Why Should You Use Metal 3D Printing for Aerospace? Experts Give Their Advice!
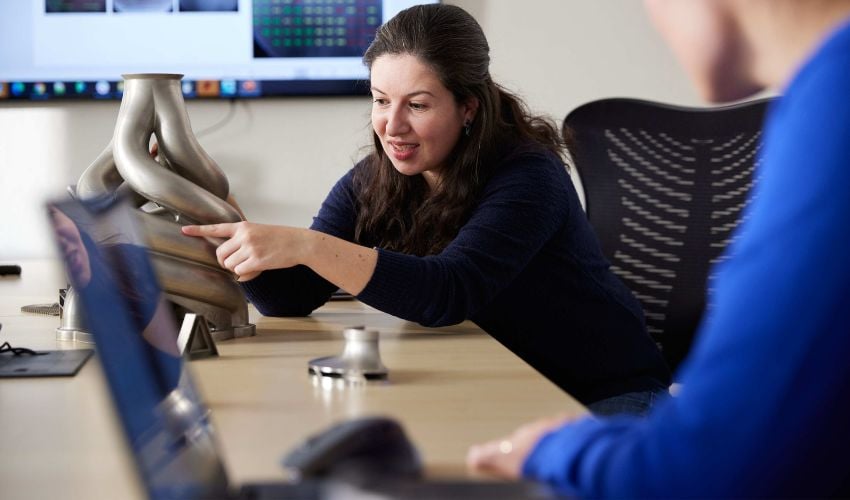
One of the first, and most fervent, adopters of additive manufacturing was undoubtedly the aerospace industry. The sector was drawn to the technologies as a way to help with lightweighting parts (optimizing their weight vis-a-vis their strength). Now, the use of the technologies has only grown, with a report from Strategic Market Research showing that the global aerospace 3D printing market is expected to reach $9.23B by 2023 with a CAGR of 20.23%. And though of course polymer 3D printing plays an important role (especially when it comes to high-performance polymers like PEEK and PEKK), metal additive manufacturing has also been quickly growing in the sector. But how exactly can you use metal 3D printing in the aerospace sector? What are its benefits? How can metal 3D printed parts be certified? To answer these questions and more, we turned to three experts in the field!
Our first expert is Dr. Martin White, the Director for Technical Operations for the Global Advanced Manufacturing Programs Division at ASTM International, an international standards organization. Dr. White oversees all of ASTM’s 3D printing technical programs, focusing on topics that range from Qualification and Certification challenges to material allowable generation, as well as accelerating Standardization and delivering specialist training. The second expert is Brian Hawkes, a technical sales engineer at Velo3D, one of the leading metal 3D printer manufacturers working in aerospace. He has about 10 years working in the aerospace industry, out of a total 20 years as an engineer, where he is focused on designing heat exchangers and complex fabrications. Last but not least, the third expert is Michael York, the Director of Additive Manufacturing at Eaton Aerospace. He is the leader of a program program which has 23 awarded metal AM components spanning commercial aerospace, military, space and aftermarket applications.
- Martin White
- Brian Hawkes
- Michael York
How to Use Metal 3D Printing in Aerospace
As mentioned, metal 3D printing is well established in the aerospace sector as aerospace in general was an early adopter of AM thanks to its many benefits. And adoption is only expected to grow in the coming years. Especially as the aerospace industry in general is moving towards looking at ways to increase sustainability in the sector. Dr. White points in particular to the use of more metal 3D printing in coming years as a need arises to design new components. This will come as aerospace moves towards electrification and alternative sources such as hydrogen. Notably, it is likely that there will be a need to make aerostructure design changes throughout the aircraft and here AM could be a key benefit. The technologies are known for their ability to create geometries that are impossible with traditional methods, allowing users to maximize structure design, performance and safety.
In addition, a number of different 3D printing technologies can be used. Commenting on the different metal technologies used in the sector, Dr. White stated, “In short – all metallic technologies are being considered. The target is always to achieve a sustainable business case, through calculated cost reduction or through performance gains. The sector needs to consider progression beyond certification for a component towards industrialization, where we want to manufacture higher volumes of parts. We see engines using the high-definition capabilities (i.e. complex parts) of powder bed fusion, whilst generally aerostructures are attracted to the high deposition rate and large size capability of Directed Energy Deposition (DED) methods.” Binder Jetting is also a commonly used metal 3D printing technology that is deployed. Mike York further confirms this, mentioning that at Eaton Aerospace “we utilize Laser Powder Bed Fusion (aluminum, titanium, Inconel and stainless steel), Electron Beam Powder Bed Fusion (titanium) and metal binder jetting (stainless steel).”
Materials are also key to the process, as you might expect. Brian Hawkes explains, “The materials that are used are again varied depending on the application and requirements. Titanium has a high strength-to-weight ratio, which is critical for aerospace as lighter-weight vehicles consume less fuel. Nickel-based alloys, like Inconel, can be used in high-temperature environments due to its ability to operate at near-melting point temperature. Aluminum has good thermal conductivity for applications like heat exchangers. Generally speaking, the materials that are widely used in aerospace through traditional manufacturing methods are also great candidates for additive”.
