Designer Julia Daviy on disrupting and bringing sustainability to the fashion industry
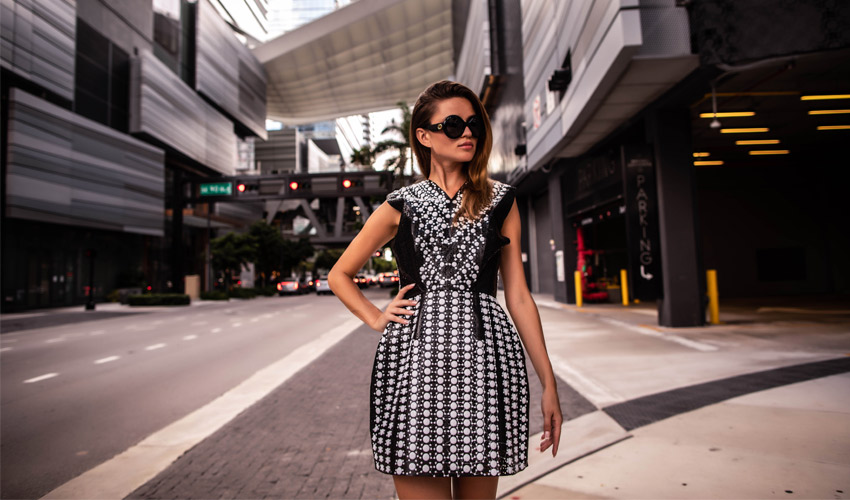
When it comes to the fashion industry, 3D technologies are proving to be a way to unleash the creativity of designers and stylists, bringing more personalisation for the end user. But it is also a way to reduce the amount of waste in an industry that is quite harmful to our environment. This is one of the main reasons why designer Julia Daviy turned to 3D printing: she designed a collection of clothing additively manufactured, disrupting traditional methods. We met with Julia Daviy to learn more about the manufacturing process behind her collection and the advantages of additive manufacturing.
3DN: Can you present yourself and your link with additive manufacturing?
I am Julia Daviy, and I am a 3D printed clothing designer and a clean tech specialist. Three years ago I dived into the learning of 3D printing software and hardware, and took each and every course I could find to get the knowledge and skills. My apartment was flooded by 3D printers and 3D scanners, different types of filaments and other materials, and I bought all the books and magazines on 3D printing I could find. My practical knowledge came from every day experimentations and hundreds of mistakes.
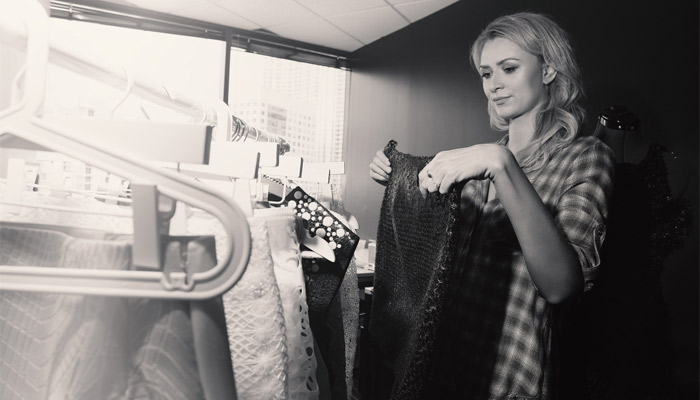
Julia Daviy | Photo Credits: Vita Zamchevska
I started to learn and experiment with 3D printing for several reasons. I was looking for a sustainable and waste-free way of producing clothing. I also noticed that the functions of clothing are changing, it is not all about beautification of our appearance any more. And at the same time, it is almost impossible to find clothes in the market that will meet these new needs. I do not like wasting time on non-intellectual monotonous repetitive operations and the current participation of millions low-paid hard working women and kids into the clothing production. I hate hard logistics in the traditional fashion industry too. All of these forced me to look for better technology for the clothing production. For the last decade, I have been working with clean technology, especially within the solar energy industry. Working in this new industry and solving challenges every time, I was not afraid to meet them again but in a new industry.
3DN: Can you tell us more about your first 3D printed clothing line ?
