What affects metal powder reusability in AM?
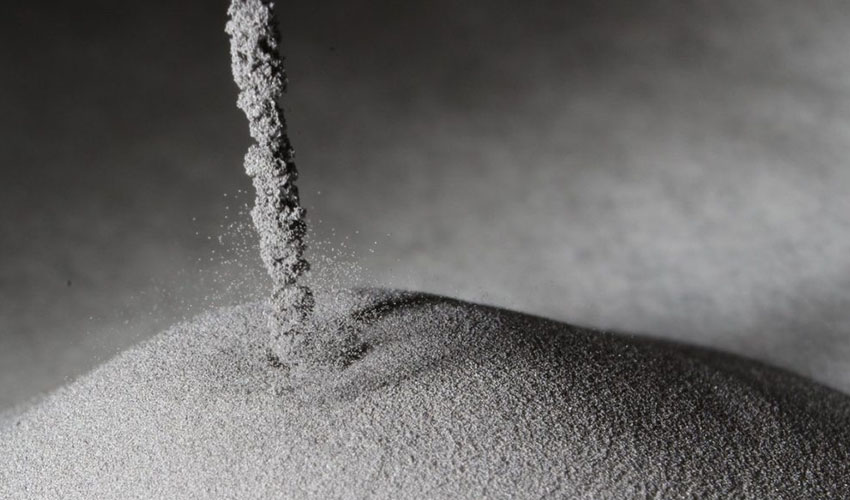
In the last ten years, metal additive manufacturing has taken hold in the industrial sector. Still largely used for prototyping, the technology is slowly reaching a state of maturity that will enable series production of end-use parts. Metal AM processes often rely on powders (sometimes metal wires) to manufacture parts. As explained by Canadian Metalworking, at the beginning of metal AM, manufacturers did not have access to metal powder specifically designed for 3D printing. Therefore, they had to work with leftovers and scrap with general specifications. Today, purchasing powders with the correct specifications for 3D printing is relatively easy. The question is can manufacturers reuse leftover metal powders effectively?
In an article published by Canadian Metalworking, the question of metal powders’ reusability is explored. As many of you may know, one of the benefits of additive manufacturing over conventional manufacturing techniques is that materials can be recycled. The key is keeping the powder under the correct specifications for the process of AM. In the most popular metal 3D printing process, also known as Laser Powder Bed Fusion (LPBF), only a small amount of material is fused to create an object, the rest is left untouched.
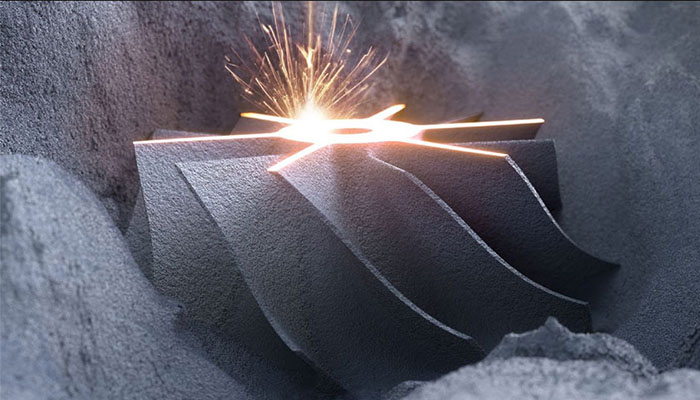
The Laser Powder Bed Fusion process
Therefore, recyclability depends largely on the material used – given that every material ages differently. Lucy Grainger, senior applications engineer at Renishaw told Canadian Metalworking: “Various steels are not as susceptible to degrading in terms of the chemical properties as titanium or aluminum alloys. Generally, the distribution of the powder size needs to be like a bell curve-type distribution. The powder needs to be generally spherical rather than angular, making it easier to flow. So when we are dosing the layers, it’s consistent and repeatable every time.” Essentially, the number of reuse cycles is limited by how much the material degrades before it is out of specification.
Every powder will perform differently according to the system used, and this is information some manufacturers may fail to take into consideration. However, it is key to understand how a material will work on a machine, which means carrying out validation experiments beforehand. Additionally, the type of part you are creating will affect the reusability of the powder. For example, a complex part such as a lattice structure will have more heat-affected zones than a simple part ( where the heat-affected zone is only on the edges). Given that powder ages more rapidly the closer it is to the heat source where the melting process is taking place, a complex part will age more powder.
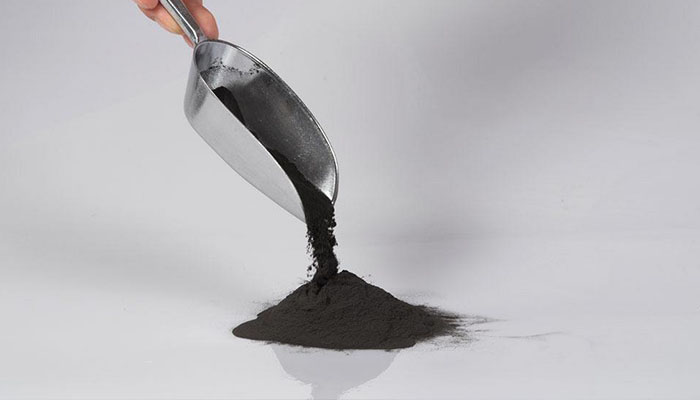
Credits: EOS
Finally, Canadian Metalworking touches on the 3D printer’s architecture. Lucy Grainger adds: “With powder chemistry, it’s pretty much all about the environment in the build chamber. As soon as the machine shoots a laser at the powder and heats it up, depending on the material, the melted material and the particles in the heat-affected zone are going to suck in any oxygen, nitrogen, and water molecules available in the chamber.” Therefore, a build chamber that is properly sealed can extend material reuse cycles by blocking air and moisture from getting into the atmosphere of the build chamber.
Did you know what affects metal powder’s reusability? You can find more information HERE. Let us know in a comment below or on our Facebook and Twitter pages! Sign up for our free weekly Newsletter, all the latest news in 3D printing straight to your inbox!