Improving Safety and Sustainability in the Oil and Gas Sector With 3D Scanning
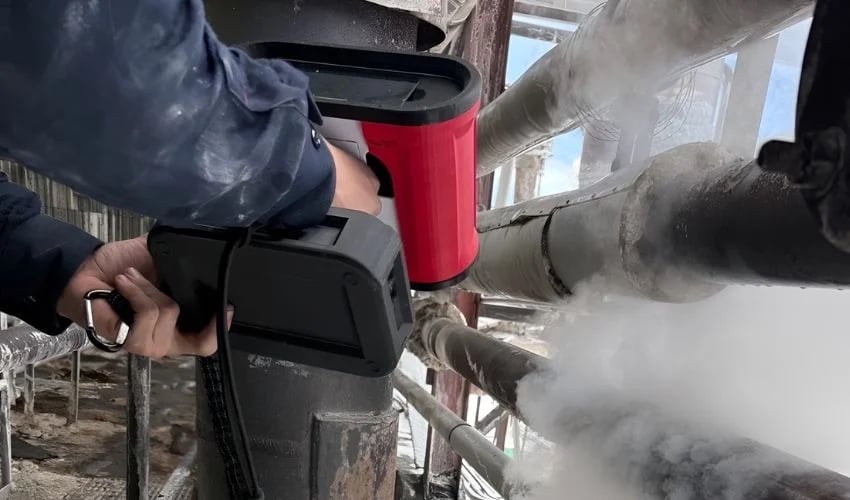
The oil & gas industry faces many challenges, notably a growing need to reduce emissions. Companies in the sector have set themselves ambitious targets for 2025, at a time when environmental concerns are becoming increasingly evident. To contribute to this reduction, some are turning to cutting-edge technologies such as 3D scanning.
The Colt Group is a good example: the company has invested in 3D scanning solutions to react quickly to leakage problems, improve on-site performance and safety, and meet its environmental commitments. Thanks to the Artec Leo 3D scanner, the company can speed up repair planning by up to 18 times, and scan complex pipes in less than 20 minutes, whatever the working environment. A new application that clearly demonstrates the added value of 3D scanning!
First, let’s take a step back via a recent study published by Rystad Energy. It analyzes the CO2 emissions reduction strategies of 120 companies in the oil and gas sector. Their activities emitted over 630 million tonnes of emissions in 2024.
For many of these companies, 2025 is a pivotal year, as this is the milestone they have set themselves for achieving their targets. While some have succeeded in lowering their targets, others are still struggling to achieve the desired results. Decarbonization is a major strategic issue in the oil & gas sector, and it has become very difficult to ignore the concerns it raises.
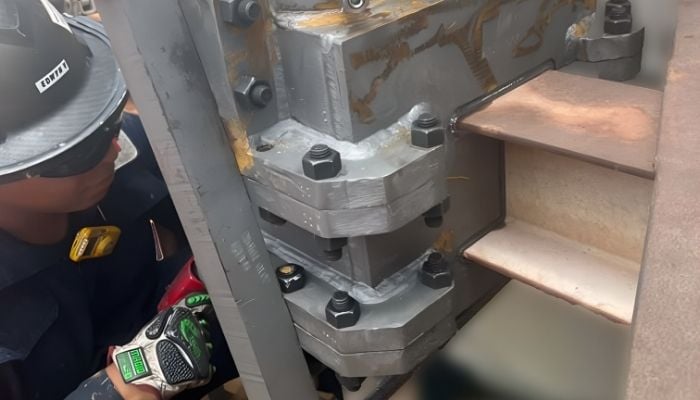
Thanks to the Artec Leo 3D scanner, teams can scan complex pipelines in less than 20 minutes.
It is against this backdrop that the Colt Group has invested in 3D scanning: specializing in leak repair, the American company provides design, manufacturing and mechanical services to keep their customers’ equipment running smoothly.
In concrete terms, the Artec Leo 3D scanner enables Colt Group’s teams to scan defective pipes directly on site, as opposed to using 2D drawings. The manual sketches previously made were not as accurate as the scans obtained. What’s more, these scans are much quicker to obtain and highly accurate, whatever the shape of the pipe. According to Colt Group, field crews can complete a scan in 15 to 20 minutes and send the data directly to engineers. This represents a huge time saving – the job is said to be done 18 times faster.
Wally Whitley is CIO of the American company, he explains, “We do ‘online’ leak repair. The faster we can do the job, the faster we can seal the leak for a customer, and decrease the likelihood of having to shut down. We’re also helping save our customers quite a bit of money by minimizing lost product and maintaining productivity. We keep them from having to shut down their process. The quicker we can do each step of our process, the more valuable we are to the customer.”
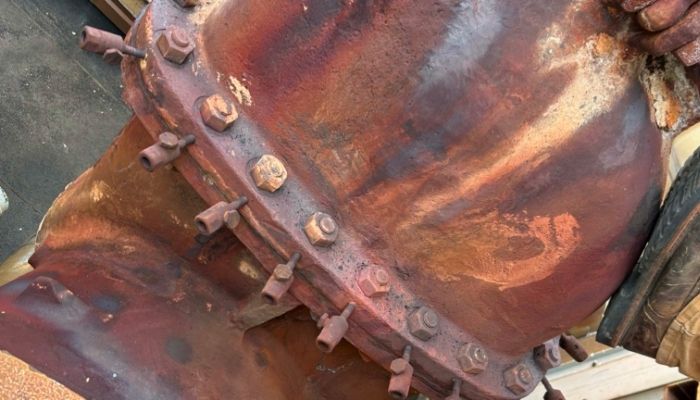
3D scanning delivers fast, accurate results, whatever the shape of the infrastructure
Colt Group is said to be able to digitize tens of thousands of parts a year, so it is easy to see the impact of 3D scanning on its work processes. Teams gain in flexibility, customers get an effective solution faster, and can count on equipment with a longer lifespan. For more information, click HERE.
What do you think of the role of 3D scanning in the oil and gas sector? Let us know in a comment below or on our LinkedIn, Facebook, and Twitter pages! Don’t forget to sign up for our free weekly Newsletter here, the latest 3D printing news straight to your inbox! You can also find all our videos on our YouTube channel.
*All Photo Credits: Artec 3D/Colt Group