But once the process has been chosen and the materials decided, metal 3D printing has a number of innovative uses in aerospace overall. Hawkes confirms this, commenting, “Additive is great for any application that operates in a high-temperature environment, involves heat transfer, or contains fluid passages, so it’s great for many things related to mission-critical aerospace engine parts, like heat exchangers, impellers, volutes, etc.” Dr. White further noted some impressive applications that were seen at ICAM 2022 last year. This includes end-use parts. For example, Airbus is currently using additive manufacturing to create a bracket on the A350 WXB on the wing pylon as a structural part while fellow aerospace giant Boeing turned to DED Wire Feed technology from Norsk to create a Boeing 787 Aft Galley bracket. The latter is especially notable as it demonstrates a reduction in the buy-to-fly ratio of 85% thanks to reduced material costs and machining time.
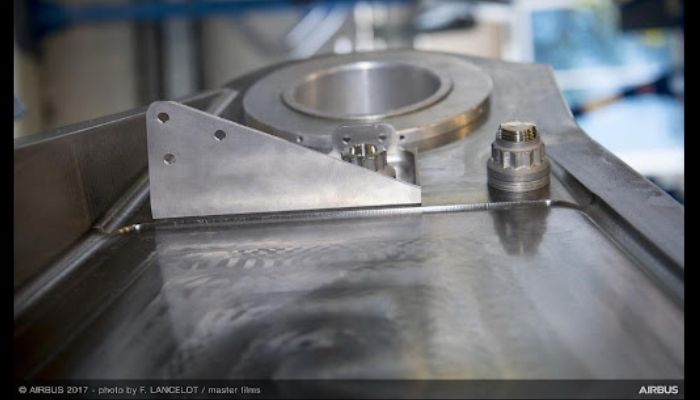
A bracket on the A350 WXB made by Airbus using metal 3D printing (photo credits: Airbus)
What Are the Benefits and Drawbacks of Using Metal AM in the Sector?
As mentioned, additive manufacturing has a number of benefits for the aerospace industry.These include, but are certainly not limited to, the ability to optimize designs, lightweighting and weight reduction, faster and less expensive development, elimination of tooling, reduction in costs and of course sustainability. These are benefits that are seen not just in aerospace of course but are critically important to the sector. This is also why aerospace continues to be one of the largest adopters of 3D printing in general.
The benefits from lightweight, or the optimization of parts to be equally strong while reducing their weight, are particularly crucial. Brian Hawkes from Velo3D notes “Additive gives engineers the ability to produce lightweight structures that meet the design requirements of the part, saving on the total weight of the aircraft but also having the secondary benefit of reducing waste material.” In fact, Mike York notes that when it comes to additively manufactured parts, 20-40% less weight is routine. A number that only grows when you consider AM’s capacity for reducing the number of necessary parts in complex structures like engines.
Moreover, additive manufacturing has benefits overall for the industry as a way to address supply chain issues, as we have seen in the past. Hawkes further commented, “As the supply chain matures and the scalability of AM is proven, spare parts can easily be produced on-demand, reducing inventory requirements, and enabling the manufacturing of parts closer to end users. Supply chains for maintenance parts can also take on a distributed architecture, as the same parts can be procured from a variety of providers without extensive time to develop new tooling.”
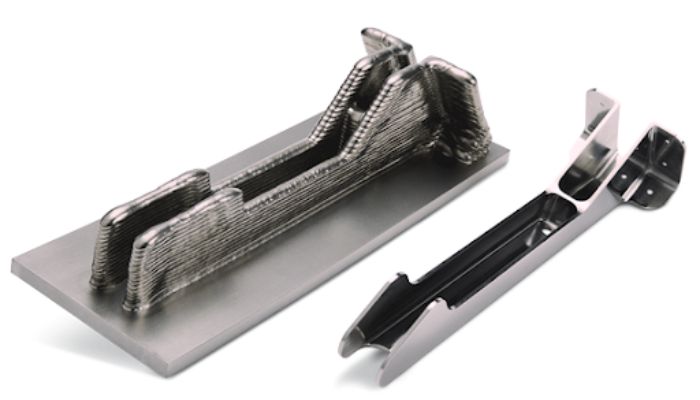
A Boeing 787 Aft Galley bracket made using DED. AM can be useful for making complex parts like this one (photo credits: Boeing)
However, that does not mean adoption of metal 3D printing is not without its challenges. Safety in particular continues to be a factor with users understandably cautious in deploying new technologies. And this is aggravated by the fact that in terms of data from testing, there is much less available in comparison to the huge repository available from testing and operating experience for casting or forged material. This means that users are thus treading a fine line something between acceptable risk and the need to innovate according to Dr. White.
Thankfully, this can be overcome. One example is the work that ASTM is doing to close this gap in gathering data through the Consortium for Materials Data and Standardization at AM CoE. This has the goal of creating high caliber datasets with input from 27 members throughout the AM value chain. Modeling and simulation also could reduce the amount of testing required, making the use of AM in general more sure in the industry.
