3D Printing Unlocks Promising Solar Cavity Receiver Solution
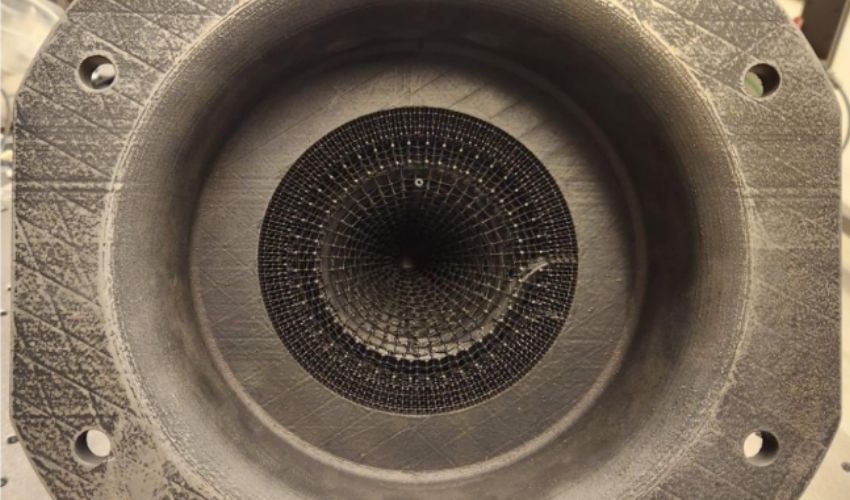
In solar energy production, a solar cavity receiver maximizes light captured from the sun, converting it into thermal energy. However, high-temperature solar receivers tend to distribute heat unevenly, causing thermal stress. This can lead to plastic deformation and a shorter lifetime for the part. To address this issue, three researchers from the King Abdullah University of Science and Technology (KAUST) in Saudi Arabia designed a solar cavity receiver to ameliorate how heat is distributed. What interests us is that 3D printing has played a vital role in the model’s development.
Current cavity receivers are designed with vertical tubes that do not allow heat to flow evenly. The non-uniform heat influx distribution and a temperature gradient between the front and back of the tube walls result in thermal stress. These issues are particularly pronounced in the case of gas solar receivers because of gasses’ lower thermal conductivity.
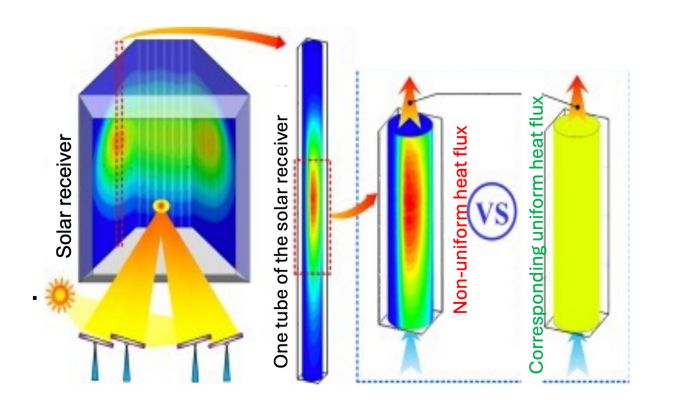
Current solar receiver with non-uniform heat distribution. (Image credits: International Journal of Heat and Mass Transfer 135 (2019) 732–745)
By contrast, the KAUST team’s model has a conical cavity receiver with a honeycomb lattice structure—entirely 3D printed. The device features a double helix heat exchanger, as opposed to vertical tubes, to reduce thermal stress, improving heat transfer and radiation trapping. This design enhances optical performance and facilitates radiation reaching the back of the helical tube. Heat is moved throughout the device’s inner tube because of pressurized air, which is heated by concentrated sunlight. Simultaneously, the honeycomb lattice structure regulates heat distribution, reducing thermal stress.
Why 3D Printing?
