Lucideon Talks Advancing Metal and Ceramic AM
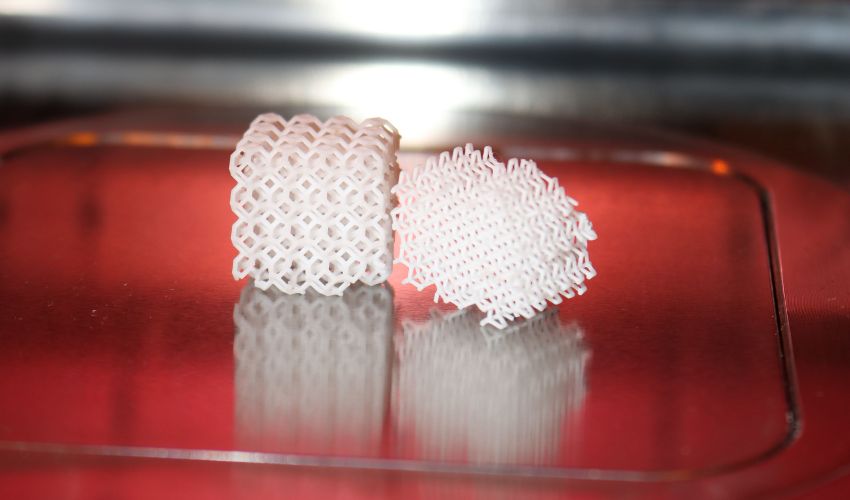
Materials are, and always will be, the core of additive manufacturing. But being able to pick the right one for the right application, and making it with the right process, is a constant challenge for many looking to adopt the technology. And this is doubly the case when it comes to ceramic and metal AM. This is where companies like Lucideon come in. With robust R&D departments and extensive experience in material development as well as the technologies, they are at the forefront of increasing the usability of AM for different applications in a variety of sectors. We sat down with two Lucideon experts, one specializing in metals and the other in ceramics, to learn more.
3DN: Could you introduce yourself and Lucideon?
Robert Crookes: I am head of advanced materials at Lucideon in the UK-based branch. We carry out developmental work of engineering ceramics and their manufacturing processes with applications in sectors including aerospace, defense and nuclear power. This means we develop material formulations, of course, but also the additive manufacturing processes themselves, taking them from the lab stage through to scale.
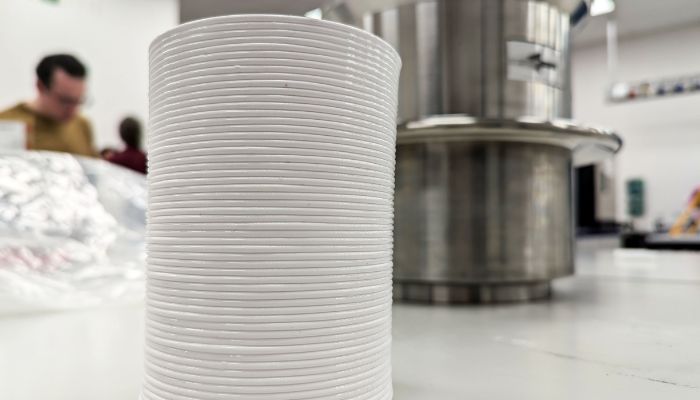
A finished part made with ceramic additive manufacturing
Lucideon is a materials development and validation company. We are materials engineers and scientists, and our goal is to help other companies to develop materials and processes and address challenges in industry. We cover a wide range of industries, although the company goes back to the British Ceramics Research Association (BCRA) which rebranded to CERAM in 1970/1980. In December 2006, the company acquired the US-based M&P Lab. Early in 2014, CERAM and M+P Labs were collectively rebranded as Lucideon under a single company name.
