How To Get Stronger FDM Parts With ADDCAAM®?
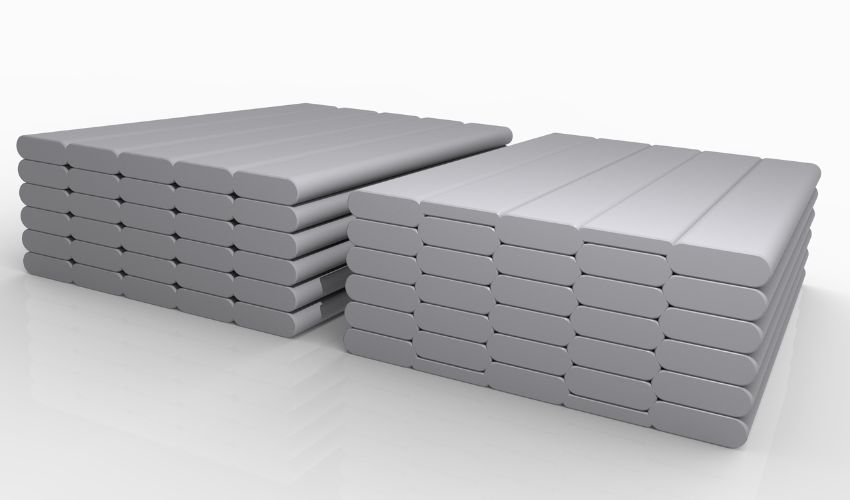
3D printing, especially polymer fused deposition modeling (FDM), has transformed the production of complex shapes and thermal-resistant components in the most demanding industries, such as aerospace and automotive. Despite its advantages, however, FDM technology also encounters limitations in part performance, especially regarding the strength and porosity of the parts.
To address this challenge, ADDMAN, a leading American contract manufacturing company specializing in industrial additive manufacturing services, has developed an innovative software solution in collaboration with Danish software company, Create It REAL, called ADDCAAM. This software optimizes FDM 3D printing, reducing part porosity and enhancing durability.
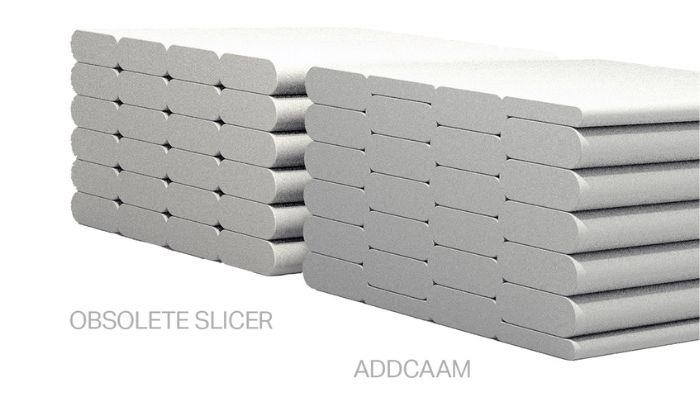
Conventional slicing vs ADDMAN ADDCAAM InterFill 3D method.
ADDMAN uses the “CAAM” (Computer-Aided Additive Manufacturing) approach to create more robust parts for both polymer and metal. For polymer FDM parts this is achieved through the ADDCAAM Software. For metal parts, it is achieved through advanced work at their metal additive facility, Castheon, where they’ve developed innovative techniques for 3D printing high-temperature refractory alloys to boost part performance.
How Does ADDCAAM Work?
The ADDCAAM concept originates from a common issue faced by ADDMAN’s customers: the weakness of the X/Y plane in 3D-printed polymer parts. To address this, ADDMAN aimed to develop a build preparation tool that diverges from standard slicers, which typically rely on conventional slicing techniques. Instead, ADDCAAM developed InterFill 3D—an interlocking filling method—and non-coplanar layering. But what exactly does “non-coplanar” mean, and what benefits does this technique offer?
Non-coplanar layering in additive manufacturing refers to a technique in which the layers are not flat and parallel to the build platform. On the contrary, the layers can be placed at various angles or curves relative to each other, allowing for more complex and structurally optimized geometries.
According to ADDMAN, this approach enhances the mechanical properties of parts by optimizing the position of the layers, thereby reducing anisotropy commonly found in traditional additive manufacturing. Non-coplanar layering mitigates this issue by creating uniform properties throughout the piece. This technique also allows for smoother surfaces and finer details, as layers conform better to the contours of the workpiece. This strategic placement of material optimizes its use and expands design freedom.
