What Is Laminated Object Manufacturing?
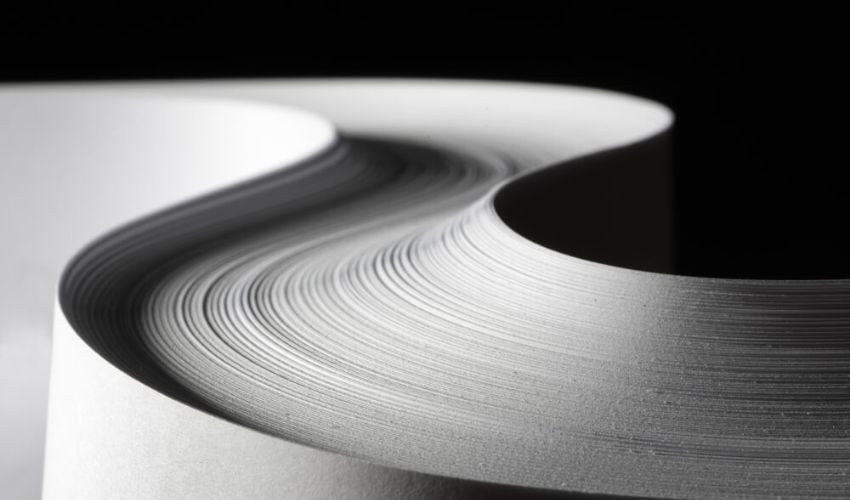
There are a number of different technologies that can fit under the additive manufacturing umbrella. Though common ones like FDM and SLA are well-known in the industry, others may be more niche. Take for example, Laminated Object Manufacturing (LOM), a unique rapid prototyping process that combines both additive and subtractive elements, making it a distinctive player in the 3D printing landscape.
The history of LOM traces back to its development in 1991, when a company called Helisys introduced laminated object manufacturing, a process in which sheets of material were fused together, and a digitally guided laser was used to cut out the desired objects. Later, in 2003, brothers Conor and Fintan MacCormack developed their version of the process. They used standard office paper and an inkjet printer to print the designs, gradually building up the object layer by layer. Then, they employed a tungsten blade to cut away the excess paper, revealing the final design.
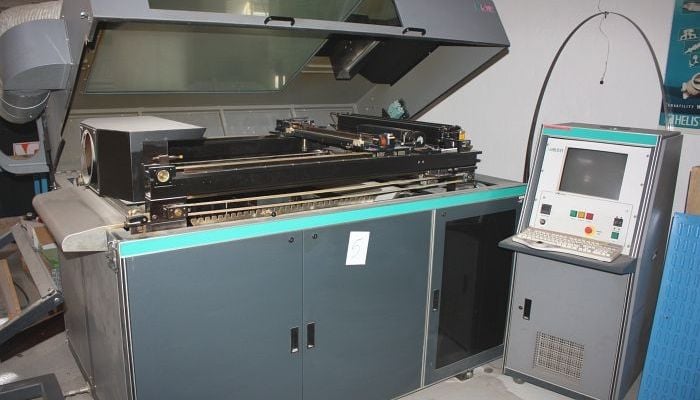
The discontinued Helisys LOM-2030 Rapid Prototype Modeling Machine, built in 1997 (Photo credits: KJ Auktion)
The MacCormack brothers took their innovation to the commercial realm through their company, Mcor Technologies. They continued to enhance the process by introducing CMYK color printing to create more vibrant objects suitable for promotional or visual prototyping purposes. This new approach, known as selective deposition lamination (SDL), involved color printing the sheets of paper before selectively gluing and cutting them. The adhesive was applied only to the areas corresponding to the design, making it easier to cut the final object from the waste material. But how has it continued to develop since then? When is it used? To better understand this interesting process, we took a closer look at Laminated Object Manufacturing in the guide below.
How Does Laminated Object Manufacturing Work?
Unlike most 3D printing technologies that build up objects layer by layer, Laminated Object Manufacturing (LOM) takes a unique approach. As mentioned above, the process involves the use of a laser cutter to cut away sections of material and gradually reveal the final shape. The process is a combination of additive and subtractive manufacturing techniques.
Initially, LOM involves the additive process of bonding layers of material together using an adhesive substance. These layers are carefully stacked upon each other, creating a solid block. Once the block is assembled, the subtractive component comes into play, as a high-precision laser cutter meticulously carves out the desired shapes and contours from each layer. This meticulous laser cutting ensures that each layer is intricately shaped to fit perfectly with the layers above and below it, resulting in 3D objects with tightly fused layers. The fusion of additive and subtractive steps in LOM enables the production of robust, complex, and accurately shaped objects, making it a promising technique for various applications across industries.
