HPP vs. Metals: Which Material Should You Use for 3D Printing?
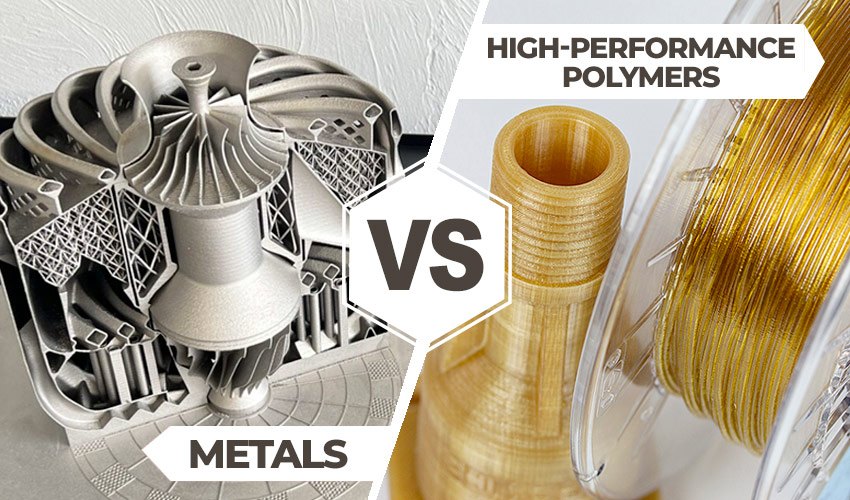
When it comes to 3D printing, materials are key. The properties and characteristics of each material family (whether metals, plastics or ceramics) will significantly impact the resulting part. And knowing which material would be best suited is a critical step in the creation of any part as the design will also be affected since it can impact everything from the use of support structures to shrinkage concerns and properties of the resulting piece. But what about when two entirely different material groups can both be used for advanced end-use parts? The best example of this is undoubtedly in the comparison between high-performance polymers (HPP) and metals.
Though it would seem obvious that metals and polymers are completely different, there are some polymers whose properties and characteristics rival those of many metals, making them a feasible alternative. But why should you use one over the other? What are the major differences between the two? What do you need to keep in mind while 3D printing? We take a closer look at these questions and more in our latest versus article.
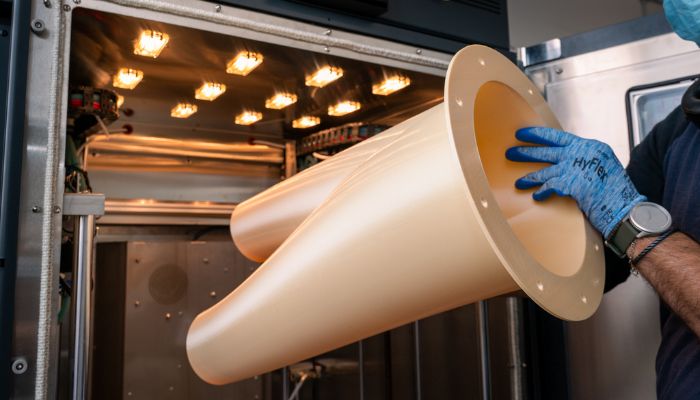
A large part made with HPP (photo credits: AON3D)
Properties & Characteristics of HPP vs. Metals
For metals and high-performance polymers, the differences start at their origins. While most metals are found in nature (except of course for alloys), polymers are made. Furthermore, the specific polymers that are used in 3D printing are made with chemically distinct polymer chains that are tangled together.
But while they might start life very differently, the characteristics and properties of what we consider HPP are similar to metal. First, however, it is important to note that high-performance is not a technical term. It refers instead to engineering grade technical polymers which tend to have a higher strength, purity, stiffness and resistance to wear and chemicals. Among these we can count thermoplastics like ULTEM, PEKK, PEEK.
