IMcoMET Fights Skin Cancer With Micro 3D Printing
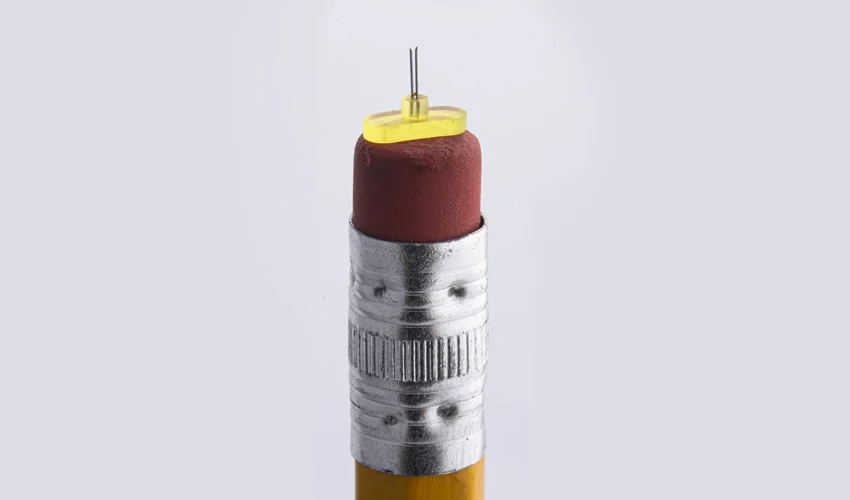
Rotterdam-based startup IMcoMET works in the medical sector, specializing in the development of solutions to fight cancer, particularly skin cancer. To do this, the company extracts interstitial fluid, filled with biomarkers, from the skin in a localized manner, to study it and improve dermatological diagnosis. The aim is to advance biomedical research and provide personalized solutions. Furthermore, to achieve this goal, the start-up relies on 3D printing, and more specifically on microprinting solutions from American manufacturer Boston Micro Fabrication (BMF). Thanks to BMF’s 3D printers, IMcoMET is able to develop microneedle technology, enabling it to extract this famous liquid in a precise, localized manner.
The majority of analyses carried out on the human body are performed using blood, involving invasive techniques and results that are often inconclusive due to coagulation. This is why other body fluids are of interest, notably dermal interstitial fluid. This is a fluid that circulates between tissue cells and incorporates numerous biomarkers. Most of the time, the fluid is extracted using microneedles. And there are many different types of microneedles on the market – for example hollow and porous, among others.
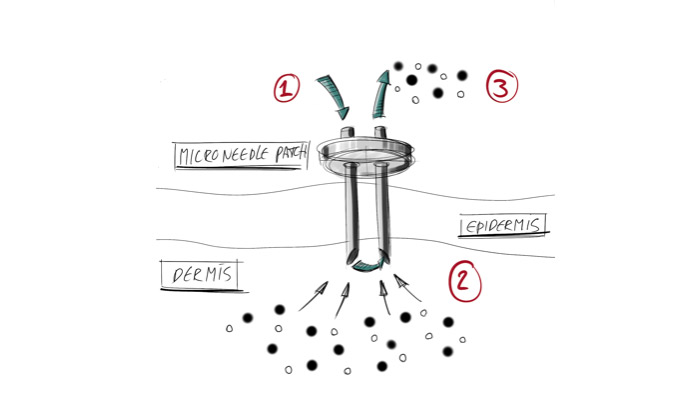
IMcoMet’s patented technology in action
However, one of the challenges associated with this method is the volume of liquid extracted: most of these microneedles, which are inserted directly into the skin, do not provide a sufficient quantity. This means that numerous needles are required to achieve the desired volume, which is not the easiest or most pleasant method. That’s where startup IMcoMET comes in: the aim was to develop a precise, minimally invasive device that could extract enough fluid in one go, doing so in a highly localized manner.
Microneedles to Extract Precise Biomarkers
The first generation of microneedles developed by IMcoMET was produced in the traditional way. Called M-Duo Technology, it consists of two needles linked to two tubes connected to a micro peristaltic pump. Operating in pairs, the first needle injects a carrier fluid and the other aspirates, done simultaneously. The system creates a loop in which the fluid travels continuously. The liquid drawn in is therefore a mixture of the carrier fluid and the interstitial fluid. IMcoMET explains that this makes it possible to detect numerous biomarkers such as exosomes, proteins and DNA.