Julius Bonini: I am a metallurgist with 40 years of experience. I am the principal consultant for Lucideon in anything metal as well as additive manufacturing. We have been active in the 3D printing industry since the beginnings of EOS, Renishaw, and other metal solution providers. Now we are working with almost every aerospace OEM in the field for things like failure analyses.
The US branch of the business is known as Lucideon M&P, and we cover a huge range of sectors, advanced ceramics engineering, metallurgy and metal AM and a whole suite of testing for aerospace, space, defense, etc. Our AM work is centered on ceramics and metals, but we also work with construction materials and structures, and pharmaceuticals.
In the US, our services focus more on our role as a testing and consulting house where we are particularly known for stress corrosion cracking (SCC) testing. My group does a lot of failure analyses, particularly with AM, and we are on the cutting edge of 3D printing including in hybrid manufacturing, which combines AM alongside traditional processes.
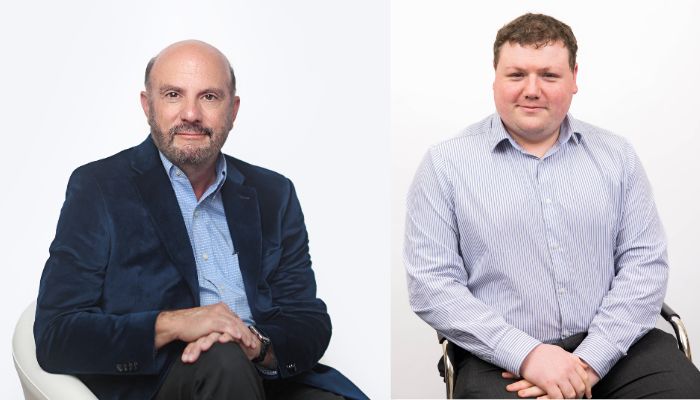
Julius Bonini (left) and Robert Crookes (right)
3DN: What are the challenges in developing materials for AM?
RC: There are a handful of major challenges, and one of the biggest is achieving the correct material densities. In ceramics, you want them to be fully dense to really unlock their extraordinary thermal and mechanical properties, but a lot of AM techniques struggle with that. Some of the mature technologies involving DLP and SLA are good at achieving thin walls, but they are extremely costly, especially when you consider that the cost does not just factor in the printer and materials, but also the necessary post-processing. This makes cost-effectiveness a challenge.
With other technologies, they are almost the mirror opposite: the process is cost effective and you can achieve density, but the tradeoff is the currently possible degree of printing resolution. Although, I will say that ceramics are much more of an emerging material family compared to metal AM, with very few solutions that are fully available, meaning that there is still a bit of a race ongoing.
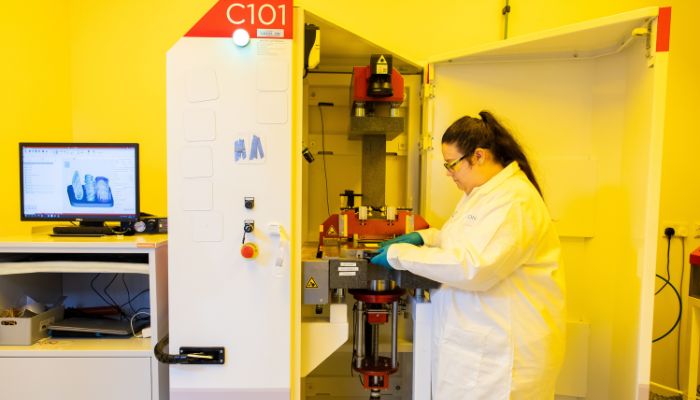
Ceramic SLA at Lucideon
JB: What is interesting is that on the metal side of AM, we have gotten over our major challenges already. A few years ago, we were still dealing with the challenge of achieving fully dense parts, but now across the industry people are getting 99% density or better. That has become common over most of the materials: stainless steels, titanium, etc. The challenge now is in getting new materials and especially the powder in the right way. How do we expand beyond our current alloys and get them prepared for medical and aerospace applications?
