Nadarra, the 3D Printed Wall of Sand on Display in Dubai
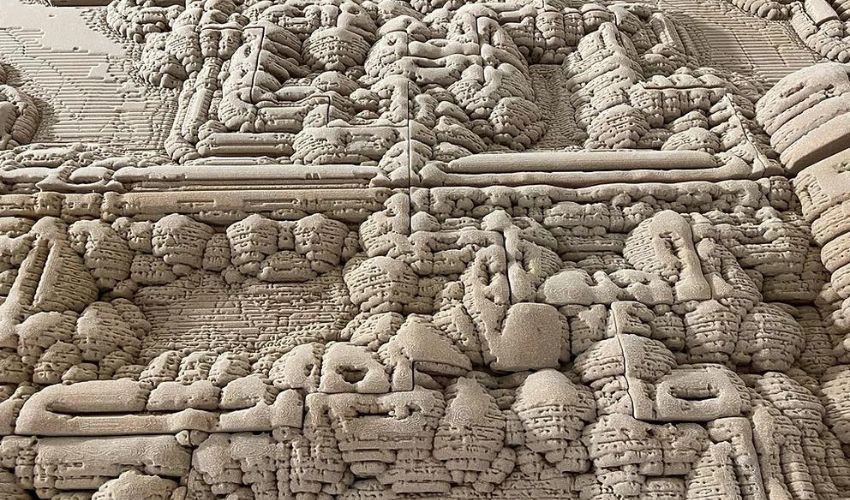
When people think of materials for 3D printing, they primarily think of polymers, resins or even metals, which have been on the rise in recent years. But ceramics are also becoming increasingly popular and one must not forget about the often overlooked sand! In fact, additive manufacturing with sand is already an established practice in the automotive industry and is becoming increasingly popular in the construction industry, especially in design. Artists and designers are experimenting with this natural material to create a wide range of applications. Among them is Barry Wark, architect and designer, who exhibited an impressive 3D-printed wall made of sand at the opening of the temporary exhibition “Tomorrow Today” at the Museum of the Future in Dubai in February 2022. Now the wall of sand, named Nadarra, has been enlarged to complement the museum’s permanent collection.
Barry Wark frequently works with international companies to realize projects around the globe. Wark founded his design studio in 2017, having worked in London and now teaches and researches at the University of Pennsylvania at the Weitzman School of Design. There is always an ecological leitmotif in his projects, the topic of sustainability is omnipresent in all projects as a comprehensive aesthetic. To achieve this overall look, Wark relies on computer-aided design options and modern, technological production methods. For the implementation of the latter, he enlists the support of international industry pioneers. Wark has already worked together with the Rotterdam-based 3D printing company CONCR3DE and also created artifacts in this collaboration that were presented at the last Formnext. There also appears to be a profitable collaboration with the German company Sandhelden, as Nadarra was built in cooperation with Sandhelden alongside other projects in the past. The Bavarian company is one of the pioneers in 3D printing with sand and the necessary post-processing steps. For example, it has made a name for itself with its 3D-printed bathroom furniture made from sand.
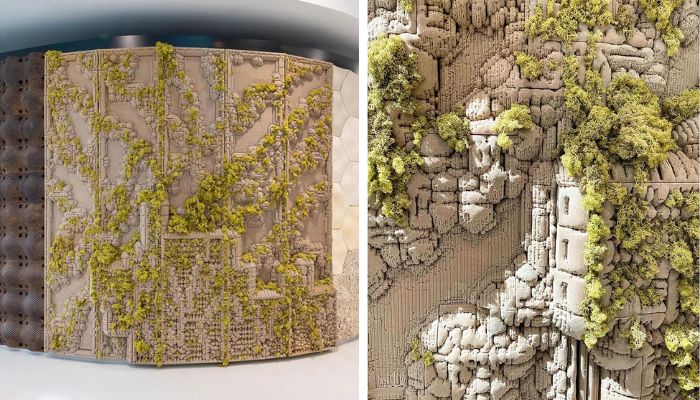
The opening exhibition featured a small first version of Nadarra, which was still overgrown with moss at the time. Now a larger version is being added to the Museum of the Future’s collection. (Photo credits: Sandhelden)
The expertise of Sandhelden was a must for Barry Wark to produce the “most complicated 3D-printed wall of all time”. In contrast to its 2022 iteration, the new version of Nadarra has no greenery, but is all the more impressive in size. It has been enlarged to 6×3 meters (almost 20’x10′) and is now part of the museum’s permanent collection. The wall has many intricate details, resulting in a unique visual design. To achieve this, 3D printing was key, as it makes it possible to create almost unlimited geometric shapes.
