Metal 3D printer uses LED instead of laser or electron beam
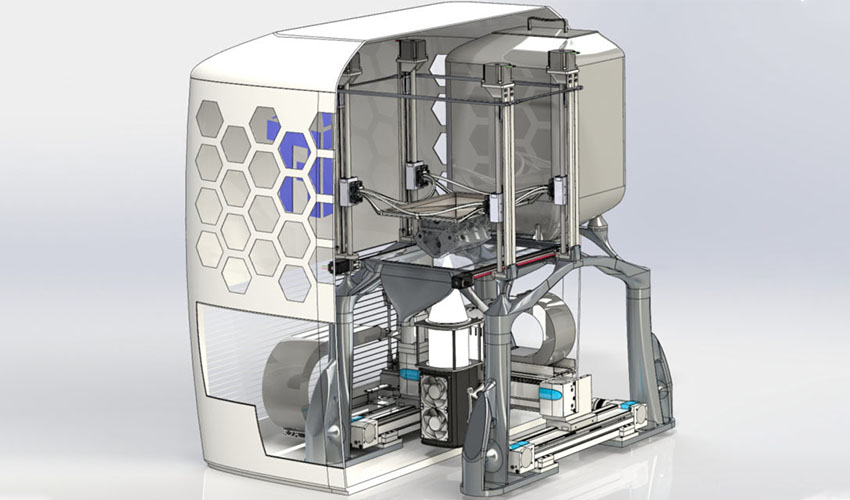
Due to the COVID-19 crisis, both staff and students have been in the home office at Graz University of Technology since mid-March. However, this has not prevented the research department of the Austrian university from presenting a newly developed powder bed process for the additive production of metal parts. Up to now, the heat source used to melt the metal powder has typically been a laser or electron beam. These techniques are more well-known as Selective Laser Melting (SLM) or Electron Beam Melting (EBM). The new system from Graz University of Technology introduces a change: the machine uses a high-power LED source for melting the individual layers. The name of the new process is directly derived from the innovation: Selective LED based Melting (SLEDM). It has been developed in the last few months by the Institute of Production Engineering under the direction of Franz Haas – a patent application has already been filed.
To what extent does this process differ from conventional metal 3D printing processes and what benefits does it offer? According to the Institute of the Graz University of Technology, the shortened construction time should play a major role. High-performance LEDs coupled with a complex lens system allow the focus diameter of the LED beam to be variably adjusted, currently between 0.05 and 20 mm. This means that large-volume areas or components can be manufactured up to 20 times faster, as less time is needed to scan the cross-sectional areas. At the same time, there is no need to dispense with filigree internal structures. For comparison, laser-based systems currently offer a variable focus diameter between 0.07 and 0.5 mm.
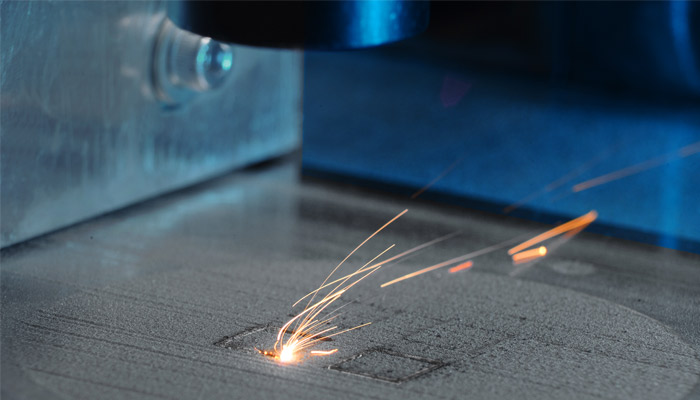
Thanks to the variable diameter of the LED beam, large areas can be produced faster. On the other hand, laser-based systems currently offer a focus diameter between 0.07 and 0.5 mm | Credits: Fraunhofer ILT
Another difference is the direction of the print. With the system from Graz University of Technology, the component is printed from top to bottom, it is exposed, so to speak, and is not covered in the powder. This is primarily intended to reduce the amount of powder required and eliminate laborious post-processing. “The time-consuming, usually manual post-processing, which is necessary with current methods, for example to smooth rough surfaces and remove supporting structures, is no longer necessary and saves further valuable time,” says Institute Director Franz Haas.
The TU’s machine should also be cheaper in terms of equipment costs. However, more detailed information on this has not yet been published. Currently, the SLEDM process is focused on two main areas: the mobility sector and the medical implants sector. For medical applications, the research team is imagining producing bioresorbable metal implants. These include screws made of magnesium alloys, which are adapted to the patient and dissolve after the fracture has grown together. These can then be manufactured directly in the operating theatre and implanted in the patient.
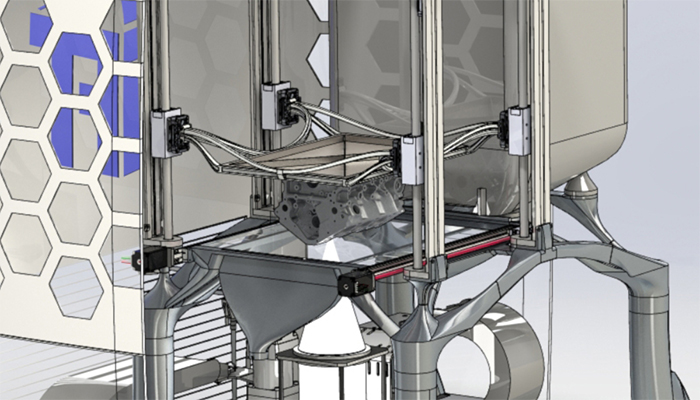
In the SLEDM process, the component is printed from top to bottom
For sustainable solutions in the mobility of the future, the production of components for battery systems with the SLEDM system could be possible. “We want to make additive manufacturing using SLEDM economically viable for e-mobility and position SLEDM in this field of research at an early stage,” says Haas. The next step in this technology should then produce a marketable prototype made by TU Graz. You can find further information HERE.
What do you think of this LED metal 3D printer? Let us know in a comment below or on our Facebook and Twitter pages! Sign up for our free weekly Newsletter, all the latest news in 3D printing straight to your inbox!
What is laser? Laser is built with same technology than LED but it has optics. I don’t think you can call this a new technology… And good luck melting 20mm spot diameter of metal powder. To melt 0.1 mm spot with 0.1 mm laser you need around 150-200W laser. The printing speed is about 1 m/s. So calculate that to 20mm spot size… kWs of energy perhaps?
Another thing… printing from bottom to top? You can do that with laser. But why it is not printed that way? Because of the “where does the smoke and waste from melting go?”. I assume it goes in the part itself and makes a lower density and worse mechanical properties.
As a metal printer manufacturer, I think that articles about this printer are full of useless functions advertised as something revolutionary.