NASA Engineers on the Importance of Metal Additive Manufacturing for Propulsion
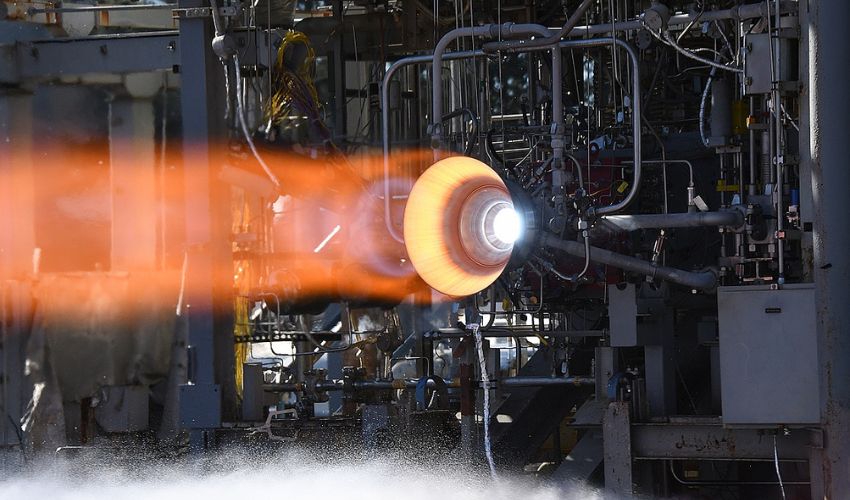
For some time now, NASA has been using 3D printing for everything from prototyping to end-use parts. In fact, it’s use has become so widespread, that the organization is becoming one of the leaders in research into the use of metal additive manufacturing especially for a variety of applications. This has been proven as well by a book released by four employees of NASA that aims to guide the adoption of metal AM specifically for propulsion applications. Aptly named Metal Additive Manufacturing for Propulsion Applications, we spoke to the authors to learn more about the use of metal 3D printing at NASA as well as what readers can expect in the book itself. Note as well, that you can register HERE for our giveaway where 10 lucky winners will receive their own free copy of the book (until June 10th).
3DN: Could you introduce yourselves and your connection to 3D printing?
We are all employees of NASA Marshall Space Flight Center in Huntsville, Alabama, United States. Paul Gradl is a principal engineer working the design, development, analysis, manufacturing and testing of liquid rocket engines. He serves as a principal investigator for several projects focused on metal additive manufacturing (AM) using new processes, novel materials, and design complexities for rocket engines. He has worked in additive for nearly two decades with some of the early powder bed fusion machines and has collaborated with various commercial partners to evolve several metal AM materials and processes into flight.
Omar Mireles is an additive manufacture research and development engineer. He serves as principal investigator for numerous additive manufacturing R&D projects including refractory metal additive manufacture maturation efforts, and infusion of additive manufacture into propulsion, cryogenic fluid management, and space nuclear power and propulsion systems. He has over 20 years of experience in design, manufacturing, post-processing, materials characterization, and testing.
Christopher Protz is the advanced manufacturing lead where he coordinates the research and development of terrestrial and in-space manufacturing technologies for NASA. He has led several additive projects including the Low-Cost Upper Stage Propulsion (LCUSP) project to design and test NASA’s first full-scale bimetallic additive combustion chamber starting in 2014.
Chance Garcia is the Deputy Chief Engineer for NASA’s human lander system at Marshall Space Flight Center. He has experience with propulsion systems development for design, analysis, manufacturing and testing of additive components. He is a graduate of the University of Texas at El Paso, the International Space University Studies Program and an advisor and session chair for various STEM activities and propulsion conferences.
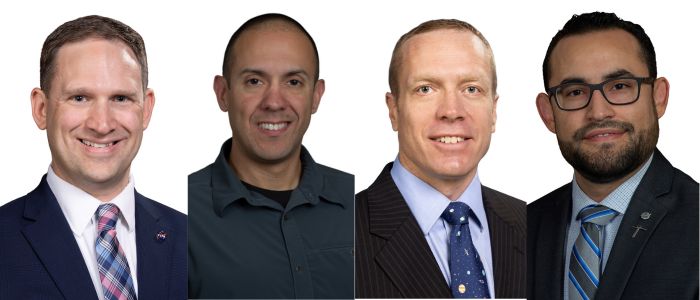
From left to right: Paul Gradl, Omar Mireles , Christopher Protz and Chance Garcia
3DN: How and why does NASA use metal additive manufacturing?
