Moorhuhn bike: competing with carbon fibre frames?
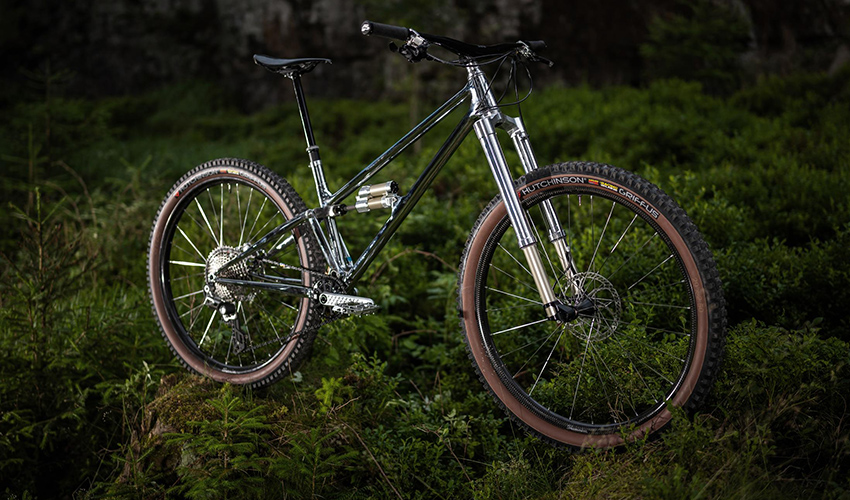
The purmundus challenge was presented for the eighth time on November 2020 as part of the digital Formnext Connect exhibition. This annual competition invites designers and engineers from around the world to participate in a theme-based 3D printing design contest. This year’s theme, Geometry and Material in Harmony, was interpreted by 35 finalists. The first prize went to HUHN cycles for its 3D printed Moorhun Bike! The jury said that they were very impressed by this project altogether. “We thought it was a great example of an innovative use of additive manufacturing for the right reasons,” they added. So, what is AM capable of doing for the bicycle industry?
An alternative to carbon fibre frames?
Over the last few years, we’ve seen some interesting innovations in this space, thanks in particular to the emergence of new materials like carbon fibre. As you may know, carbon fibre is rarely used on its own, but more often combined with other materials (usually polymers) to form composite materials. The main benefit of composites is its strength-to weight ratio, as well as the increased level of stiffness it provides to parts. For example, this year, AREVO and Superstrata presented their 3D printed carbon fibre unibody bike frame for their Superstrata bicycle and e-bicycle. Though the project was impressive, and allowed to produce a bike that was lighter but much stiffer than before, some have point out the very high carbon footprint its production involves.
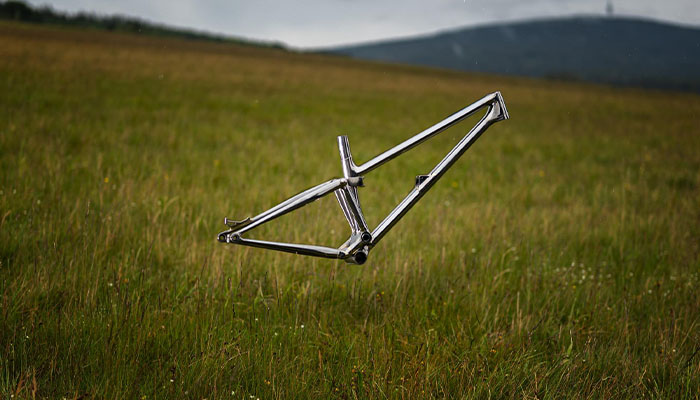
The Moorhuhn bike frame is made from titanium
You can read on the Purmundus website, “Carbon products have a very short product lifecycle as there is a certain safety risk in using second hand or crashed carbon products. Sadly there are nearly no ways of recycling this composite material, so most of the time carbon frames end up in land fields or get burned.” This explains the desire to recompensate HUHN cycles that develops bike frames made from titanium. Though titanium is a material that could compete with carbon fibre for bike frames, it is also very difficult to process, which somewhat limits the design process. It’s in altering and optimizing the design process that a frame’s performance can improve, which is quite the challenge. In addition, titanium frames are softer than carbon fibre frames.
The Moorhuhn bike
To overcome these challenges, Moorhuhn combines the advantages of super light titanium tubes and connects them with additively manufactured lugs. The joints were designed to be very light and stiff at the same time – thanks to a lattice structure inside the thin walls. The jury commented: “We thought it was an interesting example of how AM can be combined with more traditional methods to create a product that is both high performance and ultimately very desirable.”
Furthermore additive manufacturing makes it possible to produce each frame according to the needs of each individual as there are no tools required. Functions like cable guiding, seat clamps, bearing housings and additional material for welding can be integrated in the design, making the life of the frame builder much easier. Finally, the titanium frame does not need paint at all as there is no corrosion so even the finishing process involves no chemicals.

The joints were designed to be very light and stiff at the same time, thanks to a lattice structure inside the thin walls
To conclude, maybe the most important takeaway is that the production process is environmentally friendlier, and the frames can safely be repaired and recycled, unlike carbon fibre frames. You can find more information HERE. What do you think of the Moorhuhn bike? Let us know in a comment below or on our Facebook and Twitter page! Don’t forget to sign up for our free weekly Newsletter, with all the latest news in 3D printing delivered straight to your inbox!