Although TPE/TPU, PC and Nylon are sometimes also grouped among them, they should instead be considered “engineering thermoplastics” while “high-performance” thermoplastics are their own category. It should be noted that engineering materials can be sufficient to meet some application requirements and are cheaper, even if their properties are not as good as metals or HPP. Users should think about exactly what they need when choosing.
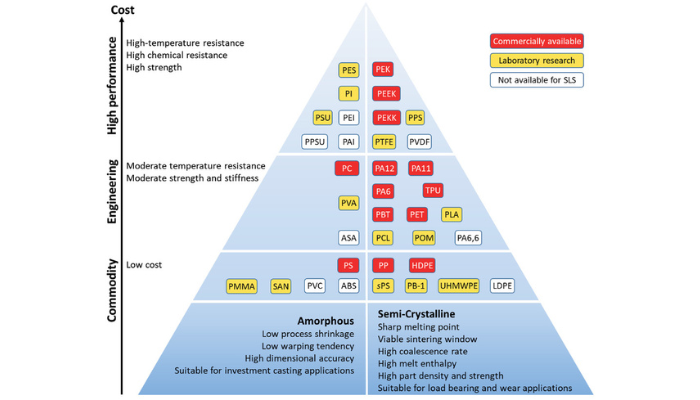
Different polymers are classed differently as can be seen is the pyramid designed to slow compatibility with SLS (image credits: Chiara Morano and Leonardo Pagnotta)
There are also many types of metals used for additive manufacturing, including ones that are natural forming as well as alloys (a metal made by combining two or more elements to give it greater strength or certain properties). To name a few, commonly used metals include aluminum and its alloys, steel (including stainless steel and tool steel), copper alloys, gallium, titanium and alloys, cobalt-chrome nickel-based alloys and, in recent years, even precious metals like gold or silver. The type of metal used depends on the intended use of the end part as each one has different properties.
Properties also differ based on the form that the metal is in. While high-performance polymers are mostly filaments with some powders, there are many more choices for metals. For example, metal is available as a powder of course but also as a filament (usually in composite form with a polymer matrix), wire and even nanoparticles. This of course has a direct impact on 3D printing as it allows for more choice, as will be discussed later on.
What Are the Properties?
The key to both HPP and metals in 3D printing is that both have incredible mechanical, thermal, and chemical properties. Indeed, high-performance thermoplastics are said to rival most metals, particularly when it comes to the so-called “super” polymers like PAEK (which includes all materials in the Poly Ether Ketones family such as PEEK and PEKK) and PEI (better known for its brand name Ultem).
For example, PAEK materials are known for their excellent chemical-, fluid-, wear-, temperature-and fire-resistance. Additionally, they have superior thermal and mechanical properties and have high impact strength even at high or subzero temperatures. Not only that, but one of the biggest advantages of using high-performance polymers is their extremely high strength-to-weight ratios (even better than that of aluminum as they are about 60-70% lighter), which allow for incredibly strong but lightweight parts. Glass transition temperatures also tend to be high as does elongation at break, though this differs between PEI, PEKK and PEEK. Corrosion resitance is also a significant benefit for all polymers in contrast to metal.
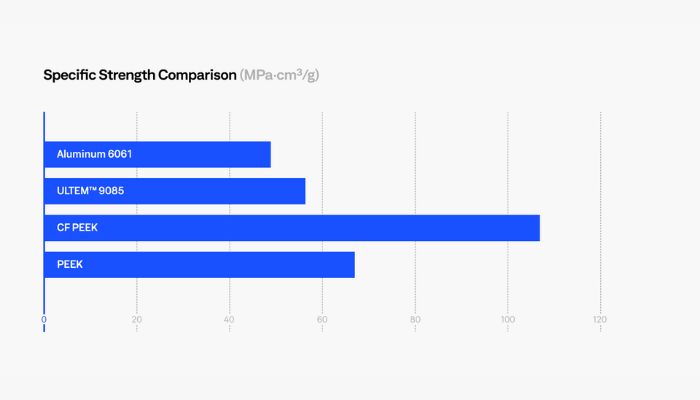
The difference in tensile strength comparing aluminum with common HPP materials (image credits: AON3D)
Metals on the other hand truly do differ depending on the one used. Aluminum for example is weaker than many others but a lot lighter, making it known for its strength-to-weight ratio. Copper meanwhile is known for its electric- and heat-conductive properties as well as great malleability. Additionally, titanium, perhaps best known for its biocompatible properties, and cobalt are favored for strength and malleability. Though it should also be said that this variation in and of itself is a strength: users can select the qualities that best suit their needs.
