#3DStartup: ING3D and its Mineral 3D Printing Solutions
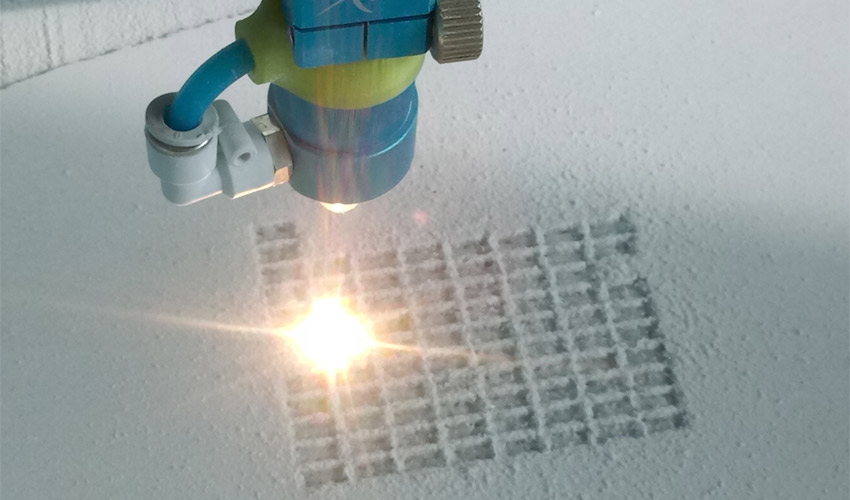
Based in Germany, our startup of the month is ING3D which has developed a mineral 3D printing process inspired by powder sintering, called Mineral Direct Laser Sintering (MDLS). Thanks to this unique process, it is possible to design very light and non-flammable parts all while reducing the cost of printing by 10 and speeding up the manufacturing process. ING3D notably uses perlite, a rock of volcanic origin containing water. Still, at the prototype stage, the machine developed by the startup could have a major impact on many industries that need to produce heat-resistant objects, for example. We met the founder of ING3D, David Manjura, to learn more about this innovative technology and the startup’s future projects.
3DN: Can you briefly introduce yourself and explain your connection to 3D printing?
Hello, my name is David Manjura, I am a materials engineer – specializing in lightweight inorganic materials – and have been working in the construction industry for 11 years. In 2015, I first discovered 3D printing when I received a request from the Technical University of Munich to develop lightweight concrete. From then on, the subject of additive manufacturing has never left my mind. After working with experts in 3D printing, participating in trade shows, forums and conferences, I am convinced that additive manufacturing could become a decisive technological step to solve a multitude of environmental, economic and other problems, perhaps even cultural.
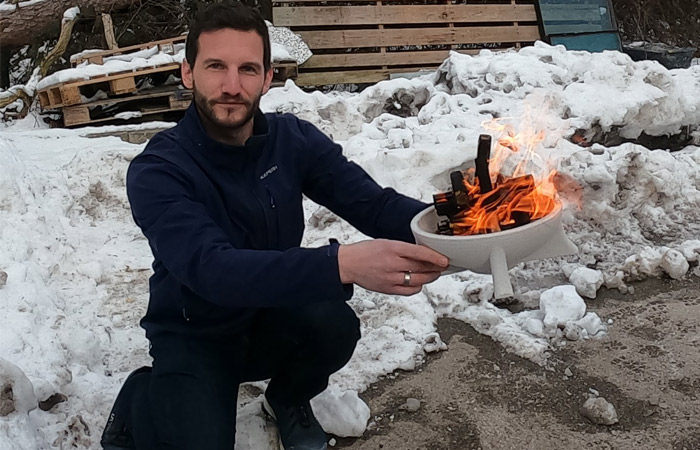
The founder of ING3D holding a part printed in 3D with the MDLS process (Photo Credit: ING3D)
3DN: How was ING3D born? Can you explain Mineral Direct Laser Sintering (MDLS) in more detail?
I noticed that additive manufacturing focused mainly on metals and plastics, and only a small percentage on inorganic materials, like concrete and ceramics. The subject of 3D printed inorganic lightweight materials had not yet been addressed in a patent or thesis. In 2016, I decided to conduct the first series of experiments independent of the work of the time and to check whether such 3D printing is feasible. This is how MDLS (Mineral Direct Laser Sintering) technology was born. The process consists of sintering light mineral materials, in particular perlite, by means of a CO2 laser combined with the well-known powder bed fusion process in a single step, that is to say without post-sintering.
3DN: You describe your solutions as sustainable, heat resistant, and ultralight. How can these properties be obtained?
