#3Dstartup: MakerOS’s collaboration platform optimizes the entire workflow for AM companies
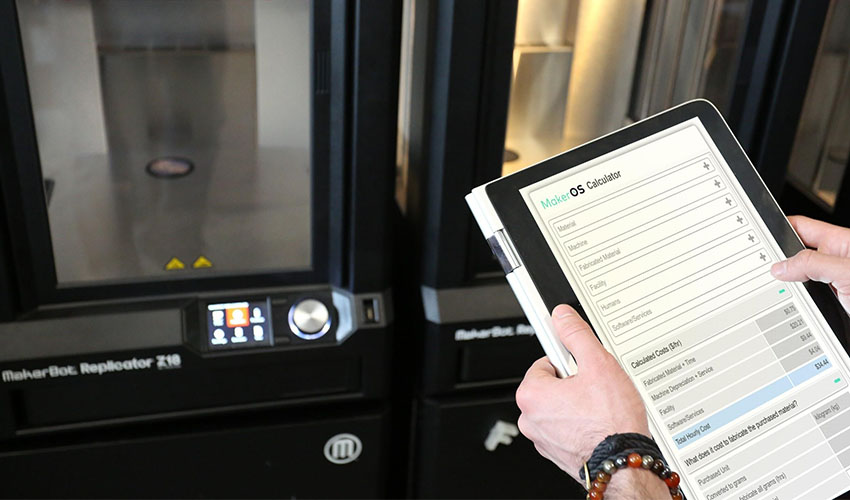
Effective communication and collaboration with clients is at the core of leading successful projects. However, it can be difficult to scale up activity in additive manufacturing when the tools are dispersed across many different platforms. This is the challenge MakerOS identified when it launched its web-based software for companies that offer 3D printing and other digital fabrication services. Essentially, the MakerOS platform is a dedicated online place to communicate, submit projects, view updates and access files and invoices all in one place. We spoke to the CEO of MakerOS, Mike Moceri to learn more about the benefits of using such a platform.
3DN: Can you present yourself and tell us about your relationship with 3D printing?
I’m Mike Moceri, CEO and founder of MakerOS. As a team, we have years of experience working in 3D printing and B2B software. Personally, I have deep experience in manufacturing, design, and software. I’ve quoted thousands of projects, produced hundreds of thousands of individual parts, and continually work with professional services around the world that offer additive manufacturing at MakerOS.
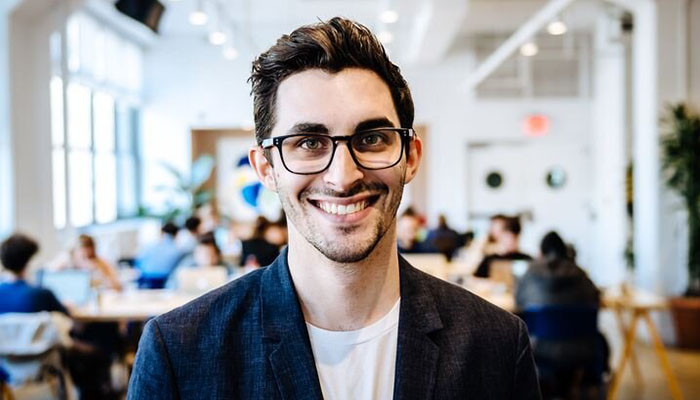
Mike Moceri, CEO and Founder of MakerOS
In 2013, I co-founded the world’s first 3D printing retail service bureau in Chicago. In 2014, I founded Manulith, a 3D printing, and product design agency, where his clientele included Fortune 500 companies within the aerospace, automotive, and medical industries.
3DN: Why did you decide to launch MakerOS? Who is this platform for?
MakerOS was born out of my frustrations from dealing with clients and managing the workflow of projects while I ran a 3D printing service bureau in Chicago back in 2013. At the time, my team and I received an order from a Fortune 500 company to print them approximately 15,000 individual parts for a toy line. We were charging a little less than $1 per cubic centimeter of PLA and Nylon PA12 printing, and that’s how we ended up pricing them for the job.
The project ended up being a very challenging one and after some time gaining more experience over the years, I realized that, considering how immensely large the job was, we should have priced about 70% more than what we originally quoted. There’s a lot we didn’t factor for: the manual time it takes to prep, slice, validate, think through how to plate up and pull off parts; the software costs to execute all of those tasks; how long it actually took to print parts accounting for machine depreciation.
