MIT Researchers Achieve Breakthrough in 3D Printing of Electromagnets
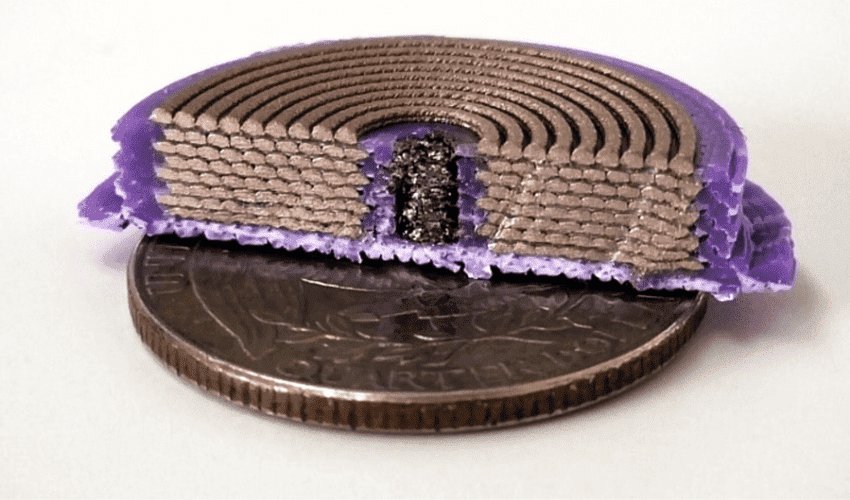
Researchers at the Massachusetts Institute of Technology (MIT) have achieved a breakthrough that could transform electronics production. Their successful 3D printing of three-dimensional solenoids represents a significant leap forward in electronics manufacturing. Solenoids, comprised of a coil of wire wound around a magnetic core, serve as indispensable components in a myriad of electronic applications. From critical medical devices like dialysis machines and respirators to everyday household appliances such as washing machines and dishwashers, solenoids play a vital role in converting electrical energy into mechanical work. Traditionally, manufacturing solenoids has required complex techniques.
The development of fully 3D-manufactured electronic devices currently poses considerable challenges. However, ongoing research marks a progression towards more economical and less wasteful production techniques. These improvements could be used across many industries, with use even in space.
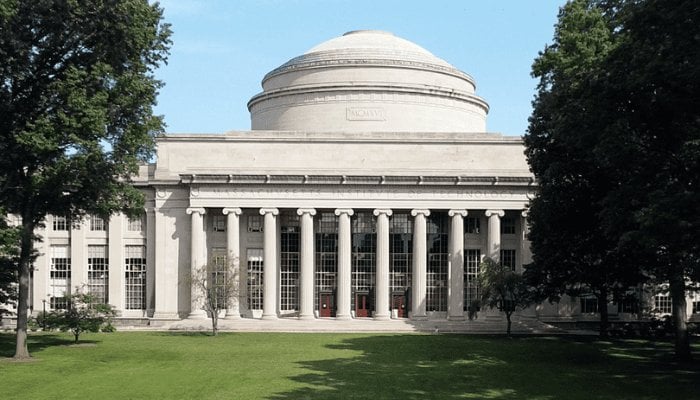
The Massachusetts Institute of Technology (MIT)
3D Printed Electromagnets
Traditional manufacture of solenoids involves the complex assembly of different materials, often limiting the size and shape of the parts. The use of 3D printing, however, offers the possibility of overcoming these constraints. MIT researchers, led by Luis Fernando Velásquez-García, have solved the problems associated with material compatibility by adapting their multi-material 3D printer to superimpose three different materials: a dielectric material serving as an insulator, a conductive material forming the electrical coil, and a soft magnetic material making up the core. This adaptation facilitated the production of compact, single-piece solenoids, eliminating the potential for assembly errors.
Through their experiments, the researchers accomplished the printing of an electromagnet with eight winding layers, arranged in a spiral configuration. This modification to the printer allowed for the creation of more compact yet higher-performing solenoids. These results showed that a 25 mm-diameter electromagnet made by 3D printing can withstand twice the electric current and generate a magnetic field three times stronger than its conventionally manufactured equivalent.
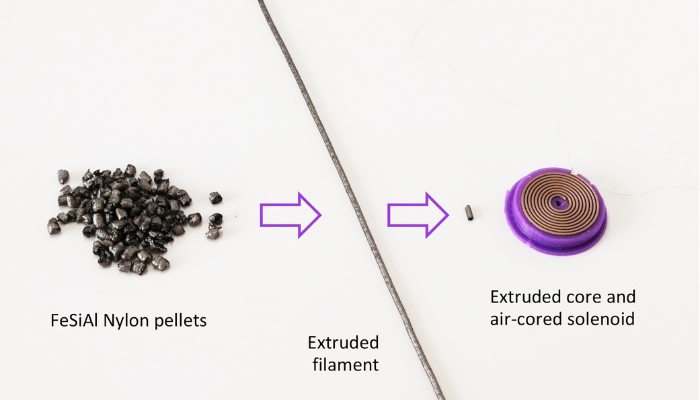
Solenoids are made by layering three materials: an insulator, a conductor for the coil, and a magnetic core.
Despite the initial investment in custom equipment, using 3D printed electromagnets has significant economic advantages over conventional manufacturing methods. This advancement could revolutionize manufacturing processes by minimizing waste and improving accessibility to essential medical equipment, such as dialysis devices, especially in remote areas. The potential benefits of 3D printing extend beyond our planet, offering intriguing possibilities for space exploration. With the capability to produce replacement electronic components on demand, this technology could significantly cut costs and time delays, presenting a sustainable solution essential for extended space missions. Speaking on these advantages, Luis Fernando Velásquez-García explained,
In addition to making electronics cheaper on Earth, this printing hardware could be particularly useful in space exploration. For example, instead of shipping replacement electronic parts to a base on Mars, which could take years and cost millions of dollars, one could send a signal containing files for the 3D printer.
What do you think of these 3D printed solenoids? Let us know in a comment below or on our LinkedIn, Facebook, and Twitter pages! Don’t forget to sign up for our free weekly newsletter here, the latest 3D printing news straight to your inbox! You can also find all our videos on our YouTube channel.
*All Photo Credits: Massachusetts Institute of Technology (MIT)