The Top Examples of 3D Printing for Mass Production
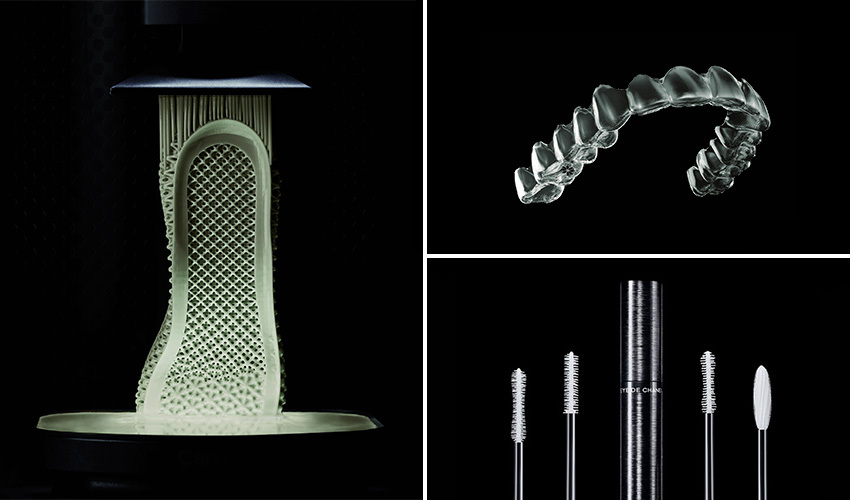
3D printing is no longer exclusively used in the development of prototypes, rather it is increasingly used for end-use parts. Although its viability in large-scale manufacturing has sometimes been questioned due to costs and production times, this perception is changing. More and more companies are demonstrating that it is possible to combine quality, customization and efficiency in high-volume production. From industrial components to customized items, 3D printing is gaining ground as a real solution for mass production. So we decided to explore some specific cases where 3D printing has been key to mass production, creating thousands of parts and therefore demonstrating its potential and challenging traditional production methods.
Adidas and Carbon Join Forces for the Mass Production of 3D Printed Sneakers
In 2016 Adidas partnered with Carbon to revolutionize the way running shoes can be made. In 2017, the two companies released Futurecraft 4D: the revolutionary multi-zone midsole produced in a single printing session and featuring an innovative mesh structure. Together, they launched the production of 100,000 pairs of Futurecraft 4D shoes with 3D printed midsoles. Futurecraft 4D was followed by AlphaEDGE in 2018, to which thickness was added compared to the previous model to the uprights directly under the heel, the point where the runner puts the most pressure during running. In 2021, the Adidas 4DFWD, the third generation of the 4D midsoles, was launched, exploiting the physical property of anisotropy to make the shoe comfortable and functional for running. Also, a collaboration between Adidas and Carbon, the new midsole is made using the Carbon DLS™ process and takes advantage of EPU 44 elastomer, an upgraded version of the previous EPU 41 used for the Futurecraft 4D. This next-generation material is highly resilient, tear-resistant and more sustainable, thanks to a 40 percent bio-based formulation. Adidas 4DFWD is the brand’s latest evolution combining technological innovation, advanced design and sustainability on an industrial scale.
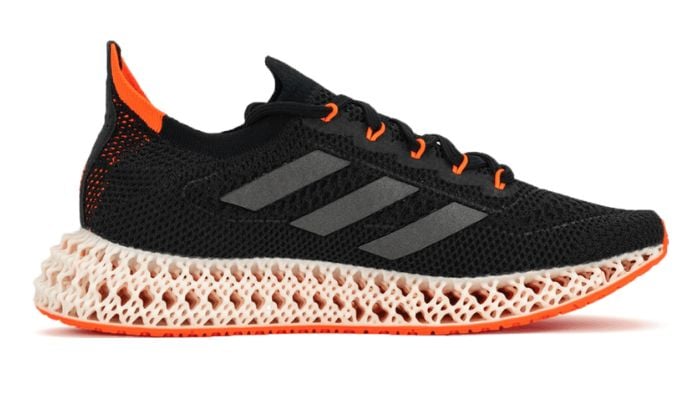
Photo Credits: Carbon
Align Technology Uses 3D Printing for Mass Production of Dental Devices
When it comes to mass production in 3D printing, Align Technology is a shining example. The American company is a specialist in orthodontic solutions made with 3D printing, notably as the inventor of Invisalign. Indeed, it has always been a strong supporter of both 3D printing and 3D scanning, seen through the acquisition of intraoral 3D scanner manufacturer iTero in 2011 and then of polymer 3D printer manufacturer Cubicure in 2024, it has also been a long time partner of 3D Systems. 3D printing is used by Align Technology for everything from molds for its flagship aligners to a palatal expander, the first direct 3D printed orthodontic device from the manufacturer. Considering that the company makes up to one million unique aligner parts per day, with 3D printing relied on to make hundreds of thousands of aligner molds, that is no small consideration. A perfect example of how to combine customization, mass production and 3D printing!