Much like Robert was talking about, our biggest challenge is cost- and time-reduction. For example, we have worked on adjusting laser parameters which can result in significant time savings. But when people are trying to cut corners to make it faster, that is when the failures happen. Our job is to see how to adjust that, how to make these tweaks more effective without diminishing the quality of the final part.
The third challenge centers on material design allowables. What do I mean by this? Well, there may be a case where people will want specific properties in AM for different things and that has become the new design standard for the industry. If then EOS can sell a design allowable that people can focus on, it would enable specific properties for technologies like wire or powder bed.
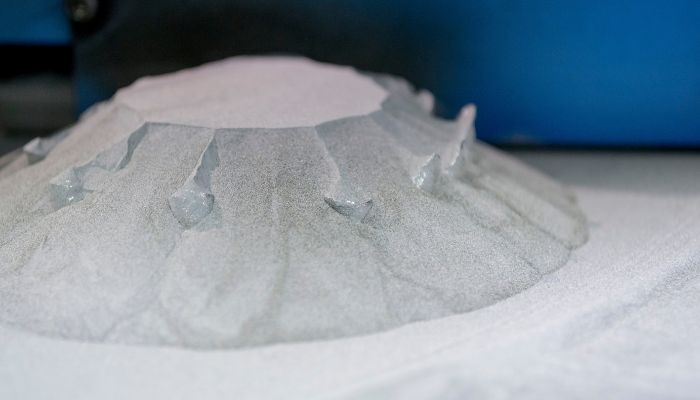
Metal AM powder analysis is a part of what Lucideon does
3DN: Could you talk to us specifically about materials for ceramic and metal AM? What are their specific needs and differences?
RC: With ceramics, we need to be realistic about challenges based on the materials’ brittleness and flaw sensitivity. They create nice, complex shapes, but users need to be careful in how they implement AM due to the possibility of catastrophic failure with sharp edges.
There are some solid and niche applications, like in the medical field which is looking heavily at ceramic AM for implants. We see a lot of clients exploring AM for complex lattice work and light weighting abilities for things like alumina and zirconia. In the end, what we really need is to reliably produce these things without fail. This is why research and expertise on the materials and processes is still so important.
To name some areas where ceramic AM has potential applications, the big ones are defense, aerospace, and nuclear power, even if current work is more exploratory. Some of the industries where ceramic AM is more consistently used are automotive and medical, but Lucideon is not directly handling those. Right now, we are really feeling the way forward with where ceramic AM lies in the industry.
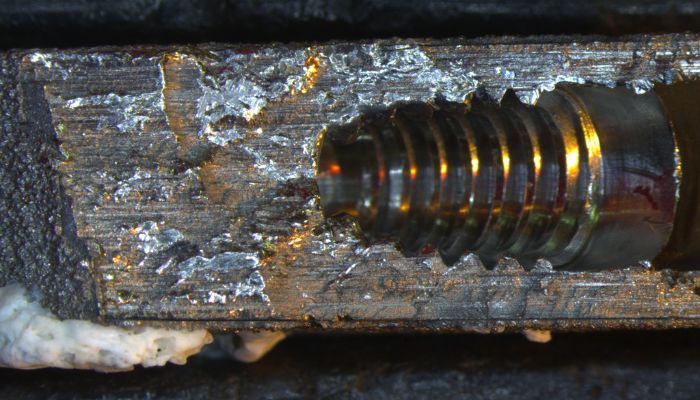
An implant failure analysis for a metal AM part
JB: On the metal side, there are a lot of differences. To illustrate, we can look at aerospace vs. medical, for example. With wire-arc additive manufacturing, aerospace is building the rocket, and with powder they are making engines. They build a lot of big parts that take a lot of time. Again, they run into that design allowable issue because they have fatigue concerns. How do we get design allowable for fatigue resistance for the large components that they are making for space applications?