Eight of my The Liberation (collection) looks were 3D printed on large-format 3D printers and one dress was created from a combination of SLA 3D printed patterns and organic ahimsa silk organza lining. During the year before I started to work on my collection, I was experimenting with different approaches to make 3D printed clothes. I saw 2 main challenges, the first one was making 3D printed pieces of clothing as soft as possible. The second challenge was to get the benefits from 3D printing such as zero waste and minimised hand work.
Working on my collection, I developed a method of zero-waste 3D printing for clothing, each piece of garment is soft and flexible enough to wear it at least for a reception or other kind of event.
Also, I wanted my pieces of clothing looking like real garments you could find in the stores. I did not want to make the 3D printed apparel models too sophisticated, despite that is one of the biggest temptations when you work with 3D printing as you have unlimited opportunities to create.
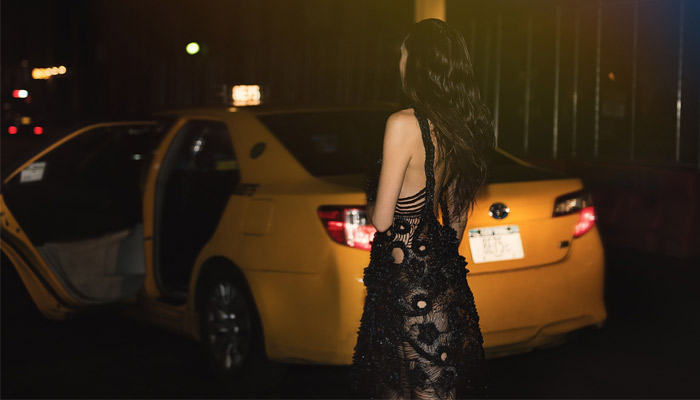
Photo Credits: Vita Zamchevska
3DN: What are the different steps to create a 3D printed garment ?
In general, we have three main stages. The first one is design, measurements, and 3D modeling of a ready piece of clothing in 3D modeling software. At the second stage we print the file or files with the patterns of the digitally ready piece of clothing on 3D printers. And we make final assembling, lining and other finishing works during the third and final stage.
3DN: What 3D printing technology do you use? What materials?
I love SLS technology but today it produces a lot of waste. So, I decided to advance my FDM 3D printing. We took one of the best large-format 3D printers in the market and started to experiment with the very flexible filaments and implementation of my approach – to 3D print ready patterns excluding the 3D printing of fabrics. In the process, we encountered numerous challenges and had to modify the machines each time to solve these problems. I am lucky to have some engineering knowledge that helped a lot. And my partner is a great engineer; he did a lot to make that happen.
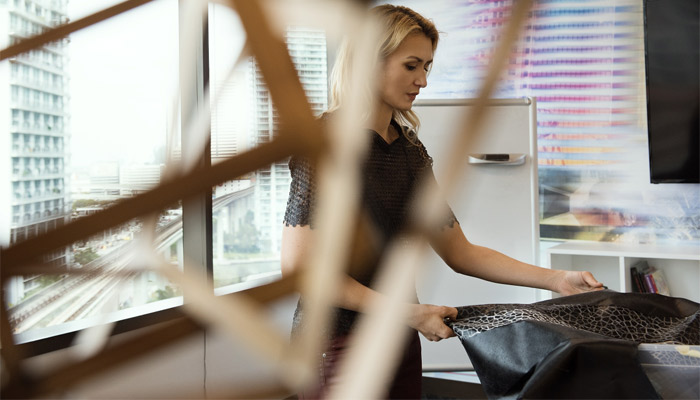
Photo Credits: Vita Zamchevska
I am also continuing to experiment with SLA, although it does have its limitations.
I have tried each and every flexible material for FDM and SLA I could find. Today, I use 70A TPE. The manufacturer makes them for me on pre-order, maybe they will launch it as a product for designers, it’s not easy to achieve the high quality 3D printing without it. As for TPE, it’s a good material for today, it is 100% recyclable. With SLA, I experiment with flexible resin and silicon. Today, the materials are actually secondary, the main idea is to implement 3D printing and spread its use. Once that happens the range of materials available will expand. I am sure that we will come to use biodegradable super flexible and textile-like materials in the near future.
