How is Additive Manufacturing Being Adopted in Defense?
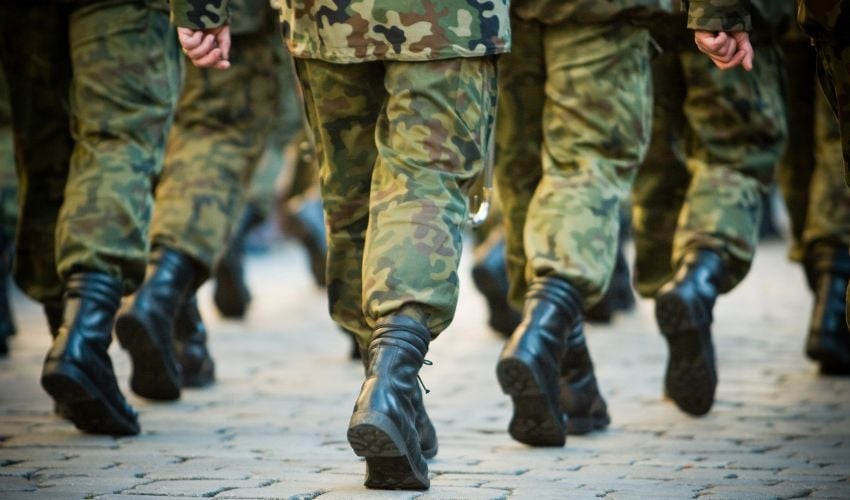
When it comes to the military, flexibility and innovation are key in ensuring the success of operations in all corners of the globe. Indeed, when we think of military personnel one of the underlying characteristics of their actions is rapidity, as speed and ability to change on the go can be the difference between success and failure on the field. For that reason, the defense sector is constantly looking for ways to improve what it terms field readiness, including with additive manufacturing.
All that has culminated in a sector that is rapidly growing, with the global additive manufacturing in aerospace and defense market valued at around $2.76B in 2022 and expected to increase to around $17.9B by 2032. Thus, growing at a rate of a CAGR of about 20.48% according to Inkwood Research. But what is the current status of additive manufacturing in defense? How has it grown and what obstacles are still barring its way? We took a closer look.
Government Policies for 3D Printing in the Military
The United States
Government policies, at both a national and international level, are driving the use of 3D printing in the military sector. The clearest examples of this comes from one of the earliest and most fervent adopters of additive manufacturing in defense: the United States Department of Defense (DOD).
The American armed forces, consisting of the army, navy, air force, marine corps and space corps, is currently the world’s third-largest military in the world numbering around 1,328,000 active personnel in 2024. Considering that the two largest, the People’s Republic of China and India, have populations that dwarf the USA, the US military constitutes a much larger proportion of the population as well as the budget of the nation. The US is also currently part of multiple wars, making a strong military even more necessary.
For that, it has become key for the Department of Defense to embrace flexibility and innovation–both key characteristics of additive manufacturing, ultimately prompting the DOD to adopt their very own Additive Manufacturing Strategy back in January 2021. This was further strengthened by the Biden Administration’s embracement of AM with their AM Forward Initiative that was announced in May 2022. We have seen the results of this with a growing use of AM in all military branches as well as testing the technologies in different training exercises.