At the same time, medical wants a lot of small things fast. You can only use titanium and cobalt chrome, but what is important is cost and time. This is where development is important as many in the sector are going back to conventional manufacturing as they see costs going up too much and they can make it quicker that way.
3DN: Could you speak more on the importance of certification? Where is the market right now? How can you help?
RC: It is interesting on the ceramics side because this is something that has been talked a lot about in metal AM, but it is not discussed at all in ceramics. We are not at that point yet, but it is going to be a massive challenge. Even the question of validation is not clear: do you validate each part for each form? That is the big debate in metals right now. If we must do the same in the ceramics route, it will be to an even greater extent, and I would not be surprised if you had to fully NDT (non-destructive test) every part to look for defects. This is one of the areas where we are working to advance the field.
Another is improving material performance. Will a given material sinter to a higher density? Will it flow with the right properties? Then there are considerations for post-processing, which is massive for ceramics, where the printing is less of a complete manufacturing process: post-print, nearly all current processes require debinding and sintering which can introduce challenges to the component. That is another aspect of Lucideon’s offering, with all the post-processing of the component.
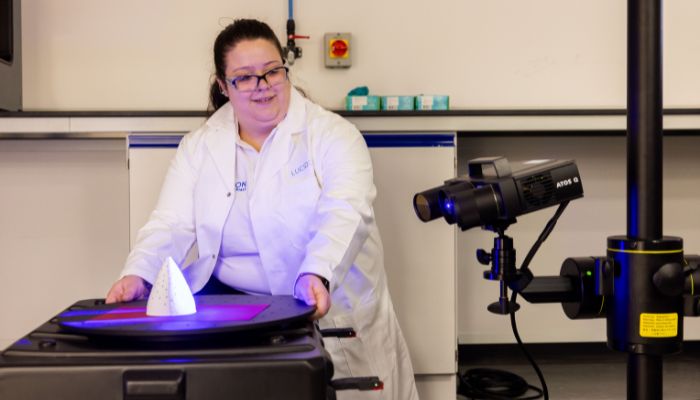
Analyzing a ceramic AM part
JB: It is complicated on the metal side. We have three certifying agencies in the USA: the FAA, FDA and NASA. NASA is for above the atmosphere; the FAA is for atmosphere to ground; and FDA is for all the people on ground. They have very rigorous certification processes to go through and for AM it has always been a challenge. However, now that we are a little more mature, it is much easier now to get a new component certified because we have all that data from previous cases, even if it is still a challenge.
Why? Well, if we make a change to one thing, it is necessary to go back to the certifying agency. We used to NDT it and just sacrifice a part; now we can often use test data from coupons and historical data instead. But now people are implementing machine learning and AI to predict product performance based on build information. It is becoming the new thing that people want to observe because it will save them long-term costs and time and they are trying for this validation. I am not an expert, but it looks interesting and will probably help develop the field even further.
3DN: What sectors are you targeting with your 3D printing materials? How can Lucideon’s consulting services help in choosing the right material for a project?
JB: That is exactly what we do. When a customer comes to us with a problem in AM, the first thing to ask is what material? How do I make it? What machine? What about post-processing? We work from the first point to the last point.
We know the additive manufacturing process so well that we know where the problems are, and people hire us to alleviate those problems before they even start. That’s a quality that is based on a lot of experience. We know who the good equipment manufacturers are, the good material providers, the correct heat treatment – we can provide services at all levels.
