Large format 3D printing with foam that expands 40 times its volume
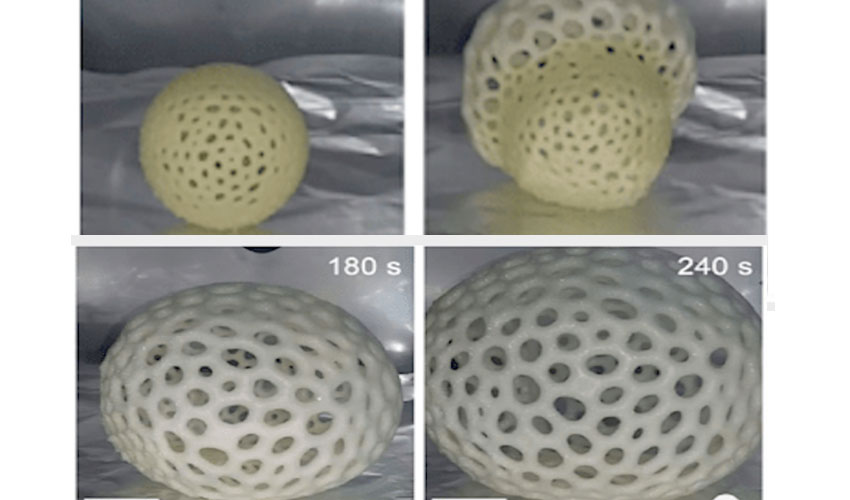
It’s an accepted limitation that parts produced with additive manufacturing must be smaller than the machine that produced them. Once these parts have been manufactured, they can be post-processed and bonded together to form larger structures. Large scale 3D printing is possible, but there are less systems available than desktop 3D printing. As of today, one of the biggest machines on the market can print volumes up to 1 m3. In a research paper published in Applied Materials & Interfaces, scientists explore the expandability of 3D printed foam as a possible solution to the limitation of build volumes.
In their Highly Expandable Foam for Lithographic 3D Printing paper, the researchers from UC San Diego explain that they developed a foaming prepolymer resin for lithographic additive manufacturing. Lithographic AM, which relies on the process of polymerization, hardens layers of material, in this case resin, using a light source. The foaming prepolymer resin can expand after being 3D printed to produce parts up to 40 times their original volume. Therefore, the build volume of the 3D printer does not limit the size of parts anymore using this process.
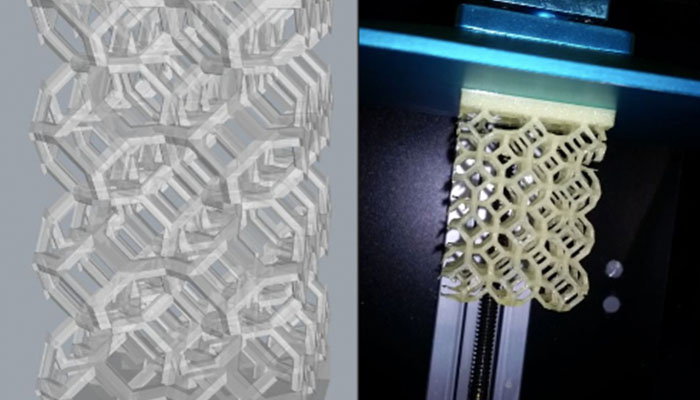
The part is modelled on CAD software and then printed on a lithography 3D printer
For what sectors will foam 3D printing be useful you might ask. The researchers write in the abstract: “Complex geometries comprised of porous foams have implications in technologically demanding fields such as architecture, aerospace, energy, and biomedicine.” During the development of their technology and material, two demonstrations were constructed. The first one was a helical wind turbine, 3D printed at one third scale and then expanded to its intended size. Then, a small boat hull was also printed at the same scale before expanding. The team heated these parts at 200°C for up to ten minutes for them to expand.
To develop the correct the material, the team selected a monomer that would act as the building block for the polymer resin: 2-hydroxyethyl methacrylate. Next, they had to find the optimal photoinitiator concentration along with an appropriate blowing agent to pair the monomer to. After several tests, the team settled on a non-traditional blowing agent typically used with polystyrene-like polymers. It will be interesting to measures how accurate this 3D printing process is. Of course, any deformation could be made worse during expansion. Therefore, consistent and precise final results could be difficult to obtain.
You can find more information on the paper HERE.
What do you think of expandable 3D printed foam for new types of applications? Let us know in a comment below or on our Facebook and Twitter pages! Don’t forget to sign up for our free weekly Newsletter, with all the latest news in 3D printing delivered straight to your inbox!