New Multi-Material Metal 3D Printing Technique for Lightweight, Durable Automobile Parts
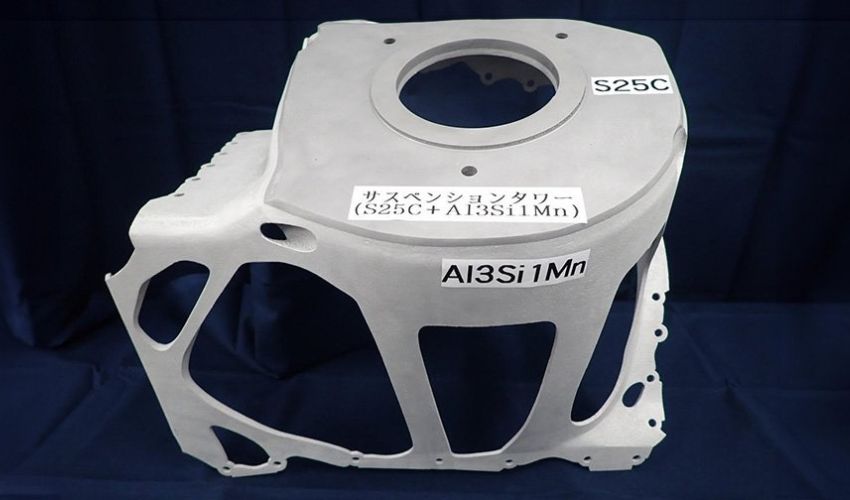
Lightweighting, or the concept that lighter cars can achieve better fuel efficiency, battery range, acceleration, braking and handling, is one of the biggest trends in automobile manufacturing today. But challenges remain, notably when it comes to combining materials to take advantage of different properties, for example the strength of steel and the lightness of aluminum. Now there might be a solution thanks to researchers from Tohoku University’s Institute for Materials Research and New Industry Creation Hatchery Center who have made a breakthrough with a new multi-material metal 3D printing technique that can be used to create lightweight, durable automobile parts.
Additive manufacturing has become immensely popular in the car manufacturing sector. In a press release from Tohoku University, the precision of 3D printing notably highlighted it as a way to produce unique, highly-customizable shapes. However, the materials used often have drawbacks, which is where multi-material 3D printing comes in. Still, that in itself is not infallible.
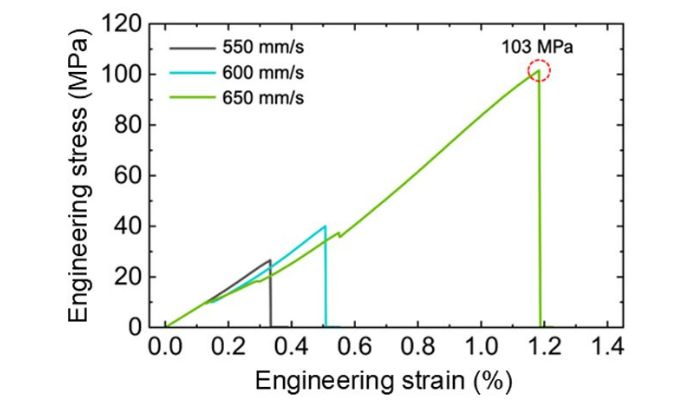
Interfacial strength for steel-aluminum alloy multi-materials melted using LPBF at different scan speeds (photo credits: Kenta Yamanaka et al.)
“Multi-materials are a hot topic in the field of additive manufacturing due to its process flexibility,” explains Associate Professor Kenta Yamanaka, “However, a major challenge in practical implementation is that for certain metal combinations, such as steel and aluminum, brittle intermetallic compounds can be formed at the dissimilar metal interfaces. So, while the material is now lighter, it ends up being more brittle.”
Turning specifically to laser powder bed fusion, one of the major metal AM processes in the automotive sector, the research team sought to produce a steel-aluminum alloy that was lightweight but strong. What they found was that increasing the scanning speed of the laser significantly suppresses the formation of brittle intermetallic compounds (giving the examples of Al5Fe2 and Al13Fe4).
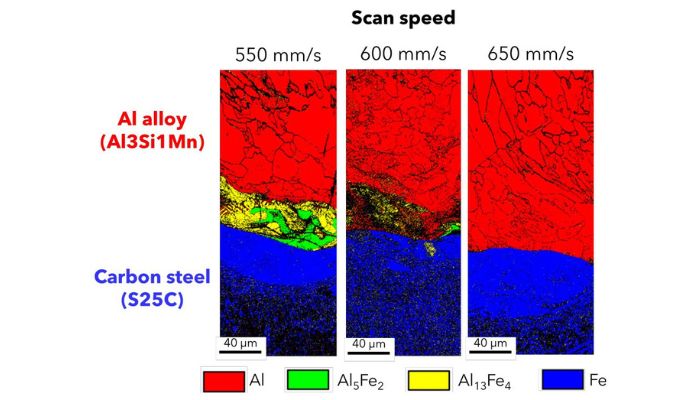
The results on bonding fr steel-aluminum alloys using LPBF at different scan speeds (photo credits: Kenta Yamanaka et al.)
The researchers believe that this is due to something called non-equilibrium solidification, which minimizes the partitioning that can result in weak points in the material. And as a result, they were able to demonstrate strong bonding interfaces. Specifically Appointed Assistant Professor Seungkyun Yim, one of the members of the team, expanded “In other words, you can’t just slap two metals together and expect them to stick without a plan. We had to fully understand the in-situ alloying mechanism first.”
The result? A successful prototype of what they claim to be the world’s first full-scale automotive multi-material component (specifically a suspension tower) with tailored geometry. The group expects to apply the findings to other metal combinations to allow for even more applications. You can access the full study HERE
What do you think of this multi-material metal 3D printing technique for lightweight but still durable car parts? Let us know in a comment below or on our LinkedIn, Facebook, and Twitter pages! You can get access to other automotive 3D printing news HERE. Don’t forget to sign up for our free weekly Newsletter here, the latest 3D printing news straight to your inbox! You can also find all our videos on our YouTube channel.
*Cover Photo Credits: Kenta Yamanaka et al.