Nesting in 3D Printing Helps Optimize Space
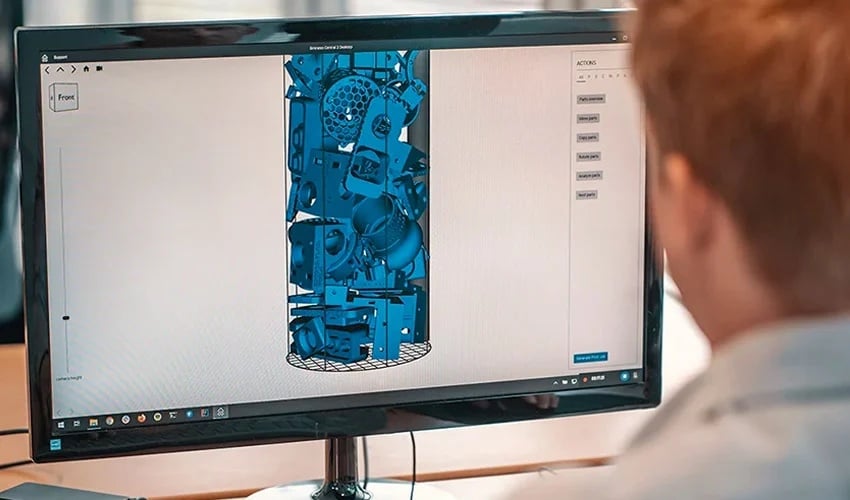
Modeling is a key step in additive manufacturing, especially when it comes to the creation of complex parts. In the 3D printing sector, there are a number of CAD programs available for 3D printing. With a growing market, players in the sector need to reduce their production times, while saving materials and without compromising part quality. The question is: how can 3D-printed products be produced faster? The answer is simple: simply increase the number of parts produced in a single print run. This is where nesting software comes in to optimize this stage of the 3D printing process.
Nesting software has a fairly straightforward role. It is used to achieve maximum savings in materials and part production time. Indeed, in and of itself the software is not considered to be CAD software, as it does not allow you to design a model. Instead, its role is to optimize the placement of parts on the printing bed to achieve the maximum parts per printing volume in a single run. Whether automated or manual, 3D nesting sorts, orients and organizes 3D files to maximize space inside a 3D printer, without interfering with non-manufacturing areas.
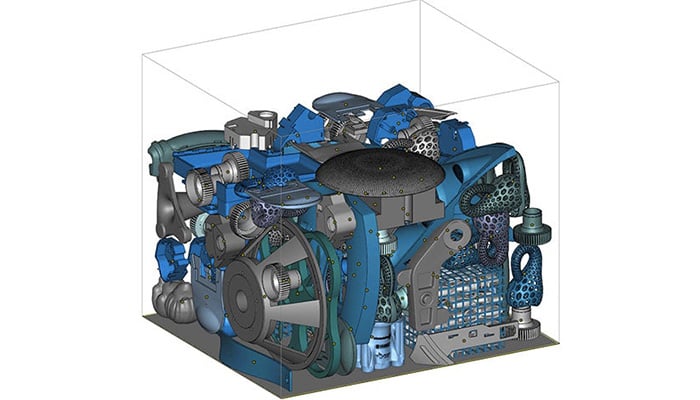
Parts are positioned and oriented to optimize space in the 3D printer (photo credits: Materialise).
However, inefficient use of nesting can lead to material wastage and printing errors. Nesting software in 3D printing thus works like the video game Tetris, where the aim is to place each block in a very specific square to optimize space on the game board. It is now increasingly available in CAD solutions as an additional design option. Some of the solutions available on the market include Sculpteo’s Fabpilot, CoreTechnologie’s 4D_Additive and Autodesk’s Fusion 360 and Inventor Nesting. Most nesting solutions are extensions to CAD software.
This method works with almost all 3D printing technologies. It’s important to note, however, that 3D nesting is more advantageous for processes that use powder and don’t require support structures. Thus, 3D printers that benefit from PBF solutions, such as DMLS, SLS, or Multi Jet Fusion will be more useful. Sintratec, a manufacturer of SLS 3D printers, has confirmed the advantages of this software with a selective laser sintering 3D printer. In fact, according to Sintratec, nesting saved 800 hours of part production, 47 kg of powder and 50 hours of labor on 100 printing jobs carried out by the company. This technique aims to increase the productivity of companies in the 3D printing market, while saving on materials. Binder jetting is another technology used for nesting. However, the powder bed fusion process is preferred.
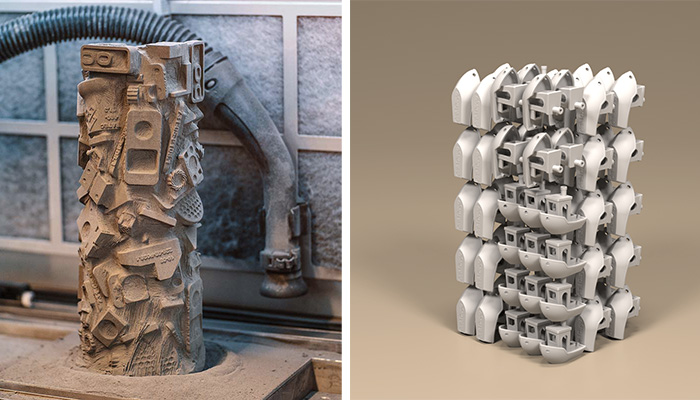
Nesting is most efficient with powder-based technologies
All materials used with these 3D printing techniques can be used with nesting software. It is therefore possible to take advantage of the 3D nesting method with metal, nylon, PEEK, polypropylene or resin. For technologies such as DLP and MSLA, 3D nesting can also be used. However, nesting does not save materials, it only saves considerable time in the creation of parts. Logically, nesting in 3D printing is compatible with all types of 3D printers. However, the vast majority of the software will be used on professional and industrial machines, due to their greater manufacturing volume. Nesting for 3D printing can also be used in the automotive, medical and aerospace industries. In fact, nesting is capable of addressing all the sectors that 3D printing technologies are capable of touching. Additionally, nested parts are not necessarily all the same, depending on the customer’s requirements. They can be of different shapes and sizes.
Mistakes to Avoid With 3D Printing Nesting Software
When using 3D nesting software, there are some important details to pay attention to in order to avoid printing errors. First of all, in automated or manual nesting, it’s important to leave at least a 1.5 mm gap between all the components in your 3D file with SLS techniques, and a 5 mm gap with MJF processes. The heat generated by 3D printers will prevent the parts from fusing during the printing process. Then there’s what we call interlocking rings. This problem arises when the software doesn’t respect the structure of two ring-shaped parts, and the elements cross or bind together. The two parts become useless. The third error is to print a small object in the open space of a larger part, making it impossible to extract. The user must therefore provide a small opening to facilitate removal of the two components. However, even if these errors are avoided, the nesting process must not undergo radical changes to avoid the risk of curling. This 3D printing phenomenon occurs when the print layers don’t stick together properly, resulting in curved edges or misaligned layers.
What do you think of nesting? Let us know in a comment below or on our LinkedIn, Facebook, and Twitter pages! Don’t forget to sign up for our free weekly Newsletter here, the latest 3D printing news straight to your inbox! You can also find all our videos on our YouTube channel.
*Cover Photo Credits: Sintratec