Multiply Labs 3D Prints Personalised Daily Pills
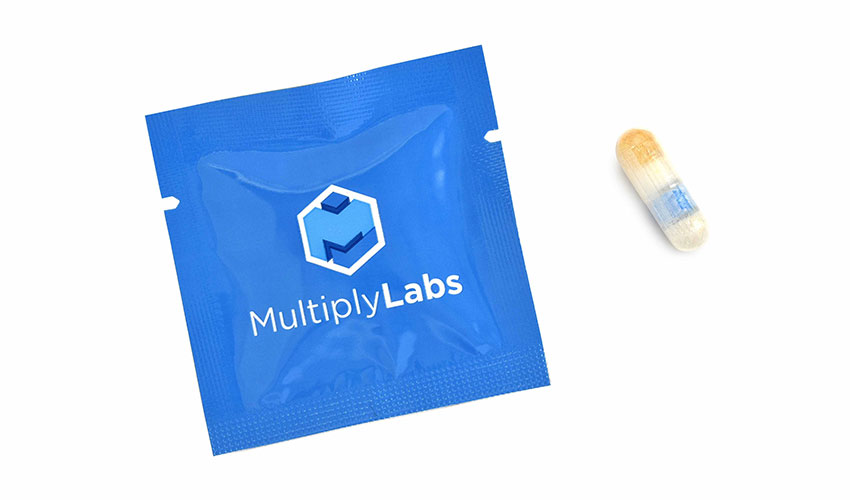
Additive manufacturing seems to have opened the door to more unique and personalised types of therapy and treatments. People supporting this convergence to personalised health care often cite its benefits, such as the ease of use they bring. As a result improving adherence and the health outcomes of patients. In fact, this is what Multiply Labs is a firm believer of. They have focused on personalisation in order to supply to each patient what they need. With the use of pharmaceutical technologies (and a background in robotics) they’ve been capable of 3D printing personalised capsules. Their capsules provide throughout the day all the medication patients need. To gain a better understanding of their technology we decided to interview the co-founder and CEO of Multiply Labs, Fred Parietti.
3DN: Could you present yourself as well as your company, Multiply Labs?
I am Fred Parietti, I am the PDG and co-founder of Multiply Labs, a new type of personalised pharmaceutical company. At the moment, we haven’t involved ourselves in the fabrication of active pharmaceutical ingredients yet. However, we’ve developed and now produce 3D printed capsules which are programmed to release pharmaceutical ingredients in a controlled way. Our first products were personalised supplement pills. It allowed us to enter the market and develop the machines and filaments we would need to create these 3D printed pills.
We are working on a new range of products. We have started some work on capsules designed for HIV treatment. Thanks to Multiply Labs we can see a future in which each patient can take a single, unique capsule that contains all the supplements or drugs they need.
3DN: What is the technology behind Multiply Labs’ capsules?
At Multiply Labs we apply 3D printing to the manufacturing of pharmaceutical products, in particular the capsule containing the ingredients. It is not any capsule, inside it we have created separate compartments of varying thickness. Each compartment contains different supplements or products which will release at different times. We can 3D print a compartment with a very thin wall which will release the product within 30 minutes. We can add to the same capsule another compartment, this time with a much thicker wall, capable of containing the supplement for two hours. We can add up to 4 or 5 compartments within a same capsule.
Our capsule is produced from a very specific pharmaceutical polymer. We introduce the medication or supplement in powder form once the capsule has been 3D printed. We use FDM technology to print our capsules. We decided it was best to separate the 3D printing process from the introduction of the supplement as it could otherwise degrade it.
3DN: Could you tell us a bit more about your pharmaceutical filament and the technology you use to print it?
At the moment we only use one polymer, called Hydroxupropyl cellulose, or HPC. It is a water soluble polymer which can be taken without any harm and dissolves naturally in the human body. We buy this product in powder form another company. Then, we convert it into a 3D filament. This way we create our own material which we can use to manufacture our capsules. We also control the thickness of the capsule’s walls which will determine when the capsule starts dissolving.
This filament is actually the only appropriate quality filament for 3D printing to exist on the market. Our product is unique on the market which we have envisaged to sell to the industry. In particular to research labs or pharmaceutical companies because it allows rapid production of capsule prototypes. In terms of additive manufacturing technology, we actually developed the print head which we mounted on our 3D printer. Since our filament is very flexible, we needed the correct printing parameters to use it appropriately.
3DN: Why use 3D printing to develop these capsules, what are the advantages of this technology?
At this moment in time, capsules are produced in large series, millions of the same are produced each day. However, we are aware that the medical field is sifting and focusing more on personalisation. Each person wants their own treatment in one pill, which is not possible with mass production. 3D printing is the best way to start because it allows us to test different compartments for different medication. Additive manufacturing gives us the freedom to test things very quickly.
3DN: Where do you see Multiply Labs in ten years’ time?
In ten years we hope to become the norm in terms of pharmaceutical products. No patient will accept taking the same as the next patient, nor will any doctor prescribe the same product to two patients. For example, at the moment, supplements, drugs or pharmaceutical products in general are conceived for adult men. This means that many women and children are prescribed an excessive dose for their bodies because their bone mass is generally less and insufficient for the dosage. At Multiply Labs we’ve imagined a future in which everyone can get their hands on a personalised product and we have the perfect technology to achieve this.
You can find more information on Multiply Lab’s website here.
What do you of personalised pills? Let us know in a comment below or on our Facebook and Twitter pages! Don’t forget to sign up for our free weekly Newsletter, with all the latest news in 3D printing delivered straight to your inbox!