MIRA3D Simplifies and Optimizes Additive Manufacturing Workflow
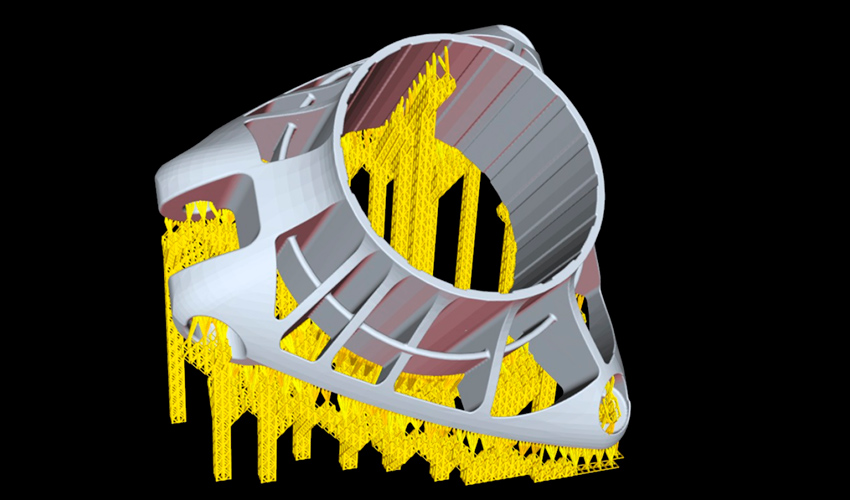
India is one of the fastest-growing countries in the world for 3D printing. It is in this context that MIRA3D was born, a company that has developed innovative solutions to simplify and optimize the 3D printing workflow, particularly in industries that demand high precision and reliability in their manufacturing processes. We had the opportunity to speak with Mohit Kumar, co-founder of MIRA3D, who shares the company’s vision and how its specialized software is helping to transform part preparation for additive manufacturing.
3DN: Could you introduce yourself and tell us about your connection with 3D printing?
My name is Mohit Kumar, and I’ve been working in the additive manufacturing industry for nearly 10 years now. After graduating as a Mechanical Engineer, I started my first business, 3Dware, in 2015, where we built India’s first industrial top-down DLP 3D printer and formulated our proprietary materials. I chose to then pivot into the software space with MIRA3D, which I co-founded to simplify and optimize the 3D printing workflow.
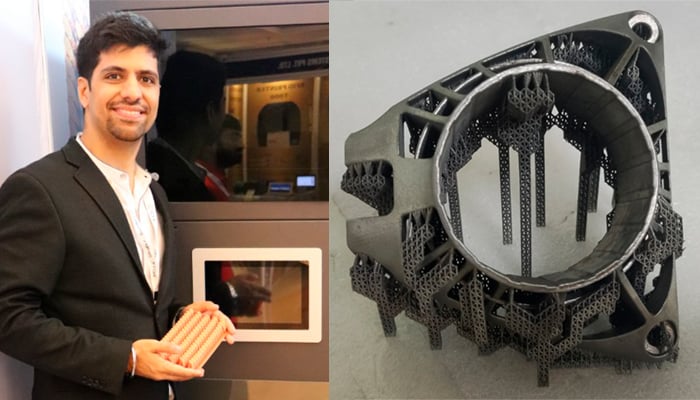
To the left, Mohit Kumar, co-founder of MIRA3D.
3DN: What is Mira3D? How did the idea of creating the company come about?
MIRA3D is a Build Preparation and Inspection Software for Additive Manufacturing made by our company Samisan Tech (the word “Samisan” is a shorthand derived from “समीकरण संसार” which translates to World of Equations). We are a young team of mathematicians and software engineers that make application specific solutions with a strong focus in AM technology.
The idea emerged when my co-founder, Dr. Jeet Desai, returned to India after completing his PhD in Applied Mathematics at École Polytechnique, Paris. We identified a gap in the market for robust and affordable mesh repair tools, particularly for the jewelry industry, where such tools are essential. Together, we envisioned a platform addressing age-old challenges like support generation and mesh repair while offering advanced tools like wall thickness analysis and 3D Nesting. What began with a focus on jewelry has since grown to serve a wide range of industries in additive manufacturing.
3DN: Can you tell us more about the MIRA3D Build Processing Software suite? What does it include?
The MIRA3D Build Processing Software suite simplifies the workflow of preparing parts for 3D printing. Notable features are as follows:
- Mesh Repair: An AutoFix feature designed to deal with large files and fix non-manifold edges, overlapping triangles, holes, and a shell repair wizard with an X-ray mode, enabling users to quickly identify erroneous shells and naked edges.
- Mesh Editing: Polygonal offset, feature-preserving Smoothening, Triangle Reduction & Boolean Operations (union/ intersection/ difference)
- Parametric Auto-Orient: Assigning custom weights to print time, overhang area, and platform area to assign the best orientation for a given part.
