Researchers develop a new method of 3D printing with latex
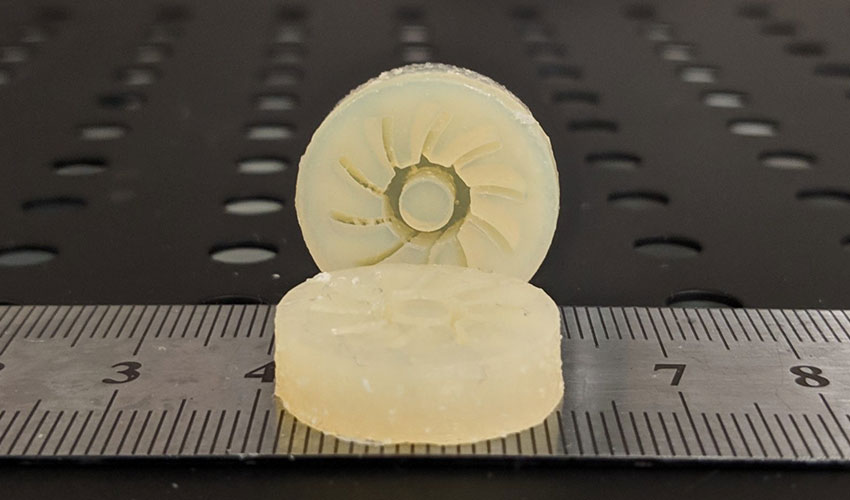
Widely used in different industries, latex is the most flexible material known so far. It has a natural origin and is composed of long polymer chains rolled into water-dispersed nanoparticles. Although, in general, latex is very well known, little has been said about it within the additive manufacturing context, as very precise characteristics are needed to be able to print with this material. This week a group of researchers from Virginia Tech University (VTU), in collaboration with the team from Michelin North America, have developed a new method for 3D printing with latex, which opens the way for printing with more elastic materials.
Phil Scott, a fifth-year student at the Long Research Group and part of the research team, had been trying for some time to synthesize latex to achieve the molecular weight and mechanical properties needed for 3D printing. By using liquid latex, he realized that the material that was extremely brittle and difficult to alter chemically.
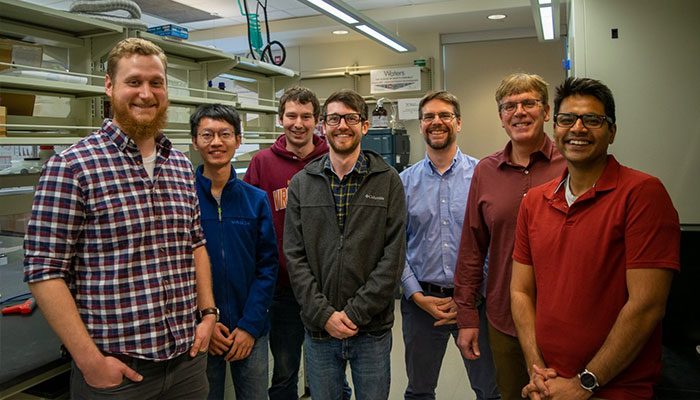
Chemists and engineers of the project’s research group. (Image credits: VTU)
“Latex is in a Zen state,” explained Viswanath Meenakshisundaram, a PhD student in mechanical engineering who is collaborating on the project. “If you add something to it, it will completely lose its stability and break.” To address the issue, the VTU team used water-soluble network precursors (photoinitiators) to create a tunable scaffold, surrounding the latex particles and allowing them to fuse together. This technique was successful and resulted in a latex variant that can be used in stereolithography.
The new technique of 3D printing with latex
Once the latex was chemically modified to become 3D-printable, a new 3D printer, capable of manufacturing with the new material, had to be developed. So, Meenakshisundaram set to work and developed an SLA machine to light-cure the new resin. But even with the custom 3D printer, the fluid particles of latex caused dispersion outside of the UV light projected on the surface of the latex resin, resulting in inaccurate parts being printed. Hence, the team had to improve and modify the machine: they inserted a camera into the printer to capture an image of each vat of latex resin. With its customized algorithm, the machine can “see” the interaction of ultraviolet light on the resin surface and then automatically adjust the printing parameters to correct the resin dispersion and cure only the desired shape.
“The scaffolding gives it shape. Once you put it in the oven, the water will evaporate and the tightly wound polymer chains can relax, spread out or flow and interpenetrate the net,” said Meenakshisundaram, who described this interpenetrating polymer net as “catching fish in a net”.
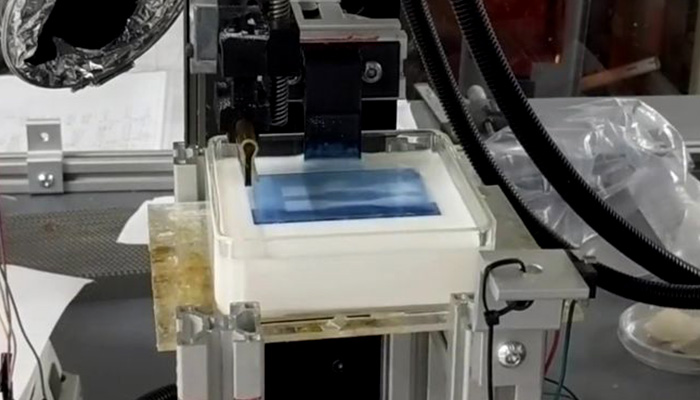
Steriolithography technique for 3D printing with latex. (Image credits: VTU)
To test its functionality, the VTU team 3D printed a series of light-cured latex objects. The samples were 3D printed in great detail and showed substantially improved strength over the existing latex materials, exhibiting elongations in excess of 500%, with an average breaking strength of 9.7 MPa.
The two other researchers of the project mentioned that the development of the new technique of 3D printing with latex actually opens the door to 3D printing with an unprecedented range of materials: “This work expands the opportunities for printing elastomers with complex characteristics that exhibit extensibilities greater than 500%, almost 200% above the leading commercial elastomers,” concluded the VTU researchers. More information about the project can be found on the university’s official website HERE.
What do you think about the new technique of 3D printing with latex? Let us know in a comment below or on our Facebook and Twitter pages! Sign up for our free weekly Newsletter, all the latest news in 3D printing straight to your inbox!