MELD Manufacturing Talks Solid-State Metal 3D Printing
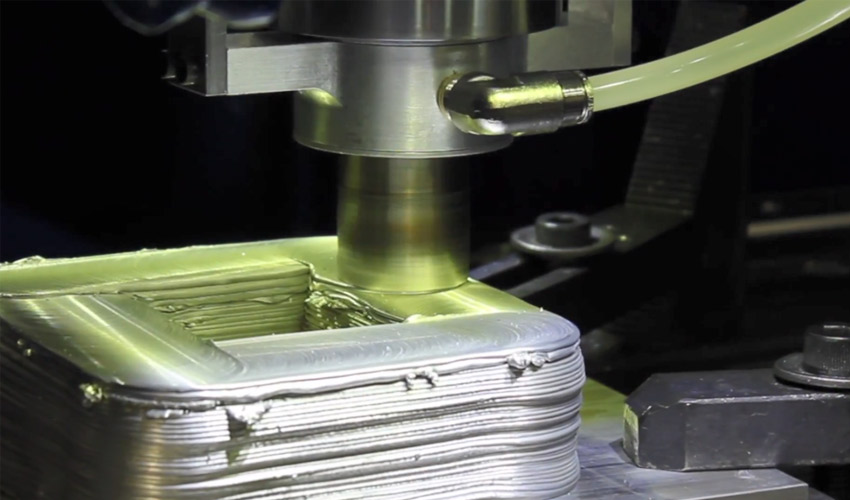
Founded in 2018, MELD Manufacturing has developed a metal 3D printer that’s a bit unusual: while most current solutions rely on fusion processes, thus melting metal particles together, this machine operates by using friction and pressure to make the material malleable. The metal can be deposited layer by layer in the open air, eliminating the stress of a closed, gas-filled chamber. MELD technology also offers the ability to repair existing parts (like Directed Energy Deposition), add features to a part or rework its coating. This makes it compatible with more metals and allows for the manufacturing of larger parts. We met with the company’s founder and CEO, Nanci Hardwick, to learn more about this innovative process.
3DN: Can you introduce yourself and your connection to additive manufacturing?
Hi, my name is Nanci Hardwick and I am an entrepreneur who has been developing MELD technology for over a decade now. I officially launched the company two years ago.
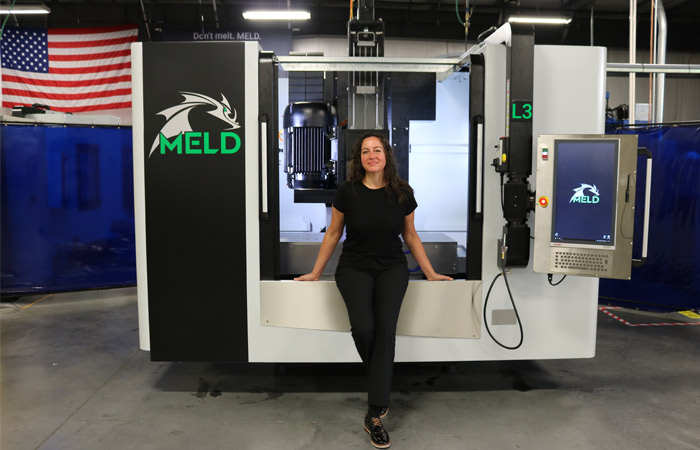
Nanci Hardwick in front of the MELD machine (photo credits: MELD Manufacturing)
3DN: Why did you create MELD Manufacturing?
I believe MELD has the power to redefine the way we do things. The company is contributing to a circular economy by reducing waste in manufacturing and enabling the reuse of materials and parts that would otherwise be discarded. With MELD, we are helping to advance environmentally friendly manufacturing by being energy and waste efficient and operating in the open air.
3DN: How does your metal 3D printing technology work?
MELD is unlike any other printing process and belongs to its own category of processes because it does not melt metal. It relies on a thermo-mechanical process that produces very high pressure and friction: these allow the plastic deformation of the extruded material and of the substrate on which the layers are deposited – remember that plastic deformation corresponds to the irreversible transformation of a part that occurs by rearranging the position of its atoms. It is a versatile technology because it can use any metal. It is simple and offers predictable results. It is fast and capable of printing large parts. It is also unique in its ability to repair existing parts.
