New Study Reveals Cause of the Formation of Bubbles Materials in DED Process
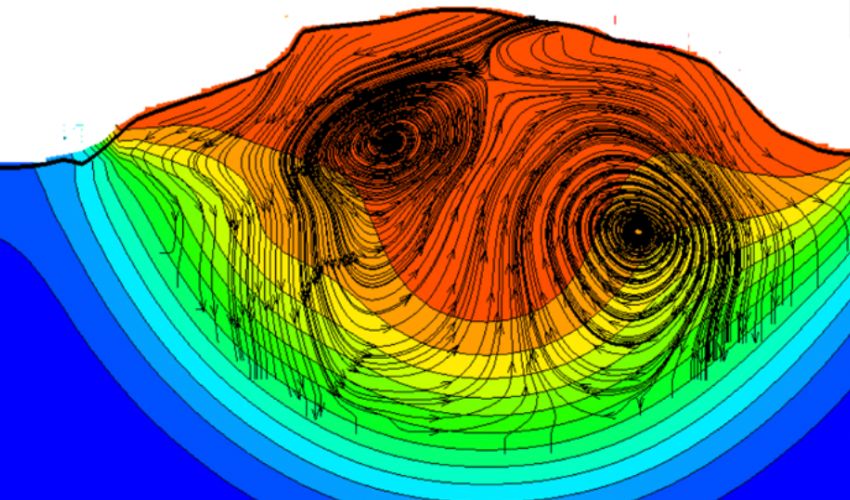
A 3D printing process that is particularly relevant for the repair or coating of metal objects such as damaged jet aircraft turbine blades is directed energy deposition (DED). It is widely used in sectors such as aerospace, automotive, shipping and biomedicine. The process works by melting materials in the form of powder or wire and applying them layer by layer to the surface of a workpiece. However, the formation of air bubbles in materials during the process can affect the long-term performance and service life, and consequently the safety, of parts. Thankfully, a new study has now investigated the causes of bubble formation during the process.
In order to improve the use of DED process in industry, Dr. Chinnapat Panwisawas at Queen Mary University of London investigated the cause of this porosity in materials, which could not be explained until now. The researchers succeeded in discovering five processes that lead to the formation, movement and growth of the bubbles or pores. The findings were made with the help of in-situ X-ray images, which were validated by multi-physics modeling, and which can now be used to develop strategies to reduce the bubbles in materials in DED in the future. Ultimately, the hope is that the study could result in improved technologies for regeneration and repair.
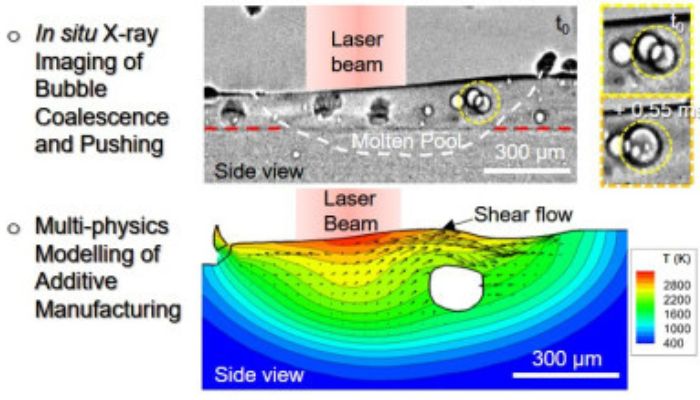
A graph showing the formation of bubbles in DED
How Do Bubbles Form During the DED Process?
The study provided explanations as to how the bubbles or pore-like unwanted structures develop in the material. It was found that the bubbles from the gas-atomized powder enter the melt pool, whereupon they begin to migrate laterally or circularly, leaving the individual bubbles to join together to form larger ones or be entrapped by solidification fronts. The bubbles, which have grown considerably in size, are able to remain in the melt pool for a much longer period of time. This is due to the fact that they are pushed by the solid/liquid interface.
Furthermore, the larger bubbles do not burst out as the shear flow on the Marangoni surface – which represents the movement of the liquid as the material melts and accumulates – prevents this. This ultimately leads to the rise of the large bubbles from the surface of the pool and the resulting pores in the material as the bubbles become trapped in the DED tracks. Dr. Chinnapat Panwisawas, Senior Lecturer in Materials and Solid Mechanics at Queen Mary’s School of Engineering and Materials Science, concluded:
“This knowledge is crucial for unlocking the full potential of DED. By minimising porosity, we can improve the mechanical properties of components, making DED a viable option for safety-critical applications ultimately leading to the production of stronger, safer, and more reliable components across various industries“
You can find out more in the study HERE. What do you think of this study on the formation of bubbles in materials in DED? Let us know in a comment below or on our LinkedIn, Facebook, and Twitter pages! Don’t forget to sign up for our free weekly newsletter here, the latest 3D printing news straight to your inbox! You can also find all our videos on our YouTube channel.
*All Photo Credits: Queen Mary University of London