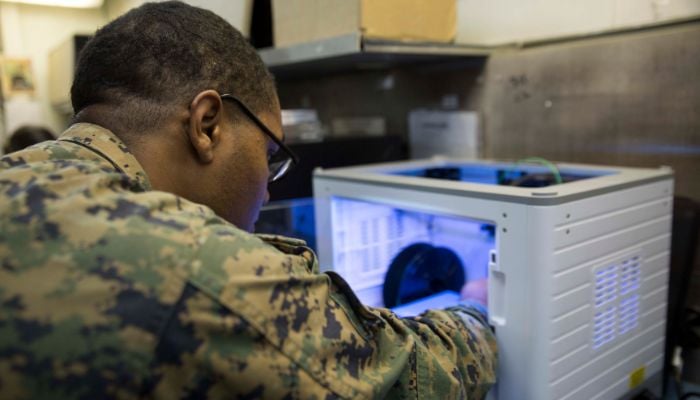
An American solider working with a 3D printer (photo credits: Cpl. Bernadette Wildes/31st Marine Expeditionary Unit)
The DOD’s Additive Manufacturing Strategy is quite long and impossible to summarize in just one article. But essentially, it outlines why and how additive manufacturing should be adopted within the wider American defense ecosystem. Notably, the strategy outlines three key ways in which the use of 3D printing aligns with the DoD’s broader mission: by modernizing national defense systems; increasing material readiness through rapid prototyping and production of direct parts, thus also reducing the risk of obsolete hardware; and of course to enable warfighters to employ innovative solutions on the battlefield through the vast capabilities of AM.
This is expected to be done through five strategic goals. Namely, to integrate AM into DoD and the Defense Industrial Base; align AM activities across DoD and with external partners; advance and promote agile use of AM; expand proficiency in AM; and secure the AM workflow. Through these, the DoD is hoping to reap the benefits of 3D printing adoption not just for themselves but also for allies. This includes making training for the technologies more accessible and overcoming issues in securitization of data for parts.
Explaining the importance of this Strategy, Robert Gold, Former Director of the Technology Manufacturing Industrial Base (TMBID) office in STP&E, OUSD (R&D), noted in official correspondence from the DoD that “Additive manufacturing offers DOD unprecedented supply chain agility while enabling our developers to sustain technological dominance for our Warfighters. This Strategy ensures that DOD will realize the most benefits from AM technology by structuring our AM activities, aligning funding opportunities, and improving AM implementation efforts – all with the objective of enhancing our Warfighters’ mission readiness.”
As mentioned, since 2012, we have continued to see the fruits of this, with direct DoD spending on AM going from $300M in 2023 to $800M in 2024. This is expected to continue to increase to an estimated $2.6B in 2030. There have been projects across all the military branches as well. Including critical submarine components, 3D printed rockets through the US Air Force, Apache helicopters, metal 3D printers aboard US Navy ships, 3D printing for weapons systems, drones for battlefield aid and even barracks.
William LaPlante, the former undersecretary of defense for acquisition and sustainment, in a panel at the Air and Space Forces Association’s Air, Space and Cyber in 2023, further explained, “Additive manufacturing is being used to produce parts in aircraft engines; car companies are using them for mission-critical parts. What’s interesting about it is not just that you can do things faster, you can produce things that we could not have produced otherwise. And what’s happening — and we’re seeing it in Ukraine — is it’s also changing how sustainment is done. Going back and forth with additive manufacturing, and going back and iterating with [digital engineering,] magic can happen. It’s happening right now in the commercial space, where [space development agencies] are going from the design phase to production and going up to orbit in three years.”
The United Kingdom
The UK Ministry of Defense (MoD) has also outlined its own intention to unlock the benefits of additive manufacturing. This has been done in a few different ways, but we must point first to its framework for additive manufacturing (AdM).
Similar to the DoD’s Additive Manufacturing Strategy, AdM seeks to not only adopt 3D printing to reap the benefits for military applications, but also to explore what may prevent its adoption in the government as well by industry partners. To do this, the MoD’s Defense Equipment & Support (DE & S) organization awarded contracts to five companies back in April 2023.
But just because the framework was unveiled more recently does not mean that there have not already been developments. In 2022, the government launched Project TAMPA aiming specifically at promoting metal additive manufacturing by seeking companies with whom the government could enter into an agreement and help accelerate the “maturity of additive manufacturing” technology. In particular, the call mentions a need to address excessive lead times by improving the end-to-end supply chain, especially for obsolete parts.