Overall, though how we can see a difference is that metals are popular for strength and stiffness. And though this is significant when compared to standard polymers, high-performance polymers have comparable properties and are often less dense than metals (allowing them to be lighter). Though, as mentioned, due to the significantly wider range of metals available for additive manufacturing, it is also easier to pick and choose the desired properties as compared to high-performance polymers. Metals also tend to be able to handle a broader range of temperatures depending on the specific alloy used. However, metal parts also tend to require more energy and time to make as the most popular processes involve lasers.
3D Printing With HPP and Metals
In terms of actual 3D printing, this is where we see how HPP and metals truly differ. This is because due to the natures of the materials, the processes used are not the same. Indeed, there are many more additive manufacturing technologies that are compatible with metals than with high-performance polymers.
In fact, metals are available in various forms for use in additive manufacturing. For example, for metal powders, you can count laser powder bed fusion processes like DMLS and EBM, which are popular for parts that must be strong, detailed and able to be optimized for maximum lightweighting. Similarly, Directed Energy Deposition (DED) processes (including WAAM, EBAM and WAM, among many others) use either metal wire or powder to create extremely large metal parts or to repair them (the only AM process to be able to do so). There is also binder jetting which uses a binder to create parts.
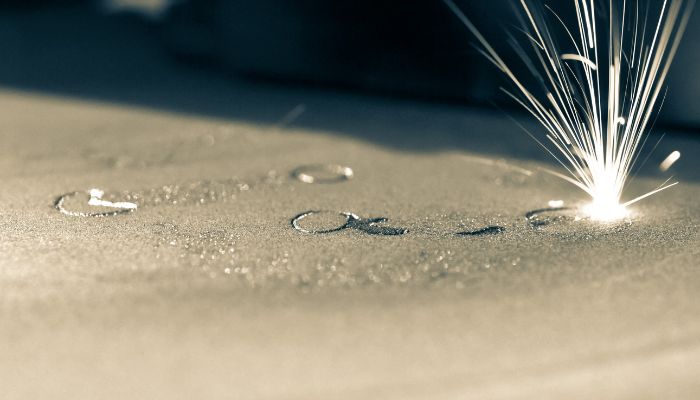
Many metal 3D printing processes involve lasers
Indeed, for processes that do not involve a laser, we can count metal extrusion and binder jetting. In binder jetting, as mentioned above, a binding agent is jetted thus binding the powder together. Though due to its nature this technology requires significant post-processing such as sintering after the initial printing. Then there is extrusion, only available through certain companies, where metal is printed along with a polymer matrix. Before the part can be used, however, it requires debinding and sintering as well.
In contrast, though standard polymers are compatible with a wide range of AM processes, high-performance polymers are not. Indeed, the main 3D printing production process used for these materials is extrusion, both with filaments and pellets (though filaments are currently more used). SLS is also possible, however there are far fewer solutions available (notably the EOS P810 machine) even though it can be useful as you do not need support structures.
What must be considered, however, is that high-performance polymers are not easy to print with. Indeed, even if extrusion is the main process, not just any FDM or FGF 3D printer will do. Rather, it is necessary to work with printers that have been designed for work with high-performance thermoplastics. This means they will always have a closed chamber that is able to heat to higher temperatures than more standard models as well as a heated print bed and nozzle that are also capable of heating up to the elevated temperatures necessary for printing with these types of thermoplastics (as their melting points are significantly higher).