I decided to start a company to help 3D printing and fabrication companies better manage projects, including how to price. First, I spoke with over 100 fabrication shops that offered 3D printing, CNC, and other similar services to see if they were experiencing the same issues I was. During a 5 month period, I personally interviewed and spoke with shop floor managers, business owners, and application engineers across the industry. Did other business owners experience the same problems? Were time and resources being wasted because of inadequate tools to facilitate projects? The answer was an overwhelming yes. So once I validated the problem, I began building the solution. That solution is MakerOS.
3DN: Can you tell us more about the MakerOS platform?
MakerOS is a software platform for 3D printing and digital fabrication companies to better collaborate with their clients throughout the entire lifecycle of the project, from start to finish. The MakerOS platform enables businesses to remotely manage and collaborate with their team to complete projects for clients.
Specifically, the Public Autuoquoter, or PAQ for short, is more than just a quoting tool. What separates the MakerOS Public Autoquoter from other online quoting software is that ours is fully integrated with all of our other project management features — our inventory manager, our online 3D viewer, and our client communication hub — so that the quote flows into the project workflow and all relevant parties are set up for success. Plus, every element is customizable for the business owner so that they can steer clients down the appropriate path based on the needs of their project. There’s less friction, projects are completed faster, and everyone wins.
3DN: Who are your clients?
Our clients are makers. They are modern day alchemists who wish to bend the physical world to their will. They are futurists who hope to build a better world with the tools and technology available to them. Specifically, our clients range from solo entrepreneurs who are just starting out in the 3D printing industry, to small and medium sized shops with a handful of machines, to big innovation labs and makerspaces.
For example, Roboto.NYC is a design and fabrication shop based in Brooklyn, and they’re one of our clients who’ve grown tremendously with the MakerOS software. They really take advantage of the communication and file sharing aspect of our software, which they refer to as their “single source of truth” when going back and forth with clients. Within the first year of using the MakerOS software, they’ve reduced their development cycle from three weeks to just 4 days and increased their revenue by 10X.
Another one of our clients, mHUB, is a product development incubator based out of Chicago, and they utilize the MakerOS software differently than Roboto.NYC. In their incubator, they have a dedicated 3D printing lab with PolyJet, SLS, SLA, FDM, and metal machines that any of their hundreds of members can use. Managing who uses the machine and at what date and time was a challenge before they implemented MakerOS. Afterward, from a single dashboard, the mHUB team is now able to review, accept, and process requests for 3D printing jobs from each member company.
Lastly, Visionminer is one of our clients who recently switched to MakerOS after realizing other 3D printing software could not manage projects beyond the quoting phase. They spent 10 months trying several other systems, but landed back on MakerOS each time because of the way the MakerOS platform holistically manages jobs, from the initial quote to completion of the project. Specifically, the project dashboard allows them to track order requests, client communication, CAD files, and anything else related to the project.
3DN: Do you have plans to add new products?
Yes, this quarter we’re rolling out a new, updated version of our platform to optimize collaboration between clients and manufacturers. These improvements are based on feedback from clients. They include a new online 3D viewer to preview and review files, an updated project management interface that follows agile management principles, more API integrations for smoother workflows, an improved onboarding experience, and more.
We also just launched an effort to fight the spread of COVID-19 called Overflow. Overflow is a supply and sales channel for product makers that we were aiming to launch later this year but accelerated given the COVID-19 global pandemic. We’ve created a dedicated site to connect organizations that need bulk order of tools and supplies to protect against COVID-19 with fabricators and product makers who can produce them. Organizations include local governments, health systems, real estate owners, and local businesses. The network is open to any and all capable fabricators. We at MakerOS, through Overflow, will do all of the heavy lifting to ensure a smooth process so that you can focus on what’s important.
3DN: What is your vision of the 3D printing market?
We envision the 3D printing market to rapidly grow in the coming few years, and yes, we expect many more companies will need MakerOS to remotely manage their supply chains and efficiently manage their entire workflow.
The current global crisis COVID-19 is bringing on this change faster than expected as global supply chains are disrupted, businesses are forced to evolve and potentially work as distributed teams. The 3D printing market will play a large part in how businesses cope with their current business needs and can enable those businesses to manage and collaborate with their company remotely.
3DN: Any last words for our readers?
Wash your hands, practice good hygiene, stay safe, and be kind to others.
You can find more information on MakerOS’ official website.
What do you think of the MakerOS platform? Let us know in a comment below or on our Facebook and Twitter pages! Don’t forget to sign up for our free weekly Newsletter, with all the latest news in 3D printing delivered straight to your inbox!