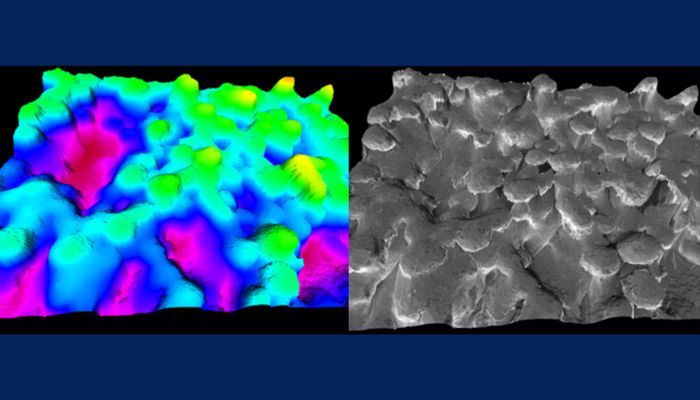
Metal AM surface analysis
RC: There are a few different things we offer. We have services around trialing SLA technology; in that service we offer the potential to trial the production of the part in-house through one of these newer high-resolution technologies. That is off-the-shelf materials and people who are just testing the waters. They have seen 3D printing, and they want to know if it is applicable – they are trying it out.
Another big element is our strong consultancy offering on selection of materials and general advice on what AM process to look into for ceramics. Ceramics is a big enough challenge speaking to most engineers because they do not know how to use them. As a result, we do a lot of advising on the proper use of ceramics and that carries over into AM in a big way.
To give an example, a lot of times in aerospace they are moving from metallic to ceramic, and the client’s question is should we use AM in this. Now there is a conflict because what you designed in metallics is not the same and we need to have the journey of how to adapt that design for ceramic AM.
However, our greatest expertise is in formulations and understanding materials and how they behave. We can formulate them to give them the properties they desire. As Julius said, there is not an established supply chain for this quite yet in ceramics, but we have the network for convention ceramic manufacturing already. This makes it easier in terms of tracking down suppliers and materials because if we cannot do it by ourselves, we know the players who can. At the end of the day, we are material scientists, and our first task is having that conversation with the client about what are the relevant properties, what do they need and advising them on that.
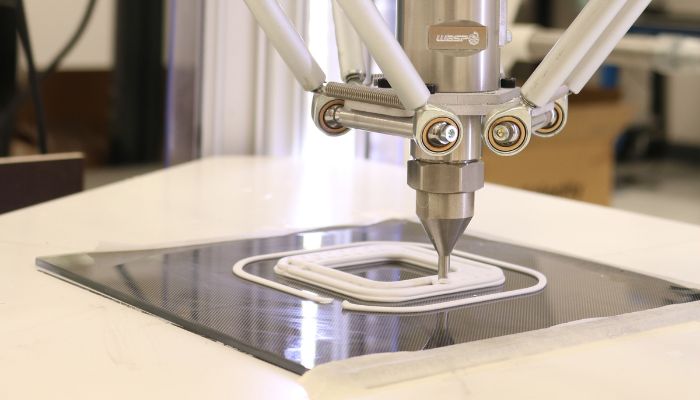
Ceramic AM robocasting is one method used by Lucideon to make parts
3DN: Any last words for our readers?
JB: We are so excited about hybrid manufacturing; it is our new challenge. What I mean by that is by combining conventional manufacturing and AM, something unique is formed which enables design possibilities that really take the best of both worlds. Now is the time to see what we can do with opening the design world and showing even more to more people the potential of this technology. I really am excited
RC: For me, I think that the thought to take away is that additive manufacturing of ceramics is so much more than just the 3D printing process, and that is what we really bring to the table. We bring the formulation of the material beforehand; how it works with the printer; and then how to process this outside of the printer, for example removing binders and sintering. All of this is what we have established expertise in, and this is what we need for a full picture of AM. There are a lot of people who are focusing on the 3D printing technology, but a lot of expertise is needed in how to process after the printer and that is where Lucideon shines. You can find out more about Lucideon HERE.
What do you think of Lucideon? How do you think that expertise can help with the wider and more sustainable adoption of metal and ceramic AM? Let us know in a comment below or on our LinkedIn, Facebook, and Twitter pages! Don’t forget to sign up for our free weekly Newsletter here, the latest 3D printing news straight to your inbox! You can also find all our videos on our YouTube channel.