Alexandre Motta, the startup’s CTO, explains: “M-Duo Technology extracts all soluble molecules around the needle insertion point. Our device is currently in clinical trials, but we now want to go one step further. The aim is to design an even smaller device that will enable us to go even deeper.”
The miniaturization of this process did, however, involve a number of challenges. Firstly, the tubes used must be connected to the pump, thus necessitating a certain diameter to connect them. However, the two needles used must be close enough to each other to work properly. This meant having two independent, parallel channels, only 20 microns apart. But how to achieve this result without losing precision?
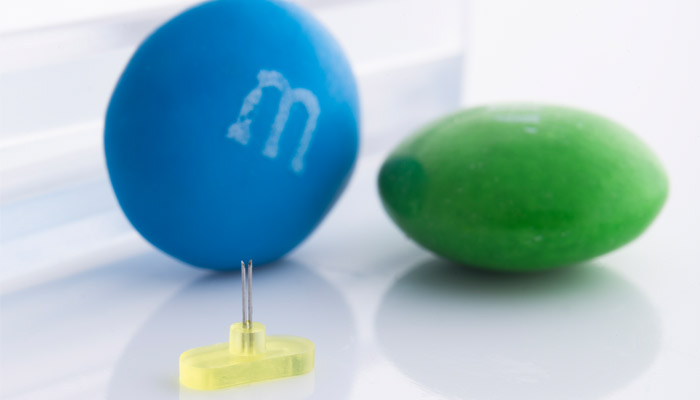
BMF’s 3D-printed device
BMF Technology for Even Higher Resolutions
This is where IMcoMET discovered Boston Micro Fabrication’s 3D microprinting technology. Based on projection micro-stereolithography (PµSL), it can achieve very high print resolutions – between 2 and 50 microns – as well as tolerances of between 10 and 25 microns. The technology is used to manufacture the cap that holds the needles in place. This component also incorporates two 100-micron diameter channels, located just 20 microns apart. They are located so that the tubes connected to them run in a V-shape, each on its own side.
Alexandre Motta continues: “Thanks to this technology, we can adjust our needles as we wish – for example, vary the depth – and thus map the interstitial liquid.” He is also confident about the device’s larger-scale production phase, as the microprinter’s printing plate enables several caps to be manufactured at the same time. He concludes: “Boston Micro Fabrication’s technology is ideal for the precision and resolution we want to achieve, where the SLA process cannot. It’s also much more affordable than nanoimprinting and enables rapid scale-up. It’s an excellent choice for IMcoMET and we’re already developing other projects with the BMF teams.”
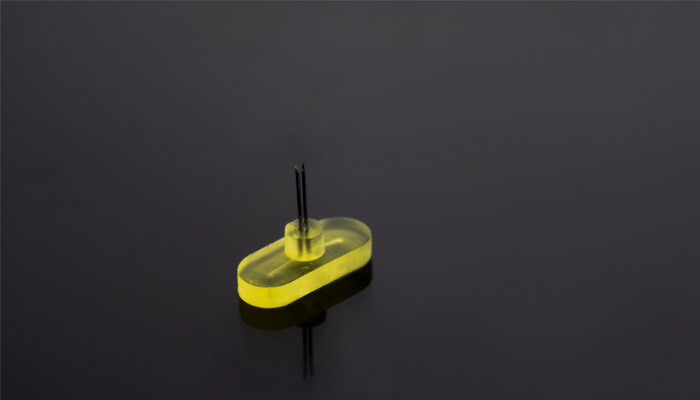
The cap includes two microneedles
Interested in BMF’s microprinting solutions? Don’t hesitate to contact their teams by clicking HERE.
What do you think of the device developed by IMcoMET? Let us know in a comment below or on our LinkedIn, Facebook, and Twitter pages! Don’t forget to sign up for our free weekly newsletter here, the latest 3D printing news straight to your inbox! You can also find all our videos on our YouTube channel.
*All Photo Credits: Boston Micro Fabrication