NASA is actively employing metal additive manufacturing (AM) across a wide range of missions, including launch vehicles, satellites, in-space, and collaborations with industry and academia partners. This encompasses both non-critical AM parts deployed during the Artemis I mission and critical components like the pogo Z-baffle on the RS-25 engines for future Artemis endeavors. Numerous components in rocket engines leverage metal AM, such as injectors, combustion chambers, nozzles, ignition systems, valves, housings, and turbomachinery. Additionally, NASA has successfully utilized metal AM for AM cubesats, satellite components like thrusters, the oxygen generator for the Mars Perseverance rover, and ongoing investigations into life support components for the International Space Station (ISS).
These components, whether utilized in rockets, rovers, or satellites, often exhibit long lead times and are composed of challenging-to-machine (or join) alloys. By embracing AM, NASA achieves substantial reductions in lead time, costs, and part count, while also unlocking unparalleled design freedom that was previously unattainable through traditional techniques. This design freedom enables performance enhancements, such as weight reduction, improved heat transfer, and enhanced flow capabilities.
Furthermore, additive manufacturing offers the ability to iterate designs through rapid prototyping and rigorous testing in actual rocket engine operating environments. While metal AM may not always be the ultimate process for full production, it serves as a crucial tool within the iterative design-fail-fix loop, guiding the development of final production designs. The commercial space industry is experiencing a significant infusion of various metal AM processes and materials as NASA continues to push the boundaries of additive manufacturing and drive innovation within the sector.
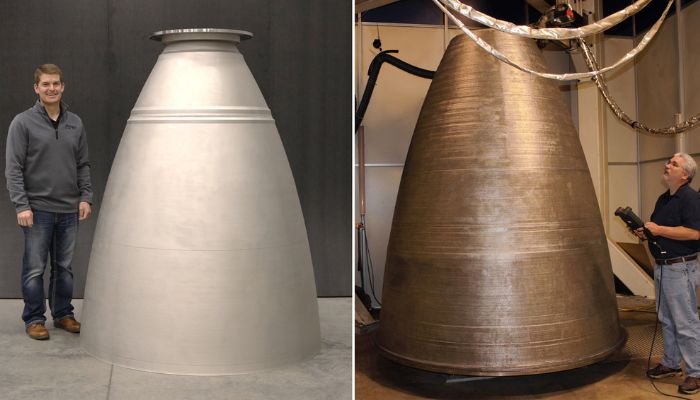
A metal part made by NASA using additive manufacturing
3DN: Could you tell us more about Metal Additive Manufacturing for Propulsion Applications?
The realization of our book has been a long-standing vision, and we believed the time had come to transform it into reality. While the realm of metal additive manufacturing (AM) holds a wealth of exceptional research, we felt there was a dearth of practical insights and implementation guidance. Over the course of well over a decade, NASA has been building and testing parts, experiencing failures during builds (including some parts on the test stand), and providing mentorship to others venturing into metal AM. “Metal Additive Manufacturing for Propulsion Applications,” published by AIAA, aims to serve as a comprehensive guide for both novice users and seasoned designers, technicians, and engineers embarking on their AM journey. By delving into the fundamentals intertwined with design and implementation, the book offers insights and examples specifically tailored to propulsion applications, while acknowledging their broad applicability across diverse industries.
Our intention was to equip readers with the knowledge to make informed decisions in selecting the appropriate process for metal AM. We provide an overview of the most commonly used processes in aerospace, such as powder bed fusion, directed energy deposition, cold spray, ultrasonic, additive friction stir deposition, and more, highlighting when and how each should be utilized. Understanding the significance of material selection and characterization in distinguishing AM from other manufacturing technologies, we dedicate two chapters to this crucial aspect, including guidance on characterizing microstructures and testing AM samples.
An extensive chapter delves into post-processing operations, recognizing their integral role in the AM process. Topics covered include powder and support removal, cleaning, machining, joining, heat treatments, inspection, and surface enhancements. To ensure a comprehensive understanding, we explore feedstock considerations, encompassing both wire and powder, emphasizing the importance of comprehending specifications and addressing potential challenges in obtaining desired feedstock.