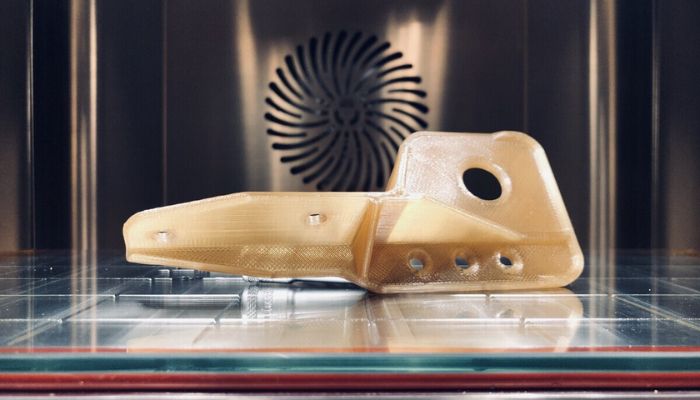
Parts made with high-performance polymers are most often made with extrusion processes (photo credits: miniFactory)
Not only that, but due to the nature of semi-crystalline polymers like PEEK and PEKK, they can be unstable at the time of melting. Making printing difficult even for expert users with advanced machines, especially as all high-performance polymers can be prone to warping. Though inclusion of fibers (for example carbon fiber, but also glass fiber or Kevlar) to make the materials stiffer and stabilize the materials in melting (due to a lower melting point and slower crystallization) can help ease printing.
Still difficulties in printing could be considered a similarity between metals and high-performance polymers. Both material families require a significant amount of work to print successfully, namely with closed chambers and high temperatures. But even this is more difficult for metals as the machines need to be in a closed chamber with no oxygen as it will react with the metal during the process. To avoid this, the chambers must be filled with a noble gas like argon.
Furthermore, due to the use of lasers and the nature of metals, some do consider that high-performance polymers are slightly easier to print since there tend to be fewer steps involved. Another example is that with laser powder bed fusion, there are additional safety measures and safety equipment required, including respirators and protective clothing to ensure that the powder does not go into the lungs or come into contact with skin.
Post-Processing Considerations
Post-processing, however, is another area where we see the advantages that HPP can have over metals in additive manufacturing processes. Namely because all metal processes require significant, obligatory post-processing before it is possible to have a final part. With DED, it is not always required but can be useful when getting rid of stress in the material that can occur during melting. It is also common to use machining to help with high surface roughness.
Removing support also is also often necessary and can be more complicated. For metals for example, milling or machining is required as the supports are in the same material. However, with HPP though initially supports were in the same material, increasingly there are specific support solutions appearing on the market that are easier to remove (though of course this requires a dual extruder machine).
Generally speaking, when it comes to metal there are additional steps involved after initial printing namely sintering and other heat treatment processes. Due to these heat-based processes as well, metal parts can be susceptible to shrinking. This thus needs to be considered during the design stage to avoid warping.
Indeed, post-processing ranges from depowdering for powder-based processes to debinding and sintering necessary for “densifying” the part (as with binder jetting).Other steps to improve the part involve either through heat treatment like hot isostatic pressing and annealing to relieve residual stress and improve certain properties or surface finishing to remove roughness and polish the final piece. Though these last stages could also be used for high-performance polymers, annealing especially is often used with materials like PEKK to maximize the mechanical, thermal, and chemical resistance properties.

Supports must be cut from metals and often require post-machining
Applications
Due to their superior properties, there is significant overlap, as well, between the applications for both HPP and metals. For example, both are used in industries like aerospace as high-strength, resistant parts are critical for the vast changes in temperature as well as conform to regulations for safety-critical parts. Though it should be mentioned as well that here HPP are beginning to truly show their worth thanks to their impressive strength-to-weight ratio and increased lightness as compared to metals, which is very important in aeronautics.
These same properties make both materials popular as well for industrial applications such as bearing cages and pipe fittings and especially in the automotive and transportation sector. Though, traditionally, aluminum has been used for the creation of parts in everything from luxury vehicles to racecars, high-performance polymers are also increasingly used thanks to their increased lightness.
