Huisman Manufactures 3D Printed Crane Hooks With 350-Ton Lifting Capacity
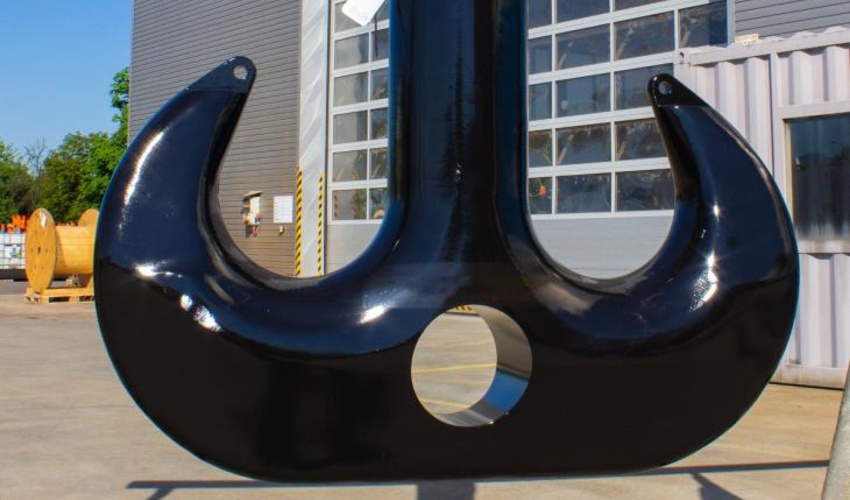
For quite some time now, additive manufacturing has been advancing far beyond FDM 3D printing. This relatively new technology can be found in numerous industrial applications today. Such is the case in the construction industry, where demands on components are particularly high due to safety regulations. Although 3D-printed houses may immediately come to mind when thinking of additive manufacturing in construction, this week’s news is not about the construction itself, but rather, a necessary tool: 3D-printed crane hooks. Of course, the crane itself must also undergo the same precautions and testing as the buildings it will be used on, which was no challenge for Huisman, manufacturer and servicer of heavy construction equipment founded in 1929. The company was able to manufacture four new 3D-printed crane hooks, which were successfully tested by the independent certification authority Lloyd’s Register, bearing quite a remarkable lifting capacity.
Huisman is a leading global supplier of technical solutions for companies in the oil & gas, renewable energy, and construction industries. Specifically, its product portfolio includes cranes, pipelay equipment, drilling equipment, winches, ship constructions, and special projects. As a rule, WAAM technology, which uses metal wire as the raw material and welding as the heat source to melt the layers, can be used to produce large, high-quality components from solid steel. “After 5 years of research, development, and testing of 3D-printed products, we have acquired the necessary expertise to use this innovative method for the production of high-quality crane hooks“, explains Daniel Bílek, project coordinator for Huisman.
Huisman Crane Lifting Capacity
The numbers on the 3D-printed crane hooks are undoubtedly impressive — they are approx. 170 x 130 cm, weigh 1,700 kg each, and have a load-bearing capacity of 350 tons. In addition, they impress with tailor-made material properties such as strength, ductility, and wear and corrosion resistance. Furthermore, the decision to manufacture crane hooks additively was by no means made arbitrary. Daniel Bílek states, “Crane hooks are commonly part of the delivery of heavy lifting cranes for the offshore industry, one of our key products. The price of a forged hook increases exponentially with size, especially if it is a non-standard size. If a hook is produced by casting, the problem of inconsistent internal quality could result in longer delivery times. All this led to the idea of making the hooks ourselves, using the so-called WAAM method.” Additive manufacturing can therefore improve costs, delivery times, and quality. You can find more information in the official press release HERE.
What do you think of Huisman’s 3D-printed crane hooks? Let us know in a comment below or on our Facebook and Twitter pages. Don’t forget to sign up for our free weekly newsletter, with all the latest news in 3D printing delivered straight to your inbox!
Cover Photo Credit: Huisman