Certification of Metal 3D Printed Parts for Aerospace Applications
Of course, one of the key questions for any manufacturer looking to adopt metal 3D printing for aerospace is whether the parts can be certified. And though it is possible, it can be difficult. Brian Hawkes points out that “It is a challenge to certify a part for aerospace applications at present because AM is seen as a relatively new technology in the aerospace industry and some standards and guidelines for certifying AM parts are not yet fully developed. In the aerospace industry, a comprehensive approach to certification is required. The qualification must go into detail about all the aspects of a printed part, including material selection, production validation, and testing. But that does not mean that there is no hope. He further adds, “Despite the challenges, the potential is there for AM to revolutionize the aerospace industry with authorities working towards comprehensive standards and guidelines.
Martin White also highlights the need especially for not only aerospace parts to be certified by regulatory agencies such as the FAA or EASA but also for companies to have their own system for quality assurance. He explains, “Given the need to control variability with AM products, there must be a foundation on which qualification and certification can be delivered – i.e. the Quality Management System (QMS). Quality Assurance for AM is a big topic for AM in itself, but at a top level the recommendation is always to ‘make a plan and stick to the plan’. ASTM/ISO consensus-based Standards can also form the basis of an aerospace QMS, as well as certifications based on Standards.”
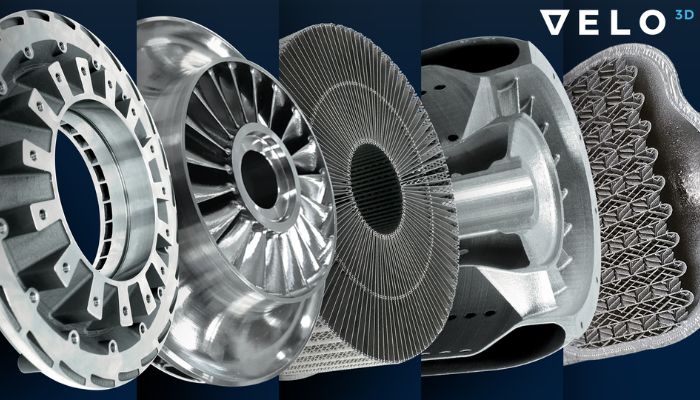
Despite limitations, companies are able to create a number of certified parts using metal AM, like these examples from Velo3D (photo credits: Velo3D)
Michael York notes another limitation, mentioning specifically the cost of qualification, “Qualification cost is higher than conventional for now, but the expectation is that it will come down over time, making it more accessible.” Regardless, as previously mentioned it is in fact possible to have certified parts, even if the process is not yet simple. York explains the experience they have had at Eaton, stating “Eaton Aerospace has certified commercial aircraft metal AM components in production. Typically the certification process requires an immense amount of material and process statistical data demonstrating you have fully characterized a specific material on a specific process and even on a specific serial number of the machine.”
It is clear that there is still much more that needs to be done to standardize and advance certification for metal 3D printed parts. However, it can certainly be done. Standards organizations like ASTM International especially are key in this. For example, ASTM has an Advanced Training Course on Quality Assurance for AM. In addition, these organizations often have certifications which can help develop the competencies of individuals, for example the ASTM Machine Operator Certification which is based on ASTM/ISO 52942 and which can support the demonstration of operator capabilities within a QMS. Additionally, it certainly helps to work with companies who may have experience in working with metal 3D printing in aerospace, whether as a manufacturer of 3D technologies, like Velo3D, or an experience aerospace company like Eaton Aerospace.
However, overall, it is safe to say that metal 3D printing is certainly well suited for a wide variety of applications in aerospace. It has a number of benefits which clearly outweigh the disadvantages and users have the ability to choose between many different processes to get their desired results. That being said, work still needs to be done to make adoption even easier, notably when it comes to certification and qualification.
A Few Last Words of Advice
“You don’t have to do it alone. Collaboration is key – the AM community is fantastic at sharing knowledge and best practices. Being part of the Standards community will provide a great overview of the state of the art, which gaps are being addressed next, and to engage directly with peers” – Martin White
“Additive manufacturing will excel when it’s used for the right application, and the selection of AM technology needs to be in line with the needs of the part. This should be considered in the early stages of the design phase of the project, sometime before the pen has been put to paper. The earlier that you consider the benefits of additive manufacturing, the better your final part will be. If you take all the restraints from the engineer at the beginning of the design phase, you may see an interesting part but it will be designed with freedom and without compromise for the manufacturing technique.” – Brian Hawkes
“The criticality of weight and enhanced performance makes AM an ideal solution. Combine this with the relatively high cost of aerospace components and the improvement in quality from AM over castings and you have a solid business case to implement AM.” – Mike Eaton
What do you think about the use of metal 3D printing in aerospace? Do you use it? Let us know in a comment below or on our LinkedIn, Facebook, and Twitter pages! Don’t forget to sign up for our free weekly Newsletter here, the latest 3D printing news straight to your inbox! You can also find all our videos on our YouTube channel.
*Cover Photo Credits: Velo3D