The Faces of Additive Manufacturing: Olaf Diegel
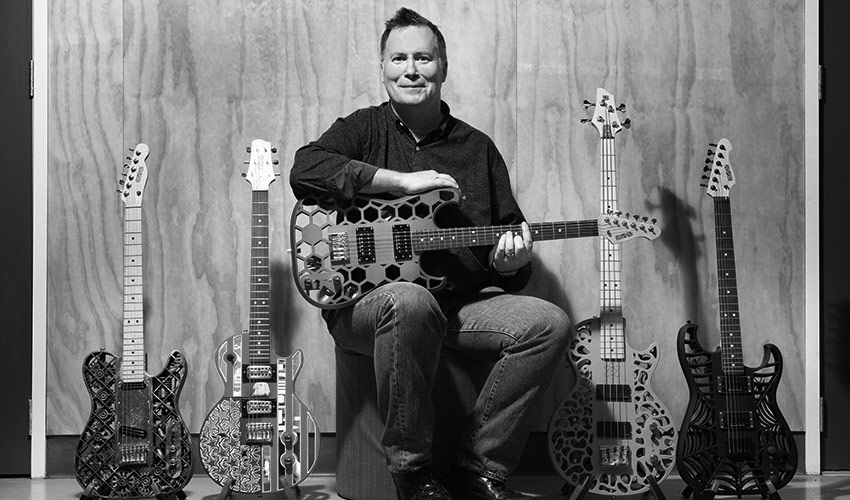
Our so-called The Faces of Additive Manufacturing series focuses on the pioneers who have shaped today’s 3D printing industry. Following our last portrait of Terry Wohlers, famous for his annual reports on the sector, we were present to you Olaf Diegel, Professor of Additive Manufacturing at the University of Auckland. Olaf Diegel understood several years ago the potential of 3D printing for the design of complex parts, whether for musical instruments, medical prostheses or jewellery. 3Dnatives went to meet him to learn more about his vision of the sector.
3DN: Could you introduce yourself and your work in regards to AM?
I am currently a professor of additive manufacturing at the University of Auckland, in New Zealand, where my area of expertise is in designing for additive manufacturing. Previous to this, I was heavily involved in product development, both in research on how to bring better products to market faster, and as a practitioner where I helped companies with their product development from finding a problem to be resolved or a market/user need, to the detailed engineering design, to the manufacturing and getting the product out to market. Over my career, I have brought well over 100 products to market in areas including theatre lighting products, home health monitoring products, marine products, musical instruments, etc.
It is this work in product development that first got me interested in additive manufacturing (or rapid prototyping, as it was known at the time). This was in the mid-90s where I would use AM strictly as a prototyping tool to test that my designs would work before investing a lot of money in production tooling. But then, as the technologies evolved over the years, I started to get more and more interested in how to use AM for production, rather than just for prototyping.
The more I got involved in AM, the more I realized that, because AM technologies are relatively slow and expensive, it was not commercially viable to manufacture AM parts that were not specifically designed for the technologies. This got me started on figuring out the best techniques to make parts that could be printed faster (and cheaper), were substantially lighter than the original parts through techniques such as topology optimisation and lattice structures, or added functionality to the end product.
3DN: Could you tell us about one of your current project ?
Recently, we worked on a project with a local artist called Gregor Kregar. He normally works on enormous large scale art projects but, in this case he wanted to both explore the potential of AM for producing art, as well as the possibility of being able to produce smaller artworks. In this particular case, he wanted to play with the contrast of dinosaurs being inflatable, so appearing to be incredibly light, but then being as heavy as possible when they were picked up. So although we printed the dinosaurs as a “shell”, with a 2mm outer wall thickness, we left all the entrapped unmelted powder inside so make them as heavy as possible.
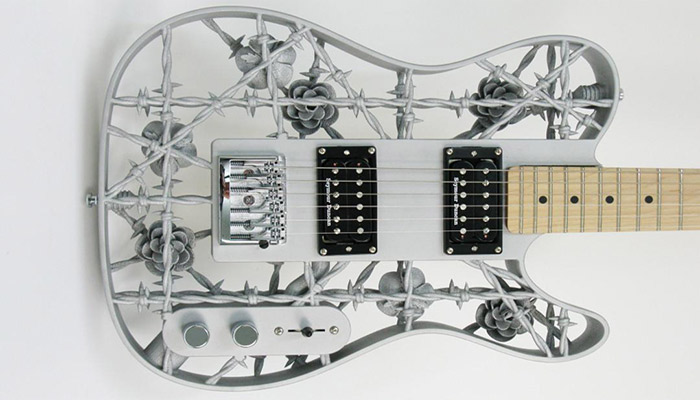
These « inflatable » triceratops were 3D printed in aluminium (AlSi10Mg) on an EOS M290 machine
It’s one of the coolest things in our Lab in that we get to work with everyone ranging from hard-core engineers to artist with the craziest ideas. Often, it’s the artists that push the technologies the furthest because they are not as bounded by what engineers know cannot be done, so they make us think about things and then figure out ways to do the impossible.
3DN: As a pioneer in the AM industry, can you give us an idea of what it looked like 10 years ago?
10 years is, in fact, a pretty good number to look at because that is roughly when some of the AM technologies evolved to the point where they could make full-strength parts suitable for production. Prior to that, almost all technologies were suitable mostly just for prototyping. Unquestionably, over the 20 years previous to that, the prototyping technologies did improve dramatically and went from just being cosmetic prototyping technologies to functional engineering prototyping technologies that really helped to accelerate the speed of product development.
