Harvard researchers develop multinozzle 3D printer that can switch between 8 inks
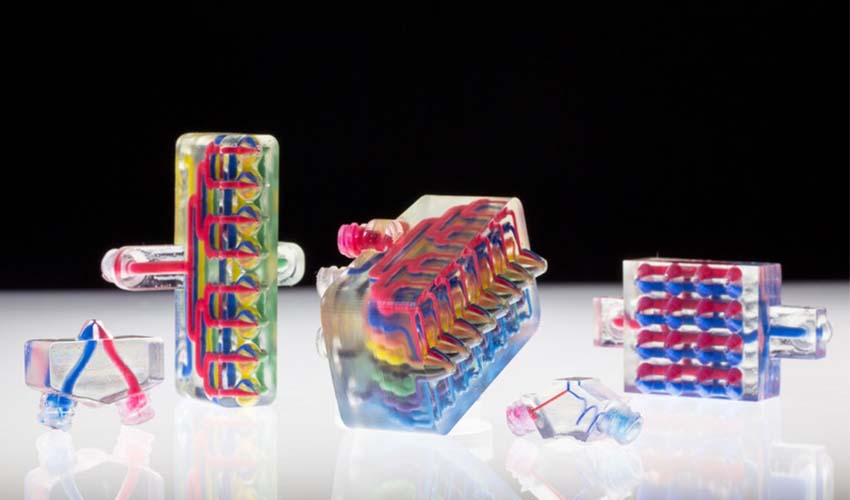
You might be aware that most commercial extrusion-based 3D printers are only able to build objects from a single material at a time. And when they do allow for multiple materials and colors to be used, the process is slow. Researchers at Harvard Wyss Institute for Biologically Inspired Engineering and John A. Paulson School of Engineering and Applied Sciences (SEAS) have developed a new technique called multimaterial multinozzle 3D printing (MM3D). According to the researchers, this technique enables a single printhead to switch between multiple different materials, up to 50 times per second. What does this multinozzle 3D printer bring to the AM industry?
This technique uses high-speed pressure valves to achieve rapid, continuous and seamless switching, as mentioned it can switch up to 50 times in one second. Additionally, the printhead can switch between 8 different printing materials. Researchers explained that the printhead developed can range from a single nozzle to large multinozzle arrays, these were also 3D printed to allow for their rapid customization.
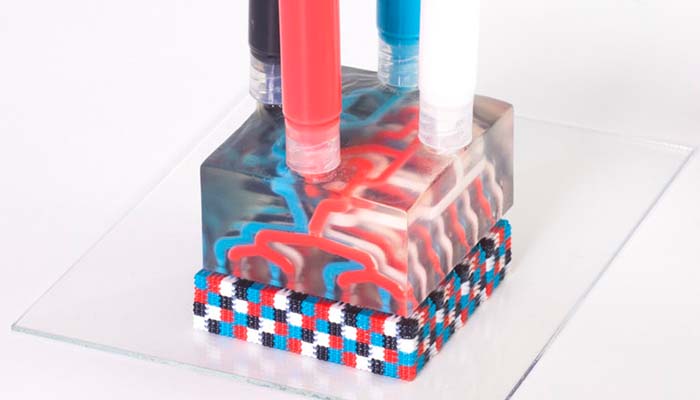
MM3D printing allows to seamlessly switch between multiple different materials up to 50 times per second, greatly streamlining the process of printing complex structures. | Credit: Wyss Institute at Harvard University
Co-first author Mark Skylar-Scott, Ph.D. a Research Associate at the Wyss Institute develops on the benefits of this new technique: “When printing an object using a conventional extrusion-based 3D printer, the time required to print it scales cubically with the length of the object, because the printing nozzle has to move in three dimensions rather than just one. MM3D’s combination of multinozzle arrays with the ability to switch between multiple inks rapidly effectively eliminates the time lost to switching printheads and helps get the scaling law down from cubic to linear, so you can print multimaterial, periodic 3D objects much more quickly.”
Multinozzle 3D printer enables new applications
Inside the printhead, multiple ink channels come together at a single output nozzle. The researchers calculated precisely the shape of the nozzle, printing pressure and ink viscosity needed so that when pressure is applied to one of the arms of the junction (as seen in the picture below), the ink that flows down through that arm does not cause the static ink in the other arm to flow backwards. In short, this prevents the inks from mixing. Additionally, the length of the printing channels can be adjusted to ensure that materials with different viscosities for example, (they would therefore flow more quickly or slowly than other inks) flow at the same pace.
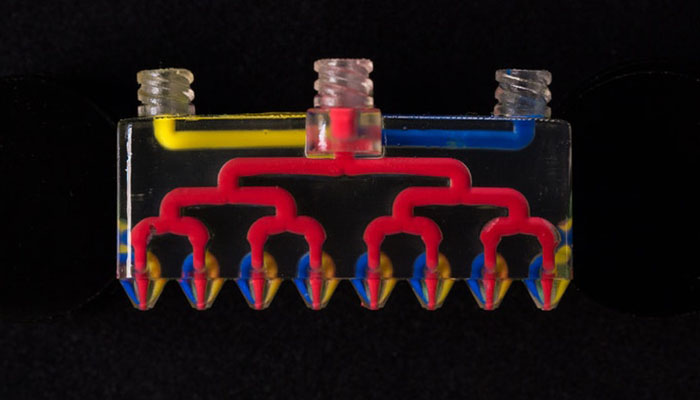
The printhead can accommodate multiple nozzles, each of which can print up to eight different materials. A series of branched channels distributes the “inks” to the nozzles | Credit: Lori K. Sanders
In terms of applications, this printing technique can use reactive materials such as epoxies, silicones and bioinks. Co-first author Jochen Mueller, Ph.D., a Research Fellow at the Wyss Institute and SEAS explains: “One can also readily integrate materials with disparate properties to create origami-like architectures or soft robots that contain both stiff and flexible elements.” The team of researchers also experimented with their technique by 3D printing a soft robot composed of rigid and soft elastomers in a millipede-like pattern. Thanks to embedded pneumatic channels the robot could move, at nearly half an inch per second while carrying a load eight times its own weight, and could be connected to other robots to carry heavier loads.
Wyss Founding Director Donald Ingber, M.D., Ph.D. concludes: “3D printing is revolutionizing the manufacturing industry by allowing people to create without the need for expensive machinery and raw materials, and this new advance promises to dramatically improve the pace of innovation in this exciting area.” We cannot wait to see the applications that flourish from this technique and report on them!
What do you think of the MM3D technique? Let us know in a comment below or on our Facebook and Twitter page! Don’t forget to sign up for our free weekly Newsletter, with all the latest news in 3D printing delivered straight to your inbox!