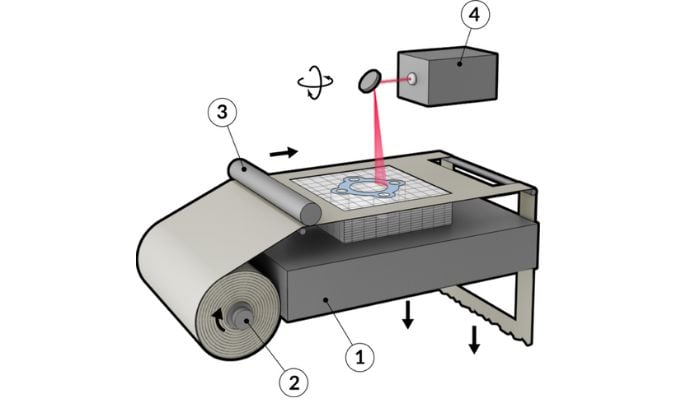
The LOM process involves gluing and cutting into sheets of material layer-by-layer using laser cutting (Photo credit: Manufacturing Guide Sweden AB)
LOM’s versatility extends to its ability to process various materials, including paper, metal, plastic, and composites. Paper is the most popular feedstock, offering wood-like properties when laminated, but it can also be combined with hard-setting resins to enhance rigidity. Other materials like metal and plastic can be used, but they may present some challenges and require additional considerations.
Furthermore, the applications of LOM are diverse, ranging from rapid prototyping of various shapes and sizes to producing full-color marketing props and architectural models. The technology is particularly well-suited for companies seeking in-house prototyping solutions in office environments. Moreover, LOM can be used to create sacrificial patterns for sand casting or investment casting processes, allowing for the production of complex shapes and designs.
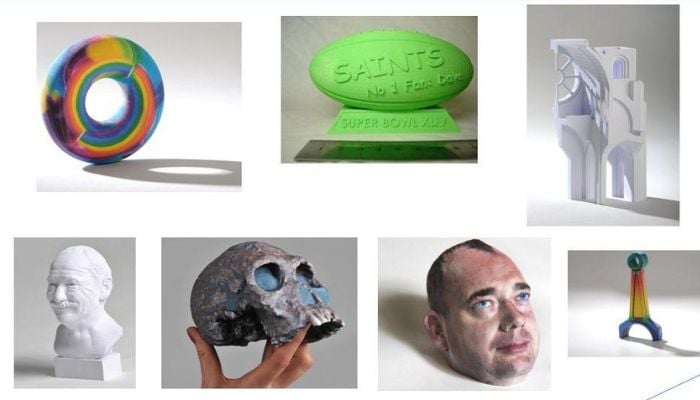
Objects made with Laminated object Manufacturing (Photo credit: MKS Technologies Pvt Ltd)
Advantages and Disadvantages
As with any technology, LOM has its pros and cons. On the positive side, LOM is a cost-effective method that employs relatively inexpensive materials such as paper or plastic sheets. It stands out for its ability to produce larger objects, making it suitable for creating prototypes and models with substantial dimensions. The resulting objects exhibit good structural integrity due to the strong bonding of layers, rendering them ideal for functional testing and design validation. LOM’s construction process minimizes the need for intricate support structures, thereby reducing the usage of additional support material and post-processing efforts. LOM also achieves a smoother surface finish on the exposed sides of the objects, lessening the necessity for extensive finishing work.
Conversely, Laminated Object Manufacturing comes with its fair share of drawbacks. The technology is limited to a range of materials, such as paper, plastic, or composites, which might not suit certain high-performance applications. The production speed can be relatively slow, especially for intricate designs, which may hamper time-sensitive projects. The nature of the process also leads to visible seams or layer lines on the surface of the object, which can affect its overall aesthetics. This may lead to LOM not achieving the same level of fine detail and precision as some other 3D printing methods, which could be a limitation for projects that require intricacies. Another concern is the generation of waste material during the cutting process, which may not be easily recyclable and raises environmental considerations.
While LOM might not be a one-size-fits-all replacement for other 3D printing techniques, it remains a compelling option for certain applications. Its cost-effectiveness, environmentally friendly nature, and ability to produce visual prototypes make it an attractive choice for rapid prototyping purposes. However, companies looking to invest in their first 3D printer should carefully assess their specific needs and consider factors like hardware availability and user support within the LOM community.
In conclusion, Laminated Object Manufacturing has its niche in the additive manufacturing landscape. With its unique combination of additive and subtractive processes, affordability, and the use of paper as feedstock, LOM remains an intriguing option for rapid prototyping and certain modeling needs. As technology continues to advance, LOM-adjacent additive manufacturing technologies like ultrasonic consolidation, a low temperature 3D printing technique for metals, could potentially become even more powerful tools in modern manufacturing.
What do you think of Laminated Object Manufacturing? Let us know in a comment below or on our LinkedIn, Facebook, and Twitter pages! Don’t forget to sign up for our free weekly Newsletter here, the latest 3D printing news straight to your inbox! You can also find all our videos on our YouTube channel.
*Cover photo credits: Wevolver