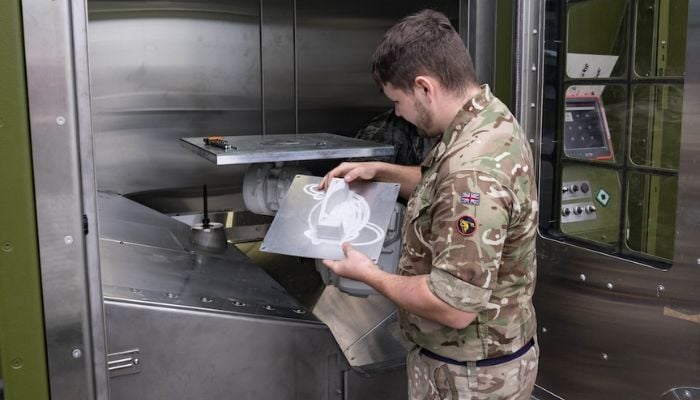
A British soldier taking a part out of a printer (photo credits: MOD Crown)
But AM has been around for longer than that in the British Military. Alexander Champion, an Additive Manufacturing Engineer at the MoD, explains, “The Ministry of Defence has been running multiple AM trials over the past ten years. They are currently looking at the adoption of Additive Manufacturing, as part of a wider advanced manufacturing toolkit. For the British Army, Youtube will show videos of the Royal Engineers in the British Army 3D printing plumbing fittings for hospitals in South Sudan back in 2019. As a result of that success, the REME are moving forward with the adoption of metal AM. More recently, in the RAF, 71 Inspection and Repair Squadron, have also built a powder bed metal facility.”
He further notes that project TAMPA is a direct result of the previous success with additive manufacturing, he expands, “This project is working with Thales, RBSL, Babcock, and NP Aerospace to accelerate the manufacture and installation of 3D printed parts by Defence manufacturers. The project has seen industry printing and fitting increasingly complex metal parts to in-service vehicles. This has helped inform future decision makers in the MOD on how to create an environment whereby additively manufacturing parts becomes ‘business as usual.’”
Furthermore, the success of project TAMPA in general has also pushed the United Kingdom to further invest in additive manufacturing with Spiral 3. This project hopes to accelerate AM adoption throughout the defense supply chain through improving AM equipment availability across the MoD and growing AM understanding between US DoD and UK MoD suppliers.
Other Examples Around the World
Though examples of specific policies are more evident in the cases of the UK and US, a number of different governments have implemented projects in order to increase the use of additive manufacturing in defense. One of the best examples is likely with SPEE3D in Australia.
For those who may not know, SPEE3D uses cold spray additive manufacturing, one of the few companies to do so. This metal technology is notable for its speed and versatility, especially in terms of material choice. This has made it an attractive option for the Australian military (as well as American). Indeed, the two have worked together on a number of projects including tests to print replacement armed vehicle parts, as well as developing an additive manufacturing team for the Australian army.
We are also seeing an increased role of additive manufacturing in defense in Europe. The European Defence Agency created a feasibility study on how additive manufacturing could enhance defense capabilities. In the report, the agency pointed notably to “mobility, sustainability, ensuring platform availability, effect and protection through e.g. on-site and on-demand field repair & maintenance, reduced logistic burden of deployments and improved sustainability in warfighting and peacekeeping missions” as key applications.
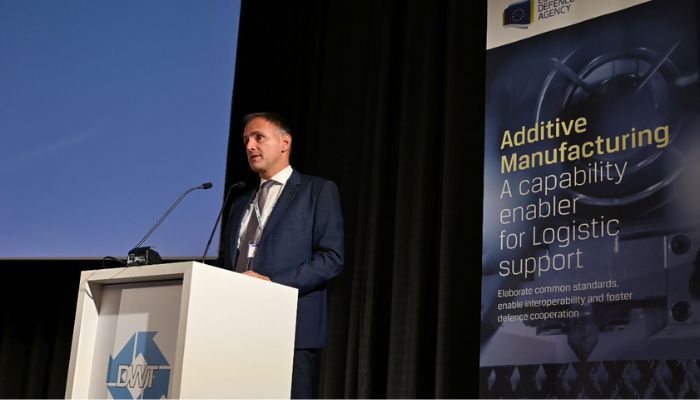
The EDA has been working to integrate additive manufacturing (photo credits: EDA)
Moreover, the findings showed that technical capabilities for the different additive manufacturing technologies are wide and varied, thus showing considerable potential in defense.