Since the sintering process does not require any coating with additives, the raw material remains pure in its form and can be disposed of without problems after the period of use – in some cases in organic waste as a soil conditioner. The raw material itself is basically temperature stable and very light. It is transformed into fire protection elements of building material class A1 or furnace insulation by the binder-free shaping of the 3D printing process with suitable infill structures and contours.
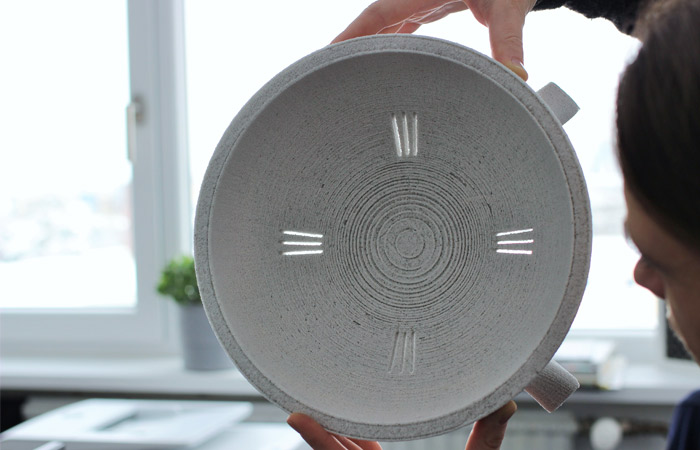
Photo Credit : ING3D
3DN: What challenges did you have to overcome during development?
First of all, there was virtually no starting point in the literature on how light mineral materials react to laser sintering. For this purpose, dozens of mineral materials have been studied and tested for more than a year with the simplest means. After the first successes were obtained, it was necessary to build a prototype system, finance it and develop it with partners to demonstrate its reliability. To achieve this, a laser cutting system has been reduced to an absolute minimum and a powder application system and rudimentary software have been developed and implemented. This gave rise to first technical specifications, then to pre-product ideas, which we printed on said prototype machine. In order to develop good printing results and suitable end products, thousands of man-hours were required in a short time until all the technical parameters of shrinkage, support, power density, etc. are settled. There are of course challenges related to the overall development of the company, be it patents, potential clients, investors, etc.
3DN: For which applications do your customers use ING3D technology? What are the benefits to them?
We are mainly in the product development phase with our customers and it is only after the construction of the industrial pilot plant that we will be able to deliver the expected amount of finished products to the market. As for the applications, they are very varied. It starts with the insulation of the already mentioned furnaces, where electronics and sensors need to be protected in complex high-temperature applications. Another possibility is water and air filtration, where the material is fundamentally very efficient due to its open porosity, and where higher efficiency and durability are achieved through the known structural design of 3d printing. Finally, there are also biotechnological applications where the footprints serve as natural coral substrates for the reforestation of reefs with heat-resistant larvae.
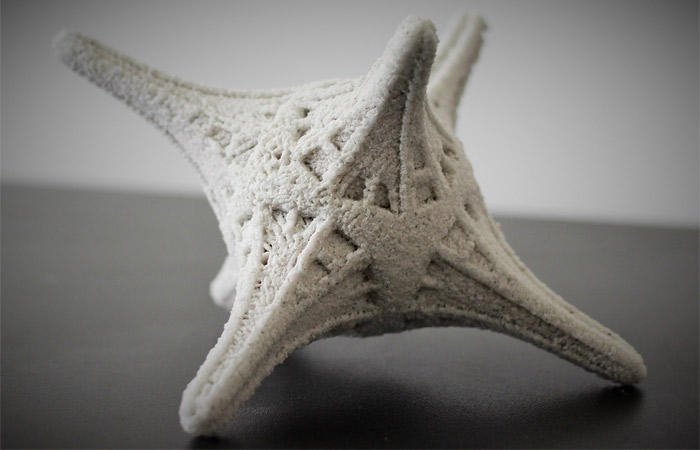
Technology enables biotechnology applications to be designed. (Photo Credit : ING3D)
3DN: What are the future projects of ING3D?
In the medium term, at least three different finished products will be manufactured and continuously developed at ING3D. This step will be followed by the development of series factories for our B2B customers and by new investments in the research and development of light mineral materials. In the latter case, we have only scratched the surface. We expect at least two or three more major scientific breakthroughs in the next few years. And of course, we want to be at the forefront of this science.
3DN: A final word for our readers?
We look forward to a lively discussion and exchange on the topic of mineral 3D printing, new application possibilities, and, of course, the 3D printing market in general. Communities like 3Dnatives are a great platform to provide insight into the ever-growing 3D printing market and for producers and customers to make decisions. You can find more information on our website.
What do you think of ING3D 3D printing minerals? Let us know in a comment below or on our Facebook and Twitter pages. Don’t forget to sign up for our free weekly newsletter, with all the latest news in 3D printing delivered straight to your inbox!