Medical applications are also important, though it needs to be noted that they are not suitable for all HPP or metals. Rather, certain ones are used as they are biocompatible, meaning that they can be used with the body. This includes titanium among the metals and PEEK and PEKK among polymers. Here you can also see a difference, titanium is popular for its biocompatibility due to a general resistance to corrosion from bodily fluids, capacity to integrate into bones and high limit. Meanwhile PEEK is interesting for that as well as the fact that it has properties that are very similar to human bones, which makes the material particularly interesting for 3D printing implants.
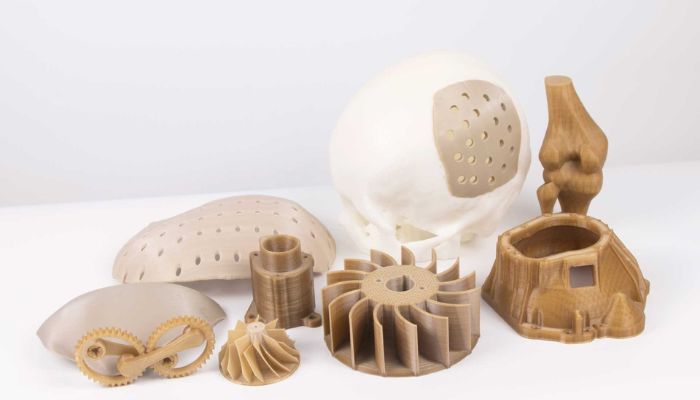
PEEK is popular for many different applications. Also, thanks to its similarities to bone, making it ideal for implants (photo credits: IEMAI)
Still, as you can see, due to the incredible properties of these material families, there are few differences in applications between the two. Rather, it comes down to individual materials and the specific benefits they bring. Such as, for example, using titanium in medical applications and aluminum in automotive. However, there are a couple of characteristics that set them apart.
Polymers will always be better for parts that must be light and are superior to metals in environments where corrosion would be a factor. Additionally, they are effective heat and electricity insulators making them ideal for electrical applications. Whereas when it comes to strength where weight is not a factor, many metals will be superior. Also, it cannot be denied that with metals there is a greater range of choice of material, meaning that selection of what is needed based on the specific properties or characteristics may be easier. Furthermore, metals are conductive which, while not appropriate for applications needed insulation, is a real boon for use in electrical components and wiring systems. It also is a factor when creating sensors or biomedical devices.
Manufacturers & Price
It must be said that for both HPP and metals, the price is significantly above that of standard polymers like PLA, ABS and PETG. For example, metal will differ based on which one is being used as well as the type (wire, powder, etc.) but for 1kg of powder it will range between $70 – 700, depending especially on how specialized the material is (cobalt will be significantly more expensive than steel). Meanwhile a 1kg roll of PEEK filament will be above $500, going significantly higher as well depending on the quality of the material and the addition of carbon fiber.
Still not all high-performance polymers will have the same price point either. 1kg of PEI filament will be available from about $200, significantly lower than PEEK, and PEKK is similar. But it is undeniable that, though the price points are similar, many metals will be cheaper than high-performance materials, especially in bulk.
What about manufacturers? Well for high-performance polymers most of the manufacturers are understandably chemical companies like Arkema, Solvay, SABIC, BASF and Evonik or companies with 3D printers designed for high-temperature, high-performance polymers such as INTAMSYS. Though it should be highlighted that most HPP materials do still come from chemical companies, including some who also provide 3D printing solutions, for example Lehmann&Voss. Meanwhile metal 3D printing materials are available mainly from 3D printing solution providers like EOS, 3D Systems, Trumpf, Sciaky, Desktop Metal and HP.
What do you think of the differences between high-performance polymers vs metals? Do you prefer one over the other? Let us know in a comment below or on our LinkedIn, Facebook, and Twitter pages! Don’t forget to sign up for our free weekly Newsletter here, the latest 3D printing news straight to your inbox! You can also find all our videos on our YouTube channel.