Using a DMP (Direct Metal Printing) Flex 350 Dual Laser machine, the KAUST team printed the receivers out of Inconel, a nickel superalloy commonly employed in environments with extreme temperatures and pressure. Ceramics had been used for high-temperature solar thermal research previously, but for the research team at KAUST, Inconel was a more attractive option. In an interview with SolarPACES, one of the researchers explained why: “The advantage over ceramic, which is more fragile, is that a metal can be scaled up to a large scale application,” KAUST Post Doc Fellow, Omar Behar. “so, it will be possible to scale up the technology and make it commercial.”
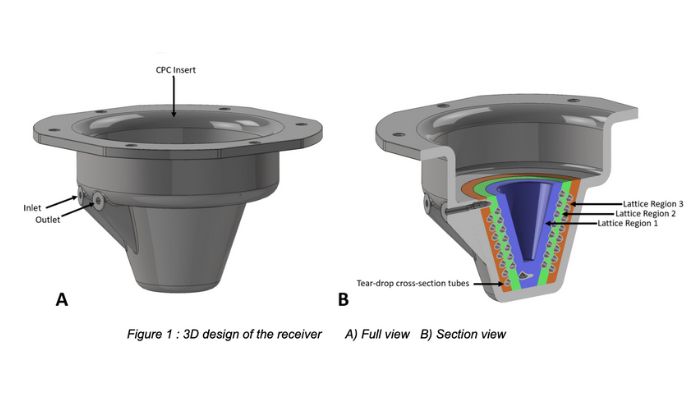
The new design features a conical design and three lattice regions (Image credits: KAUST)
In the same article for SolarPACES, Behard elaborated on why 3D printing was a game-changer for this design. “This mesh would be really difficult to manufacture using classical technology,” Behar said. “It’s like a honeycomb, that starts big and then it decreases slowly. So this design is difficult using the classic manufacturing process. The only way to do this is to manufacture it with a printed process.”
After printing, the solar cavity receiver was treated with a double-aging heat treatment, to ensure that the receiver was heat resistant to high temperatures. In all, the design was made to improve the thermal, optical, and mechanical performance of the solar cavity receiver. The results delivered, and the design allowed for significant improvements in heat distribution. According to the KAUST team’s report, “Simulation results indicate that the receiver operates efficiently at a maximum heat flux density of 230 kW/m², corresponding to the maximum working temperature of Inconel 718 (1000°C), while maintaining a low-pressure drop of approximately 170 mbar.”
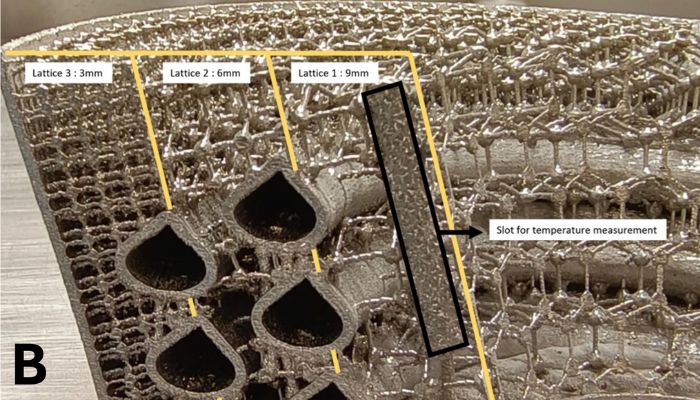
Photo credits: KAUST
Going forward, the KAUST team plans to test their work using KAUST’s High Flux Solar Simulator, capable of 8000 kWth at aperture. To learn more about the research, read their report here.
What do you think of 3D printing solar cavity receivers? Do you think the research is promising? Let us know in a comment below or on our LinkedIn, Facebook, and Twitter pages! Don’t forget to sign up for our free weekly Newsletter here, the latest 3D printing news straight to your inbox! You can also find all our videos on our YouTube channel.
*Cover Photo Credits: KAUST