Designing objects as complex as nature: Interview with Hyperganic
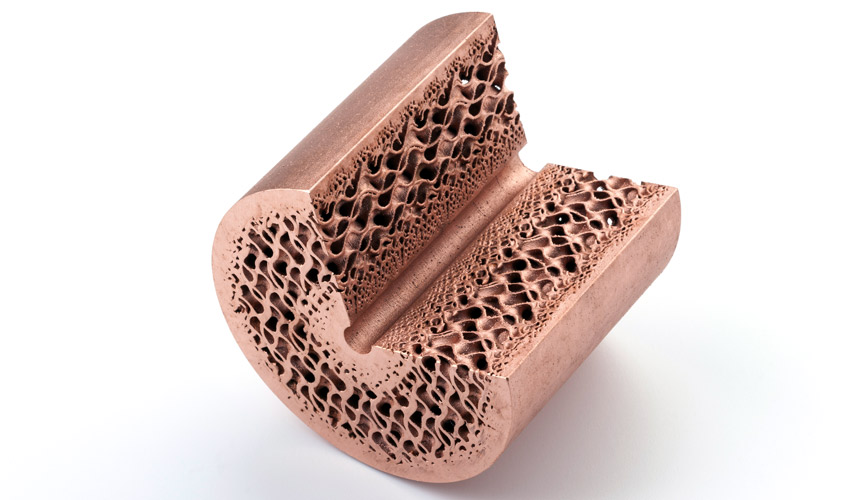
What if you could design objects as complex as nature? What would you produce? Since the majority of current software tools for additive manufacturing are not yet adapted to this complexity, the Munich-based company Hyperganic offers a technology that overcomes current limitations and allows objects to be designed with complete freedom of design. We got the opportunity to talk to Markus Finke, Director of Business Development at Hyperganic to learn more about the company’s technology.
3DN: Can you present yourself and your link to additive manufacturing?
Today’s software tools are designed for traditional manufacturing – a world where simplicity is key. The true potential of AM is realised with the ability to produce generatively designed objects with complex internal structures. Applications are mass customization and print automation, for example. Hyperganic enables our customers to reliably automate design processes and ensure complex objects can accurately be printed on next generation 3D printers.
3DN: How was Hyperganic founded and what is its mission?
Hyperganic was founded in 2015. Our mission is to enable our customers to: build objects as complex as Nature; automate these design and engineering processes; ensure the resulting objects can easily be printed, therefore utilizing the full potential of today’s 3DP machinery. We work with companies to automate production workflows and partner with leading printer manufacturers to utilize the full potential of their machines. Printer manufacturers use our technology to drive their printers. Hyperganic’s technologies enable users to control print parameters at the voxel-level, to optimize print strategies for speed, quality and to allow for next generation applications like material gradient printing.
Engineers use our technology, to create workflows for breakthrough designs. Say your business is to design heat exchangers. The key Input variables to control are build volume and heat dissipation. With the help of algorithms, you can now write a recipe to design your perfect heat exchanger based on these inputs. You now have an automated design workflow. This is the object’s DNA. It’s not a blueprint, it is a workflow, that generates a blueprint. Next time you change the inputs, the engine will generate a completely new object. This is what we call a mass customization workflow. It can be setup for anything that needs customization. From custom industrial parts to close to body applications.

Visualization of an automated object generation workflow for mass customization. I Credits: Hyperganic
3DN: What are the current design limitations of additively manufacturing objects?
We look at Nature as the benchmark for design complexity. Natural objects are multi-material, high-tech organisms. Our technology can generate designs at this level of complexity. But while we can dream big on the screen, can we actually manufacture these objects yet? Some of them yes. We see existing printer hardware as the main limiting factor, however the capability of printer hardware continues to improve. There are many manufacturers developing revolutionary printers, especially on the multi-material side. This enables our users to have greater design freedom, resulting in more interesting and efficient objects. Think of composite objects manufactured from multi-material gradients for example.
3DN: How does your software differ from others?
The first difference is our approach: We don’t provide another CAD tool. Instead, we provide a way to describe objects through algorithms and AI. Under the hood, we work with our own geometry kernel that is based on a high-performance voxel engine that performs at printer resolution or higher. Voxels allow for a secure and reliable way to automate design processes and to control print-parameters at the most granular level. Because print requirements are part of the input data, we ensure that the generated objects are always printable. Our workflows are recipes that can easily be adjusted and extended.
3DN: What are Hyperganic’s future plans?
We continue to partner with the most technologically advanced market players to take AM to the next level. We have a diverse partner base: from printer manufacturers to companies that want to leverage the full potential of AM. In past years, we saw AM move from prototyping to the production of industry-standard end-use parts. Today, we see that these companies now produce customized parts on machines that allow more and more design complexity.
3DN: Any last words for our readers?
Ask yourself: “If design complexity was free, what would I design?”. I ask this all the time because it gets you thinking outside of the box. It might take time to get an answer but when you get one you will be surprised by the ingenuity.
What do you think of Hyperganic? Let us know in a comment below or on our Facebook and Twitter pages! Don’t forget to sign up for our free weekly Newsletter, with all the latest news in 3D printing delivered straight to your inbox!