A New Process Allows for Mass Production of 3D Printed Microscale Particles
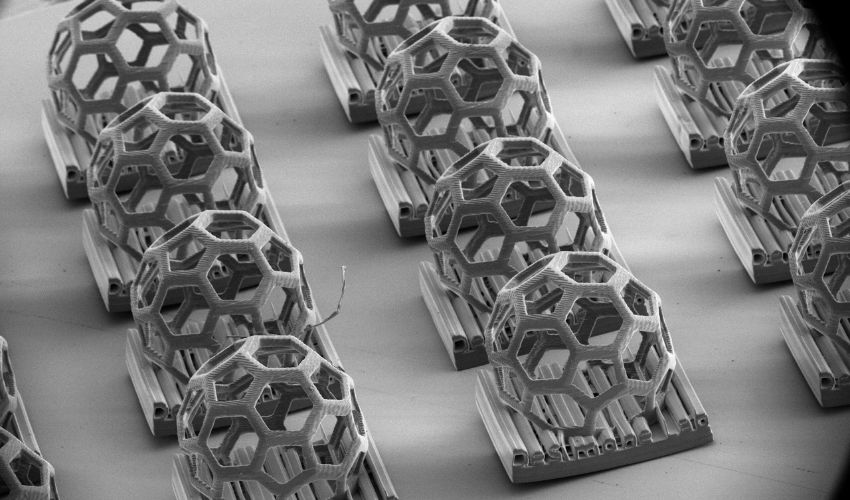
Over the past year, we have seen a number of major milestones in the field of microscale 3D printing. Now there has been yet another, as researchers at Stanford University in California have developed a new microscale 3D printing process for the production of particles in a variety of shapes. What is most notable about the new process is its exceptional speed, allowing for up to one million highly detailed and customizable particles to be produced efficiently every day.
According to a press release from Stanford, these 3D-printed microscopic particles are suitable for use in manufacturing, medicine and research. For example, they could be used specifically in microelectronics, microfluidics and as abrasives for complex manufacturing processes as well as for drug and vaccine delivery. The research was funded in part by the Bill & Melinda Gates Foundation and the National Science Foundation Graduate Research Fellowship Program.
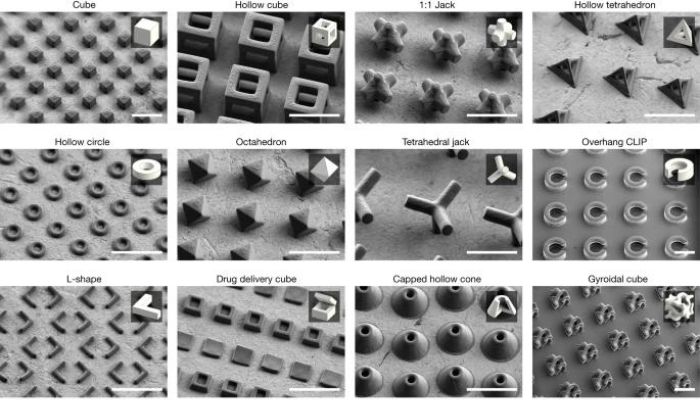
Geometries produced with r2rCLIP (image credits: Kronenfeld, Rother, Saccone, Dulay & DeSimone)
Until now, the production of such microscale particles has been exceptionally difficult. A very specific combination of light supply, resin properties and stage movement is required to produce the particles in a scalable manner. However, this new photopolymerization process provides a solution.
Joseph DeSimone, the Sanjiv Sam Gambhir Professor in Translational Medicine at Stanford Medicine and corresponding author of the paper, explains “Using light to fabricate objects without molds opens up a whole new horizon in the particle world. And we think doing it in a scalable manner leads to opportunities for using these particles to drive the industries of the future. We’re excited about where this can lead and where others can use these ideas to advance their own aspirations.”
A New Process for 3D Printing Microscale Particles
The microscale particle process builds off of “Continuous Liquid Interface Production” (CLIP), a fast resin process introduced by DeSimone and colleagues back in 2015 (and which you may have heard about as it was what Carbon’s own technology was based off of). This speed is made possible by the fact that sensitive structures can harden without having to tear off each layer from a window. This is thanks to an oxygen-permeable window above the UV light source, which creates a so-called “dead zone” that prevents the liquid plastic from hardening, thus preventing it from sticking to the window unintentionally.
However, the researchers wanted to use the process to produce a larger number of particles at once, up to 1 million highly detailed and customizable microscale particles a day, which previously involved manual work and a great deal of time. In order to adapt the existing process for the mass production of customized tiny particles, the researchers therefore created an extension called “roll-to-roll CLIP”, or r2rCLIP for short. The name is derived from the way the process works, which is similar to a conveyor belt. First, a film is stretched and transferred to the CLIP 3D printer, which then prints hundreds of structures on the film at once. After printing, the structures are washed, cured and removed on the conveyor belt before the empty film is rolled up again.
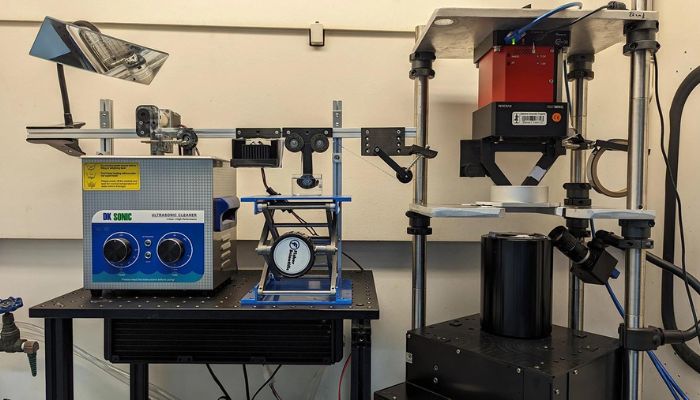
The r2rCLIP setup in the DeSimone lab (photo credits: DeSimone Research Group)
Jason Kronenfeld, the lead author of the paper, concludes, “We’re navigating a precise balance between speed and resolution. Our approach is distinctively capable of producing high-resolution outputs while preserving the fabrication pace required to meet the particle production volumes that experts consider essential for various applications. Techniques with potential for translational impact must be feasibly adaptable from the research lab scale to that of industrial production.” You can find out more in the press release HERE.
What do you think of this new microscale resin 3D printing process for particles? Let us know in a comment below or on our LinkedIn, Facebook, and Twitter pages! Don’t forget to sign up for our free weekly newsletter here, the latest 3D printing news straight to your inbox! You can also find all our videos on our YouTube channel.
*Cover Photo Credits: DeSimone Research Group, SEM courtesy of Stanford Nano Shared Facilities