LLNL Develops Novel, Fast-Curing Silicone Ink: A Game-Changer for Silicone 3D Printing
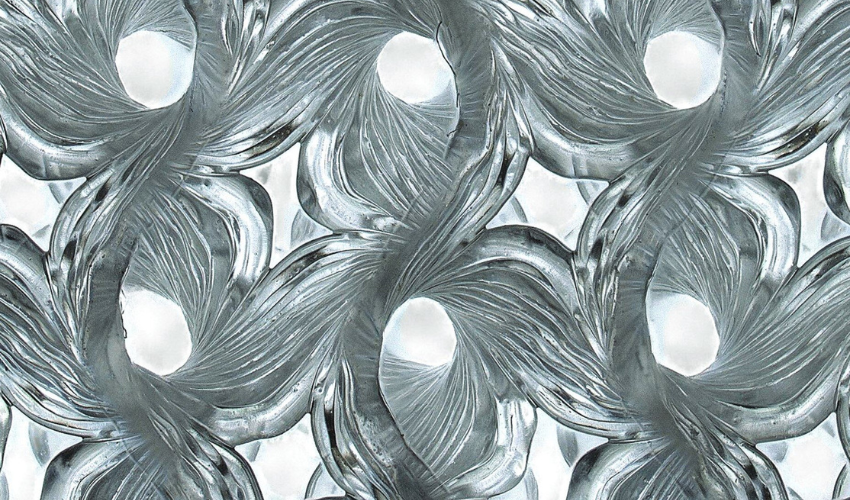
While 3D printing has been around for decades, silicone 3D printing technology is something relatively new. The material is compatible with photopolymerization and material extrusion, but there are relatively few manufacturers making silicone 3D printing solutions. That does not mean the material does not have attractive qualities: it is biocompatible, flexible and resilient. It is also used for a wide range of applications, like protective materials, biomedical devices, flexible electronics and more. Given the wide range of applications, it is no wonder that researchers are working on making the material more suitable for 3D printing. Now, scientists at the Lawrence Livermore National Laboratory (LLNL) have developed a novel silicone ink for 3D printing that promises to change the game.
The team’s new silicone ink is not only fast-curing, but also allows for prints that are bigger, taller, thinner and more porous than ever before. The key to the new material is that it is actually in two parts. Silicone inks have both a catalyst (which speeds up a chemical reaction) and a crosslinker (which chemically joins molecules together). When the catalyst and crosslinker mix, they slowly gel together to bind structures. So, the LLNL researchers separated the catalyst and crosslinker. Then, the two are mixed during the printing process, producing silicone structures by inline mixing and co-extruding both materials. After the ink passes through the nozzle, it rapidly becomes rigid, increasing its self-supportive capacity.

Two-part “fast cure” silicone-based ink for direct ink writing, mixes just before printing, sets quickly at room temp, allowing for longer print times, ensuring structures will not collapse or sag, even in complex shapes and configurations (Image credits: LLNL)
“Since the ink is kept separate, you don’t have to worry about the print time because it is not going to solidify in the syringes,” said Anna Güell Izard, a postdoc in the Materials Engineering Division (MED) and the paper’s first author. “It’s also sturdier because the layers are gelling as you’re printing, so your structure will not start sagging.”
LLNL’s ink is designed for direct ink writing (DIW), a process that entails forcing ink through a nozzle, whereafter it rapidly solidifies. It differs from FDM in that it prints using material that is already liquid, rather than melting a solid filament. Often, DIW is suitable for highly viscous resins that are difficult to use with other AM processes. According to LLNL, DIW is still limited to manufacturing relatively simple, planar designs because of the low self-supporting capabilities of silicone-based inks.
Addressing DIW Limitations with the Novel Silicone Ink
What’s challenging about DIW silicone printing is that the process is quite sensitive. The machine’s accuracy, nozzle quality and ink properties must be perfect, and the structure has to support its own weight throughout printing and thermal curing in an oven. Additionally, printing has to be completed before the ink begins to set. With all of those difficulties in mind, LLNL researchers sought to create their new silicone.
The novel ink from the LLNL can form structures that were previously impossible to print in silicone. Superior shape retention can be achieved, and tall parts with overhanging features can be made. What’s more is that the fast-cure ink does not require any extra curing, support structures or suspension baths.“There are other methods for silicone direct-ink writing, but this is the simplest solution and the bulletproof one,” Güell Izard said.
LLNL’s Fast Cure formulation permits researchers to have greater control over the mix-to-print-to-cure time. The team reported that they were so excited with their results that they printed several configurations that were previously unattainable with silicone, like tall and slender structures, acute and unsupported overhangs and even cubic octets with porosities (empty spaces) of up to 90 percent.
“These beautiful cubic octets and overhangs turned out of the oven exactly as I printed them with the walls totally firm, while the baseline ink structures collapsed,” Güell Izard added. “It made us feel like we were onto something; that all this magic chemistry was doing its job.”
Going forward, the team will fine-tune the ink’s properties. They also want to apply the concept to other materials in hopes of unlocking new structures. To learn more about the research, read LLNL’s press release here.
What do you think of the LLNL’s novel silicone ink? Let us know in a comment below or on our LinkedIn, Facebook, and Twitter pages! Don’t forget to sign up for our free weekly Newsletter here, the latest 3D printing news straight to your inbox! You can also find all our videos on our YouTube channel.
*Cover Photo Credits: LLNL
Great!