Champion acknowledged this growing use of AM as well, commenting, “Outside of UK MOD, it is also clear that our NATO allies have a significant appetite to increase their Additive Manufacturing capabilities. The UK MOD have therefore already taken part in multiple military training exercises looking to better cohere and align exploitation of the technology with countries such as France, the Netherlands, the USA and Australia. In future this could help unlock a new global supply web, whereby parts can be printed at or near the point of need by industry, UK Military or a NATO neighbor.”
China also seems to be turning towards 3D technologies. This past year, after an announcement that Taiwan was using 3D printing for drones, news came out that China’s People’s Liberation Army (PLA) is also using 3D printing. More specifically, the PLA has been using AM to test remote weapons maintenance by delivering 3D printed parts via UAV, a trend that we can expect to continue.
How Is Additive Manufacturing Being Used in Defense?
Now that we see how important additive manufacturing is becoming in the defense sector, it is important to determine which technologies are most prominent. Of course, due to the vast applications possible with the technologies, there are also many different materials that are used, including metals, composites and plastics. We took a look at the different kinds and how they are used.
Composite 3D Printing
Defined as materials made of two or more “constituent materials,” composites are popular in many sectors for their lightness and strength. Notably, they have been quickly adopted in sectors like space and aeronautics, where light-weighting is critical for the success of flights. As you can therefore imagine, they are also very applicable in defense.
For example, composites can be used for the creation of lighter components such as helmets, weapons, electrical components, spare parts and much more. The air force meanwhile uses composites in much the same ways as for with aviation. Namely, creating spare parts and recreating obsolete parts for legacy fighter jets such as B-52s, the massive C-5M Super Galaxy, and the B-2 Stealth Bomber. Both have eyed composite 3D printing as a way to lighten tools and literally take a load off.
Metal 3D Printing
Metal 3D printing is where we are seeing the most growth in the defense field. This has been particularly obvious with the army and navy. The US Navy has partnered with SPEE3D and AML3D to overcome severe supply chain issues for making submarine parts. Not only that, but the military branch worked extensively with Xerox, before it sold its 3D printing capabilities. This was notably seen when a metal 3D printer was put on the USS Essex for the first time in 2022.
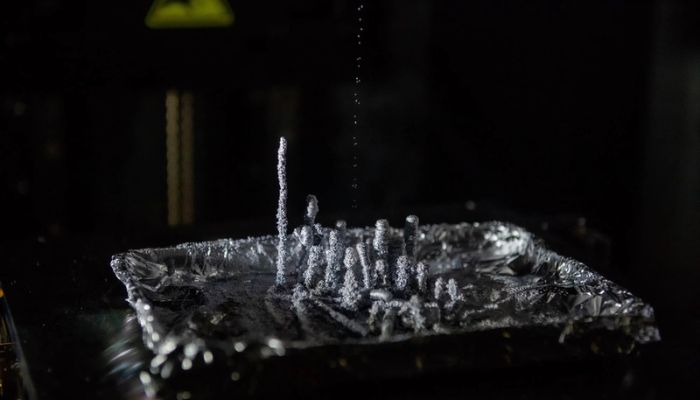
A metal 3D printed part made on the USS Essex (photo credits: Mass Communication Specialist 3rd Class Isaak Martinez/U.S. Navy)
Champion further comments, “Metal AM is also being investigated within the MOD, however this is slower due to the cost and complexity of equipment. We are already seeing Defence suppliers such as Lockheed Martin, Rolls Royce, Airbus Defence and Boeing printing critical metal parts for flight. This includes metal powder bed but also larger technologies such as DED and cold spray for use in both Additive Manufacturing as well as Additive Repair.”
Polymer 3D Printing
However, even with the vast applications for both metals and composites in additive manufacturing in the military, polymers should not be forgotten either. For one, simple polymers and FDM printing is often how soldiers learn about AM as well as how it started being adopted in the first place.