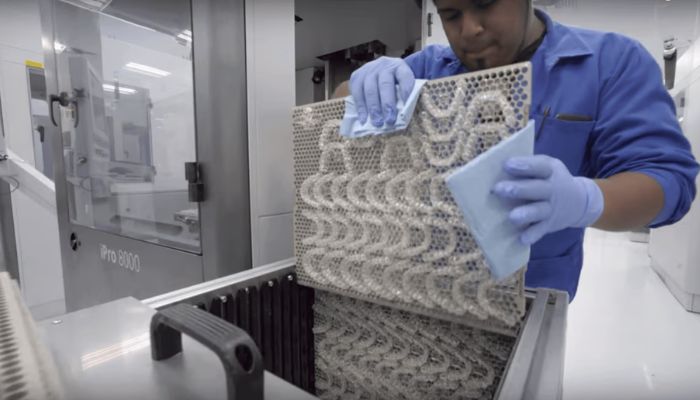
Photo Credits: Align Technology
Chanel Is 3D Printing Mascara Brushes
You may remember Chanel’s Volume Révolution mascara: launched in 2018, it had the distinctive feature of incorporating a 3D-printed brush. The project caused quite a stir at the time because it was a true mass production. Indeed, Erpro 3D Factory, the startup behind the brush printing, claimed that it could design 250,000 brushes every week using some fifteen machines. Since then, the two brands have launched E.Y.E, a made-to-measure 3D-printed mascara service. In concrete terms, thanks to a tablet application, users can choose their mascara brush from 10 models, according to their make-up needs and desires. The brush is then 3D printed with PA 11. We don’t know exactly how many brushes have been 3D printed to date, but one thing’s for sure: this example demonstrates the advantages of additive manufacturing, and how it’s possible to combine personalization and mass production!
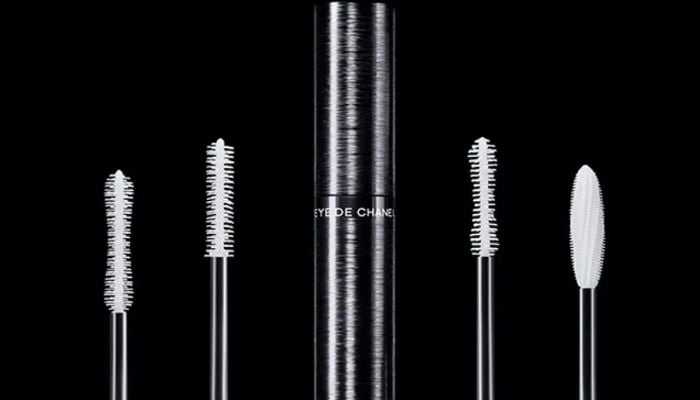
Photo Credits: ERPRO / Chanel
GE Aviation and Mass Production of Aeronautical Parts With 3D Printing
GE Aviation has reached several milestones in mass production using 3D printing. The GE Aviation plant in Asheville, North Carolina, has produced more than 100,000 turbine components made from Ceramic Matrix Composite (CMC) materials over the years, while the plant in Auburn, Alabama, has produced more than 100,000 nozzle components manufactured with additive manufacturing. CMC is an advanced material containing silicon carbide fibers that weighs one-third of traditional metal alloys and withstands twice the temperature, helping to improve engine thermal efficiency, thereby reducing fuel consumption and carbon emissions. The Asheville plant is the aviation industry’s first additive manufacturing mass production site for jet engine components made with CMC, which started in 2014. The Auburn site began producing fuel nozzles in 2015 and was the industry’s first mass production site for aircraft engine components using additive manufacturing.
