NIST Announces Metal 3D Printing Breakthrough Which Could Help Spur Wider Adoption
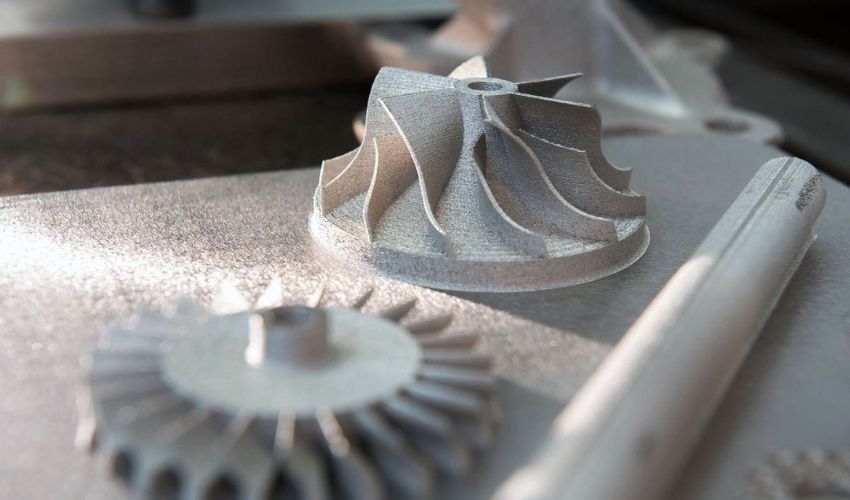
One of the biggest obstacles to widespread adoption of metal additive manufacturing is that we still have large gaps of understanding about what happens to the material during the process. More specifically, there are few tools which can show what happens to the internal structure of different metals as it is melted and then solidified during printing. However, this issue may be a thing of the past. The National Institute of Standards and Technology (NIST), KTH Royal Institute of Technology in Sweden and other institutions have announced a breakthrough in the ability to predict and control the characteristics of metal 3D printed parts. This has the potential to improve the technology’s consistency, making it more feasible to adopt it for large-scale manufacturing.
This is not the first time that NIST has shown interest in metal 3D printing. Just last year, not long after the Biden Administration launched its AM Forward Initiative, the institution awarded about $3.7 million in grants to address current and future barriers to adoption of metal additive manufacturing. These projects centered on addressing topics such as determining key material properties for quality control in AM as well as establishing data-driven frameworks for nondestructive qualification of AM materials and parts. The latter especially is a topic of some consideration as AM is being increasingly adopted for even security-critical applications in various sectors. This latest breakthrough seems to be operating within the same vein.
Turning to the Past to Improve Metal AM in the Future
The news comes on the heels of another announcement from NASA that it would be further investigating ways to improve certification and qualification for metal 3D printed parts. Indeed, this trend is one that has been a long time coming. 3D printing is only gaining in popularity thanks to its benefits in terms of lower costs and lesser waste. But issues surrounding qualification and continued consistency for part properties has made even wider adoption difficult. NIST hopes that this discovery could change that, as it will grant what they consider to be an unprecedented level of mastery over metal 3D printing. And to do this, they actually turned to the past.
The scientists knew that in order to guarantee material properties, there needed to be greater understanding surrounding what happened during the melting and cooling rates of metal within the printing process. Specifically, they needed to understand how the cooling rates of metal influence crystal structure. However, this has proven difficult to do as solidification occurs almost instantly, making it almost impossible to investigate. To get around this, the researchers used two different particle accelerator facilities to peer into the internal structure of steel as it was melted and then solidified during 3D printing. Powerful x-rays generated by particle accelerators at Argonne National Laboratory’s Advanced Photon Source and the Paul Scherrer Institute’s Swiss Light Source. These x-rays were powerful enough to capture images of the fleeting processes, testing the rate for temperatures ranging from tens of thousands to more than a million kelvins per second.
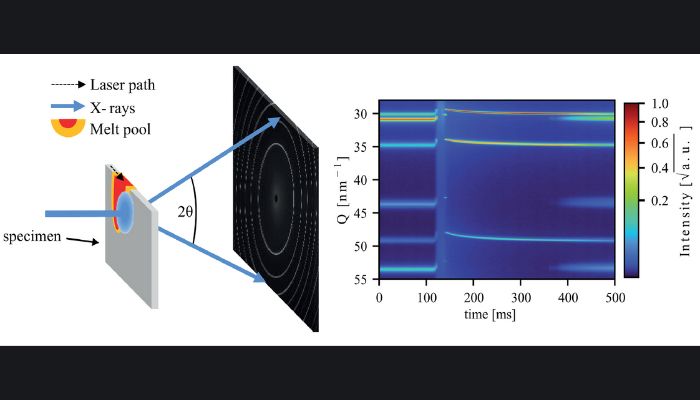
Researchers used high-speed X-ray diffraction to identify the crystal structures that form within steel as it is 3D printed (photo credits: H. König et al. via Creative Commons, adapted by N. Hanacek/NIST)
These results were then compared with a computational model that was developed in the ’80s that describes the solidification of alloys. This look into the past was not done for no reason either. This model is well trusted for predicting the properties of materials in traditional manufacturing processes, however up until this point it was not sure whether it would be applicable to metal additive manufacturing considering the rapid temperature shifts during printing. Incredibly, the researchers found that what they observed was also predicted in the model. This model has been a reliable tool for materials design in traditional manufacturing and now it seems that it could be used as well as a support for 3D printing. The press release mentions that the model could be used to inform scientists and engineers on the necessary cooling rates for the early solidification steps in the printing process. This will ensure that the optimal crystal structure will appear within their desired material, making metal 3D printing more reliable overall.
NIST physicist Fan Zhang, a study co-author, concluded, “Basically, if we can control the microstructure during the initial steps of the printing process, then we can obtain the desired crystals and, ultimately, determine the performance of additively manufactured parts. The model and the experimental data are nicely in agreement. When we saw the results, we were really excited. If we have data, we can use it to validate the models. That’s how you accelerate the widespread adoption of additive manufacturing for industrial use.” You can find out more in the research paper published in Acta Materialia HERE.
What do you think of this research from NIST? Do you think that metal AM will see even further widespread industrial adoption? Let us know in a comment below or on our LinkedIn, Facebook, and Twitter pages! Don’t forget to sign up for our free weekly Newsletter here, the latest 3D printing news straight to your inbox! You can also find all our videos on our YouTube channel.
*Cover Photo Credits: CCDC Army Research Laboratory