Lighter Antennas Thanks to 3D Printing?
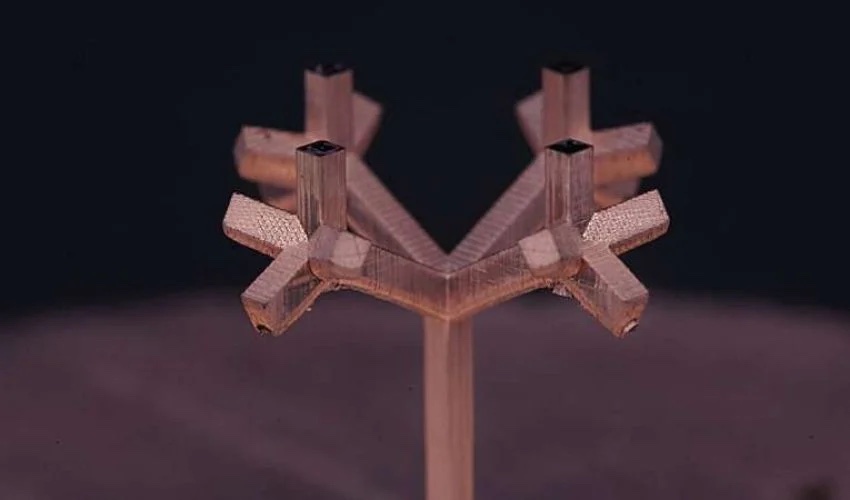
As our modes of communication have gone wireless, the internet has become ever more important and aerospace applications multiply, the need for efficient, lightweight antennas has become urgent. 5G and 6G have accelerated this, and industry players need to find solutions to produce faster, better, all while cutting costs. In the face of such challenges, additive manufacturing could provide some answers, given its flexibility and the geometries it can produce. A team of researchers led by Xiaoyu (Rayne) Zheng, Associate Professor in the Department of Materials Science and Engineering at UC Berkeley, has been studying this issue. They have developed a 3D printing platform that will enable complex antennas to be designed as quickly as possible.
A recent study published by Mordor Intelligence showed that the antenna market is expected to reach $34.24 billion by 2029, representing annual growth of 7.8% over the analysis period (2024-2029). As we all know, antennas are becoming increasingly numerous, as they are essential for communication. In fact, they are components in all radio equipment capable of transmitting and receiving energy in the form of electromagnetic waves. We’re talking here about the Internet of Things, 5 and 6G, certain satellite communications, and so on. These components need to be as small and light as possible, while offering high performance and speed. Most often, they are manufactured by machining, but 3D technologies are of growing interest, notably thanks to the integration of lattice structures that can considerably reduce the final weight of the antenna.
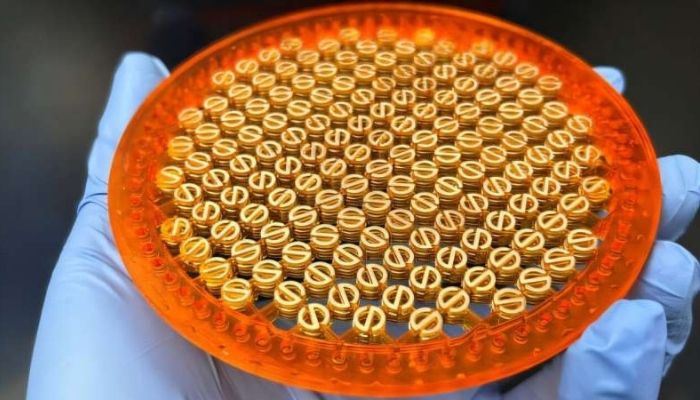
Phase gradient emission grating with three layers of interpenetrating S-rings and dielectric materials (photo credit: X. Zheng)
Antennas and 3D Printing
The use of additive manufacturing for antenna production has certain limitations. The processes currently available on the market do not allow certain materials to be mixed – typically, a choice has to be made between an all-dielectric or all-metal antenna. As a result, certain applications cannot be realized. And when it is possible to mix them, we have to go through very cumbersome post-processing steps or tool and substrate paths that make it difficult to make full use of additive manufacturing. In short, current solutions are not enough.
With this in mind, Zheng and his team have developed a new 3D printing platform. He explains, “The new platform—dubbed “charge programmed multi-material 3D printing (CPD)—is a universal system for rapid production of nearly all 3D antenna systems. It can pattern highly conductive metals with a wide range of dielectric materials into a 3D layout.”
What have they actually done? The CPBD process controls charge polarity through multi-material photomonomer printing. The team uses stereolithography to deposit photopolymers in different locations, creating a kind of 3D mosaic. These photopolymers will then attract metal ions deposited by metal plating on the 3D structure. This allows us to control the design of the final antenna.
Zheng adds, “It allows essentially any complex 3D structure, including complex lattices, and has demonstrated deposition of copper with near pristine conductivity, as well as magnetic materials, semiconductors, nanomaterials and combinations of these.”
The team is working on the creation of complex antennas, but they want to go even further, with the aim of making the manufacturing process quicker and easier. You can find out more in the study published HERE.
What do you think about using 3D printing to produce antennas? Let us know in a comment below or on our LinkedIn, Facebook, and Twitter pages! Don’t forget to sign up for our free weekly Newsletter here, the latest 3D printing news straight to your inbox! You can also find all our videos on our YouTube channel.