Champion expands, “Deployed Military users such as soldiers in the Army started with FDM printing, this is a very fast and affordable way to learn how additive manufacturing can support. Very quickly we learnt that AM will not replace the supply-chain, or the other tools which MOD engineers use, such as welding. AM is, however, a very powerful tool when used for the correct applications. Several organizations both in Defense and Industry are now upgraded to using additional polymer printing technologies such as SLS printing and continuous carbon fiber reinforced. These technologies are perfect for larger volume, higher-strength, end use parts.”
High-performance polymers also have their place. Lighter than metal but just as strong, materials like PEEK and PEKK are already popular for aerospace operations and are therefore being used in similar capacities in defense.
What Are the Current Obstacles to Greater Adoption?
Still, even with this increasingly widespread adoption, challenges remain when it comes to the use of additive manufacturing for defense. These obstacles actually reflect many of those present in other industries for the adoption of 3D printing, including lack of training, issues with certification and security concerns notably related to data breaches. However, due to the sensitive nature of the work in the defense sector, these become even more prominent.
Therefore, in order to truly propagate the technology, beyond where it is now and in more countries’ militaries, these obstacles need to be addressed. This is also acknowledged by the EDA in their previously mentioned report, stating “non-technical factors (IPR, training, standardization and certification, health and safety, etc.) represent solid limitations for AM implementation, stronger in fact than technical ones.”
It could be said that it is not so much the technologies themselves that are difficult to find applications for but rather standardization and certification and training people to work with the machines that pose the biggest issues. That being said, this is a weakness that the additive manufacturing industry has been aware of for some time. Over the past few years, we have seen a growing presence of certification and qualification organizations at events like RAPID + TCT and Formnext, as 3D printer and material manufacturers are showing their interest in their services.
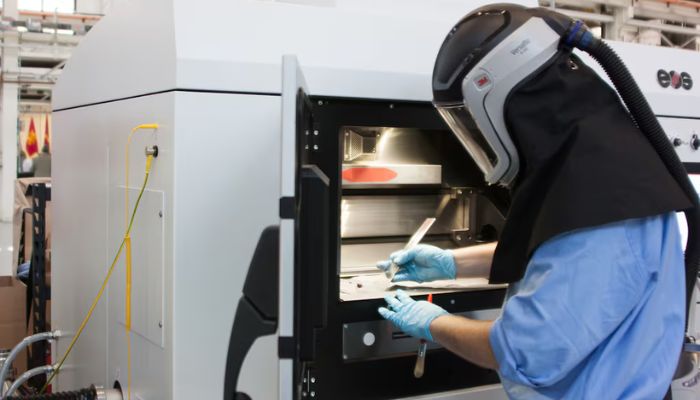
At the Rock Island Arsenal, engineers are working on using additive manufacturing for many defense applications (photo Credits: Debralee Best/U.S. Army)
Not only that, but the US Army at least is actively targeting this with calls for white papers, as can be seen in a recent example. Looking to adopt AM for flight-critical parts, the military has called for 3D printing vendors, the best placed to make many of these parts due to their vast knowledge and skills in different 3D printing processes, who are qualified to create them to send them. This solution may be one that can be adopted in other countries, at least while we are still working to grow additive manufacturing capabilities within the military corps of engineers.
Champion highlights additional obstacles, stating, “The most critical obstacle to the widespread adoption is the availability of CAD and design information, large numbers of our unavailable spare parts stopped being manufactured in the 1970s, there are therefore no technical drawings or digital CAD to build a ‘thingiverse’ style library from. The task of assessing and reverse engineering the +1million different items in our supply chain will not be a fast or easy problem to solve. Once we have some digital files which are suitable for manufacture, the MOD can then begin to mature all the other key topics, called Defence Lines of Development (DLOD’s). These will include, proportional certification, access to Intellectual Property Rights, improving user training and understanding maintenance in a deployed environment will all be challenges to overcome, as well as understanding demand signal issue from the MOD to make this possible and worthwhile.”