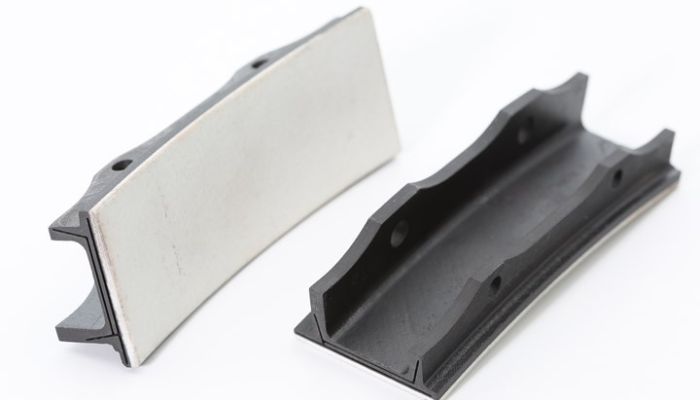
3D printed turbine components in CMC (photo credits: GE Aviation)
Photocentric 3D Prints Badges for Badgemaster
Another example of the use of 3D printing for mass production is the collaboration between UK-based Badgemaster and 3D printer manufacturer Photocentric. Faced with an urgent need to produce customized badges on a tight deadline, Badgemaster turned to Photocentric’s resin 3D printing technology, using its LC Magna machines. This method made it possible to produce 30,000 final parts quickly and with quality, without the need for traditional molds or tooling. The choice of this technology was in part due to the logistical challenges resulting from the pandemic, which limited conventional production. This collaboration highlights the potential of additive manufacturing to respond to industrial demands, offering fast, flexible and efficient solutions, even in high-demand scenarios.
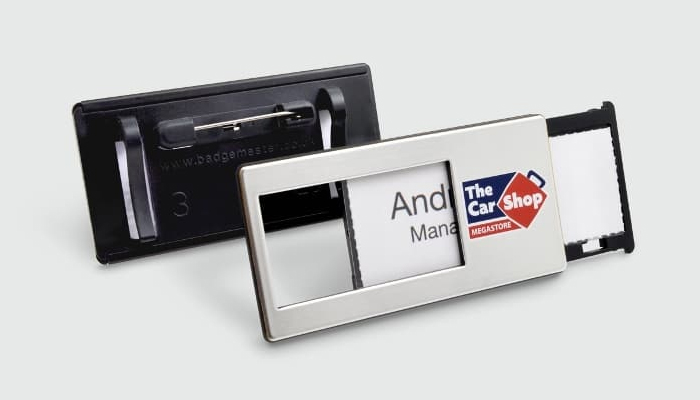
Photo Credits: Badgemaster
Cobra Transforms the World of Golf With Metal 3D Printing
The company unveiled the first mass-produced putter using HP Metal Jet technology, ushering in a new era in golf equipment. Its aim: to combine innovation and large-scale production while keeping costs under control. For several years now, Cobra Golf has been exploring the possibilities offered by additive manufacturing to design ever-higher-performance clubs. Thanks to HP Metal Jet technology, its engineers enjoy unprecedented design freedom, enabling them to imagine structures impossible to produce using traditional methods. Once limited to prototypes, metal 3D printing now achieves sufficient quality and speed for large-scale production. In collaboration with HP, Cobra has been able to accelerate the development of its clubs and make them accessible to the general public.