Non-coplanar layering enables more sophisticated, high-performance additive manufacturing, producing stronger parts with significantly lower porosity than industry standards. The improved porosity achieved through ADDCAAM revolutionizes traditional FDM applications by addressing issues of poor sealing and voids in sliced parts. This enhancement facilitates the creation of water-tight containers, reduces air loss in ducting, and improves the functionality of pneumatics and low-pressure hydraulic applications. Additionally, it allows for more predictable dielectric properties in radio frequency applications. The enhanced material properties further elevate the versatility of FDM parts, making them more isotropic, increasing their strength-to-weight ratio, and reducing their weight, leading to higher fuel efficiency.
Less Porous and Stronger Parts for the Aerospace Industry
To illustrate this, ADDMAN highlighted how their innovative software can drive innovation and address design and manufacturing challenges in the aerospace industry. In aircraft, ducting is crucial for transporting and distributing air or fluids, commonly found in the engine or cooling system. These ducts can be made from various materials, including aluminum, titanium, and composites, and their design is vital for the vehicle’s proper functioning.
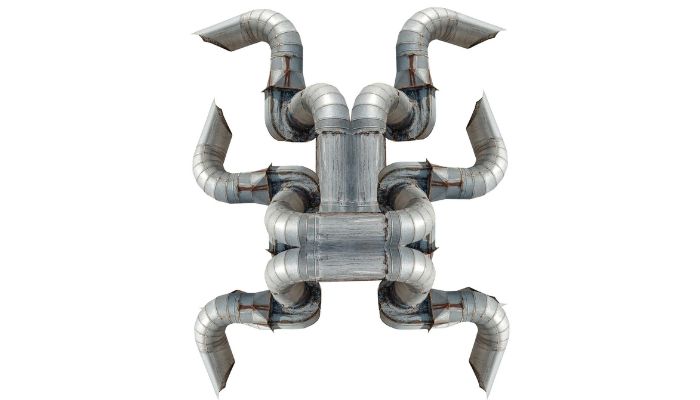
With the help of ADDCAAM, low-pressure ductwork can now be made of polymer materials vs metal.
While high-pressure air or exhaust ducts are typically metal, lower-pressure ductwork can be made from polymer materials. 3D printing technologies like FDM, SLA, and MJF enable the production of polymer ducts with complex, lightweight, and high-strength structures that are unattainable with traditional methods. However, excessive porosity in 3D-printed parts poses a significant challenge, as even minor leaks in aircraft ducting can adversely affect performance and safety.
ADDMAN, leveraging the ADDCAAM software and methodology, has drastically reduced the porosity of FDM 3D-printed ductwork prototypes, cutting costs for their customers by 15% compared to other additive technologies. Beyond cost savings, the FDM parts were 70% stronger and 100 times less porous, resulting in enhanced performance and durability.
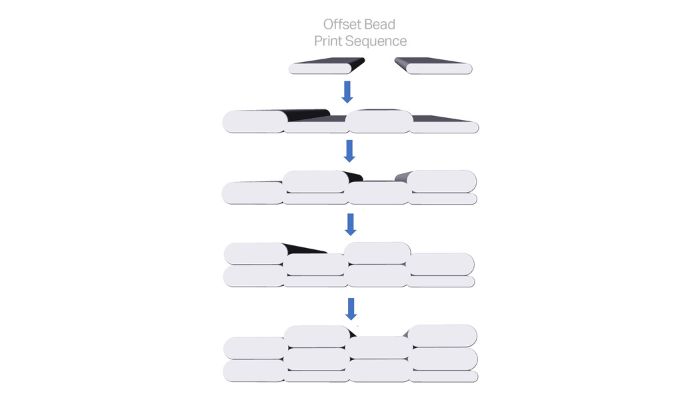
Build sequence of the beads for ADDCAAM toolpaths.
Mark Saberton, CTO of ADDMAN, commented: “Our ADDMAN culture is about starting with problems and working backward. By solving customers’ problems, we identified the need for stronger parts and developed something revolutionary.” The ADDCAAM software solution has also received numerous recognitions. In 2023, it was a finalist in the TCT Group Software Awards and the Advanced Concepts category of AMUG (Additive Manufacturing Users Group), as an exemplary use of additive manufacturing technologies that “push the envelope”. ADDMAN will be showcasing ADDCAAM at Rapid + TCT 2024.
To learn more about ADDCAAM software, visit ADDMAN’s booth at Rapid + TCT 2024 (842) or click HERE. What do you think of ADDCAAM software for stronger FDM 3D-printed polymer parts? Let us know in a comment below or on our LinkedIn, Facebook, and Twitter pages! Don’t forget to sign up for our free weekly newsletter here for the latest 3D printing news straight to your inbox! You can also find all our videos on our YouTube channel.
*Cover: The difference between the bead stacking of traditional slicers vs ADDCAAM
*All Photo Credits: ADDMAN