Makino and Fraunhofer ILT Advance Additive Manufacturing with EHLA3D
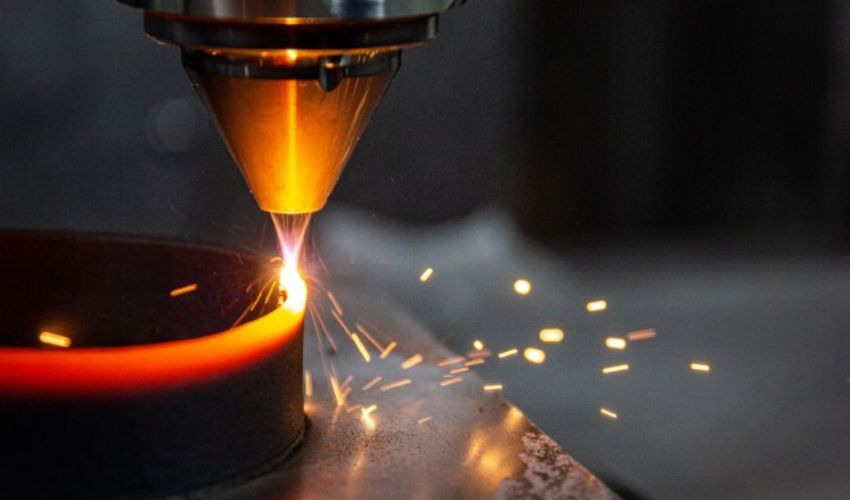
The collaboration between Makino and the Fraunhofer Institute for Laser Technology ILT has yielded a significant advancement in additive manufacturing: EHLA3D. This process, resulting from the integration of high-speed laser cladding technology with advanced five-axis CNC machinery, is transforming the production, coating, and repair of complex geometries using high-strength materials. EHLA3D not only substantially reduces production times but also significantly extends component lifespans across a diverse range of industries, while simultaneously promoting sustainable practices within the circular economy.
Laser technology continues to be a cornerstone of the manufacturing sector, particularly in additive manufacturing. Recognizing this, the Fraunhofer ILT, a leader in laser technology research, partnered with Makino, a globally renowned Japanese machine tool manufacturer. They aimed to alter the extremely high-speed laser cladding EHLA for use on a five-axis CNC platform. This would involve the development of new kinematics that would allow rapid and dynamic movements of the machining head, facilitating the flexible processing of a wide range of geometrical shapes and materials.
Initially focused on AM, the project soon expanded to include repair applications. “Repairs are extremely exciting,” said Min-Uh Ko, Group Leader for Additive Manufacturing and Repair LMD at Fraunhofer ILT. “Many expensive components must be replaced even for minor defects. A flexible system like the one from Makino, with its rotary and tilting table, offers excellent repair options. This approach reduces costs associated with new production, eliminates transportation and delivery delays, and minimizes downtimes. Moreover, repair is a fundamental aspect of the future circular economy.”
Makino’s role in the project extended beyond the CNC hardware to include a complete redesign of process control. The challenge was to tailor the machine for higher accelerations and enhance process control and machine kinematics to ensure precise interaction between the material and the laser beam.
Enhanced Feed Speed and High-Quality Output
The result, developed by Makino’s Singapore subsidiary, is a machine tool that achieves an effective feed speed of up to 30 meters per minute—a significant improvement over more traditional systems. This increased speed is significantly more beneficial for machining large, complex components, drastically reducing production times while maintaining high product quality, which is especially crucial for the toolmaking and aerospace sectors
“Our entry into additive manufacturing, particularly high-speed LMD, is a strategic expansion of our portfolio,” Dr. Johannes Finger, Makino’s project manager, explained. “The new five-axis CNC machine enables us to produce complex geometrical shapes quickly and precisely with materials that are difficult to weld, such as high-strength steels or carbide. This capability is unique.”
The project also focused on repairing and maintaining high-quality tools and machine parts. The adapted EHLA3D technology enables efficient repairs and wear-resistant coatings, extending component life in mining and heavy industry sectors. Makino’s swift implementation of these results in the AML 500 processing machine demonstrates the technology’s practical applicability and significant cost, efficiency, and performance advantages.
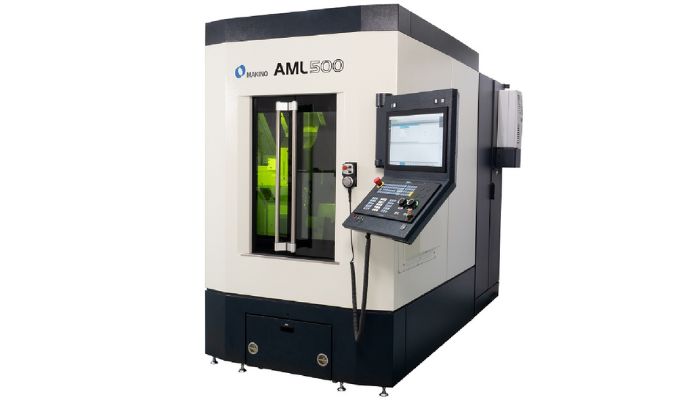
Makino’s latest innovation, the AML 500 processing machine, incorporates the outcomes of the collaborative project and boasts an impressive effective feed rate reaching 30 meters per minute.
Future developments will explore new applications for EHLA3D, particularly multi-material systems and fine-structure printing. The process’s flexibility in material processing opens up possibilities previously unattainable with traditional LMD processes, promising broader industrial applications. To learn more about this achievement, click here.
What do you think of the EHLA3D achievement? Let us know in a comment below or on our LinkedIn, Facebook, and Twitter pages! Don’t forget to sign up for our free weekly newsletter here for the latest 3D printing news straight to your inbox! You can also find all our videos on our YouTube channel.
*All Photo Credits: Fraunhofer Institute for Laser Technology ILT