An Introduction to Post-Processing in 3D Printing
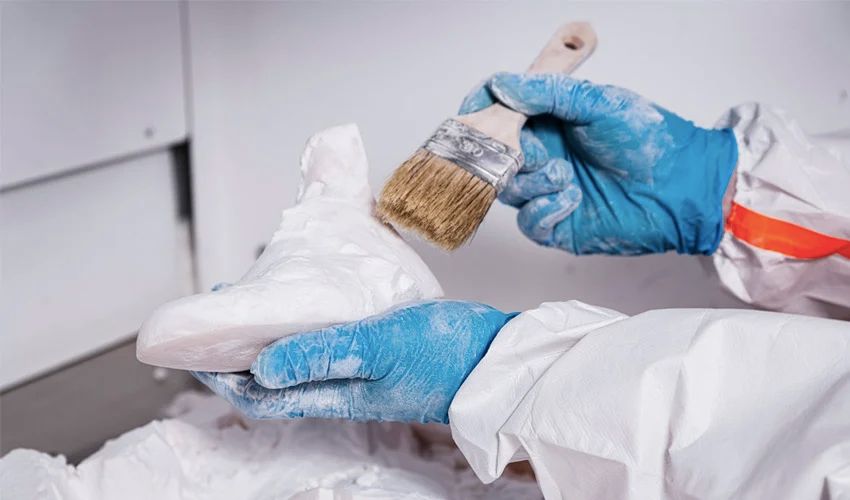
The value chain of additive manufacturing consists of multiple steps before having a final part. There is, of course, the printing phase, but also the modeling phase, which is start of any project. But once the 3D printer has finished its work, it is often necessary to work on the part itself: this is where post-processing comes in. Post-processing includes any work that is carried out once the part has left the machine; including but not limited to cleaning, surface finishing, annealing and even coloring. Post-processing techniques in 3D printing are as varied as the manufacturing processes themselves and each has its own specific requirements. But why is this step key in 3D printing? How is the market structured? This introduction to post processing can answer these questions, so read on to find out.
Post-processing in 3D printing is mainly used to improve the aesthetics of manufactured parts and/or to improve their properties. For example, to make a surface smoother or to anneal a component to increase its strength and optimize its resistance. While some post-processing techniques can be used with any 3D printing process, others are technology-specific. Indeed, an FDM part must be treated differently to a metal part. Post-processing is therefore an important aspect to take into account when you want to start 3D printing.

Post-processing is used to improve the aesthetics of 3D printed parts (photo credits: Sinterit)
Introduction to Post-Processing Methods
To help to better understand the different types of post-processing, this introduction will be the first of a number of articles dedicated to the subject in the coming months. First of all, the cleaning of the parts. As the name suggests, this includes all the techniques that will make our part cleaner: de-soldering, rinsing, brushing, blowing, etc. The goal is to remove all excess material, whether it is powder or resin. Depending on the printing process used, this step will take more or less time. For example, with powder sintering this is often a lengthy step that increases the manufacturing time.
The second category is annealing. This involves increasing the temperature of a part to improve its mechanical properties. These could include its resistance to heat, traction, UV or even its strength or thermal stability. This step mainly concerns polymer parts – for example, for resin processes, there are “curing” machines directly designed to be used with a particular printer, as is the case for Formlabs solutions. For powder bonding or indirect metal 3D printing processes it is necessary to go through a debinding and then sintering stage via an adapted oven. Annealing techniques are therefore used to improve the final properties and functionality of the part.
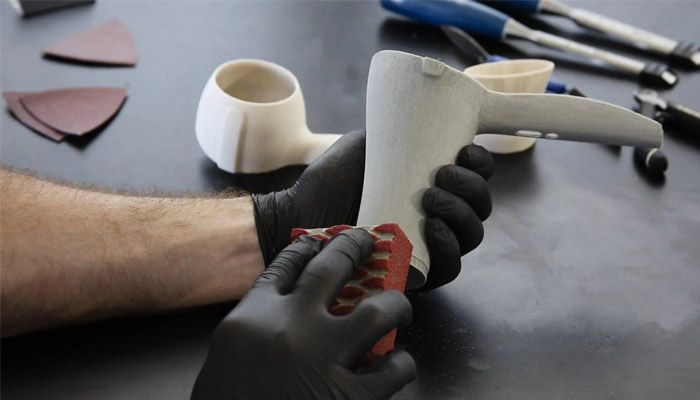
Photo credits : MakerBot
There are two categories used to optimize the aesthetics of the parts: surface finishing and coloring. The first category includes all the methods used to improve appearance: smoothing, polishing, sandblasting, infiltration or milling. There are currently many processes to modify the surface of a part, either by adding or removing material. For example, sanding will remove surface unevenness while spraying will add a layer of product to obtain a better shine.
If we now take staining, the final objective is of course to add color to the finished piece. Dyeing and painting are two methods used today; the choice depends mainly on the printing material used. For example, dyeing is more popular for polymer powder-based processes, while painting is more popular for parts made with FDM.
The Benefits and Limitations of Post-processing
As you can see, post-processing in 3D printing is a key step to improve the visual aspect of a part but also its final characteristics. Thanks to the different techniques, the 3D printed part can be be used to its fully potential or even marketed as an end-use part. Post-processing allows users to correct certain defects and sometimes even “camouflage” the 3D printed aspect by removing the look of the printed layers. Moreover, thanks to post-processing, some plastic parts have characteristics similar to metal parts for a considerably reduced price.
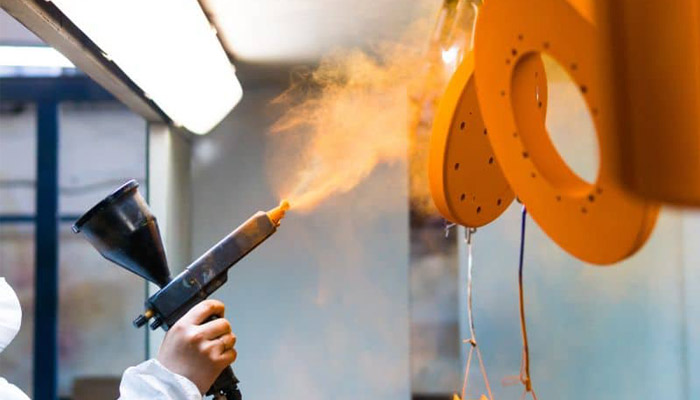
Several coloring techniques exist today (photo credits: BigRep)
Of course, post-processing also has its challenges and limitations that the market has been trying to solve for a few years. One of the biggest barriers to post-processing in 3D printing is the time it takes. According to the annual study published by PostProcess Technologies, 53% of participants say that their biggest challenge is post-processing cycle duration. According to them, these steps are still too time-consuming and do not allow them to take full advantage of the reduced manufacturing time offered by 3D printing itself. As a result, the search for automated processes has become a priority for many professionals in the sector. These automated steps free up labor that can then be employed on other strategic positions. Moreover, by automating certain post-processing techniques, employee safety is ensured. In any case, automation is one of the key trends in the market, both in post-processing and in the actual printing of parts, and we look forward to seeing further innovations in this field!
Has this introduction to post-processing taught you more about its role in 3D printing? Let us know in a comment below or on our LinkedIn, Facebook, and Twitter pages! Don’t forget to sign up for our free weekly Newsletter here, the latest 3D printing news straight to your inbox! You can also find all our videos on our YouTube channel.
*Cover photo credits: Protiq
Good start to post processing.
Will there be anything about the sealing (water resistant / water proofing) coming?