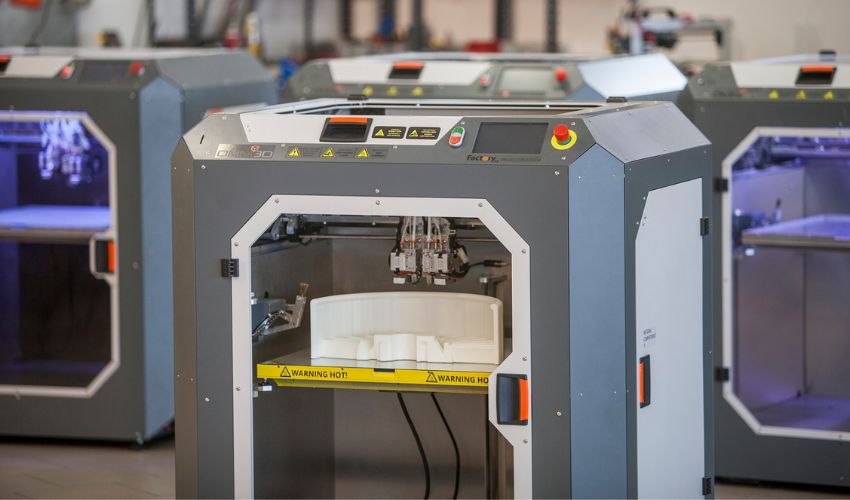
Over the past few years, the 3D printing market has steadily moved towards greater industrialization, especially as it continues to expand. Indeed a recent report from Research and Markets showed that the market value of additive manufacturing would increase to $44.03B by 2027 (an increase from $13.92B in 2021) and industrial 3D printers would hold a major share, explained perhaps as well by the growth in the production of end-use parts which is expected to increase. Moreover, just industrializing is no longer enough. Users are also seeking more precision as well as large-format 3D printing. This is an area where Polish 3D printer manufacturer OMNI3D truly shines. To learn more about the company as well as its solutions, we sat down with Paweł Robak, the CEO.
3DN: Could you introduce yourself and your connection to 3D printing?
My name is Paweł Robak, I have been the CEO of OMNI3D since May 2017. After graduating from the University of Economics, I started to work in finance as a CFO for over 20 years. As an enthusiast of the new technologies I decided to switch to the CEO position in one of the most promising Polish companies in Industry 4.0. OMNI3D was set up in 2013 and after the conceptual stage investors were looking for somebody who can develop strategy and put proper, scalable 3D printing solutions on the market.
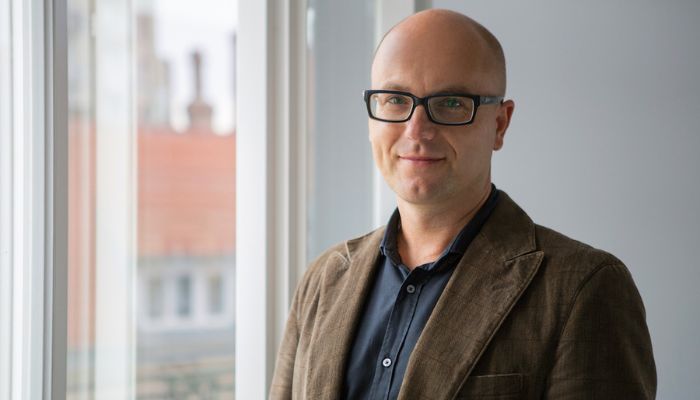
Paweł Robak, the CEO of OMNI3D
3DN: What is OMNI3D? How did the company come about? What is your mission?
OMNI3D initially was focused on delivering products to the B2C market, but during 2016 the concept was changed and the company has converted into B2B. The actual mission is to provide tools and complete ecosystems to create the most innovative and cost-effective products.
We want to deliver best-in-class 3D printing solutions in order to bring exceptional dimensional accuracy and stable prints. As the former CFO, I pride myself on delivering solutions that would increase the capital value of our customers by both significant reduction of production costs and increase of returns on investments.