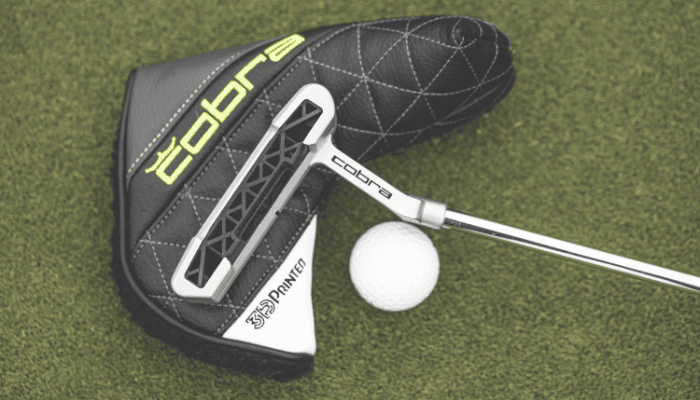
Photo Credits: HP
Mass Producing Prostheses With 3D Printing
Another initiative that combines additive manufacturing with mass production comes from the medical sector. Since 2013, the Irish company Stryker has improved production by making about 2 million prostheses using 3D printing technologies. To do so, it has developed a proprietary material called Tritanium, a titanium alloy designed specifically for printing, with which it has produced both a cementless knee porthesis, called the Triathlon Tritanium, and three different Tritanium spinal prostheses. But how does the Triathlon Tritanium system work? This prosthesis combines an advanced design with highly porous biologic fixation technology designed with SOMA tools and fabricated using Stryker’s proprietary additive technology. Through the life cycle analysis of the knee prosthesis, the company has highlighted numerous benefits of using additive manufacturing, both in terms of economics and material and environmental resource savings. But it doesn’t end there. Stryker has joined the Additive Green Manufacturing Trade Association, with the aim of promoting the use of 3D printing in industry to adopt increasingly sustainable manufacturing choices.
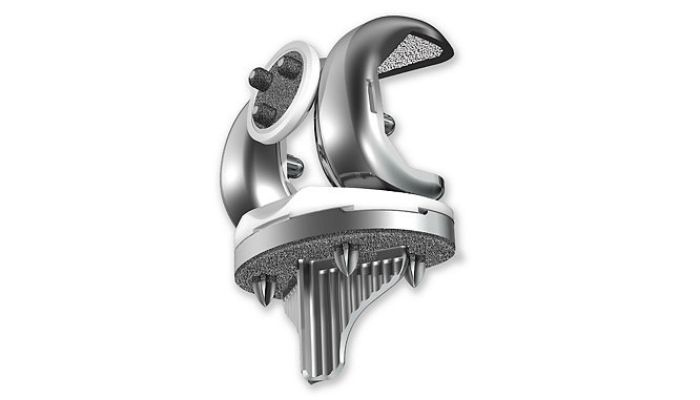
The Triathlon Tritanium model, the uncemented knee prosthesis, can be seen in the image (photo credits:
Bosch Advanced Ceramics Brings Ceramic 3D Printing to Mass Production
It is no secret that ceramics have become key players in the additive manufacturing industry. Bosch Advanced Ceramics has managed to capitalize on this material and 3D printing by scaling up the production of high-precision medical components. These are insulating sleeves, a component of laparoscopic instruments used in invasive surgeries. After a successful sampling phase, the company was able to print 1400 components in a single batch. This level would enable it to meet an annual demand of up to 20,000 units. The development of these insulating sleeves was challenging due to their small dimensions, an outer diameter of just 1.3 mm and a wall thickness of 90 microns. To achieve this level of detail, Bosch Advanced Ceramics used Lithoz’s LCM (DLP) technology, based on a layer-by-layer photopolymerization process that allows complex geometries to be manufactured with high quality control and precision.
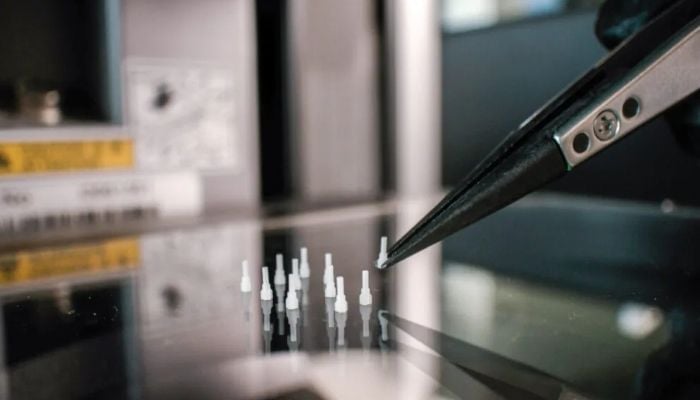
Caption: 3D printed ceramic components ready for use in laparoscopic instruments (photo credits: Lithoz)
Do you know of any other mass production projects in 3D printing? Let us know in a comment below or on our LinkedIn, Facebook, and Twitter pages! Don’t forget to sign up for our free weekly newsletter here, the latest 3D printing news straight to your inbox! You can also find all our videos on our YouTube channel.
What a out mass producing wearable eye protection devices