Copper Laser Fusion: AFU Overcomes Density Challenge
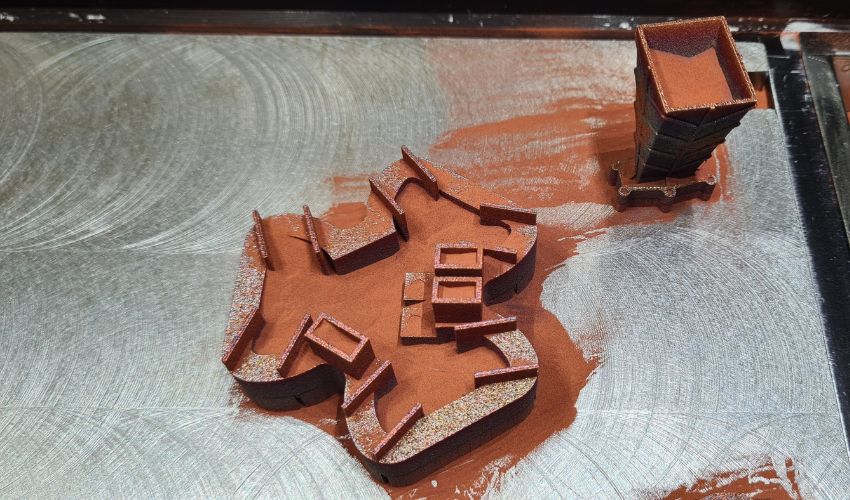
AFU, a French company specializing in machining, has been investing in metal 3D printing since 2014 to expand its capabilities and produce more complex components. Now equipped with three machines, it has worked for two years on copper parametrics, and more specifically on the copper-chromium-zirconium alloy (CuCrZr). The aim was to be able to 3D print copper parts with excellent density while preserving the intrinsic properties, all on a standard machine equipped with a 400W infrared laser. This challenge was successfully met, as the company has been able to manufacture dense parts (>99.5%), with a layer thickness of 40 microns, since summer 2024 – a first in France.
AFU has been helping industrial customers from a wide range of sectors to realize their projects for many years. In 2014, it turned to metal additive manufacturing, and more specifically to laser powder bed fusion (L-PBF / SLM), in order to offer more complex, bespoke parts or even prototypes in record time. The company offers a wide range of metals, including copper, renowned for its thermal and electrical properties. However, the latter are also the reasons why copper in powder form is more difficult to print than other metals such as titanium, aluminum or steel.
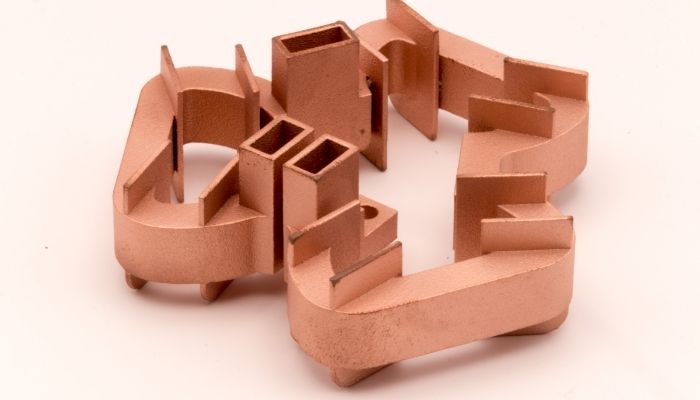
3D printed CuCrZr inductor
3D Printed CuCrZr Inductor
In recent years, the additive manufacturing market has seen numerous developments around copper, a metal particularly appreciated for its conductivity, ductility, wear resistance and corrosion resistance. It is therefore ideal for applications in aerospace and electronics, the manufacture of heat exchangers or inductors, and so on. However, copper is not an easy metal to print, especially when using a machine that employs an infrared laser, as is the case with most laser fusion solutions.
Copper dissipates part of the laser’s energy, resulting in a significant loss of power, which prevents optimum fusion. With an infrared laser of 200W or 400W power – which corresponds to the majority of metal solutions on the market – fusion is not complete, creating fragile zones, excessively high porosity and low conductivity. In concrete terms, 100% of the laser’s power would have to be used to obtain satisfactory results and good density. However, 60% of the energy transmitted to the material is lost (dissipated by the powder or reflected during melting). It’s clear, therefore, that with a laser of this power and without any specific development, we cannot compensate for these losses, and the resulting parts will be porous.
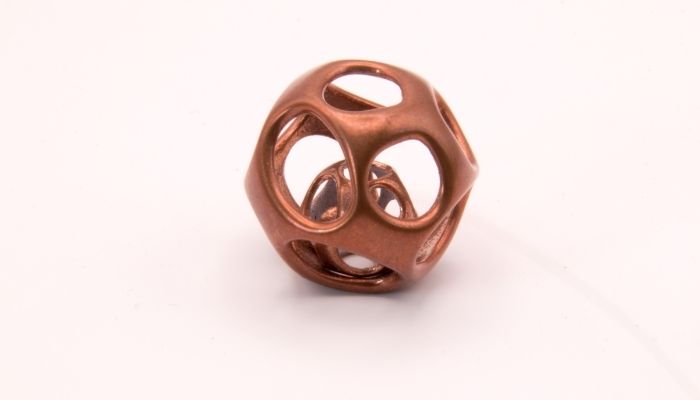
3D printed openwork ball in CuCrZr
How Can We Meet This Challenge?