3DN: Could you tell us more about the current rebranding of OMNI3D 3D printers? What does it mean for product development?
The problem we are facing now is the brand recognition on the world market. We are delivering on our promise to have these top solutions but still are not recognizable to a wider audience. Besides marketing tools which we have started to use in a regular manner to grow brand awareness, there is also a necessity to equalize brand and product names. We want to aggregate industrial products, both actual ones and new ones. All while also introducing new product lines for the educational sector which are less demanding than industrial grade ones. All products should have the OMNI3D brand.
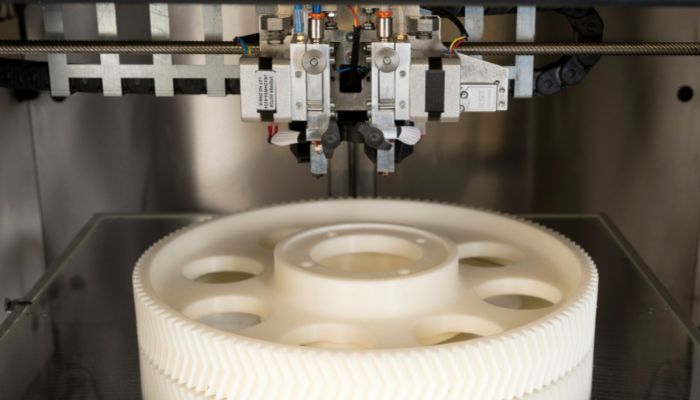
OMNI3D’s industrial solutions include double extrusion and the ability to print with difficult materials like ABS
3DN: OMNI3D is known for being a provider of an entire 3D printing ecosystem, what is your goal in providing this? What do you hope to achieve?
We have grown as a 3D printer producer but the real value comes from delivering process solutions. In our case it means to deliver pre- and post-processing tools, audits (consisting of analysis of a user’s situation, defining objectives, determining the savings involved in implementing a 3D printer and an estimation on the return on investment), a proper level of service and maintenance, as well as compatible materials. That’s why over 2022, the group has increased to include material producers and we have introduced dryers, washing machines, service packages to provide comprehensive solutions to our clients.
Moreover, in terms of our printing solutions, our 3D system creates a unique value for the user. In our team we have specialists who are at the constant disposal of our clients (experts from the print room, experienced service technicians). These are people who have been working practically since the beginning of the company, so their know-how is huge. That’s why we want to communicate not only as a supplier of equipment, but of the whole ecosystem. It’s the whole environment and the additional values we offer that make our offering truly unique and valuable.
Beyond that, we also highly value printing quality. Something that we have achieved thanks to a variety of different software features that are available for all users. For example, the OMNI3D Cooling System which allows users to control the temperature in the printing chamber throughout the printing process, crucial for printing with materials like ABS. Additional features include a platform auto-leveling system for fast and precise printing from the first layer or Filament Flow Control and Head leveling control to increase the repeatability of prints.
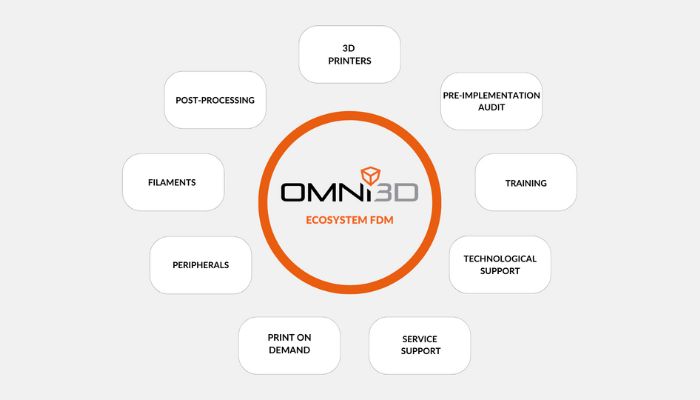
The OMNI3D ecosystem
3DN: What challenges or problems do your machines address and solve?