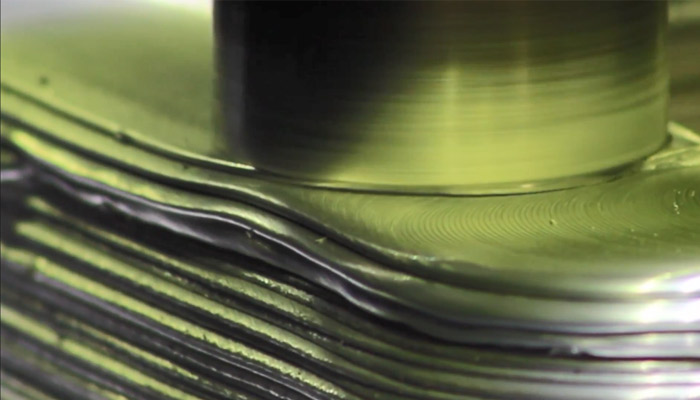
Photo Credits: MELD Manufacturing
3DN: What are the challenges related to large format 3D printing? How do you overcome them?
The main obstacle to large-format 3D printing that MELD has been able to overcome is the printing environment. Fusion-based processes must be done in special chambers that protect the molten metal from oxygen while the part is being built. Beyond cost, this limits feasibility. MELD technology does not use this melting process and can therefore be done in the open air, making it extremely scalable.
3DN: For what type of applications is MELD Manufacturing suitable?
MELD machines can produce large parts using any metal. Whether users are adding features to parts such as bosses, flanges and ribs, building entire parts or repairing parts, the same machine can meet all their needs.
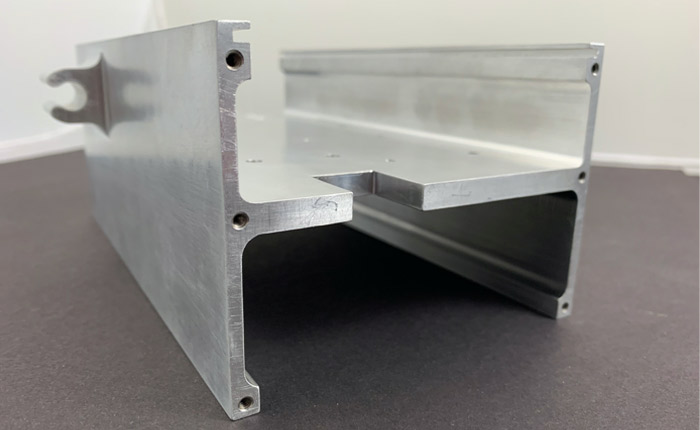
A 3D printed part made with MELD technology (photo credits: MELD Manufacturing)
3DN: Who is your machine for?
Some of the biggest benefits come from using MELD technology to print light, high-strength metals. For example, with MELD, you can print titanium parts. This very expensive material is often used in part geometries that see up to 90% of the material machined. That’s 90% waste. By printing this same part, we only use what we need, so much less material. This reduces the associated costs. Ti64 printed with MELD technology exceeds the ASTM standard for forged materials. This means you can now print parts that were previously only possible by forging. Currently, a user can wait two years to receive certain forged parts. This means that manufacturing times can be reduced from years to hours, with less cost and less waste.
3DN: What are MELD Manufacturing’s future projects?
We are working on other projects with high-value materials, as many of these metals cannot be used in other additive manufacturing processes at all. We look forward to expanding our international distribution network in 2021 and adding to our equipment offering.
3DN: Any last words for our readers?
While we are excited about the part size and material performance achieved with MELD technology, we still need to emphasize its ability to repair existing parts. Not only is reuse essential for our environment, but sometimes millimeters of material can save hundreds of thousands of dollars. You can find more information HERE.
What do you think about this unique metal manufacturing technique? Let us know in a comment below or on our Facebook, Twitter and LinkedIn pages! Sign up for our free weekly Newsletter here, the latest 3D printing news straight to your inbox!