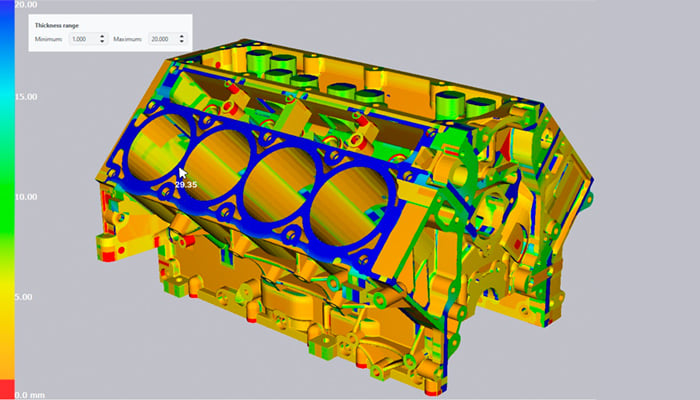
This software solution simplifies the process of preparing 3D parts.
- OPF Support Technology: Our Optimized Path Finding (OPF) significantly reduces post-processing time and material waste in supports.
- Instant Wall Thickness Analysis: Displays the wall thickness map instantly for several GBs of file, without the need to unify the mesh. Users can check thickness in real-time simply by hovering over a part’s geometry and highlighting the areas within a minimum thickness.
- 3D Inspection: To check dimensional variations between the 3D Scan of a manufactured part and its corresponding CAD.
The suite focuses on reliability, ease of use, and reducing the total cost of ownership for businesses using AM software.
3DN: What differentiates your preparation software from other solutions on the AM market?
As we are a relatively new business, our focus is towards building niche solutions in collaboration with machine manufacturers/ industry professionals/ service bureaus. For instance, our partnership with a Metal Binder Jetting machine manufacturer helped us prepare a one-click solution for setter supports that have different offset values in XY and Z directions which is quite unique. Similarly, our (OPF) support generation technology, which reduces post-processing time by 50% and support weight by upto 40% for large size, industrial parts was primarily developed keeping the needs of service bureaus with industrial SLA printers in mind.
Therefore, besides the tools in our software suite, our prime differentiator is our openness for collaboration and agility to come up with custom-made tools for special purpose applications.
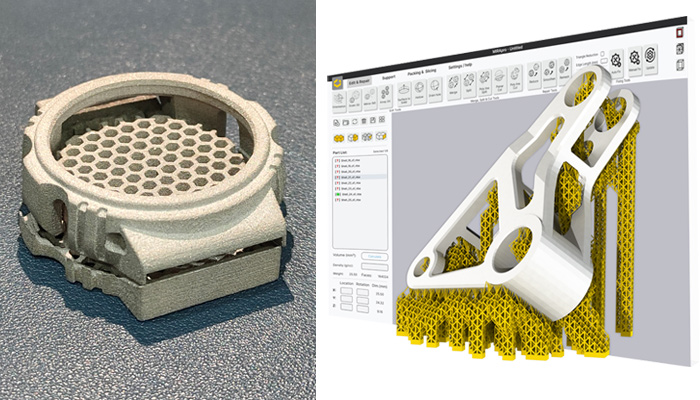
Crédits photo : MIRA3D
3DN: How do you see the future of 3D printing in 10 years? What about Mira3D?
In the next decade, I see 3D Printing as a key manufacturing technology for fully automated factories, with metal AM leading the industry’s growth. As material and equipment costs decrease, companies will digitize their inventory, reducing storage costs and rethinking traditional manufacturing. However, for wider adoption, the cost per part must drop, and processes need to become more consistent, both in print outcomes and material properties.
At MIRA3D, we are working to make the build preparation process more reliable and automated. Our support generation is already accurate and adaptable, and we’re developing tools to automatically alter support profiles based on part geometry, material, and machinery. Features like wall thickness analysis can eventually trigger automated design adjustments based on user-defined constraints to minimize build failure without affecting functionality/ aesthetics of the part. Additionally, we would be integrating traceability tools that can track parts from design to production. These improvements will add a layer of accountability and enforce quality control in additive manufacturing.
3DN: Any last words for our readers?
Given the academic and engineering background of our core team, we go beyond being limited to a software development company. Another part of our business focuses exclusively on understanding how AM as a technology can be useful for companies that haven’t explored AM before as a manufacturing method. We handhold our customers by assisting them end-to-end with the design/ development process with our team’s knowhow. We also ensure that the transition to AM is technically as well as commercially viable for our customer.
What do you think of MIRA3D’s software? Let us know in a comment below or on our LinkedIn or Facebook pages! Plus, don’t forget to sign up for our free weekly Newsletter to get the latest 3D printing news straight to your inbox. You can also find all our videos on our YouTube channel.
*All Photo Credits: MIRA3D