GF Machining Solutions facilitates the manufacture of hybrid parts
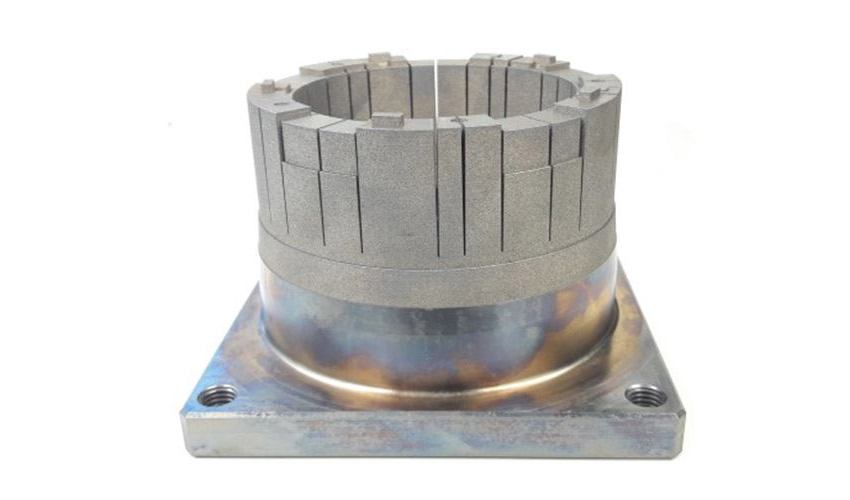
In the manufacturing industry, different production methods are used depending on the type of part created. While additive manufacturing has proven its worth, whether for rapid prototyping or end-use part applications, it is still a method that is often complementary to subtractive manufacturing processes. Indeed, current technologies do not yet allow for the design of large volumes and are often too slow. Additive manufacturing is preferred for parts with very complex geometries, small series, prototyping or tooling. However, it can be seen that more and more manufacturers are looking to combine the two production processes: known as “hybrid manufacturing”, it offers a number of advantages and is, in some cases, more viable from an economic view point.
Nevertheless, combining these two processes can generate some challenges. In most cases, the part is 3D printed and then post-processed and machined to obtain the final geometry or a better surface finish. This is often the case for very complex components that incorporate internal geometries, such as cooling channels, or anything that cannot be machined directly from a metal block. These geometries require steps such as supports removal, heat treatment, milling or even manual polishing to achieve a better finish. These are often time-consuming and expensive and should be kept to a minimum.
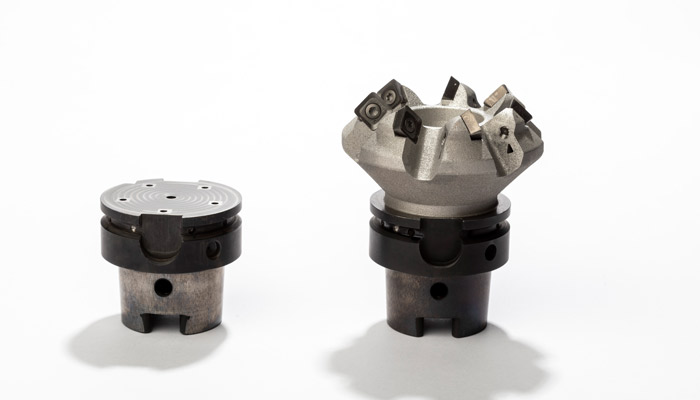
Hybrid cutting tool | Image via GF Machining Solutions
Therefore, the hybrid manufacturing process has been increasingly employed to create these so-called “hybrid” parts. This process consists not only of combining additive and subtractive technologies, but more precisely of printing directly onto a conventionally pre-machined preform. Indeed, metal 3D printing is a process that can be time consuming and costly. Therefore, industrialists are able to machine their preform and then create or add, thanks to additive manufacturing, characteristics that would be impossible to obtain using conventional processes. The result: reduced production time, limited costs, and retained technological benefits.
One of the limitations of this approach is the positioning of the preform in question. This is because the position of the preform, fixed on the printing plate, is difficult to identify. There is no mechanical link between the preform and the optical system, as can be the case in a milling machine, for example. So how can you print accurately on this preform? Many manufacturers rely on visual alignment or external coordinate measuring machines (CMMs). These methods are far from perfect, with a high risk of error and a significant lack of precision – the accuracy is only within 100 microns. What’s more, it’s a fairly time-consuming operation.
