MIT Engineers 3D Print Electrospray Engine Ideal for Small Satellites

Have you heard of electrospray engines? These propulsion systems involve applying an electric field to a conductive liquid, generating a high-speed jet of tiny droplets capable of propelling a spacecraft. Such miniature motors are particularly suitable for small satellites, known as CubeSats, which are used in academic research. Furthermore, electrospray engines can use fuel more efficiently than conventional chemical rockets, making them particularly suitable for precise movements in orbit.
Traditionally, electrospray engines are manufactured using expensive and time-consuming semiconductor cleanroom fabrication, which limits the range of applications and the number of manufacturers. To circumvent this problem, MIT engineers developed an electrospray motor made entirely using 3D printing.
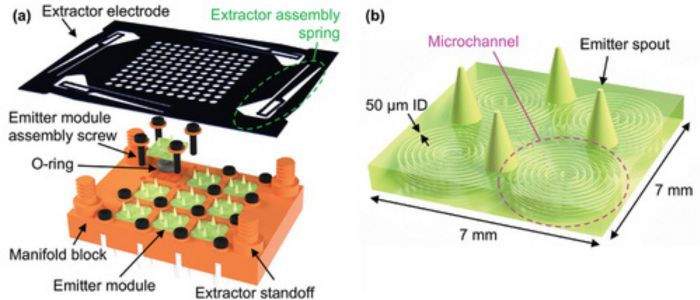
3D CAD models of the electrospray thruster design explored in this study: a) exploded view of assembled thruster made of a manifold block, an array of emitter modules, and an extractor electrode (during the experiments, the central emitter module was replaced with a non-functional module to ensure uniform emitter operation across the other eight emitter modules); b) close-up of an emitter module composed of an array of four emitters, each fed by a long, narrow, and winding capillary.
How do electrospray engines work? Well, they have a reservoir of propellant that flows to a series of emitters via microfluidic channels. A strong electrostatic field is applied to the tip of these emitters, which triggers an electrohydrodynamic effect. Then, this shapes the liquid into a cone-shaped meniscus that ejects a stream of high-speed charged droplets from its apex, generating thrust.
To 3D print the electrospray engines, the researchers needed to use two types of photopolymerization. To construct the emitter modules, they used two-photon printing, in which a highly focused laser beam hardens liquid resin in a targeted manner. Thanks to this precision, they produced fine emitter tips and uniform, narrow capillaries for propellant transport.
The emitter modules are installed in a rectangular distributor block, which fixes them in place and supplies them with propellant. This block also integrates an extractor electrode, which releases the propellant from the emitter tips when a suitable voltage is applied. The two-photon printing would not have been efficient for larger structures due to its limited printing volume, so they opted for an alternative technique: the distribution block was produced using digital light processing (DLP). In this method, a microscopic projector projects light onto the resin, curing an entire layer of the 3D structure at a time. This technique enables larger components to be produced more quickly and complements high-precision two-photon printing for finer details.
The MIT researchers then experimented to make sure the 3D printing materials were compatible with the liquid propellant. A method was also developed to precisely connect the individual components and avoid misalignments that could affect the system’s performance. Overall, 3D printing offered several advantages: it lowered costs, allowed the use of commercially available materials and manufacturing techniques and could even enable manufacturing in orbit. That way, astronauts could produce propulsion systems for satellites directly in space without having to wait for supplies from Earth.
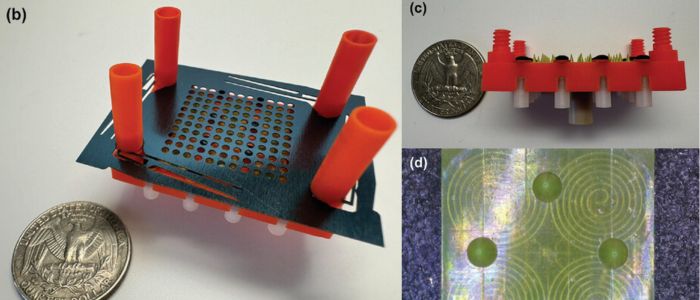
Images of a 3D-printed electrospray thruster: b) optical image of a fully assembled device next to a US quarter; c) optical image from the side of the device without the extractor electrode next to a US quarter; d) close-up optical image of an emitter module.
Ultimately, the MIT team’s 3D printed prototype generated thrust more efficiently than larger, more expensive chemical rockets and outperformed existing droplet electrospray engines. Going forward, they hope to create denser arrangements of emitter modules and to explore the advantages of voltage modulation and the use of multiple electrodes to improve the efficiency and performance of electrospray motors. Find out more about the project HERE.
What do you think of the 3D printed electrospray engine? Let us know in a comment below or on our LinkedIn, Facebook, and Twitter pages! If you are looking for more 3D printing in aerospace & defense content, check out our dedicated page HERE. Don’t forget to sign up for our free weekly Newsletter here, the latest 3D printing news straight to your inbox! You can also find all our videos on our YouTube channel.
*All Image Credits: Hyeonseok Kim, Luis Fernando Velásquez-García (MIT)