Lithoz Premieres CeraFab S320 at Formnext: Ready for the Series Production of Medium-Sized Ceramic Parts
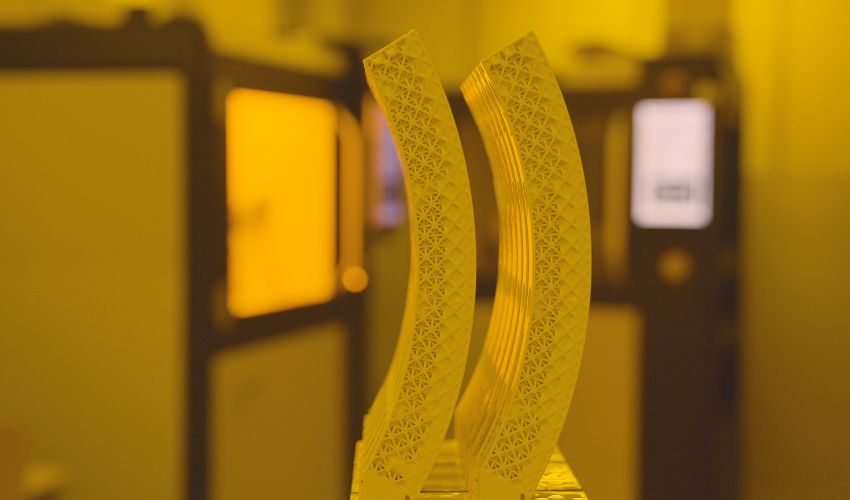
Lithoz is committed to delivering high-performance solutions for technical ceramics. The company’s innovative developments – including powerful ceramic materials, LCM technology and the CeraFab System series – are proof that Lithoz is living up to these promises. Now, just in time for Formnext, the company is adding the new CeraFab System S320 system to its range of printers. This ceramic 3D printer for the serial production of medium-sized components is aimed at meeting the needs of the aerospace and semiconductor manufacturing industries.
CeraFab S320 for Medium-Sized Parts and Series Production
The CeraFab System S320 ceramic 3D printer is Lithoz’s answer to the industry’s demand for larger, more precise parts in series production. The new machine is aimed at increasing production capacity and enabling the efficient production of medium-sized ceramic parts in large runs. This is ensured by the winning combination of Lithoz’s LCM technology with a large build platform. At 246 x 130 x 320 mm, the latter is five times larger than the platform of the CeraFab S65. This increases the maximum number of parts per print job, allowing for the scaling up of the LCM process.
The printer also impresses with a speed of up to 150 layers per hour in a thickness of up to 200 µm and a resolution of 60 µm. With its 4K projection system, the S320 functions as a perfect complement to the ultra-precise S65. With these features, the CeraFab S320 offers a powerful tool for series production of industrial and aerospace applications.
Lithoz partners have already used such CeraFab printers to achieve breakthroughs in industrial applications. Alumina Systems, for example, used Lithoz LCM technology to manufacture a semiconductor ALD ring with a diameter of 15 inches. To ensure constant gas flow and pressure even when using reactive gases, alumina ceramics were used. The combination of ceramics with the Lithoz 3D printing process provided numerous advantages for the production of the gas distributor ring.
Notably, Alumina Systems noted that it was possible to significantly reduce manufacturing costs while still achieving more lightweight and thin-walled inner structures, boosting performance. Using conventional methods, it would not have been possible to manufacture this sophisticated design with the required precision in a cost-efficient manner.
3D-Printed Ceramic Casting Cores for Aerospace and Industrial Gas Turbines
When it comes to high-demand sectors, the CeraFab S320 plays to its strengths perfectly. One field with particularly high requirements is aerospace. Aircraft engines need to be environmentally friendly and fuel-efficient and therefore require innovative turbines and efficient cooling. Complex components are required to meet these demands. LCM technology is able to efficiently produce such functional components with highly complex geometries.
For example, 3D-printed ceramic cores for aircraft turbine blades made from superalloys and ceramic casting cores for industrial gas turbines have already been produced on the CeraFab S320. In both cases, the precision (60 µm) of the system and the implementation of complex designs were crucial in achieving improved end results. The optimized design of the cooling channels was noticeable in the increased efficiency of the aircraft engines. In addition, the CeraFab S320 can reduce development times and significantly accelerate the time to market. The new ceramic 3D printer thus meets another requirement of the current aerospace industry.
At Formnext, the CeraFab S320 and its possibilities will be given an ideal stage to show the printer’s performance and specific applications. Lithoz will be presenting the above-mentioned applications on its stand C49 in Hall 11.1 and you can marvel at the semiconductor ALD ring as well as industrial filter devices and ceramic casting cores and radomes for aerospace. You can also get an idea of the new CeraFab S320 and other Lithoz solutions on site.
In addition to industrial applications, the latest breakthroughs in medicine and dentistry will also be on show at Formnext, for instance a replica of the 3D-printed subperiosteal jaw implant from zirconia that was implanted in a world first surgery earlier this year. Further information on the CeraFab S320 ceramic 3D printer and its applications can be found HERE.
What do you think of the new CeraFab System S320 ceramic 3D printer from Lithoz? Let us know in a comment below or on our LinkedIn, Facebook, and Twitter pages! Don’t forget to sign up for our free weekly newsletter here for the latest 3D printing news straight to your inbox! You can also find all our videos on our YouTube channel.
*All Photo Credits: Lithoz