The range of applications we are able to cover is very wide. As a matter of fact we are currently delivering to all sectors including aerospace, automotive, defense, or electronics. We are constantly developing a material portfolio which is compatible with our system, therefore the spectrum of problems we are able to resolve increases every month. The historical focus was to deliver large ABS parts (above 450 mm in each axis) with the accuracy reaching above 100 micrometers. Actual mainstream is to deliver stable solutions to maintenance departments eg. spare parts, production tools or final parts from CF PA12, PEKK, PC ABS or ESD certified specifically to the railway industry. Still though, even as we develop, we remain focused on creating large-format, precision parts. Addressing the needs of all our customers.
Because of our large chamber we were reached by Victor Engler, founder of SUPERQUAD SLOVAKIA s.r.o who wanted to print world’s first SUPERQUAD – ENGLER F.F. The Factory 2.0 NET was able to make the prototype body using ABS+PC material. Now, the company is considering using it for mass production. Another customer of ours, printed durable parts using CF PA-12 to replace his steel tooling, shortening lead time from 4 weeks to 1 day and reducing production costs by 91%. We also pride ourselves on working with demanding industries – for example, the Volkswagen Factory in Poland, made heat- and chemical-resistant parts for their robotic arms using our printer and THERMEC™ ZED material, which in this case was necessary due to exposure of parts to corrosive substances.
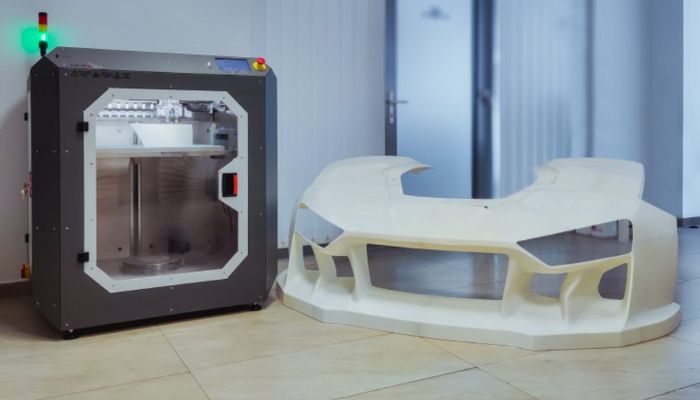
The Factory 2.0 NET 3D printer was used to help create the front of a car
3DN: You will have a new 3D printer soon, could you tell us more about it? Who is the target?
As the range of applications grows dramatically we have to follow the natural trend of development of our systems. We want to keep the big chamber we are well known for, but the actual development of the new materials will also increase the drive to produce and install systems which will be more sophisticated with less opportunity to make mistakes by end users. At the same time we can see that there is still a lack of sufficient knowledge on how to prepare models for 3D printing and how to use the systems properly. In such an environment we want to deliver a new solution with the possibility to cover 98% of existing materials, keeping accuracy and repeatability at the highest levels with an easy to use interface at an affordable price. The new system will be dedicated to the most demanding sectors, such as defense and transportation, with additional value to printing on demand bureaus.
3DN: Any last words for our readers?
I’m more than pleased to announce that we will be celebrating the 10 year anniversary of OMNI3D with our esteemed investors in May this year. At this point I also want to thank all my colleagues and partners for very extensive work, especially in the last two years during which our company almost doubled in growth even despite such unpredictable and hostile macroeconomic conditions. You can find out more about OMNI3D HERE.
What do you think of OMNI3D and its industrial 3D printing solutions? Let us know in a comment below or on our LinkedIn, Facebook, and Twitter pages! Don’t forget to sign up for our free weekly Newsletter here, the latest 3D printing news straight to your inbox! You can also find all our videos on our YouTube channel.
*All Photo Credits: OMNI3D