3D printing was not the only technology that contributed to this work, however. Wark used AI software to design the surface. After successfully creating the detailed model, the wall was printed in small pieces and then assembled like a puzzle. The contractor for this step was Sandhelden, which operates with binder jetting technology and uses its own post-processing method. The printing itself, in which the sand particles of the SH-P14 quartz sand were bonded with a binder, was carried out using the Voxeljet VX1000. Binder jetting makes it possible to process various types of sand and gravel and solid, functional structures can be achieved with post-processing. According to Wark, Nadarra can withstand up to eight sanding cycles without any loss of texture or aesthetics. Carlos del Castillo, Head of Design at Sandhelden, also emphasizes this: “Our 3D printing technology enables us to combine high-quality design with unlimited technical and aesthetic possibilities.“
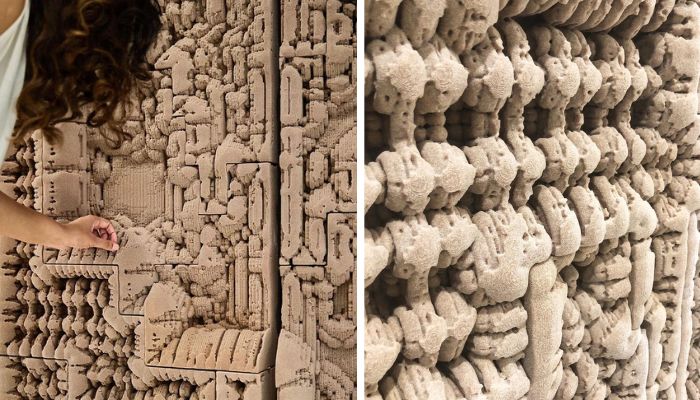
The components of Nadarra were printed individually and then assembled like a puzzle. (Photo credits: Barry Wark)
The environmental concept that prevails in Wark’s work has also been incorporated into the 3D-printed Nadarra, as 3D printing only uses the amount of materials that are required for the end product, reducing waste. In addition, the wall made of sand can be disposed of and recycled at the end of its service life. “The project engages with the importance of materials and their life cycles in the built environment, employing advanced 3D printing sand technology, the parts can be fabricated, installed, and then recycled up to 8 times after use,” says the Sandhelden website.
The 3D-printed wall reflects the life cycle in a special way. The surface is designed so that it is reminiscent of natural erosion. Barry Wark thus alludes to nature and its own laws of weathering and erosion on the one hand, but also to the traces created by hand on the other. On Nadarra, he blurs the boundaries between the natural and the man-made. “Motivated by the recognition that all buildings eventually erode, stain and weather, the project is designed to display its interconnectedness with its environment in other words, its ecology,” says Sandhelden. Find out more about Barry Wark and Nadarra HERE.
What do you think about the Nadarra sand wall? Let us know in a comment below or on our Linkedin, Facebook, and Twitter pages! Don’t forget to sign up for our free weekly Newsletter here, the latest 3D printing news straight to your inbox! You can also find all our videos on our YouTube channel.
*Cover photo credits: Sandhelden GmbH & Co. KG