Functional design is addressed in a later chapter, allowing readers to grasp the other inputs that contribute to an AM build before diving into the intricacies of designing parts. With practicality in mind, we incorporate a chapter that explores various component and application characteristics, as well as certification considerations specific to metal AM. Acknowledging the rapid evolution of the field, we dedicate a section to emerging applications of AM.
Lastly, we include appendices showcasing NASA’s significant investments in developing initial mechanical and thermophysical properties, providing valuable supplementary information to readers.
Overall, “Metal Additive Manufacturing for Propulsion Applications” aims to bridge the gap between theory and practical implementation, serving as an indispensable resource for individuals navigating the realm of metal AM, regardless of their level of expertise.
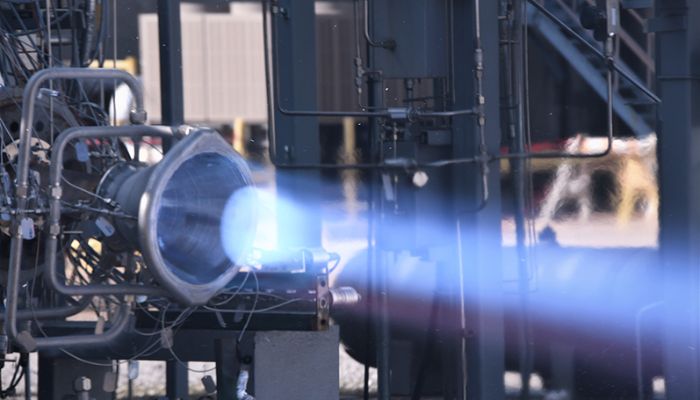
Metal additive manufacturing is increasingly being used for propulsion applications, like this part of a rocket
3DN: With this book, what gaps in knowledge are you hoping to address for both those who are new to the industry and veterans?
As with any new process, it is tempting to become captivated by the excitement of AM and its application and to give little forethought to the potential economic and technical challenges. This book aims to assist AM adopters by promoting a deliberate approach to applying these technologies and by providing a comprehensive understanding of the life cycle of AM components. Particularly in the aerospace industry, the roles of design engineers, materials engineers, and manufacturing engineers are closely intertwined when employing AM. It is crucial for all stakeholders involved in AM to grasp the entire life cycle.
To effectively harness the benefits of AM, engineers must have a holistic comprehension of the entire process, including the material selection and characterization (why AM microstructure is different), processes, post-processing, performance evaluation of AM parts, and the approach for implementation and certification. The propulsion industry is embracing this technology but is also navigating the challenges that arise with new technological advancements. As AM processes evolve, new failure modes are emerging and gaining a deeper understanding. AM represents a new era of industrial revolution, introducing design solutions that were previously unattainable. However, the enthusiasm surrounding these possibilities can result in hasty incorporation of AM technologies without considering the sustained implementation challenges. This book aims to strike a balance by advocating for the technology while providing a realistic overview of the design and process life cycle.
3DN: Any last words for our readers?
Additive manufacturing is a complex endeavor that cannot be seen as a universal solution. We strongly advise that AM be approached in conjunction with traditional manufacturing techniques and employed only when it aligns with the specific needs of a project. However, when a decision is made to pursue AM based on technical and programmatic considerations, it is crucial to approach the entire process with proper rigor and a critical mindset. From the initial conceptual design to the selection of feedstock, the build process, post-processing, certification, and eventual implementation — every step must be thoroughly evaluated. Design for additive manufacturing (DfAM) should encompass all process steps, extending beyond the build process itself. It is important to recognize that the AM process is not always sequential, and iterations in part development will require practice. Challenges and, inevitably, some failed builds may arise, but it is crucial to remember that AM is an evolving field, and the only limitation is one’s imagination. And don’t miss the chance to sign up for the giveaway for a free copy of the book. You can do so HERE until June 10th, 2023.
What do you think of NASA’s use of metal additive manufacturing? Will you be reading the book? Let us know in a comment below or on our Linkedin, Facebook, and Twitter pages! Don’t forget to sign up for our free weekly Newsletter here, the latest 3D printing news straight to your inbox! You can also find all our videos on our YouTube channel.
*All Photo Credits: NASA