How can metal additive manufacturing improve existing production processes?
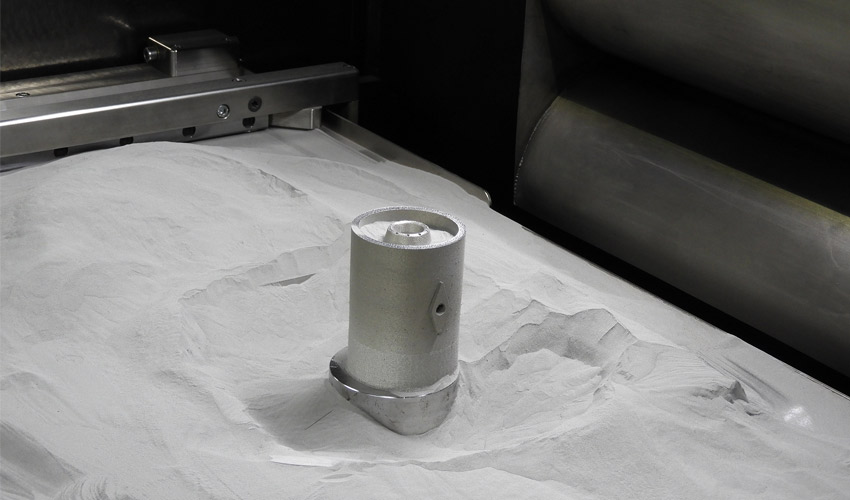
Krüger Fertigungstechnologie is a German company that recently invested in a metal additive manufacturing solution from GF Machining Solutions, an expert in Laser Powder Bed Fusion technology. Since 1996, the company specializes in subcontracting manufacturing, focusing mainly on High Speed Cutting (HSC) and milling processes. By investing in additive manufacturing, the company was able to push the boundaries of design further and offer its customers a fast and accurate solution. For example, it designed a 3D printed heat exchanger in a single piece for the nuclear industry. What benefits does Krüger derive on a daily basis from the integration of metal AM, and more specifically, from the workflow offered by GF Machining Solutions? Additionally, how did the company manage to integrate this new production method so quickly?
The Swiss company GF Machining Solutions has developed a strong value chain around additive manufacturing, from design to post-processing and inspection of the final part, enabling its customers to accelerate their production processes. Its DMP Flex 350 machine offers higher yields, more precise quality and the ability to design parts with complex geometries. In particular, it integrates an interchangeable 3D printing module to avoid tedious cleaning when changing materials. It also offers real-time process tracking and traceability that minimizes the risk of errors and associated costs. These are the features that led Krüger to choose this industrial machine.
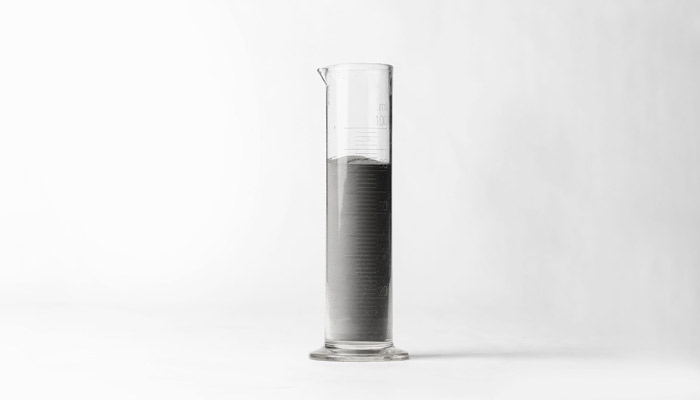
GF Machining Solutions masters metal additive manufacturing | Photo Credits: GF Machining Solutions
Rapid integration of the DMP Flex 350
The Krüger teams told us that the installation of their new metal machine was done in only one week. Managing Director Friedhelm Krüger explains: “I am impressed with the speed and fluidity with which the GF Machining Solutions team set up metal 3D printing for us. The printer was installed, commissioned and staff trained in just one week. Thanks to the DMP Flex 350, we can offer our customers an even wider range of services“.
It should be noted, however, that the teams already had some expertise in 3D modeling and general manufacturing processes, which contributed to the success of the integration. Robert Volland, sales engineer at GF Machining Solutions, explains: “Before implementing a new machine, we analyze the customer’s training needs. Krüger already had some experience with modern 3D software, so we could rely on this software and knowledge“. Today, the DMP Flex 350 machine is based on the 3DXpertTM software, which is designed to facilitate the overall process of metal fabrication. For example, the German company leveraged the automatic alignment functionality, improving part quality, but also optimizing the build volume’s use to create multiple components at a time. Friedhelm Krüger adds: “This saves us money – a saving that we are happy to pass on to our customers. Support structures are also part of this automatic optimization. They are generated at the same time, taking into account the part support, material consumption and printing time“.
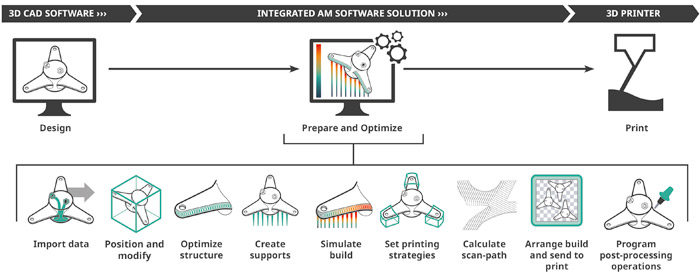
The AM process from modeling to production | Photo Credits: GF Machining Solutions
Going further in manufacturing
Thanks to this investment, Krüger is able to combine several manufacturing processes and increase the possibilities for all its customers. The company is able to create hybrid parts that combine the advantages of metal additive manufacturing with those of more traditional methods already mastered for more than 20 years. In particular, the company is working on the ITER (International Thermonuclear Experimental Reactor) project, which brings together 35 countries to design the world’s largest tokamak, an experimental machine designed to harness the energy of fusion. In particular, it has imagined a heat exchanger in a single piece, combining 3D printing and milling.
Friedhelm Krüger concludes: “The easy integration of other manufacturing technologies is a great advantage. With 3DXpert, we can easily manufacture hybrid parts, for example 3D printed parts that still need to be milled.” Would you like to know more about the possibilities offered by GF Machining Solutions? Visit the website HERE.
Can metal additive manufacturing facilitate your current production processes? Let us know in a comment below or on our Facebook and Twitter page! Don’t forget to sign up for our free weekly Newsletter, with all the latest news in 3D printing delivered straight to your inbox!