3DN: What are the main benefits of additive manufacturing for you?
For today, I see additive manufacturing as the only possible way for sustainable fashion industry to develop.
3D printing helps on many levels – from digitisation, easy and faster prototyping, etc. Also, less handwork and therefore, potentially, the exclusion of low-skilled manufacturing from people and more opportunities to create and develop creative pieces – not just for designers, but for everyone. Again, zero-waste and cruelty-free fashion – that is my dream that is coming true with every new step. It is cool when you can contribute and supply this world with something really good on many levels. I feel that the younger generations understand this feeling, they understand that money “smells” and they want to make money smell good, and 3D printing permits us to do that too.
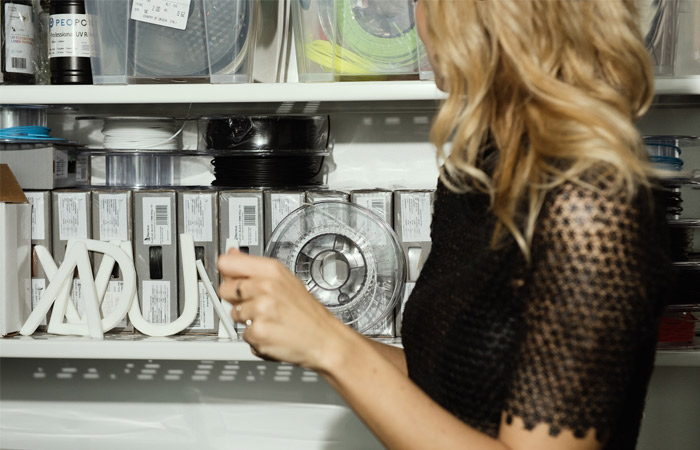
Photo Credits: Vita Zamchevska
3DN: How do you see the future of 3D printing in the fashion industry?
I cannot imagine a good future for fashion without the use of 3D printing. This is a much-needed step for future accomplishments such as digital logistics, the creation of smart clothing (clothing that will protect, heat or cool when needed) and much more.
To me, it would be a shame if we just take 3D printers and continue to utilise the old approach. We need to innovate, we need to use this technology to create something new. Therefore, we need to use 3D printing for good, for a sustainable and cruelty-free way of producing clothing and accessories.
Unfortunately, fur and leather are still widely used in the fashion industry. Those are the first materials that need to be absolutely replaced. They create enormous suffering for millions of animals as well as enormous water, soil and air pollution and severe illness. Moreover, these materials are boring and kill the creativity of designers.
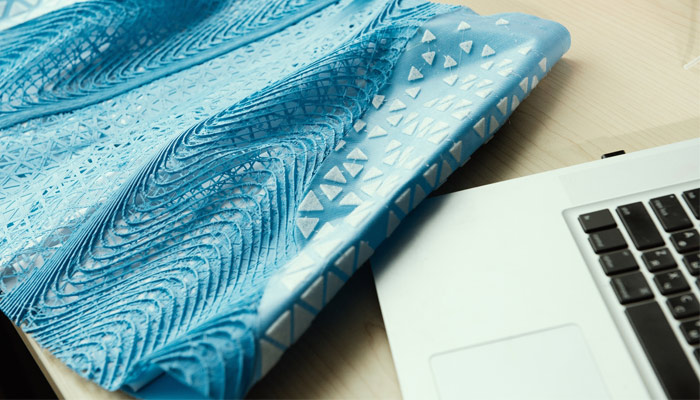
Photo Credits: Vita Zamchevska
3DN: Any last words for our readers?
Many designers like to say that 3D printing is still underdeveloped for its use in clothing production. Nevertheless, 3D printing technology will not develop itself. People will. We, the designers of 3D printed clothing, designers of new materials and designers of new 3D printers are making that happen. With every attempt we are closer to the sustainable 3D printing clothing production that will be the end of an unsustainable process that is killing our planet. Most importantly, this amazing technology will help to unleash the creator inside every consumer.
What do you think of this interview with Julia Daviy and her vision of the fashion industry? Let us know in a comment below or on our Facebook and Twitter page! Don’t forget to sign up for our free weekly Newsletter, with all the latest news in 3D printing delivered straight to your inbox!