How can we address this problem? Well, the answer cannot be simple due to confidential nature of defense work. However, looking at examples from other industries, notably railroad, it is certainly possible to make this kind of digital database and we have seen that it has benefits. The question however will always be how to make it more secure, meaning that this is perhaps something that should be developed primarily through governments, even if the industrial sector may have more resources.
Security is yet another concern. 3D printers are difficult to secure and there have been controversies in the past about using them for sensitive information. Being able to protect digital files is paramount to prevent hacking or sabotage. Thankfully, given the number of additive manufacturing working in the defense sector, many have been working on this issue, making it easier for the militaries of different countries to adopt different 3D technologies.
What Will Be the Role of AM in Defense in the Future?
So, where to go from here? Given the constant advancements in additive manufacturing in the defense sector, it seems safe to say that it will continue to grow. And while the United States, followed by the United Kingdom, were the first to create a policy centered on additive manufacturing in defense, they will likely not be the last. NATO countries especially are likely to develop their own, given their already existing interest in 3D printing, plus the work being done in two of the world’s largest militaries.
Additionally, it is likely that the use of AM will continue to grow in the United States. One of the cornerstones of President Trump’s intended policies in this second term is a stronger military. And a surefire way to achieve this is through technological advances, including additive manufacturing. Nothing is sure, of course, but there is potential for investment for military applications.
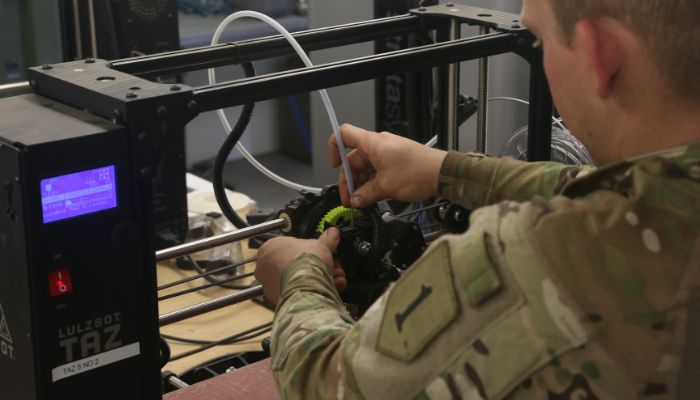
A U.S. soldier working with a 3D printer back in 2019 (photo credits: U.S. Army)
Collaboration will also help additive manufacturing grow as a key tool in the defense sector. Champion concludes, “The MOD have not undertaken this journey alone, they are already collaborating with some of the biggest names in the industry to guide us along the way, such as the National Centre for Additive Manufacturing based in the MTC in Coventry. Likewise, we have a close working relationship with our NATO allies. Finally, the MOD is not just interested in 3D printing, it is just the first new tool to be considered for the toolbox. There is a growing appetite to understand other Advanced Manufacturing processes such as laser cutting. Additive Manufacturing will hopefully be the first step in helping the MOD realize the benefits of digital manufacturing.”
What do you think of the use of additive manufacturing in the defense sector? Do you know of other countries where 3D printing is being used in the military? Let us know in a comment below or on our LinkedIn, Facebook, and Twitter pages! Don’t forget to sign up for our free weekly Newsletter here, the latest 3D printing news straight to your inbox! You can also find all our videos on our YouTube channel.
You might be interested in this latest Press Release from DMC where all the key players you mentioned were at the latest MOD Project TAMPA workshop
https://www.digitalmanufacturingcentre.com/news/uk-ministry-of-defence-and-industry-collaboration-breaks-new-ground-at-the-digital-manufacturing-centre
I really appreciate you sharing this — learned something new today.
A creative journey and waiting for the explosion
While armies around the world are accelerating the application of 3D printing technology to respond flexibly on the battlefield, in Geometry Arrow, players must also continuously adapt to obstacles, react quickly like a digital warrior, and overcome increasingly difficult levels.