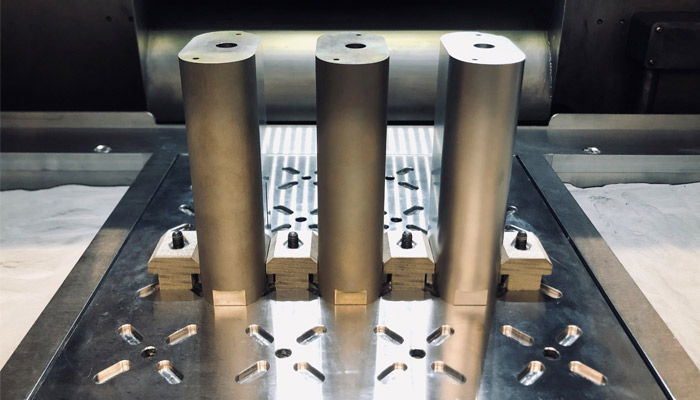
Preforms inside the DMP Flex 350 | Image via GF Machining Solutions
DMP Calibration Tool: a tool to facilitate hybrid manufacturing
To overcome this problem, GF Machining Solutions, an expert in metal additive manufacturing, has developed a tool with its partner 3D Systems, one of the pioneers in the market. Known as the DMP Calibration Tool, it reduces the number of errors made by operators, saving them a considerable amount of time. It is a software solution based on the monitoring functionality of the melting tank integrated into the DMP machine range, DMP Monitoring. This feature was originally designed to detect potential defects during the manufacturing process. However, GF Machining Solutions has diverted its main function. Dogan Basic, Product Manager at GF Machining Solutions explains: “The DMP Calibration Tool uses this light-sensing monitoring equipment for another purpose: scanning preforms to identify pre-machined positioning holes in the workpiece surface.” In practice, the laser scans the holes in the preform and sensors analyze the differences in light reflection. Thus, by triangulation and after correction of the orientation of the x, y and z axes by the software, the positioning of the preforms is known precisely. This process can be carried out very quickly and on several preforms at the same time. The risk of human error is also eliminated. This allows the user to additively add material to an already machined workpiece in a much more optimized way.
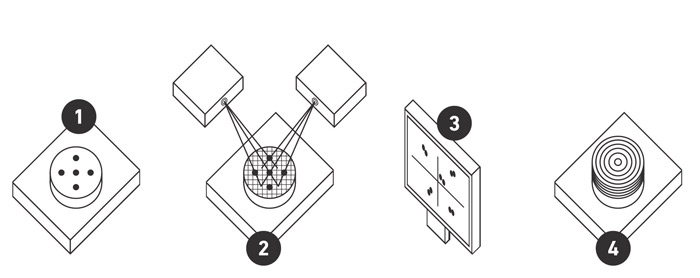
Diagram of the process described by GF Machining Solutions
On the application side, GF Machining Solutions says that this hybrid manufacturing approach will be of use to many industries including aerospace and medical, which produce complex parts in terms of internal structure, but also in the creation of tibial tray-type implants. These could be more geometrically accurate while being more suitable with each patient’s body. Finally, the tool should be of particular benefit to manufacturers of mold inserts and dies.
Dogan concludes: “Cutting tools are another application example. Increasingly they are produced by hybrid manufacturing, involving a machined preform on which an additive section is printed. Hybrid methods are preferred because the preform has a geometry that is very simple to produce by conventional methods. The use of additive manufacturing on such tools creates complicated lubrication and cooling channels that would be difficult to produce with conventional machining. A lack of precision in additive manufacturing can lead to a large deficit in tool performance. This is why our unique reference solution is highly appreciated.” More information can be found on the GF Machining Solutions website HERE.
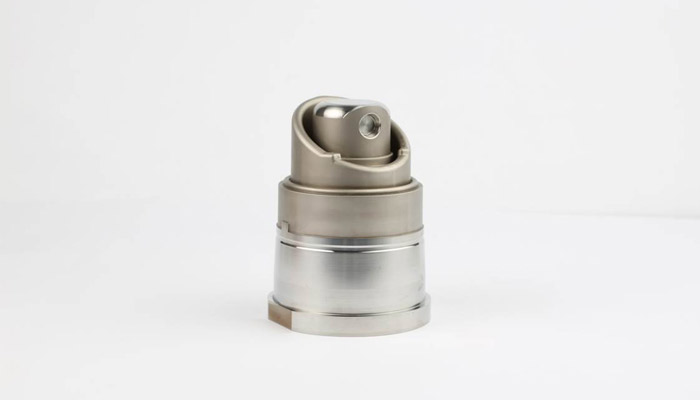
A mould designed through different manufacturing processes, including additive manufacturing | Image via GF Machining Solutions
What do you think of hybrid manufacturing? Let us know in a comment down below or on our Facebook and Twitter pages! Don’t forget to sign up for our free weekly Newsletter, with all the latest news in 3D printing delivered straight to your inbox!