One of the first solutions would be to use a machine with a more powerful laser, 1kW for example. These are available on the market, but are very expensive and require additional investment in infrastructure to accommodate them.
The other option is to opt for a green laser, which offers a much higher copper absorption rate than an infrared laser. The resulting parts have better properties, and parametrics are easier to determine. However, machines equipped with such lasers are still rare, expensive and often limited in terms of print volume size.
Finally, some market players have turned their attention to the composition of copper itself. By applying a coating to copper particles, such as graphene, it would be possible to improve energy absorption. However, this alters the metal’s thermal and electrical properties, which is potentially problematic for the production of the desired parts.
It would seem, therefore, that the possibilities for overcoming the challenges of printing copper with a 400W laser machine are limited. With this in mind, AFU conducted two years of research to find the ideal parameters for using CuCrZr alloy on an EOS M290 400W 3D printer.
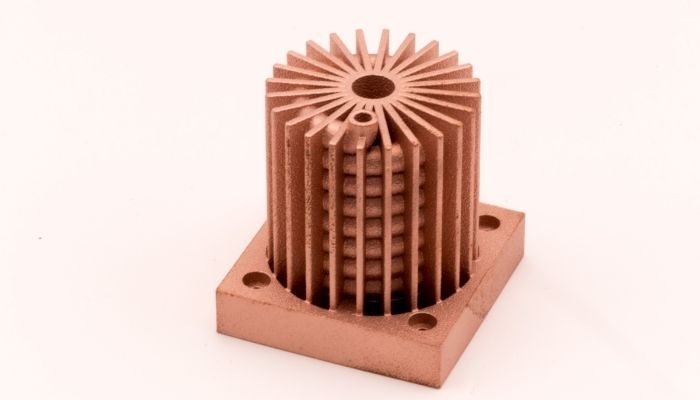
3D printed CuCrZr cooler
AFU’s Copper Printing
Having invested in a new metalworking machine in 2021, an EOS M290 400W, AFU has begun tests with pure copper. While the demonstration parts produced were satisfactory, with good surface finish and dimensional accuracy, the components incorporating piping did not produce the same results. In fact, metallographic examinations revealed all the above-mentioned limitations. Too many porosities were found, making it impossible to manufacture watertight parts. Raising the question, would it be possible to print copper with good properties on a 400W machine using an infrared laser?
AFU then began testing a 1kW machine and characterized several parts made from standard 40µm CuCp (Commercially Pure Copper). The density was much better and the results were satisfactory. However, investing in such a solution was too costly for the French company. It therefore decided to look at the parameters of its current machine, and embarked on a project to find the right balance between the various parameters.
Four factors directly influence copper laser fusion in additive manufacturing: layer thickness, laser scanning speed, laser power and vector spacing. The balance between these four parameters is more difficult to strike than for other metals such as TA6V titanium or AlSi10Mg.
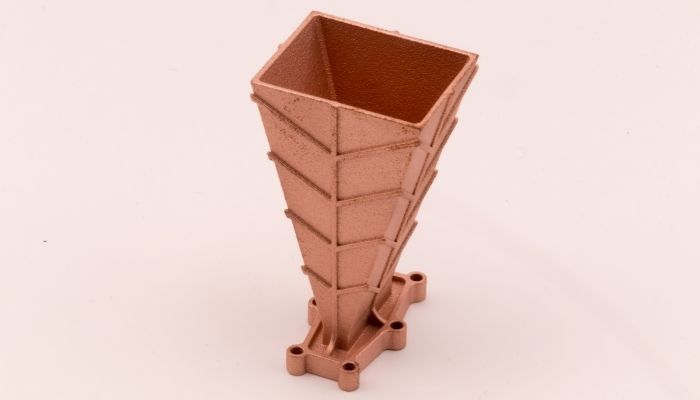
3D printed CuCrZr waveguide
AFU then carried out extensive research into the particle size and chemical composition of the powders used, the behavior of the material when processed by laser fusion, powder suppliers for additive manufacturing, etc. Numerous tests were carried out, according to very precise laboratory control requirements (control of powder bulk and tapped density, powder chemical composition, powder granulometry, part chemical composition, tensile strength and electrical conductivity). Two layer thicknesses were tested – 20 and 40 microns – with two different powder suppliers.
After several print runs, AFU achieved the desired results on its 400W machine. The company explains, “We are able to produce watertight parts, with metallurgical properties equivalent to CuCrZr available in bar, plate, wire… with a stable, repeatable process. We are the only company in France to do this on a standard machine and in 40µm. The CuCrZr available on the EOS M400 1kW is exclusively in 80µm, for example.”
What do you think of the achievements of French company AFU? Let us know in a comment below or on our LinkedIn, Facebook, and Twitter pages! Don’t forget to sign up for our free weekly Newsletter here, the latest 3D printing news straight to your inbox! You can also find all our videos on our YouTube channel.
*All Photo Credits: AFU