Since then, almost every year we see some quite significant advancements in the technologies that are making them more and more suitable for a wider range of production needs. As machine speeds increase, and surface qualities and material properties continue to improve, I believe that we will see them used in a wider range of commercial applications by more companies that might not be considering them today.
3DN: What were the most crucial changes in the industry over the years?
I think the single biggest change in the industry occurred when some pioneering companies realized that the technologies had evolved to the point of being used to produce real parts. This would have required quite a mental shift in the company, and probably quite a bit of bravery to risk putting printed parts into a real product. So even though the technology itself had been improving gradually over the years, I think it was the mental shift that it could be used for production that was the catalyst to making AM what it is today.
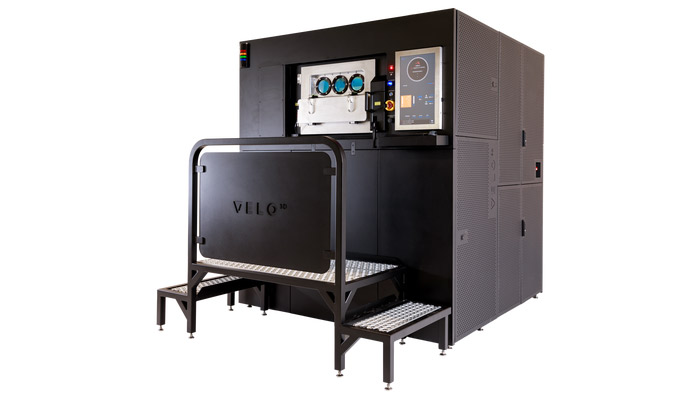
Passionate about music, Olaf worked on various 3D printed instruments, including guitars, drums or even a saxophone
3DN: Can you give us more details on the technologies and materials you think will experience most growth?
The technologies using material in powder form (metal and polymer powder bed fusion) are the ones most suitable for real production. This is, largely, because most of the current photopolymer based technologies are cured by UV light, and therefore sensitive to ambient UV so do not age well (although there are exceptions to this). Once the chemist figure out how to make these polymers cure into a permanent plastic, then these could become very interesting technologies from a product development point of view because of their ability to do multi-materials and functionally graded materials. This could help to create an entire new type of products that takes advantage of such new materials that are not possible today.
3DN: What are the remaining challenges to the global adoption of AM and how are they addressed?
Today, I believe that the single biggest challenge is that the majority of designers and engineers do not yet know how to design for AM (DfAM). Most companies that come to our lab arrive with a part that was designed for machining or injection molding and ask us if we can print it for them. We tell them that, yes, we can but they then have a mild heart attack when we tell them the price. This is because all AM technologies are, today, relatively slow, and the parts they make are therefore very expensive, so can only be used for the very highest value products. However, with good design for AM, prices can be reduced substantially (often by up to 80% or 90% compared to a part that was not designed for AM) while, at the same time, greatly improving the functionality of the part by, for example, making it 70% lighter, or reducing the number of components in the design.
Yes, absolutely, as the AM technologies become faster, adoption will increase at an ever growing pace but good design for AM practices just lower that barrier to adoption much more quickly.
It is really good to see that, particularly over the last 2 years, we have started to see a growing number of DfAM courses to remedy this education problem. But what we are not quite seeing yet is university curricula building this into their general manufacturing courses so that graduates come out of the university knowing how to design for AM (or at least knowing that they need to design differently for AM than for other technologies). It’s starting to happen, but just a bit more slowly than I would like to see…
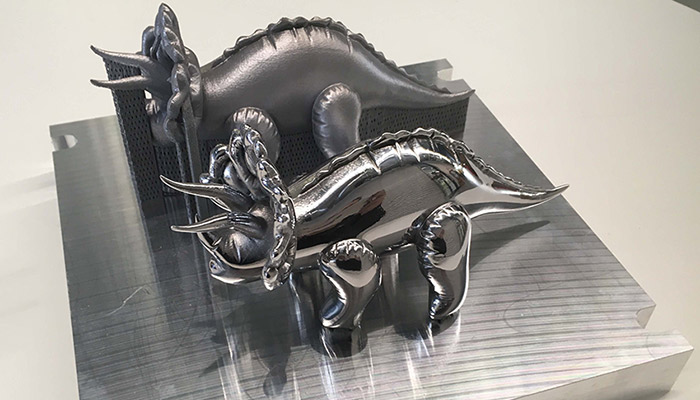
Velo3D’s machine to be able to print metal parts that are free-floating manufacturing
3DN: Finally, have any news, companies, technologies or applications caught your eye in the last few months?
Probably the two technologies that have excited me the most over the last year are the potential of Velo3D’s machine to be able to print metal parts that are free-floating in the metal powder, with no support material at all (or with very low support angles), and EOS’s LaserProFusion technology with an array of a million laser diodes to melt to polymer powder as this has the potential to greatly increase the speed of the printer.
But, as with the care we always have to take with all the marketing hype in the industry, the proof will be in the pudding once these new technologies start to get tested by real users on real parts.
*Credits Cover Image: Dean Carruthers/University of Auckland
What do you think of Olaf Diegel’s vision of the market? Let us know in a comment below or on our Facebook and Twitter pages! Sign up for our free weekly Newsletter, all the latest news in 3D printing straight to your inbox!