NASA develops a new metal additive manufacturing method
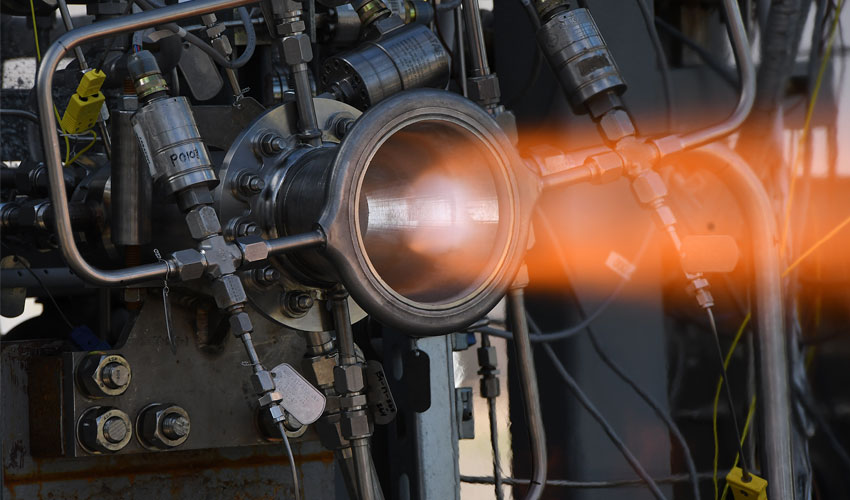
Engineers at NASA’s Marshall Space Flight Center in Huntsville, Alabama have reportedly developed and tested a new metal additive manufacturing method called Laser Wire Direct Closeout (LWDC). A process that could be used to make nozzles more quickly for rocket engines at a reduced cost.
NASA has been working with additive manufacturing for some time now, using it to help streamline 3D printing in space, their development of stronger materials and the design of better equipment. In addition, they also have partnered with others for several projects, including Relativity Space, which creates rockets through additive manufacturing.
More recently, NASA engineers have claimed to have developed a new metal additive manufacturing process called Laser Wire Direct Closeout. As its name implies, this process is not based on a powder bed but instead, uses a concentrated energy wire metal deposition process to create complex metal parts. NASA has already filed a patent for LWDC technology that would reduce manufacturing time from a few months to just a few weeks.
According to NASA researchers, the 3D printing process was designed to precisely close the cooling channels of the 3D printed nozzle. These channels contain the high-pressure coolant that protects the extremely thin walls of a nozzle against very high temperatures.
The nozzles used by NASA are actively cooled thanks to the channels located inside the engine nozzle; these must be closed in order to keep the high-pressure coolant, thus allowing the walls to cool properly. NASA’s LWDC process would effectively shut down the cooling channels and form a support “jacket” that would respond to structural loads during engine cooling.
“Our motivation behind this technology was to develop a robust process that eliminates several steps in the traditional manufacturing process,” said Paul Gradl, a senior propulsion engineer in Marshall’s Engine Components Development & Technology Branch. “The manufacturing process is further complicated by the fact that the hot wall of the nozzle is only the thickness of a few sheets of paper and must withstand high temperatures and strains during operation.”
The additive manufacturing technology developed by NASA has already been tested by Keystone Synergistic: the 3D rocket engine nozzle has been tested for a little over 1040 seconds at very high pressures and temperatures. Find more information on NASA’s official website.
Facebook and Twitter pages! Don’t forget to sign up for our free weekly Newsletter, with all the latest news in 3D printing delivered straight to your inbox!
What do you think about this new 3D printing technology from NASA? Let us know in a comment below or on our
What do you think about this new 3D printing technology from NASA? Let us know in a comment below or on our Facebook and Twitter pages! Don’t forget to sign up for our free weekly Newsletter, with all the latest news in 3D printing delivered straight to your inbox!